Comparison Between DCS and SCADA System
Comparison between DCS and Scada System
DCS and SCADA are monitoring and control mechanisms used in industrial facilities to monitor and control processes and equipment; to ensure that everything is running smoothly and that no equipment is operating outside the specified limits. The most significant difference between the two is their overall design. DCS, or Data Control System, is process-oriented because it focuses more on processes at each step of the operation. SCADA, or monitoring and data acquisition, focuses more on the acquisition and compilation of data for reference purposes for staff monitoring the progress of the operation.
DCS is driven by the state of the process, while SCADA is even driven. DCS performs all its tasks sequentially and events are not recorded until they are analyzed by the station. However, while SCADA and HMI System is event driven, it does not call scans regularly but waits for an event or value change in a component to trigger certain actions. SCADA is a little more advantageous in this regard, as it lightens the load on the host. Changes are also saved much earlier since an event is recorded when a value changes state.
In terms of applications, DCS is the system of choice for facilities limited to a small area, such as a single plant or plant, whereas SCADA is preferable when the complete system is distributed over a much larger geographical area. oil wells spread over a large field. This is partly because DCS must always be connected to the system’s I/O, while SCADA is supposed to work even when field communications fail for a while. HMI SCADA does this by keeping a record of all current values, so that even if the base station cannot extract new.
In addition to their design and application differences, DCS and SCADA systems also have variations in terms of their architecture and scalability. DCS is typically characterized by a centralized architecture, where all control functions are concentrated in a central control room. It offers a high level of integration, with control algorithms and data processing functions performed within the central controller. DCS systems are often preferred for complex processes that require intricate control strategies and extensive automation.
On the other hand, SCADA systems have a more distributed architecture, with remote terminal units (RTUs) or programmable logic controllers (PLCs) deployed at various locations within the industrial facility. These RTUs or PLCs are responsible for data acquisition and local control, while the central SCADA server collects and processes the data for monitoring and control purposes. SCADA systems are known for their scalability and flexibility, making them suitable for applications where remote monitoring and control of geographically dispersed assets are required.
Another aspect to consider when comparing DCS and SCADA systems is their level of customization and vendor compatibility. DCS systems are typically proprietary and provided by specific vendors, which can limit interoperability with equipment from different manufacturers. On the other hand, SCADA systems often employ open standards and protocols, allowing for more flexibility in integrating devices and equipment from multiple vendors. This interoperability can be particularly advantageous when upgrading or expanding existing industrial infrastructure.
Both DCS and SCADA systems play important roles in ensuring operational efficiency and safety in industrial processes. DCS excels in complex and integrated process control applications, providing advanced control strategies and centralized management.
DCS and SCADA systems also differ in terms of their level of sophistication and complexity. DCS systems are known for their advanced control algorithms and integrated functionalities, making them capable of handling intricate processes with multiple variables. SCADA systems, while offering essential monitoring and control capabilities, may have a simpler and more straightforward configuration, making them easier to deploy and maintain.
It's important for industrial facilities to carefully assess their specific needs and requirements when choosing between DCS and SCADA systems. Factors such as the size of the operation, the complexity of the processes, and the geographical distribution of assets will play a significant role in determining the most suitable system for effective monitoring and control.
In conclusion, while DCS and SCADA systems have overlapping functionalities, they differ in their design, application, architecture, and scalability. DCS focuses on process-oriented control and is commonly used in smaller, centralized facilities, while SCADA systems are more suitable for distributed applications over larger areas. Understanding the strengths and limitations of each system can help industrial operators make informed decisions when choosing the appropriate monitoring and control mechanism for their specific requirements.
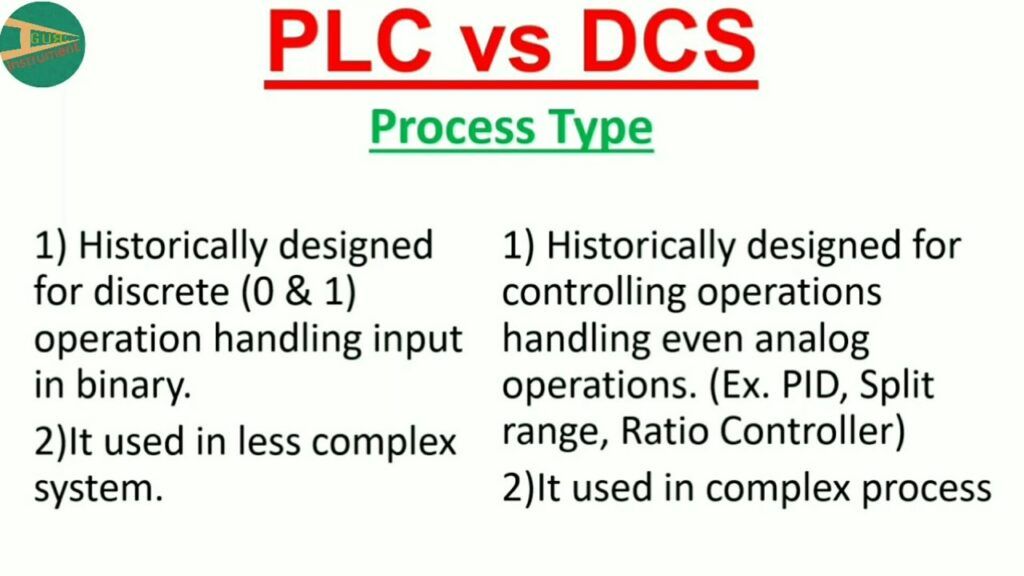
You might also like
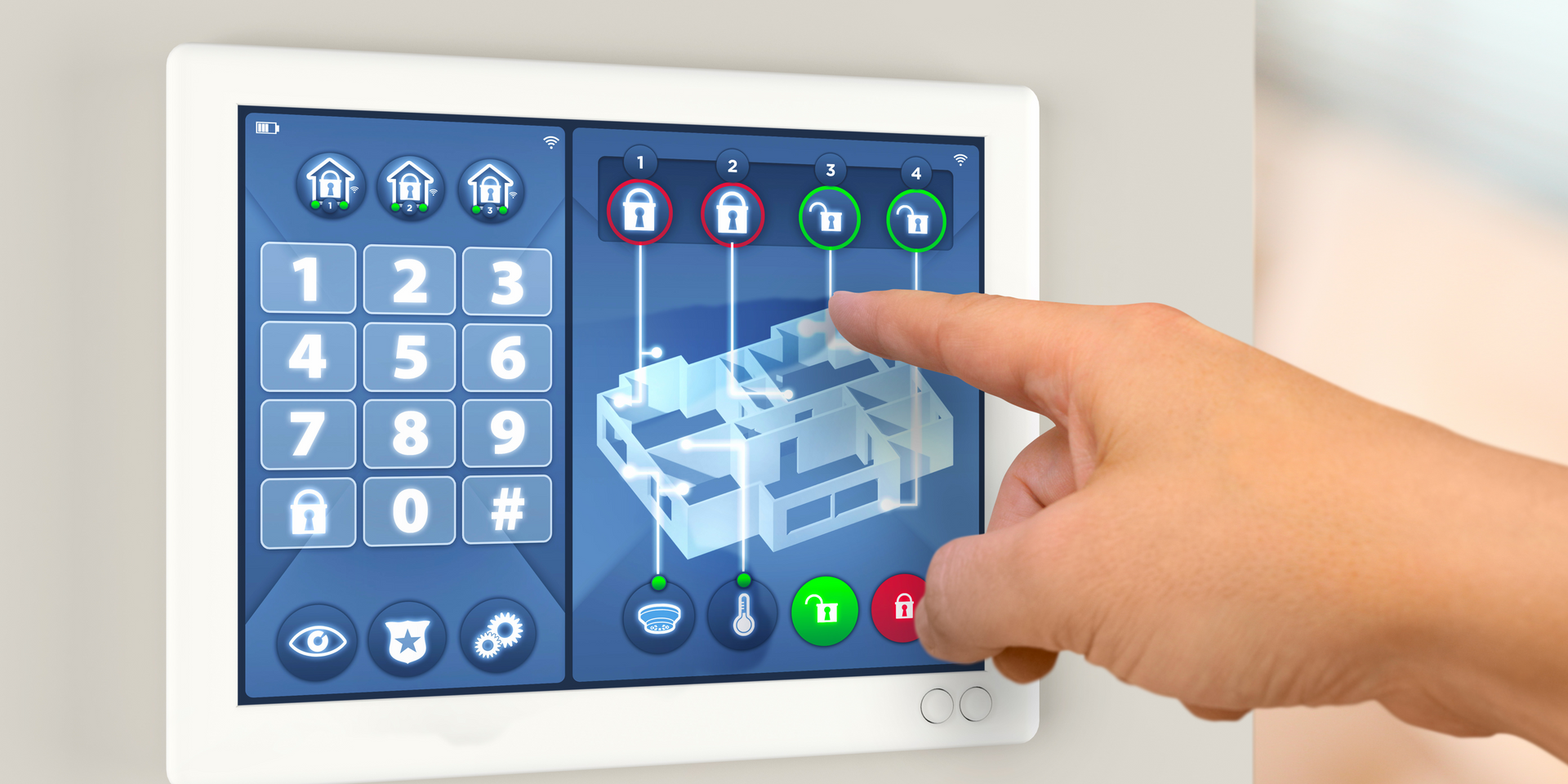
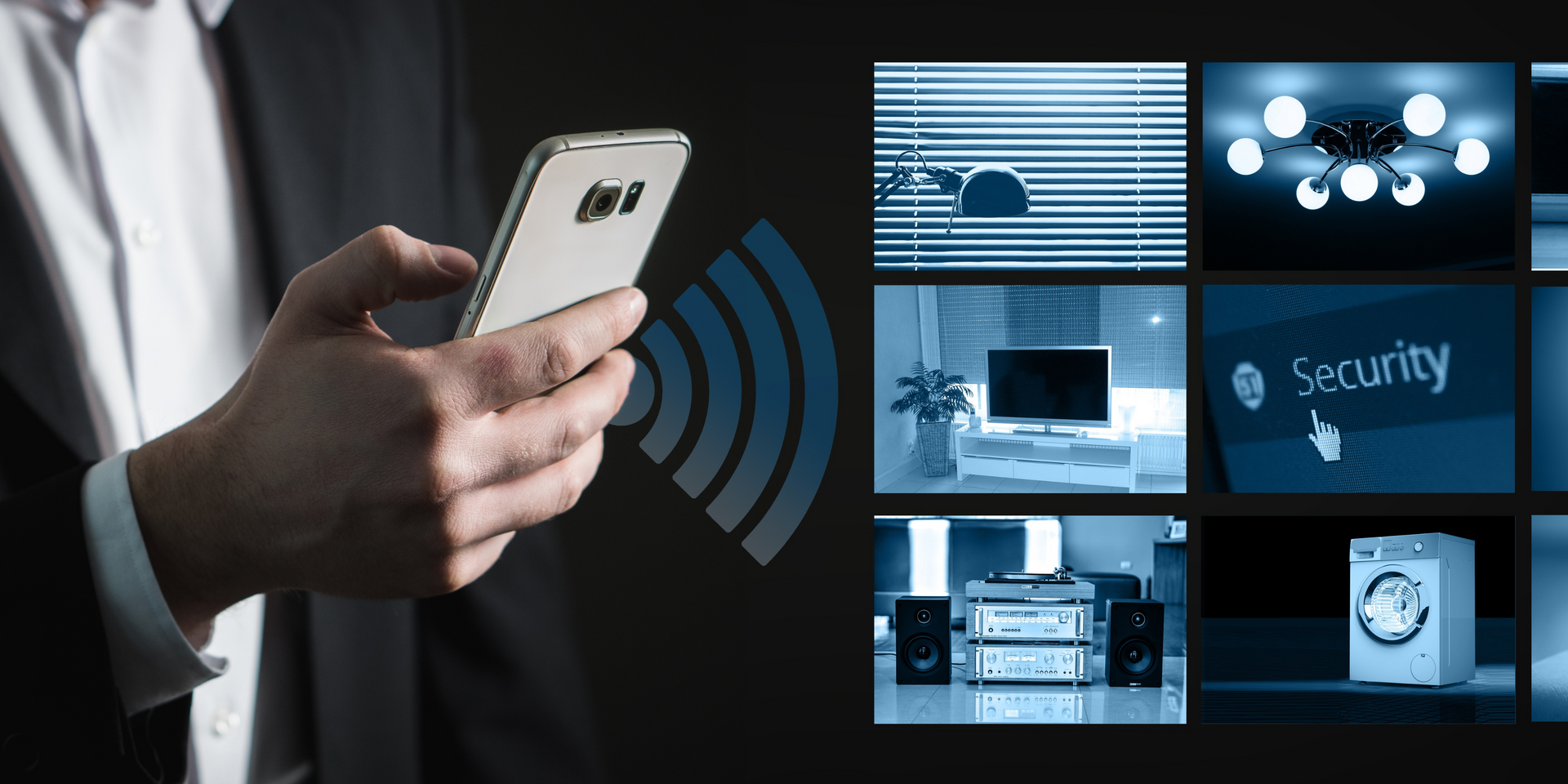
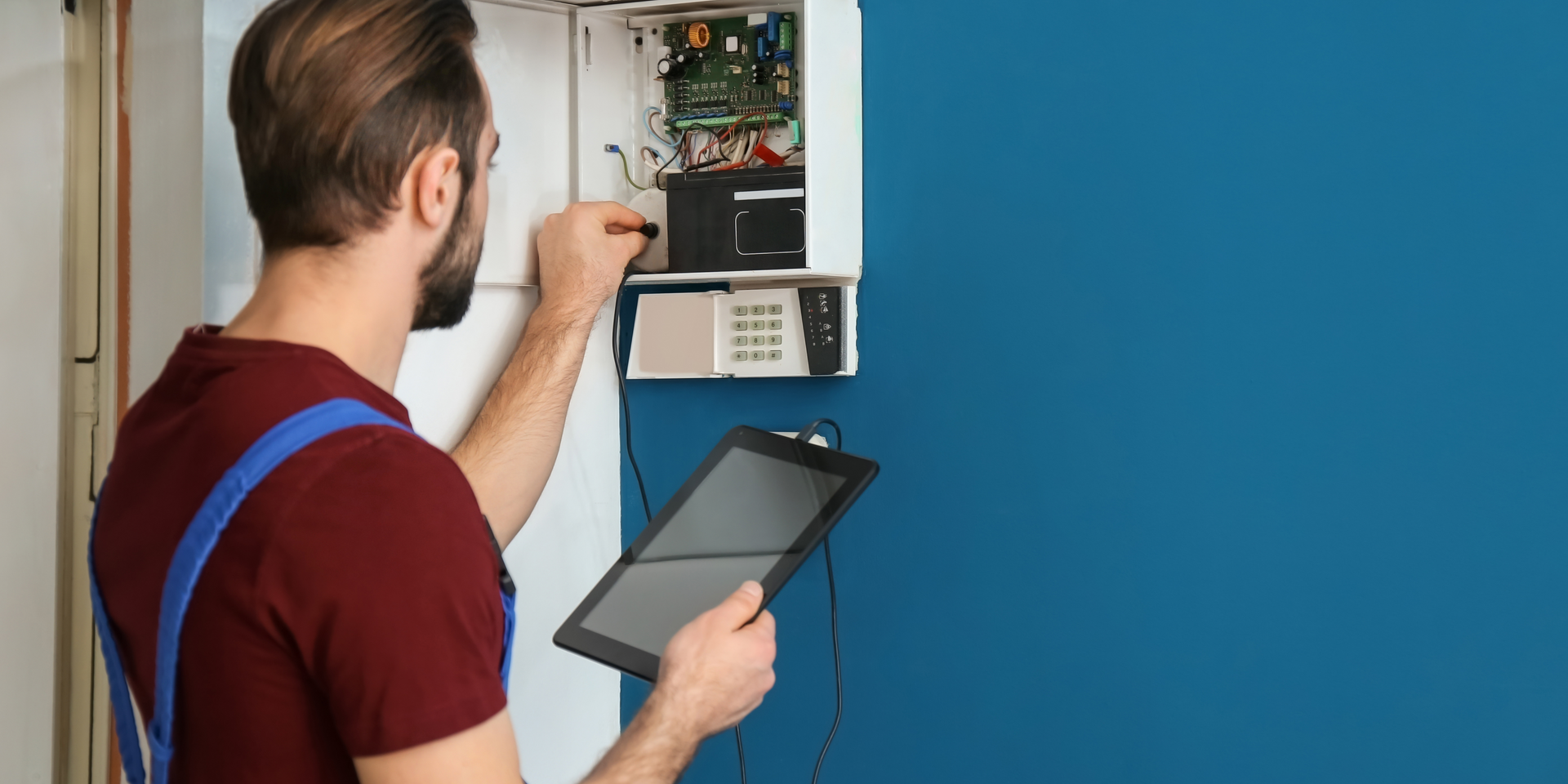