What Are the Advantages of OPC Protocol?
What Are the Advantages of OPC Protocol?
The OPC (OLE for Process Control) protocol, which stands for OLE (Object Linking and Embedding) for Process Control, is a highly popular and extensively utilized communication standard in the realm of SCADA (Supervisory Control and Data Acquisition) systems. This protocol plays a pivotal role in enabling seamless communication and data exchange between various industrial automation devices and software applications. By adhering to the OPC protocol, SCADA systems can efficiently monitor, control, and acquire data from diverse processes across different industries such as manufacturing, utilities, oil and gas, and more. OPC SCADA provides a standardized framework that ensures interoperability between different hardware vendors' devices and software applications, allowing for easy integration and compatibility. It provides a standardized way for different industrial automation devices and software applications to communicate with each other.
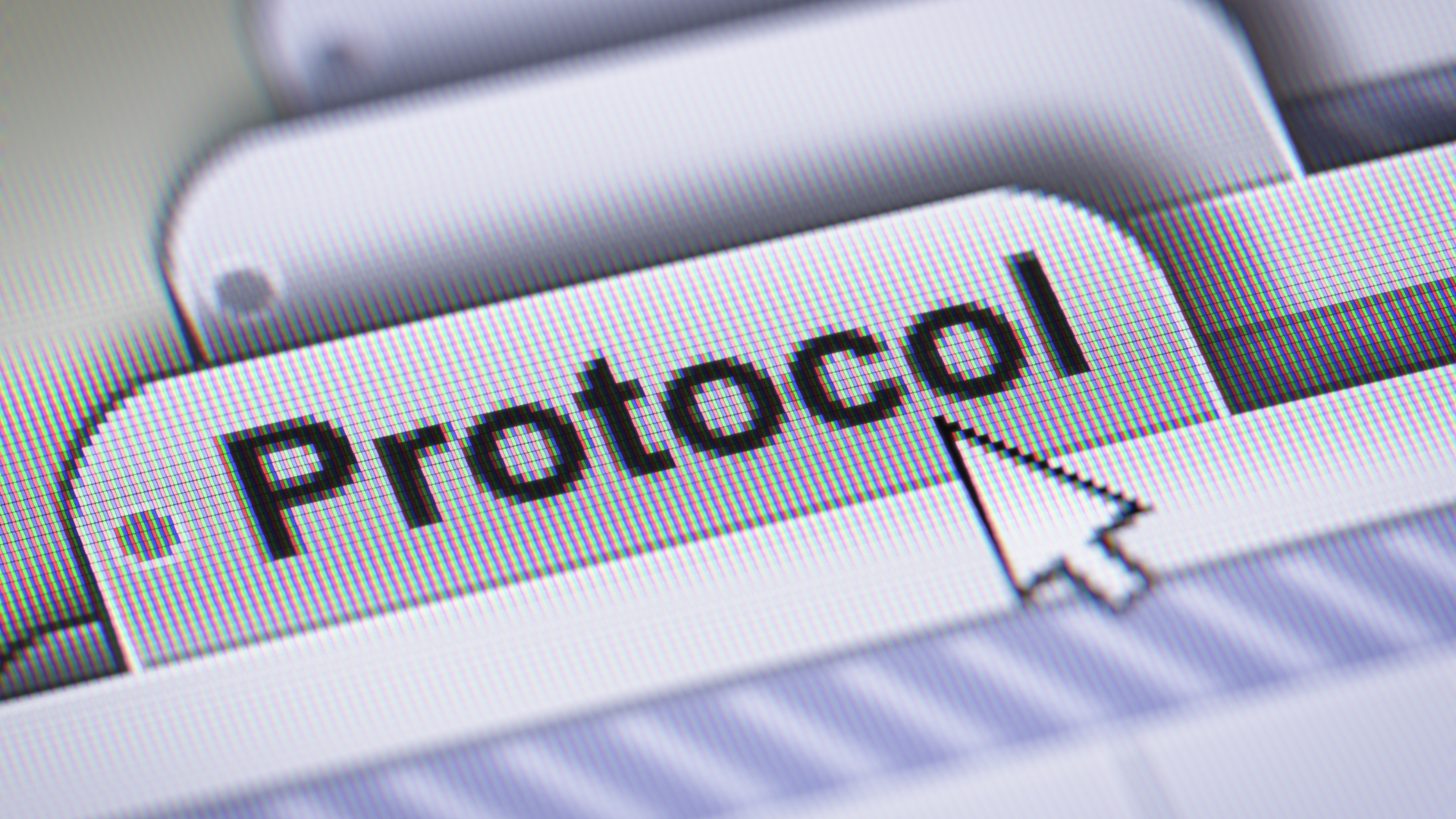
One of the notable advantages of utilizing the OPC (OLE for Process Control) protocol is its remarkable level of interoperability. This means that systems and devices from different manufacturers can seamlessly communicate with each other, regardless of their brand or origin. This interoperability feature ensures a smooth integration and compatibility across various platforms, resulting in increased efficiency and flexibility in industrial automation processes. By employing the OPC protocol, businesses can easily connect disparate systems, enabling them to exchange data and share information effortlessly. It allows devices and software from different manufacturers to seamlessly exchange data, regardless of the underlying communication protocols or operating systems they use. This makes it easier to integrate various components of a SCADA system, reducing compatibility issues and simplifying maintenance.
The OPC (OLE for Process Control) protocol, commonly used in industrial automation systems, offers a wide range of benefits and flexibility when it comes to data access. This protocol allows users to easily connect and communicate with various devices and software applications, enabling seamless integration across different platforms. One of the key advantages of OPC is its ability to provide real-time access to data from diverse sources such as sensors, actuators, PLCs (Programmable Logic Controllers), and other industrial devices. This accessibility ensures that critical information can be collected and utilized efficiently for monitoring, control, and optimization purposes. Furthermore, the flexibility provided by the OPC protocol allows users to choose between different communication methods such as COM/DCOM (Component Object Model/Distributed Component Object Model) or web services based on their specific requirements. This adaptability ensures compatibility with a wide range of hardware and software systems commonly used in industrial environments. In addition to its versatility in terms of data access, OPC also offers robust security features to safeguard sensitive information. Encryption techniques ensure that data transmitted over networks remains confidential and protected from unauthorized access. Overall, the OPC protocol's flexibility in facilitating data access is highly valued in industries where efficient communication between different devices and software applications is crucial for optimal operational performance. It supports both real-time and historical data access, enabling users to monitor and analyze process variables in real-time while also providing access to historical data for trend analysis or troubleshooting purposes.
OPC UA
OPC UA (Unified Architecture) is an enhanced version of the OPC protocol that further improves security, scalability, and cross-platform compatibility. It incorporates modern technologies such as web services and XML into the communication framework, making it suitable for both local networks and cloud-based applications.
OPC Protocol Example
There are numerous instances where the OPC (OLE for Process Control) protocol has proved to be highly effective in various industries and applications. One such example is in industrial automation, where OPC facilitates seamless communication between different devices and software systems, enabling efficient monitoring and control of complex processes. In the energy sector, OPC is widely used to connect and integrate diverse systems such as power generation units, distribution networks, and SCADA (Supervisory Control And Data Acquisition) systems. This allows for real-time data exchange, leading to enhanced operational efficiency and better decision-making. Another area where OPC has proven its effectiveness is in building automation. By leveraging the protocol, building management systems are able to seamlessly communicate with HVAC (Heating, Ventilation, and Air Conditioning), lighting control systems, security devices, and other components. This enables centralized monitoring and control of various building functions, resulting in improved energy efficiency and occupant comfort. Moreover, OPC has found applications in the pharmaceutical industry as well. It plays a crucial role in facilitating data exchange between manufacturing equipment such as PLCs (Programmable Logic Controllers), MES (Manufacturing Execution Systems), SCADA systems, and other software platforms. This helps streamline production processes by ensuring accurate data collection and analysis for quality assurance purposes. In summary, the OPC protocol has proven its worth across diverse industries including industrial automation, energy management, building automation, pharmaceuticals – contributing significantly to enhanced operational efficiency while promoting seamless integration between different components of complex systems. For instance, in manufacturing plants, OPC servers enable communication between PLCs (Programmable Logic Controllers) on the shop floor and SCADA systems in control rooms. In energy management systems, OPC allows integration between smart meters, sensors, and software applications for efficient monitoring and control.
In the market, there is a wide range of commercial OPC server software options available that come with advanced features and comprehensive support services. These solutions usually have a cost associated with them. However, it is worth noting that there are also free alternatives like Matrikon OPC server or OPC Expert that offer basic functionality without requiring any licensing fees. These free options can be a viable choice for those who require standard OPC server functionality without the need for additional advanced features or dedicated support services. However, it's important to note that the availability of free versions may vary depending on specific vendors' policies.
In summary, the advantages of using OPC protocol include interoperability between different devices and software applications, flexibility in accessing real-time and historical data, enhanced security through protocols like OPC UA, scalability for large-scale systems, and the ability to integrate diverse components of a SCADA system.
You might also like
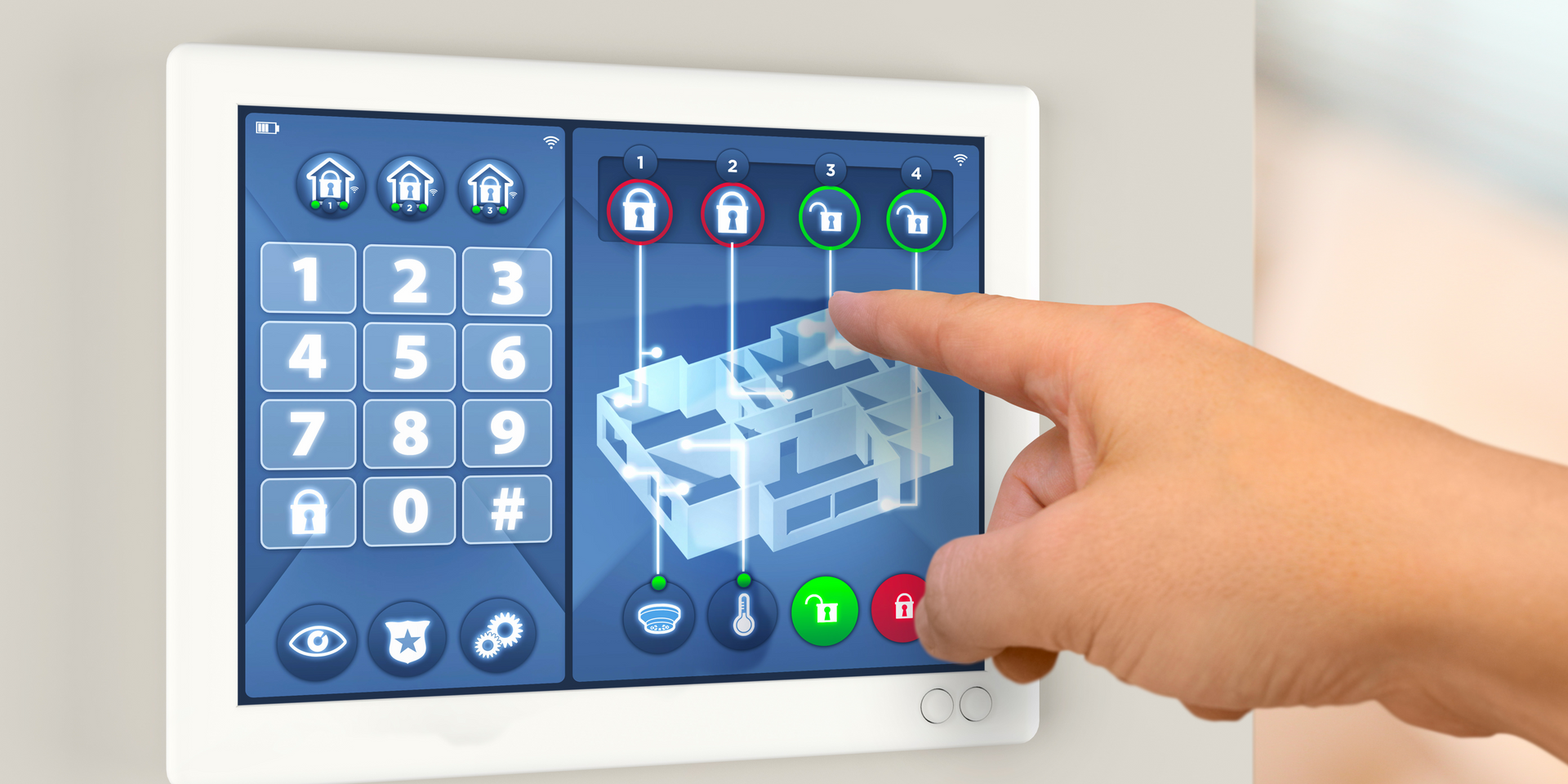
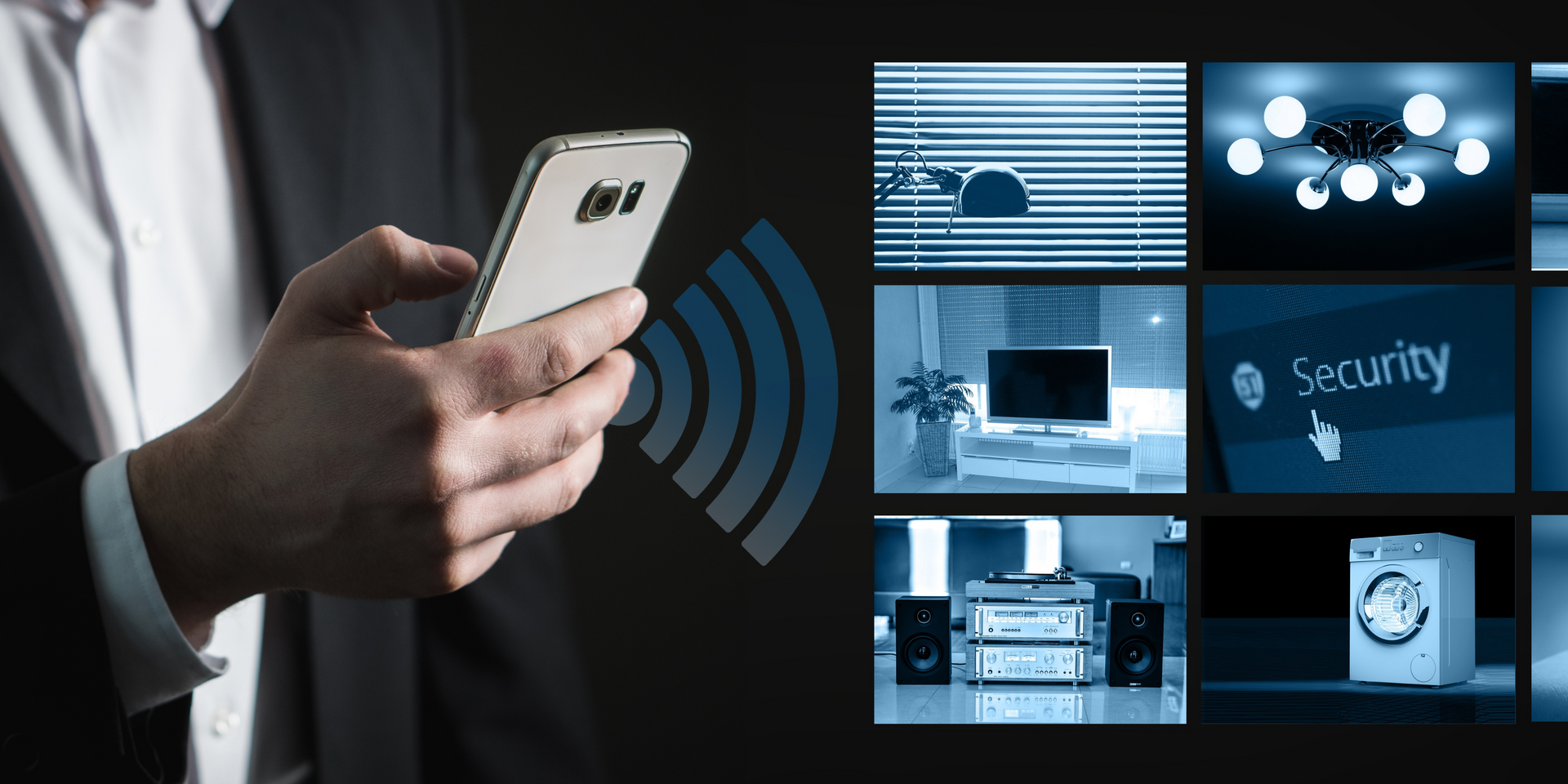
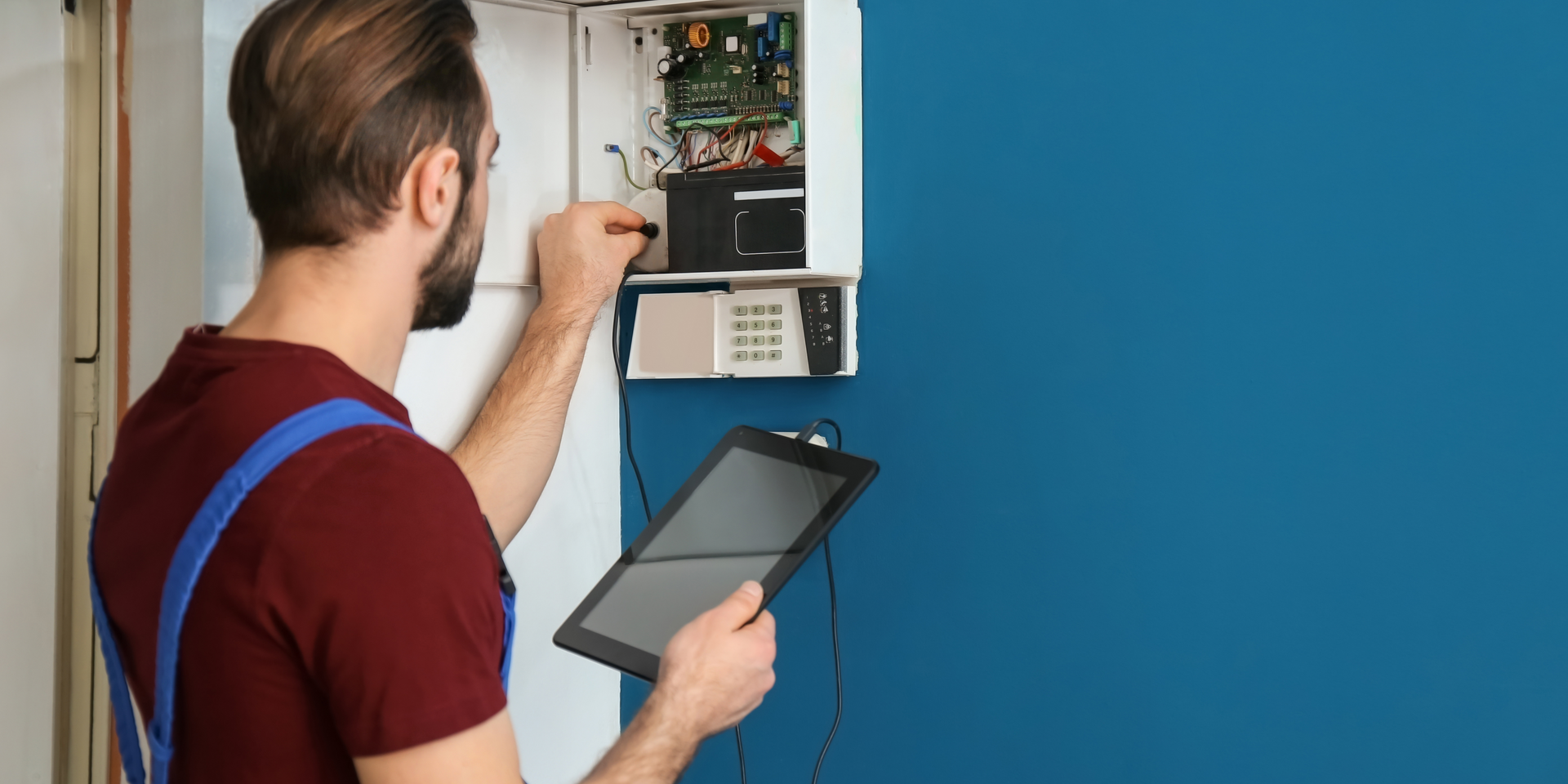