OEE (Overall Equipment Effectiveness or Total Equipment Effectiveness)
In definition, the OEE is an indicator that measures the efficiency of industrial machinery and is positioned as a key tool for the philosophy of continuous improvement in a company.
For companies, there has always been the need to be able to quantify the productivity and efficiency of production processes, which is why this indicator was born with the ability to indicate, using a percentage, the real effectiveness of any production process. It is a relentless tool when it comes to detecting inefficiencies that originate during a production process. Let us bear in mind that what is measured can be managed and improved.
Certainly deciding to measure OEE in your production plant is an indication that you are on the road to increasing production.
To measure the OEE in your plant there are 3 ways; Manual, traditional automatic, and modern automatic.
Manual Capture
To measure OEE manually, you must make a format and use it on each machine to be tested. The important data in the format are:
- Production Order
- Machine Setup
- Production Time
- Units Produced
- Amount of Waste
- Stops (Time)
These data must be measured for each shift that the machine is running and times must be entered each time they occur (never at the end of the shift) with a clock in hand.
Then at the same time every day, a team in charge of entering the data in Excel (or another platform for this), will deliver data to the production analyst and he will generate a daily production report. Then a monitoring committee must check that the information is up-to-date and up-to-date.
A team of digitizers will be in charge of collecting these forms always at the same time and entering them into an Excel format to deliver them to the production analyst who will generate a daily production report. Then, you should organize a monitoring committee that, in no more than 5 minutes, checks that the information is up-to-date and up-to-date.
With the data in this report, you will apply the OEE formula:
Availability x Performance x Quality = OEE
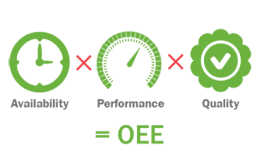
Availability: Is the percentage of the time that the machine was operational. For example, if in an 8-hour shift, the machine was producing 6 functional hours, it will have an Availability of 75%.
Yield: These are the units produced compared to the cruising speed of the machine. For example, if the equipment has a production capacity of 10 units per minute, but actually produced 8, it will represent a yield of 80%.
Quality: Is the percentage of the total production that is produced without defects. For example, if out of 1000 units produced, 100 do not meet the standards, the Quality will be 90%.
Advantages:
- Raises awareness among operators about its indicators
- It allows implementing Lean Manufacturing tools
- Faster implementation
Disadvantages:
- Long learning curve
- Inaccurate information
- Delayed response time
- Long implementation time
- Information and indicators are not standardized between plants
Traditional Auto-Capture
To measure OEE in a traditional automatic way, some physical adjustments must be made that consist of:
- PLCs for each machine, a different adaptation is needed depending on the technology of each one. It is necessary to configure a software that interprets the information of all the PLCs in a standard
- Server infrastructure where the information is collected (SCADA and HISTORIAN licenses)
- Second level of servers where the information is processed and sent to the control center/(MOM, MES, EDM SYSTEMS)
- Unit where the ERP is located, which will be reviewed by the team in charge of the plants
The data collected with this method is much more complete and has a longer history than the manual method. Key indicators, such as the OEE, will be calculated automatically.
Advantages:
- Shorter learning curve than manual capture
- Accurate information
- Standardized information between plants
Disadvantages:
- It requires specialized equipment and infrastructure
- Complex maintenance
- Very high costs in the market
Modern Auto Capture
To measure OEE in a modern automatic way, you must implement a sensor (in most cases independent of the plc you have) in each machine you want to measure, install specialized software where all the sensors will report, and make an initial configuration, consisting of:
- Machine cruising speed
- It is recommended to choose 30 possible causes of machine stoppage
The software will take care of taking the times automatically, of keeping the count of the units produced and the defective units. In addition, it will ask the operator the reason for each stop each time it occurs (he will choose from the 30 recommended that were configured).
Finally, the software will automatically generate the reports and calculate the OEE, making it available to the people involved through screens in the plant and online files.
Advantages:
- It costs less than traditional automatic capture
- Few or no infrastructure equipment
- It is naturally impregnated with good measurement, calculation, and reporting practices
- You can take advantage of the existing infrastructure in the plant
- Industry 4.0 processes
- Easy maintenance
Disadvantages:
- Can’t remotely control machines
- It does not calculate all the variables of the machines
Thus, we can affirm that the OEE indicator should be an essential tool in all the processes carried out in a plant committed to continuous improvement.