MES (Manufacturing Execution Systems)
MES (Manufacturing Execution Systems) are advanced software systems used to improve capacity, quality, transmission, and visibility. These elements are used to create a production management system that can help you improve productivity, track and synchronize plant resources, and empower business systems and people with real-time information about what’s happening in its production.
Fundamentals of the MES (Manufacturing Execution Systems)
A manufacturing execution system application is composed of three basic elements:
- Database: centralized, relational, and with robust production
- Business rules: analyzed through a mechanism that enforces customer-specific production processes
- View: real-time information reports showing real results
These elements of a manufacturing execution system can affect the following business functions:
- Capacity: improve the production volume of machines and people’s productivity
- Quality: monitor products and processes to identify causes and eliminate errors
- Transmission: meet schedules with better coordination and communication throughout the factory
- Visibility: Track and control what you can see
If you want to connect, manage, validate and optimize your production, the answer is yes. A comprehensive manufacturing execution system, which can be purchased as a specific solution for single or multiple plants and even for industrial facilities, can help you meet a variety of productivity, quality, compatibility, and cost reduction goals.
MES (Manufacturing Execution Systems) improves your manufacturing operation to drive your production goals. Whether it’s compliance regulations, excessive work in process, or inefficient use of resources, increasing production costs in your profits. Instead of worrying about paperwork or tracking approvals, focus your energy on achieving operational goals.
MES (Manufacturing Execution Systems) combines documents, equipment, and materials management in electronic work procedures to form an optimized manufacturing environment for Life Science organization.
Main Objective of ME
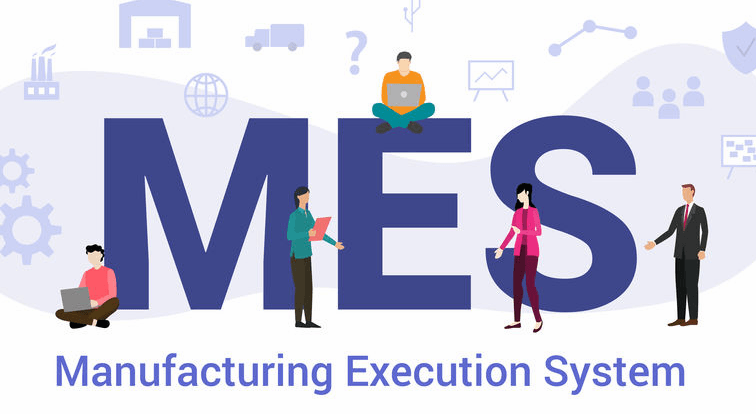
The main objective of an MES is to increase productivity by optimizing processes and making better use of available resources. Its particularities vary according to the types of product produced, the production volume, the profile of customers and suppliers, as well as the quality and control standards implemented. They are positioned on a demand for communication between ERP systems ( Enterprise Resource Planning ) and SCADA systems ( Supervisory Control and Data Acquisition ). Even acting in this operational niche of informative treatment, MES systems are not simple links between ERP and automation, since they also guarantee the implementation of manufacturing because, due to their position, they provide relevant indicators in real-time of the state of production.
In addition to the essential functions of production execution, it also provides several functions, such as planning, machine data acquisition (MDA – Machine Data Acquisition ), production data acquisition (PDA – Production Data Acquisition ), energy monitoring, health monitoring, maintenance, and traceability. They are considered key technologies to improve manufacturing capacity, fundamental to long-term corporate goals, but with obvious short-term impacts on the performance of organizations. With integrated MES systems, the manufacturing process is guided by an efficient information network, becoming a key element both for productivity and for the company’s financial viability.
The MES concept is very broad, however, as mentioned above, its objectives are simple: to optimize processes and improve the use of production resources. However, this simplicity regarding the objectives contrasts with complex integration and a diversified approach, to find the best solution for the configuration of the evaluated industrial plant. The implementation of an integrated MES (Manufacturing Execution Systems) system in the industrial plant provides a broad view of operations, allowing real-time data to be related to other information systems, such as production planning and distributed control systems.
You might also like
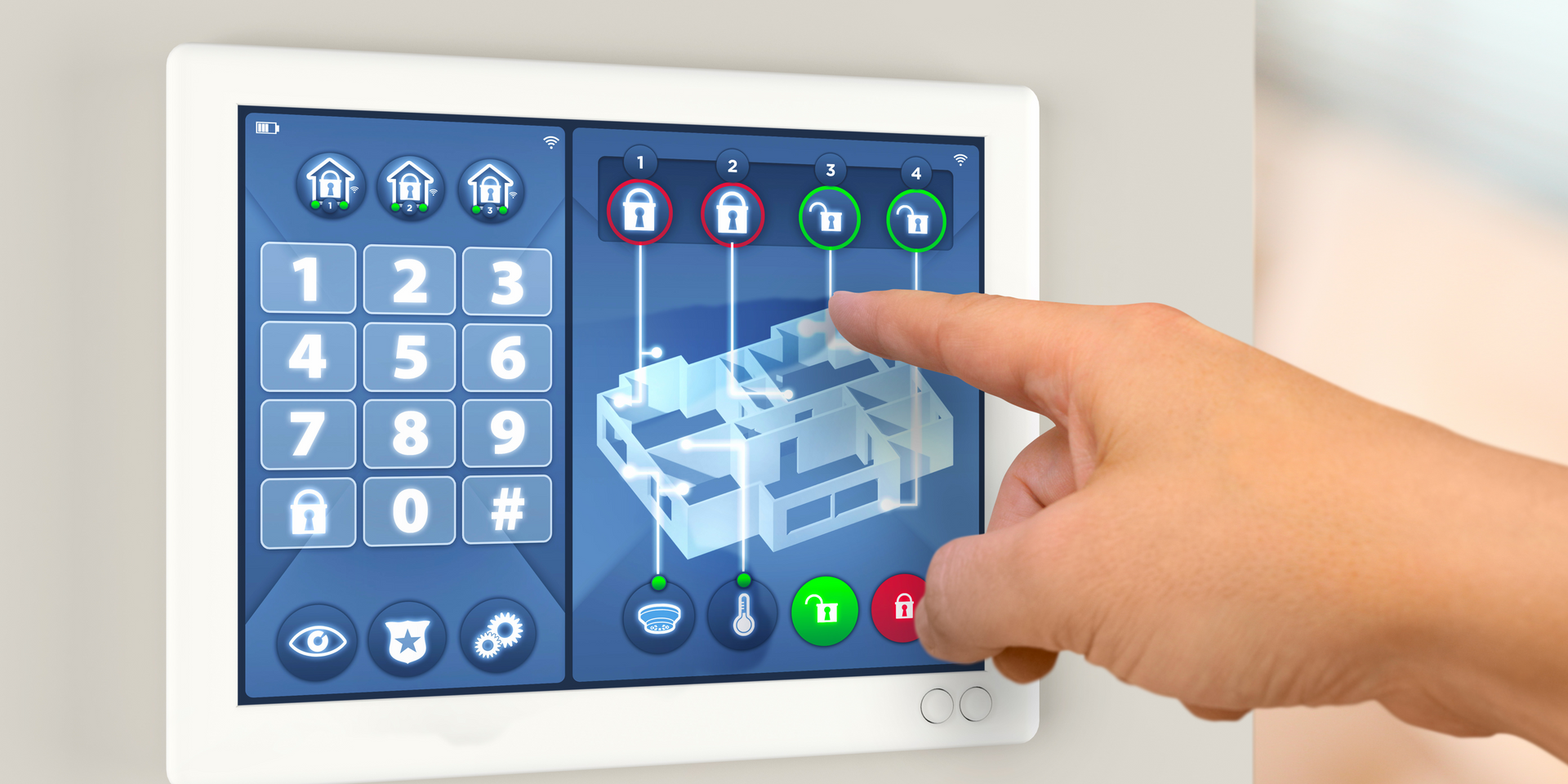
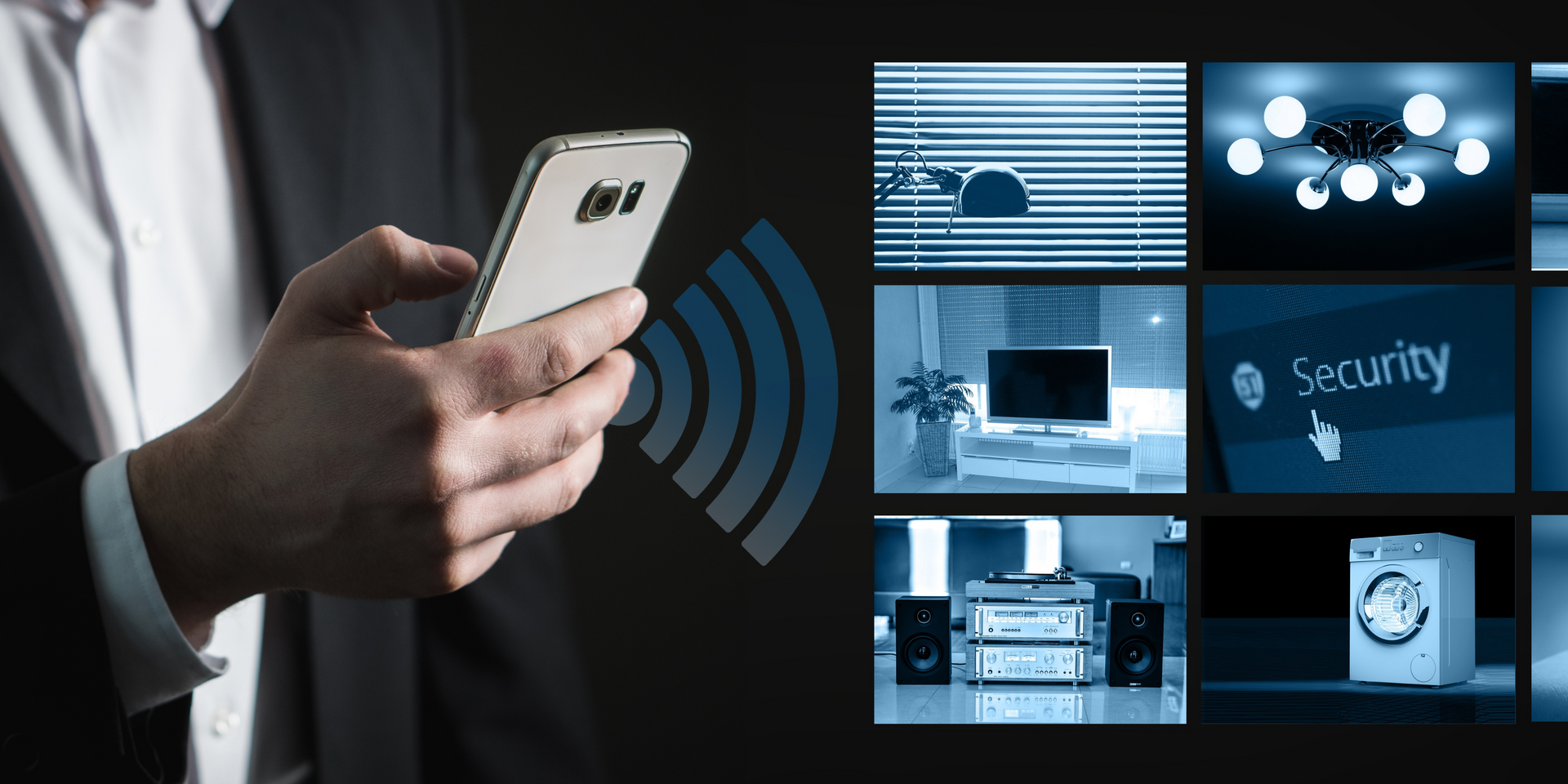
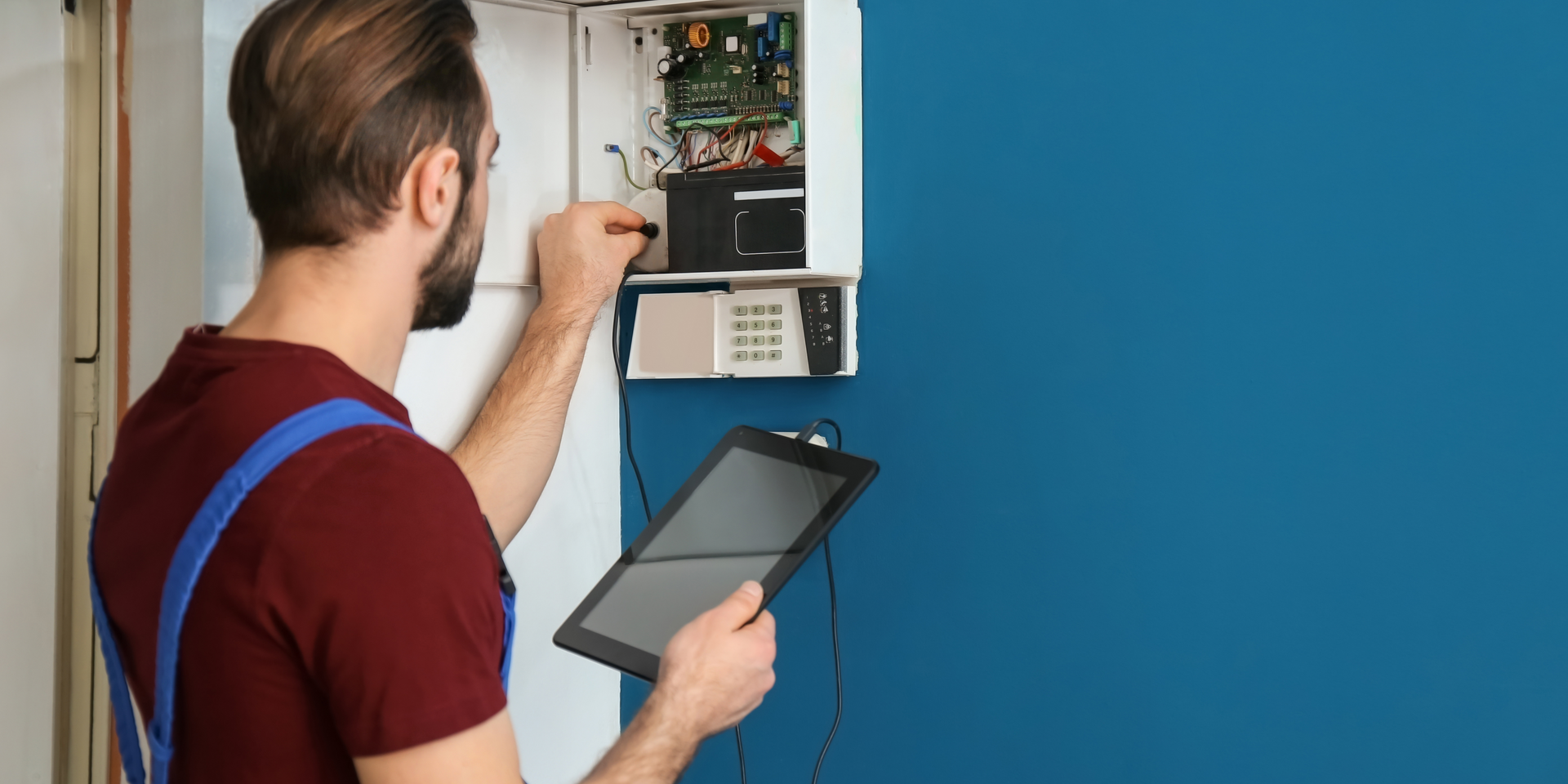