What is an Automation System
An industrial automation system is a system used to control and monitor a process, machine, or equipment in a computerized manner, often performing repetitive functions or actions. Automation systems and automation solutions operate in a wide range of applications, such as control and monitoring systems, data security applications, factory automation systems, manufacturing, automatic message response systems, and more. The operation of automated systems uses sensor systems, feedback control circuits, and automatic actuators. Automation system operation is the part of automation system control where manual processes are fully automated using special control machine schemes and logic. An automated system is a computer-controlled machine that uses a computer to perform control operations by collecting, processing, calculating, and controlling process variables.
At the same time, various automation tools such as CNC machine tools and industrial robots are used to automate the entire production process (including production, planning and control). The entire machine systems, from planning and design to product shipment, is fully integrated and automated. Industrial automation relies on various control systems for integrating each piece of process equipment or equipment into a larger system. Industrial automation uses control systems and equipment, such as computer software and robots, to perform tasks that used to be done manually.
Industrial automation is the use of control systems and information technology such as computers or robots to control various processes and machines in an industry to replace humans. Automation includes the use of various control systems to operate equipment such as machines, factory processes, thermal boilers and furnaces, ignition of telephone networks, control and stabilization of ships, aircraft and other applications, and vehicles with reduced human intervention. Automation covers applications ranging from home boiler control thermostats to large industrial control systems with tens of thousands of measurement inputs and control outputs. Automation software works in repetitive instructions and processes to complete tasks with little or no human intervention.
Programmable automation systems used by a system integrator can easily change job sequences and machine configurations through electronic control. In the case of fixed automation, the machining or assembly operations in the system are fixed by the equipment configuration, while in the case of programmable automation, the production equipment can change the sequence of operations to be able to handle different product configurations. In this type of automation, modification of a certain type of product, as well as assembly or mechanical operation, can be modified by changing the control program in the automation equipment. Stationary automation systems are mainly used in discrete mass production systems and continuous flow systems such as paint shops, distillation processes, conveyor lines and conveyor belts.
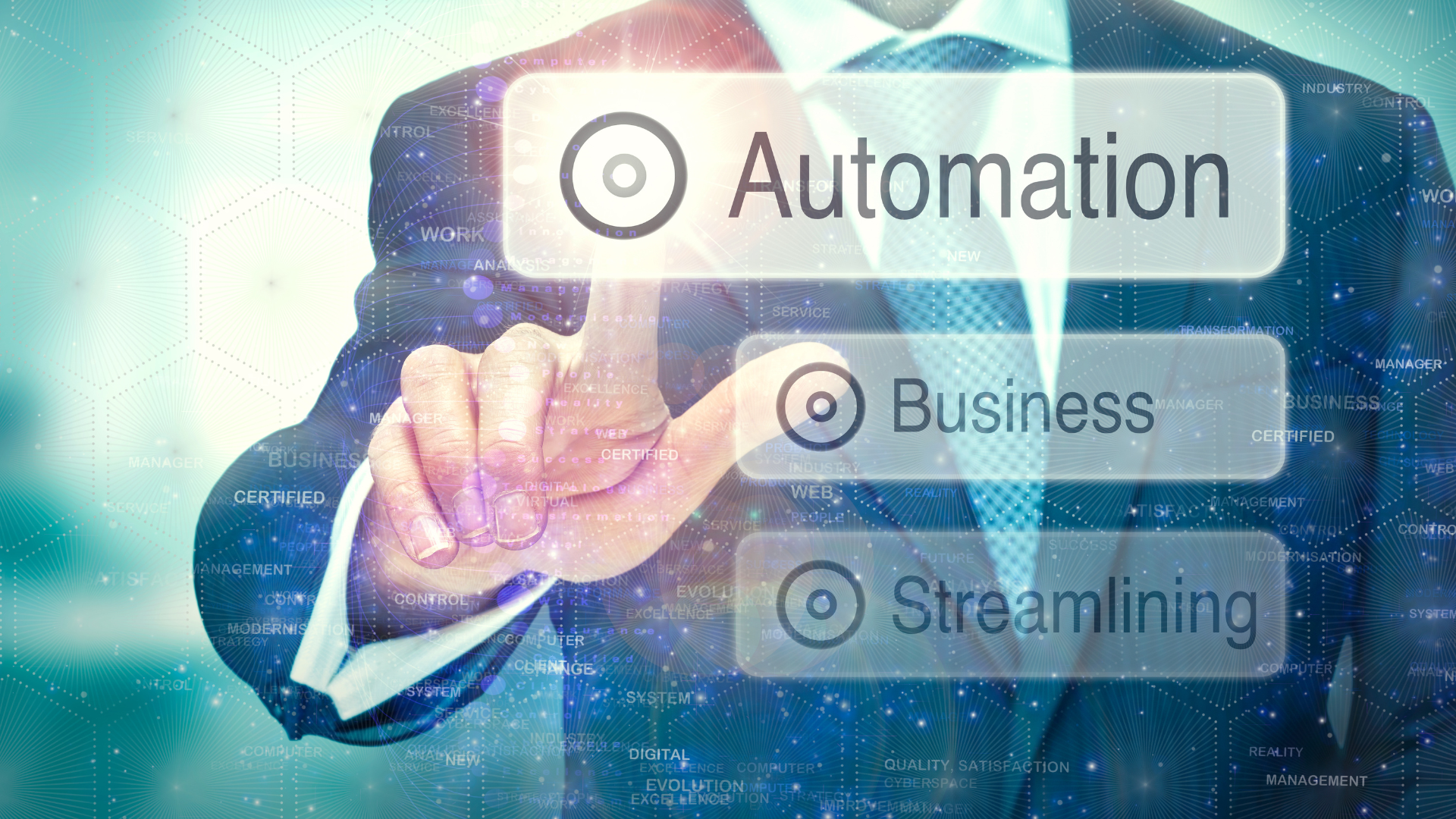
In a factory, we can automate production machines and tools, material handling equipment, control equipment, and even computer systems that control production operations. Automation can be included at every step of the line, from the initial blending or production of raw materials through production and processing to final packaging. Thanks to adaptive control and monitoring in various production steps and processes, industrial automation systems are useful in eliminating human errors and therefore in improving the quality and uniformity of the products offered.
You might also like
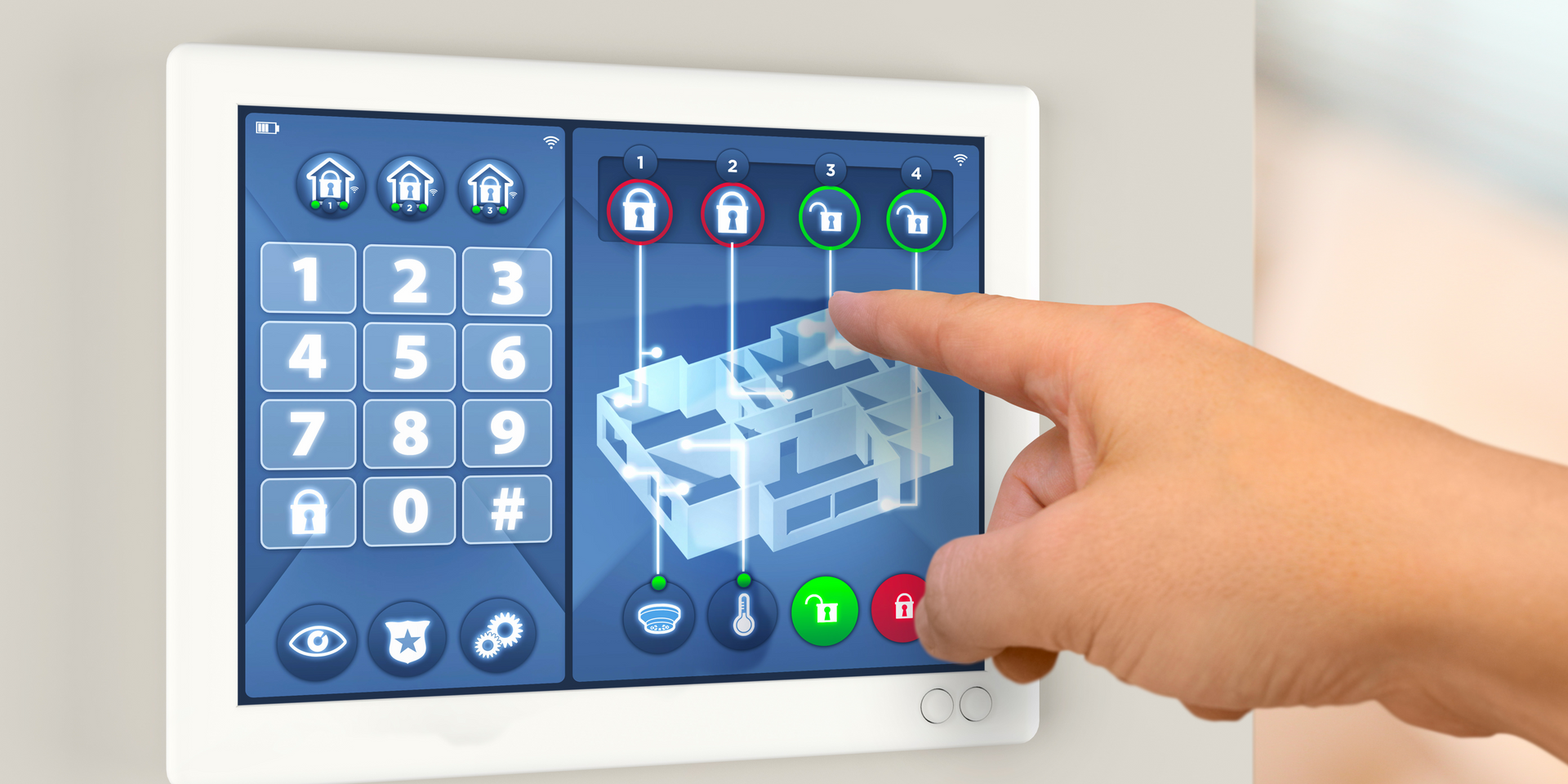
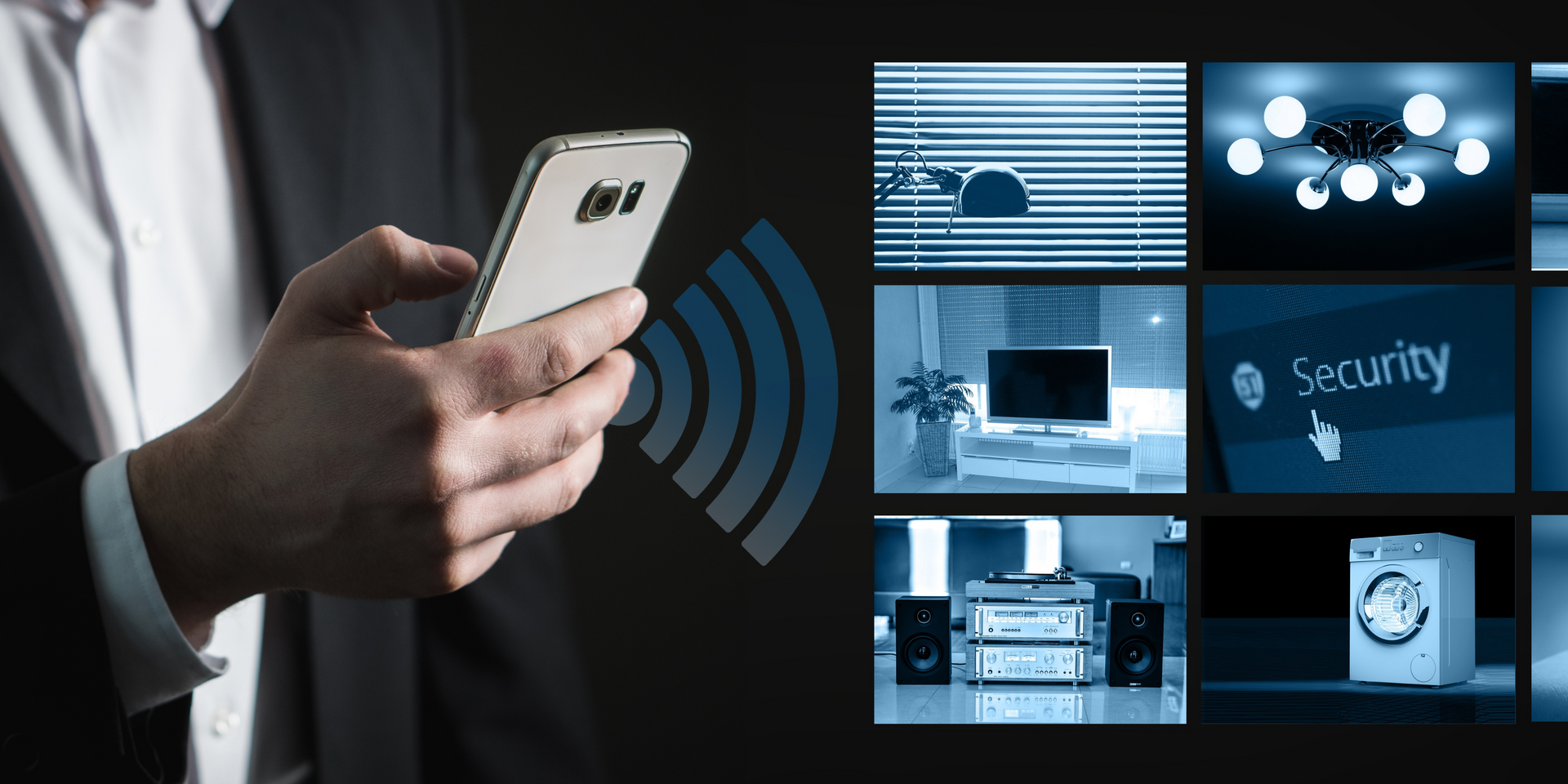
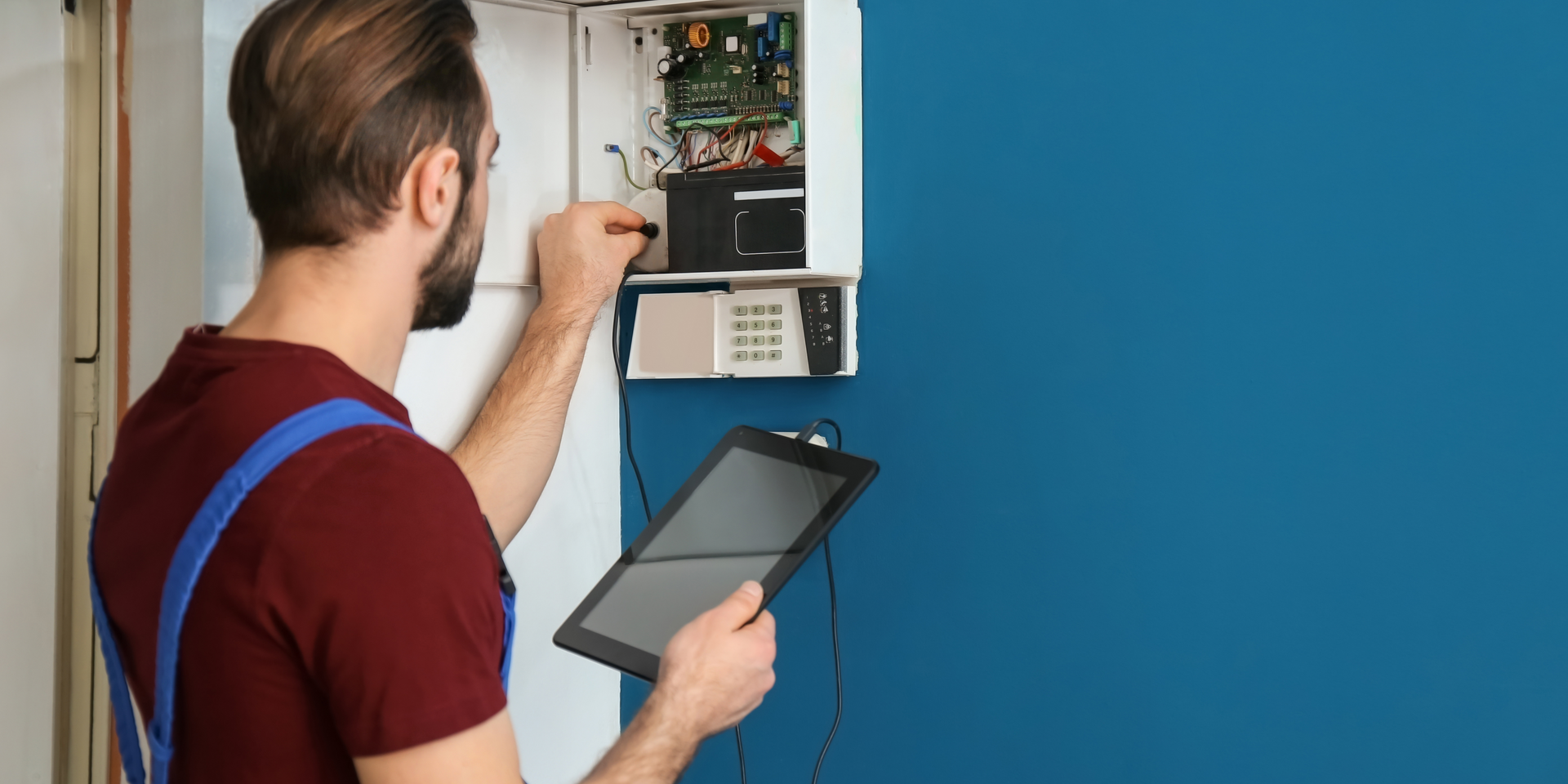