Industry 5.0 Examples
Industry 5.0 Examples
The term "Industry 4.0" refers to the fourth industrial revolution, characterized by the integration of digital technologies into manufacturing processes. It encompasses a wide range of technologies such as artificial intelligence, internet of things, cloud computing, and big data analytics.
The concept of "Industry 5.0 meaning" is an extension of Industry 4.0 and focuses on the collaboration between humans and machines in the manufacturing industry. It emphasizes the importance of human skills and creativity alongside advanced automation technologies.
When it comes to understanding the meaning and impacts of Industry 4.0 and Industry 5.0, there are numerous resources available in various formats such as PowerPoint presentations (PPTs), case studies in PDF format, and even essays discussing these topics.
To provide you with some examples of Industry 4.0 applications, companies have been implementing smart factories where machines communicate with each other through IoT devices to optimize production processes. Additionally, augmented reality is being used for training purposes in industries like aerospace and automotive.
As for the benefits of Industry 5.0, it aims to create more meaningful jobs that require human skills such as critical thinking, problem-solving, and creativity while leveraging technology for increased productivity.
It's important to note that there are many case studies available that provide detailed insights into specific industries or companies' experiences with implementing Industry 4.0 practices or transitioning towards Industry 5.0 principles.
Overall, exploring these resources will help you gain a comprehensive understanding of the meaning behind Industry 4.0 and its impacts on various sectors while also shedding light on emerging trends related to Industry 5.0 concepts.
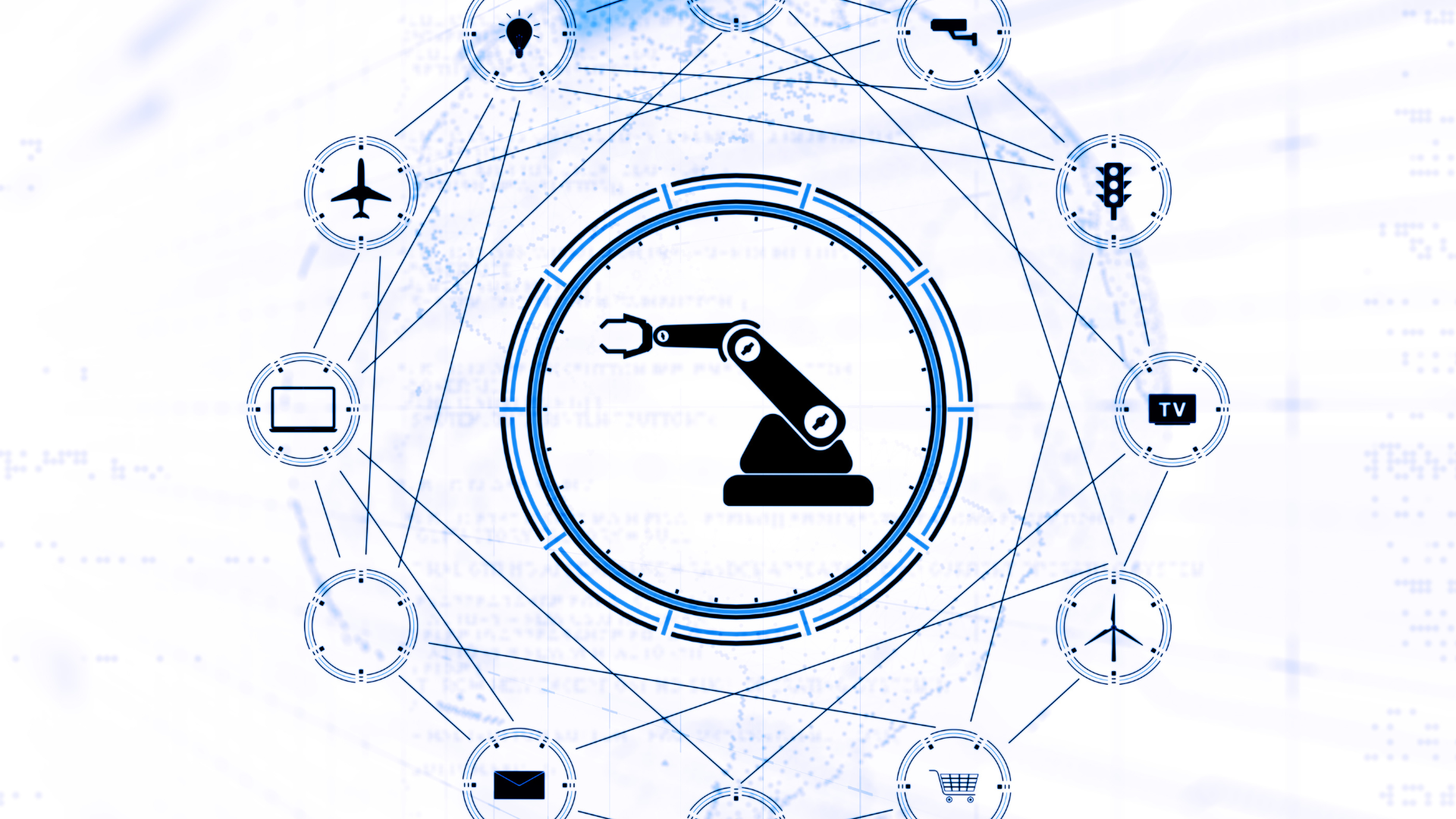
Industry 4.0, also known as the Fourth Industrial Revolution or Industry 4.0, refers to the ongoing automation and digitization of traditional manufacturing and industrial practices. It involves the integration of advanced technologies such as artificial intelligence, Internet of Things (IoT), cloud computing, robotics, and big data analytics into industrial processes.
The term "Industry 4.0" was coined in Germany to describe a strategic initiative aimed at transforming manufacturing through the use of smart technologies. It represents a shift towards smart factories that are interconnected and capable of autonomous decision-making.
Some examples of Industry 4.0 technologies include:
1. Internet of Things (IoT) sensors: These sensors collect real-time data from machines and devices on the factory floor, enabling better monitoring and predictive maintenance.
2. Robotics and automation: Intelligent robots can perform repetitive tasks with precision and speed, improving productivity.
3. Additive manufacturing (3D printing): This technology allows for rapid prototyping and customization of products.
4. Artificial intelligence (AI) and machine learning: AI algorithms can analyze large amounts of data to optimize production processes, detect anomalies, or predict maintenance needs.
5. Cloud computing: Cloud-based platforms enable real-time collaboration between different stakeholders in the manufacturing process.
6. Big data analytics: Advanced analytics techniques can extract valuable insights from vast amounts of data collected during production.
Industry 4.0 standards are being developed globally to ensure interoperability between different systems and devices used in smart factories.
It is worth mentioning that there is no specific concept called "Industry 50". However, it is possible that it may refer to a hypothetical future stage beyond Industry 4.0 where even more advanced technologies are utilized in industrial settings.
For further information on Industry 4.0 technology concepts, you may refer to PDF resources available online that provide detailed insights into its meaning, applications, benefits, and challenges faced by industries embracing this revolution.
Industry 4.0, also known as the Fourth Industrial Revolution, refers to the integration of advanced technologies and automation into various industries. It encompasses the use of artificial intelligence, machine learning, Internet of Things (IoT), big data analytics, and robotics to transform traditional manufacturing and supply chain processes.
In simple words, Industry 4.0 represents a new era where machines and systems are interconnected, allowing for increased efficiency, productivity, and flexibility in manufacturing and supply chain operations. It involves the digitization of processes and the utilization of real-time data to optimize decision-making.
Industry 4.0 has a significant impact on people within the supply chain ecosystem. While it introduces automation that can replace certain manual tasks, it also creates new job opportunities that require specialized skills in managing advanced technologies. Additionally, Industry 4.0 enables greater customization in production processes, resulting in more personalized products for consumers.
ResearchGate is an online platform where researchers can share their work and collaborate with others in their field. It serves as a valuable resource for accessing research papers related to Industry 4.0.
As for Industry 5.0 or "Industry Renaissance," it is a concept that focuses on human-machine collaboration rather than complete automation seen in Industry 4.0. McKinsey & Company is a global management consulting firm that provides insights into various topics including industry trends and transformations.
Overall, Industry 4.0 represents a transformative shift in how industries operate by leveraging advanced technologies to enhance efficiency, productivity, and innovation within supply chains.
You might also like
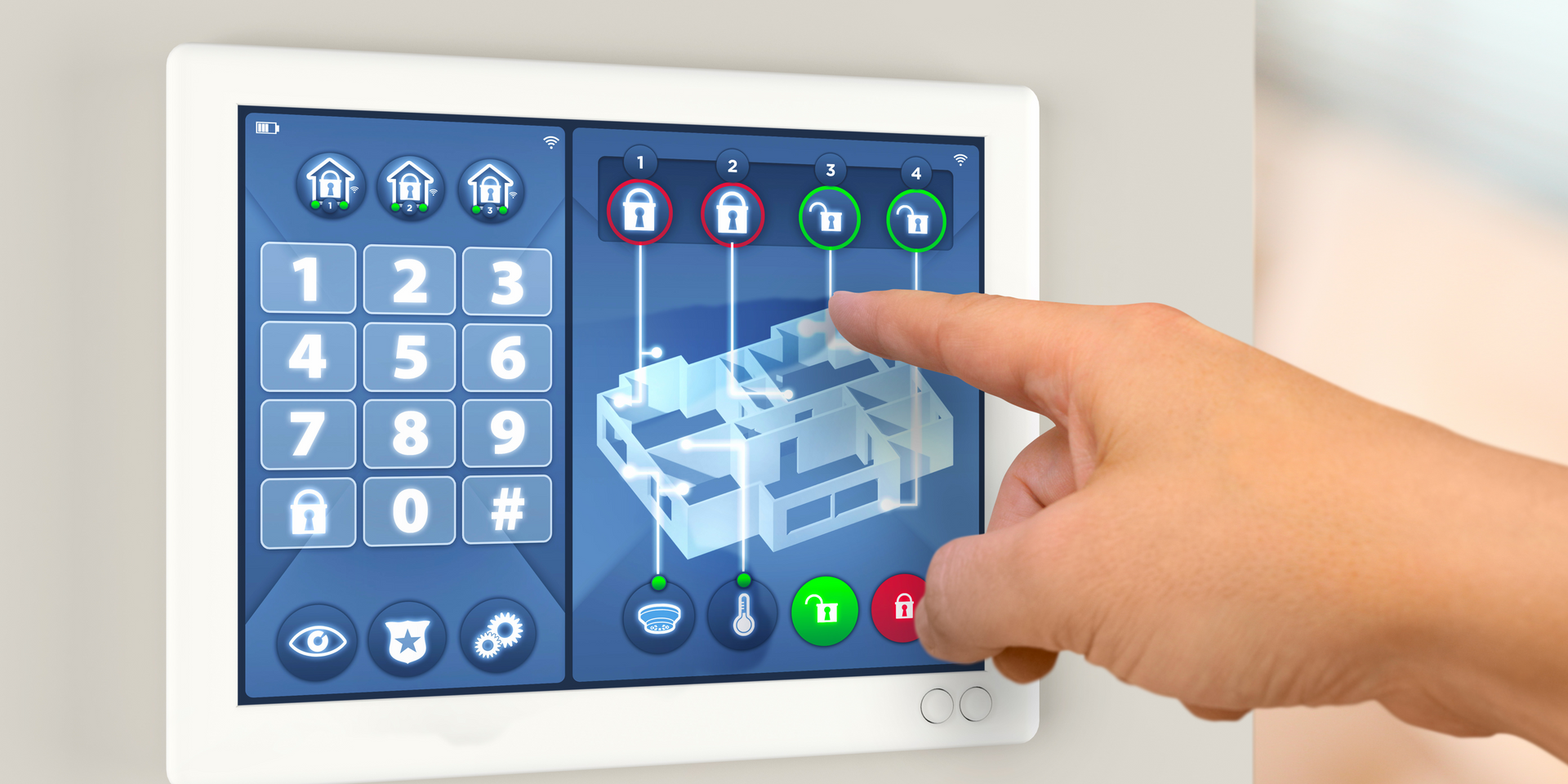
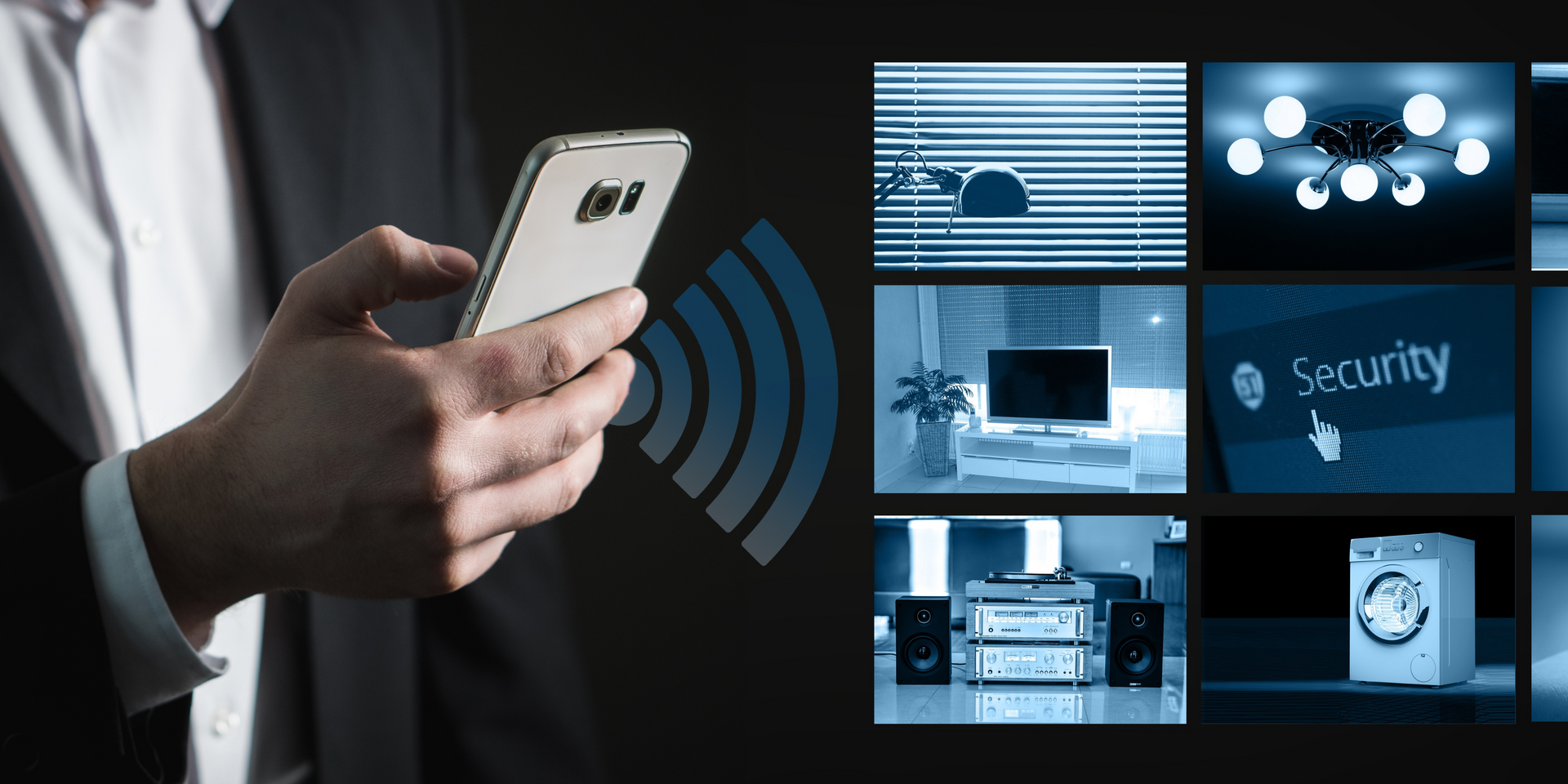
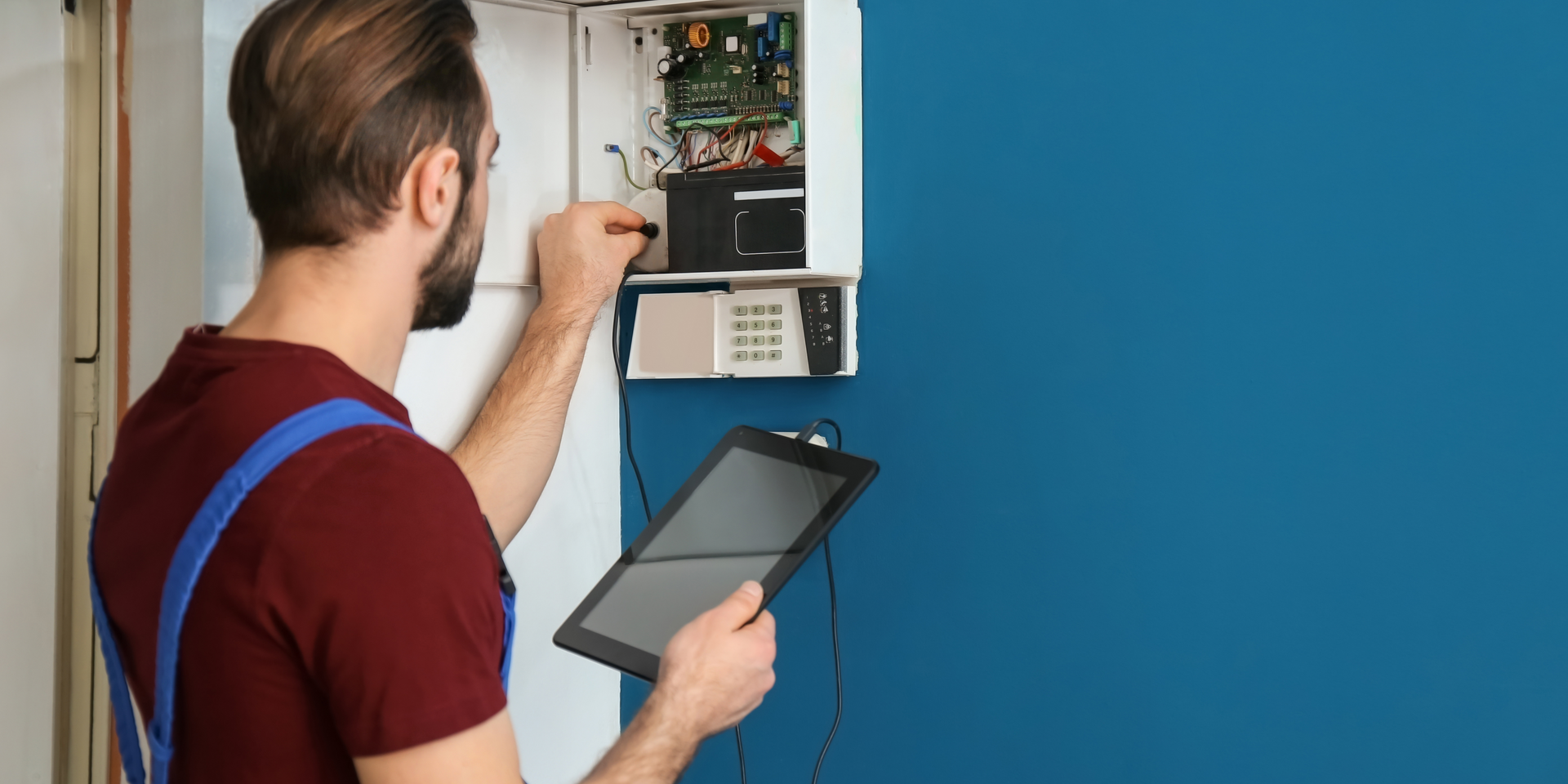