What is MES vs. SCADA vs. ERP?
What Is MES vs. SCADA vs. ERP?
Is SCADA an MES System?
No, SCADA (Supervisory Control and Data Acquisition) is not an MES but a system used to monitor and control industrial processes in real-time, focusing on equipment and machinery. MES (Manufacturing Execution System), on the other hand, manages the entire production process, from raw materials to finished goods, ensuring quality control and optimizing manufacturing workflows. ERP (Enterprise Resource Planning) is broader, integrating business functions like finance, supply chain, and HR to manage organizational resources. While SCADA focuses on machine-level control, MES manages production, and ERP oversees business operations, all serving distinct but complementary roles.
MES vs ERP
MES (Manufacturing Execution System) focuses on managing real-time production processes on the shop floor, including tracking work-in-progress, equipment performance, and quality control. ERP (Enterprise Resource Planning), on the other hand, handles broader business functions like finance, human resources, and supply chain management. While MES is specialized in optimizing manufacturing operations, ERP integrates various business processes across the organization. Together, MES and ERP systems complement each other by connecting shop floor activities with enterprise-wide planning and resource management.
ERP vs MES vs SCADA
ERP (Enterprise Resource Planning), MES (Manufacturing Execution System), and SCADA (Supervisory Control and Data Acquisition) serve distinct roles in industrial and manufacturing environments:
- ERP manages the overall business processes, including finance, human resources, procurement, and supply chain, integrating data across departments for organizational planning and decision-making.
- MES focuses on real-time management of production on the shop floor, overseeing tasks like work-in-progress tracking, equipment performance, and quality control, optimizing manufacturing operations.
- SCADA is primarily used for monitoring and controlling equipment and industrial processes in real-time, focusing on data acquisition and control at the machine level.
In short, ERP handles business operations, MES manages production processes, and SCADA controls equipment performance and monitoring. All three systems can integrate to ensure seamless information flow and efficient operations across the organization.
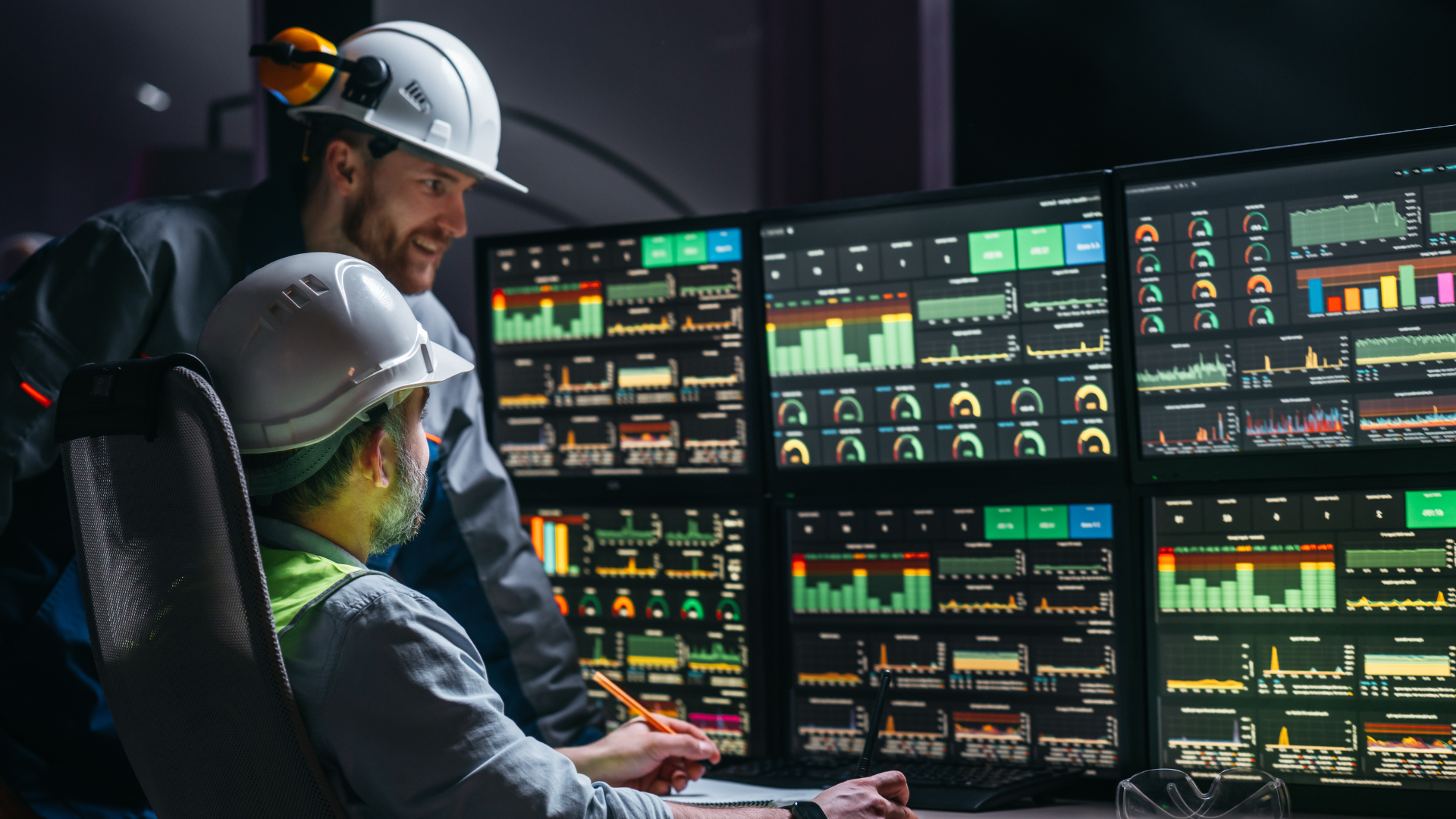
What Does ERP Mean?
MES ERP Meaning
MES (Manufacturing Execution System) manages real-time production processes on the shop floor, optimizing tasks like work-in-progress tracking and quality control. ERP (Enterprise Resource Planning), on the other hand, integrates broader business functions such as finance, human resources, and supply chain management. While MES focuses on manufacturing efficiency, ERP streamlines overall business operations. When combined, MES and ERP provide a comprehensive solution for managing both production and enterprise-wide activities.
MES Meaning
MES (Manufacturing Execution System) is a software solution that manages and controls manufacturing operations on the shop floor in real time. It focuses on optimizing production processes, tracking work-in-progress, monitoring equipment performance, and ensuring product quality. MES provides manufacturers with valuable insights to improve efficiency, reduce downtime, and maintain compliance with industry standards.
What Is The Difference Between MES and ERP?
The main difference between MES (Manufacturing Execution System) and ERP (Enterprise Resource Planning) is their focus: MES manages real-time production processes on the shop floor, optimizing tasks like work-in-progress tracking and quality control, while ERP handles broader business functions such as finance, human resources, and supply chain management. MES focuses on manufacturing operations, whereas ERP integrates data across departments to streamline overall business processes. Together, they provide a cohesive system for managing both production and enterprise-level activities.
MES System
A MES (Manufacturing Execution System) is a software solution designed to manage and optimize manufacturing operations in real-time on the shop floor. It tracks and monitors production activities, equipment performance, work-in-progress, and ensures product quality. MES helps manufacturers improve efficiency, reduce downtime, and maintain compliance with industry regulations by providing real-time insights into production processes. It often integrates with other enterprise systems, such as ERP, to create a seamless flow of data across the organization.
ERP System
An ERP (Enterprise Resource Planning) system is a software platform that integrates and manages core business processes across various departments, such as finance, human resources, procurement, inventory, and supply chain management. By centralizing data and automating workflows, ERP systems help organizations streamline operations, improve efficiency, and enhance decision-making. With real-time insights and reporting, ERP systems enable better resource planning and coordination, leading to improved productivity and business performance across the organization.
What Is The Difference Between MES and SAP?
The key difference between MES and SAP is that MES is focused on managing and optimizing real-time production processes on the shop floor, such as tracking work-in-progress and ensuring quality control, while SAP is a comprehensive enterprise software provider offering solutions like ERP and MES. SAP MES is specifically designed for manufacturing operations, while SAP ERP covers broader business functions like finance, human resources, and supply chain management. Essentially, MES focuses on production, and SAP offers both MES and ERP as part of its software suite.
SAP ERP
SAP ERP (Enterprise Resource Planning) is a comprehensive software solution designed to integrate and manage core business functions across an organization. It centralizes data from departments like finance, human resources, procurement, supply chain, and production, allowing for better coordination, real-time insights, and streamlined operations. SAP ERP automates key processes, improves decision-making, and enhances overall business efficiency by providing a unified platform for managing resources, planning, and reporting. It is widely used across industries to optimize workflows and drive organizational growth.
MES ERP Integration
MES ERP integration refers to the seamless connection between a Manufacturing Execution System (MES) and an Enterprise Resource Planning (ERP) system. This integration enables real-time data flow between the shop floor and business management functions. MES handles production operations, monitoring work-in-progress, equipment performance, and quality control, while ERP manages business functions like finance, inventory, and supply chain.
By integrating MES and ERP, manufacturers can improve overall efficiency by synchronizing production data with broader business processes, reducing errors, and enhancing decision-making. This integration provides a complete view of both manufacturing and organizational performance, ensuring smoother operations and better resource management.
What is The Difference Between ERP and MES Systems?
ERP (Enterprise Resource Planning) systems manage broad business functions such as finance, human resources, and supply chain, integrating data across departments to streamline operations and support decision-making. In contrast, MES (Manufacturing Execution System) focuses specifically on real-time production processes on the shop floor, handling tasks like work-in-progress tracking, equipment monitoring, and quality control. While ERP oversees organizational operations, MES optimizes manufacturing activities. Integrating both systems provides a comprehensive view of production and business processes, enhancing overall efficiency and coordination.
What Role Does MES Play In Production Scheduling?
MES (Manufacturing Execution System) plays a crucial role in production scheduling by providing real-time visibility and control over manufacturing processes. It helps manage and optimize production schedules by tracking work-in-progress, monitoring equipment availability, and adjusting schedules based on real-time data and operational conditions. MES enables manufacturers to respond quickly to changes, such as equipment failures or material shortages, ensuring that production plans are adjusted efficiently to minimize downtime and meet delivery deadlines. By integrating with higher-level systems like ERP, MES ensures that production schedules are aligned with overall business objectives and resource availability.
What is ERP?
ERP (Enterprise Resource Planning) is a software system that integrates and manages key business functions across an organization. It centralizes data and automates processes related to finance, human resources, supply chain, procurement, inventory management, and more. By providing a unified platform for managing various business operations, ERP systems help improve efficiency, streamline workflows, and support better decision-making through real-time data and reporting. ERP systems are used to ensure that different departments work in harmony, leading to enhanced overall organizational performance.
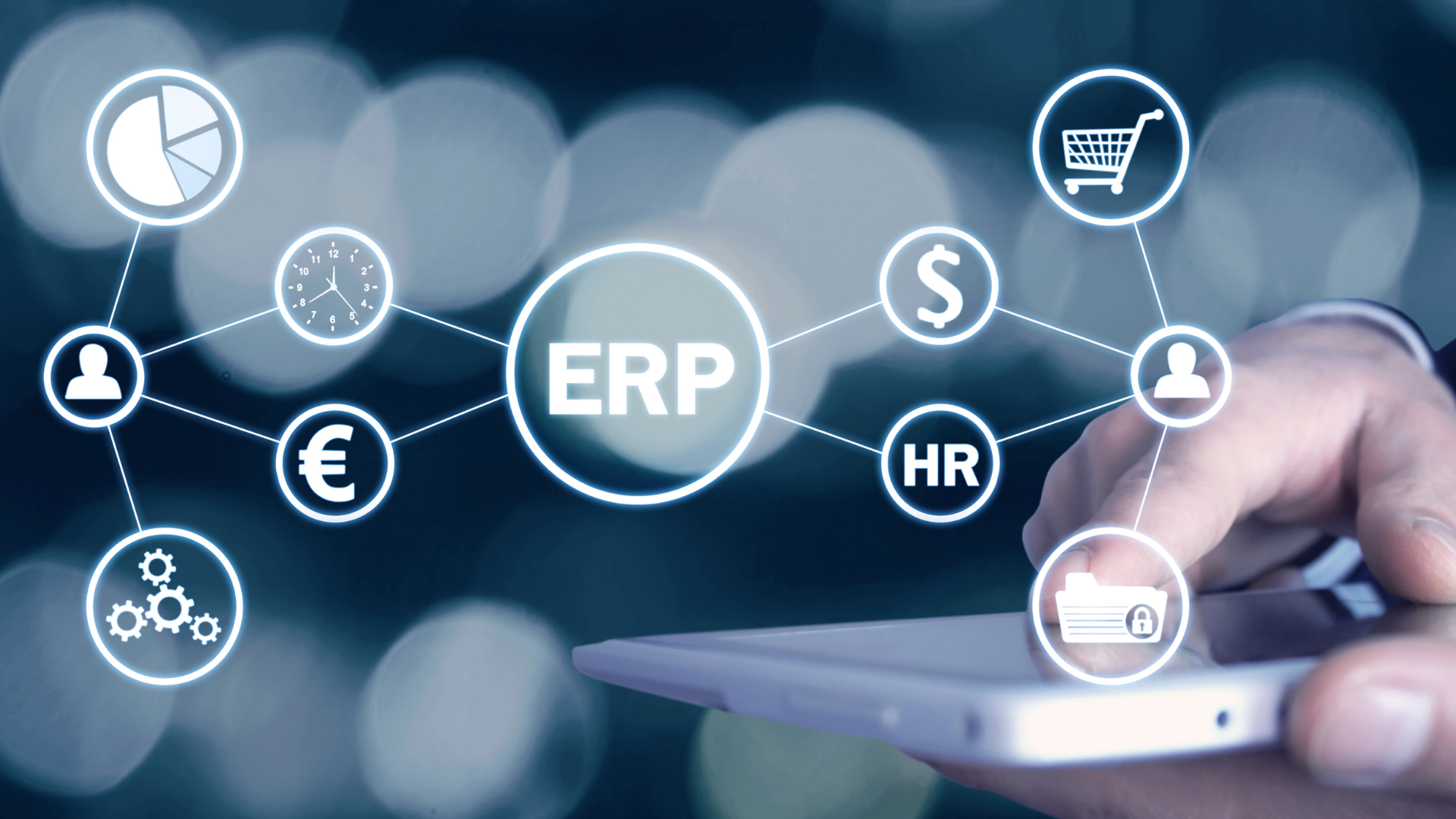
What Does MES Stand For?
What is MES?
MES (Manufacturing Execution System) is a software system used to manage and control manufacturing operations on the shop floor. It provides real-time visibility into production processes, tracking work-in-progress, monitoring equipment performance, and ensuring quality control. MES bridges the gap between enterprise-level systems, like ERP (Enterprise Resource Planning), and the actual production environment, enabling manufacturers to optimize workflows, reduce downtime, and maintain compliance with industry standards. By integrating data from various sources, MES helps improve operational efficiency and support better decision-making in manufacturing.
Manufacturing Execution System?
A Manufacturing Execution System (MES) is a software solution designed to manage and optimize production processes on the shop floor. It provides real-time monitoring and control of manufacturing operations, including tracking work-in-progress, managing inventory, and ensuring product quality. MES integrates with other enterprise systems, such as ERP (Enterprise Resource Planning), to synchronize production data with broader business processes. This integration helps manufacturers improve efficiency, reduce downtime, and maintain compliance with industry regulations, ultimately enhancing overall production performance.
Is MES The Same As SCADA?
MES (Manufacturing Execution System) and SCADA (Supervisory Control and Data Acquisition) serve different purposes in industrial automation. MES manages and optimizes real-time production processes, focusing on tracking work-in-progress, equipment performance, and quality control. SCADA, on the other hand, is designed for monitoring and controlling industrial equipment, providing real-time data and visualization at the machine level. While MES oversees overall production management, SCADA focuses on equipment-level control, and both can be integrated to provide a comprehensive view of manufacturing operations.
MES Software
MES (Manufacturing Execution System) software is designed to manage and optimize manufacturing processes in real-time. It provides tools for tracking production activities, monitoring equipment performance, ensuring quality control, and managing inventory. MES software integrates with other enterprise systems, such as ERP (Enterprise Resource Planning), to align production data with broader business processes. This integration helps manufacturers enhance efficiency, reduce downtime, and improve decision-making by providing real-time insights into production operations. MES software is crucial for maintaining smooth operations and achieving higher productivity in manufacturing environments.
SCADA System
A
SCADA (Supervisory Control and Data Acquisition) system is designed to monitor and control industrial processes and machinery in real-time. It provides a centralized platform for collecting and visualizing data from various sensors and control devices across a facility. SCADA systems allow operators to oversee operations, adjust settings, and respond to alarms from a central interface, facilitating efficient management of equipment and processes. They are commonly used in industries such as manufacturing, energy, and water management to ensure smooth and safe operation by providing real-time insights and control capabilities.
What is ERP in SCADA?
ERP (Enterprise Resource Planning) is not part of SCADA (Supervisory Control and Data Acquisition) systems, but the two can be integrated. SCADA focuses on real-time monitoring and control of industrial processes and equipment, while ERP manages broader business functions like finance, human resources, and supply chain. Integration of SCADA with ERP allows for the synchronization of real-time operational data with organizational processes, enhancing coordination and decision-making by aligning production activities with business goals.
What Is ERP and How Does It Work?
ERP (Enterprise Resource Planning) is a software system that integrates and manages core business functions across an organization, such as finance, human resources, supply chain, procurement, and inventory management. It works by centralizing data from various departments into a unified platform, allowing for streamlined processes and real-time access to information.
ERP systems facilitate the flow of data between different business functions, automating tasks like financial reporting, order processing, and resource planning. This integration helps improve efficiency, reduce errors, and provide comprehensive insights for better decision-making. By offering a single source of truth, ERP systems enable organizations to manage their resources effectively and respond swiftly to changing business conditions.
What Is An ERP System In Accounting?
In accounting, an ERP (Enterprise Resource Planning) system serves as a comprehensive software solution that integrates financial management functions with other business processes. It provides tools for managing key accounting tasks such as general ledger, accounts payable, accounts receivable, payroll, and financial reporting.
The ERP system centralizes financial data, automating processes like transaction recording, budgeting, and financial consolidation. This integration ensures accuracy, improves efficiency, and provides real-time insights into the organization’s financial status. By streamlining accounting operations and linking them with other business functions, an ERP system enhances overall financial management and supports better decision-making.
What Is The Difference Between ERP and Professional Services Automation?
ERP (Enterprise Resource Planning) and Professional Services Automation (PSA) serve different functions: ERP systems integrate and manage various business processes across an organization, such as finance, human resources, and supply chain, providing a comprehensive view of operations and facilitating data-driven decision-making. In contrast, PSA software is tailored for professional services firms, focusing on project management, resource allocation, time tracking, and billing to optimize project performance and profitability. Essentially, ERP covers broad organizational functions, while PSA is specialized for managing service-based projects and resources.
ERP System Examples
ERP (Enterprise Resource Planning) systems are used across various industries to streamline business processes. Some notable examples include:
- SAP ERP – A comprehensive and widely used ERP solution known for its extensive functionality across finance, supply chain, human resources, and more.
- Oracle ERP Cloud – Offers a suite of cloud-based ERP applications that cover finance, project management, procurement, and risk management.
- Microsoft Dynamics 365 – Provides integrated ERP and CRM solutions, offering modules for finance, operations, and business analytics.
- Infor CloudSuite – A cloud-based ERP system that provides industry-specific solutions for sectors like manufacturing, healthcare, and retail.
- NetSuite ERP – A cloud-based ERP solution offering financial management, CRM, e-commerce, and inventory management for businesses of all sizes.
- Epicor ERP – Designed for manufacturing and distribution industries, it includes modules for finance, supply chain management, and production planning.
These ERP systems help organizations improve efficiency, integrate various business functions, and support informed decision-making.
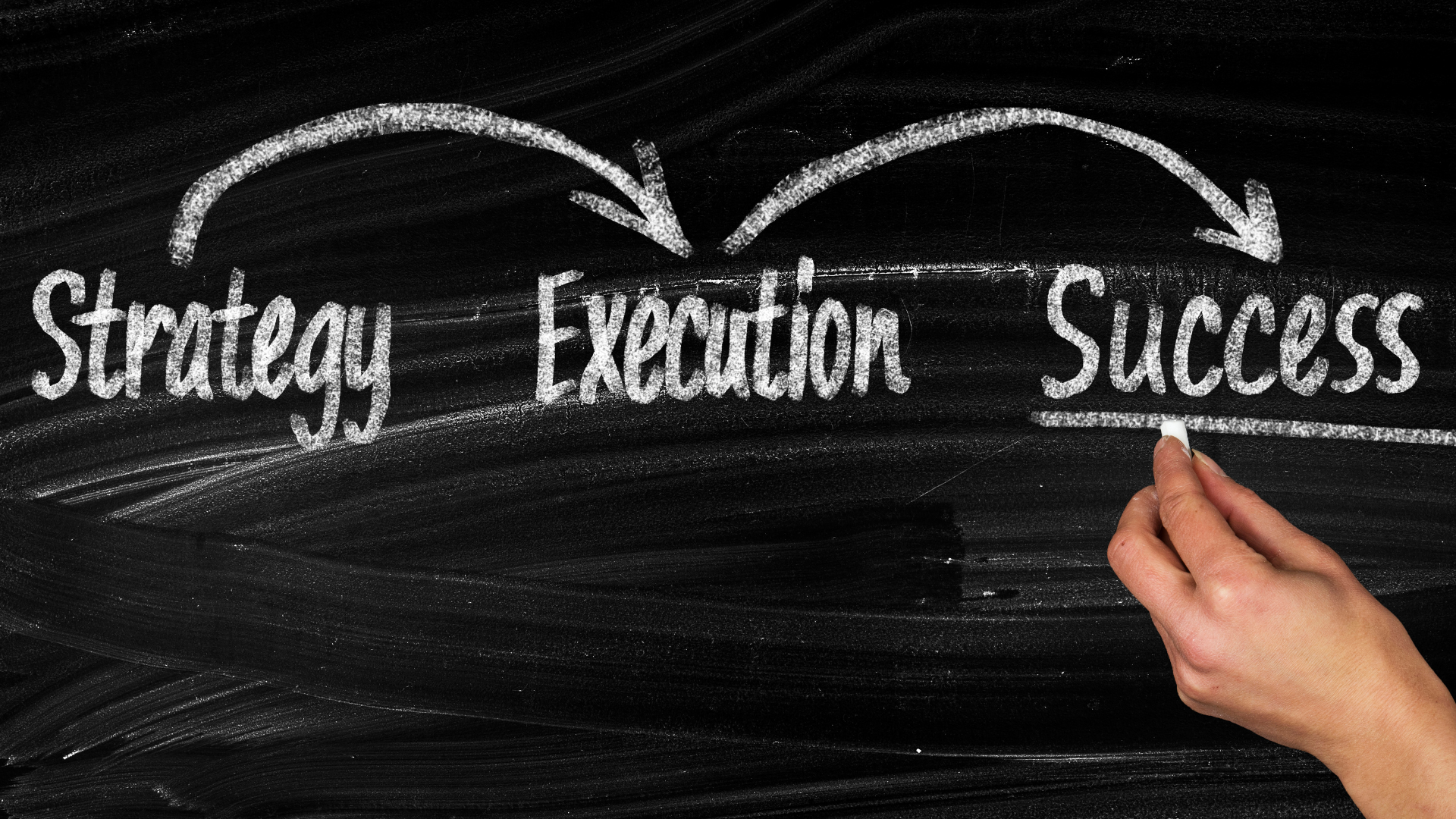
How is ERP Different From MIS?
ERP (Enterprise Resource Planning) systems integrate and manage various business processes across an organization, such as finance, human resources, and supply chain, providing a unified platform for streamlined operations and real-time decision-making. In contrast, MIS (Management Information Systems) focuses on generating and analyzing information to support managerial decision-making, typically through data collection and reporting. While ERP systems offer comprehensive integration of business functions, MIS is concerned with providing insights and reports to help managers monitor performance and make informed decisions.
Is Ignition a SCADA or MES?
Ignition by Inductive Automation is primarily a SCADA (Supervisory Control and Data Acquisition) system, but it also offers features that can support MES (Manufacturing Execution System) functionalities. Ignition is designed for real-time monitoring and control of industrial processes, providing tools for data acquisition, visualization, and control. It can collect data from various sources, visualize it through customizable dashboards, and provide control capabilities over equipment.
Additionally, Ignition’s flexibility and extensibility allow it to integrate with MES functionalities, such as tracking work-in-progress and managing production data. This makes it a versatile platform that can be used both for SCADA applications and for supporting some MES capabilities, depending on how it is configured and used.
What is MES vs ERP vs SCADA?
MES (Manufacturing Execution System), ERP (Enterprise Resource Planning), and SCADA (Supervisory Control and Data Acquisition) are distinct systems used in industrial and manufacturing environments, each serving a different role:
- MES focuses on managing and optimizing real-time production processes on the shop floor. It tracks work-in-progress, monitors equipment performance, ensures quality control, and provides data to enhance manufacturing efficiency and operational control.
- ERP integrates and manages a wide range of business functions across an organization, such as finance, human resources, supply chain, and inventory management. It centralizes data from various departments to streamline operations, improve resource planning, and support overall business decision-making.
- SCADA is designed for real-time monitoring and control of industrial processes and machinery. It provides tools for data acquisition, visualization, and operational control at the equipment level, allowing operators to oversee and manage processes effectively.
In summary, MES manages production processes, ERP handles comprehensive business functions, and SCADA focuses on equipment-level control and monitoring. Together, these systems can be integrated to provide a comprehensive view of both manufacturing operations and business management.
You might also like
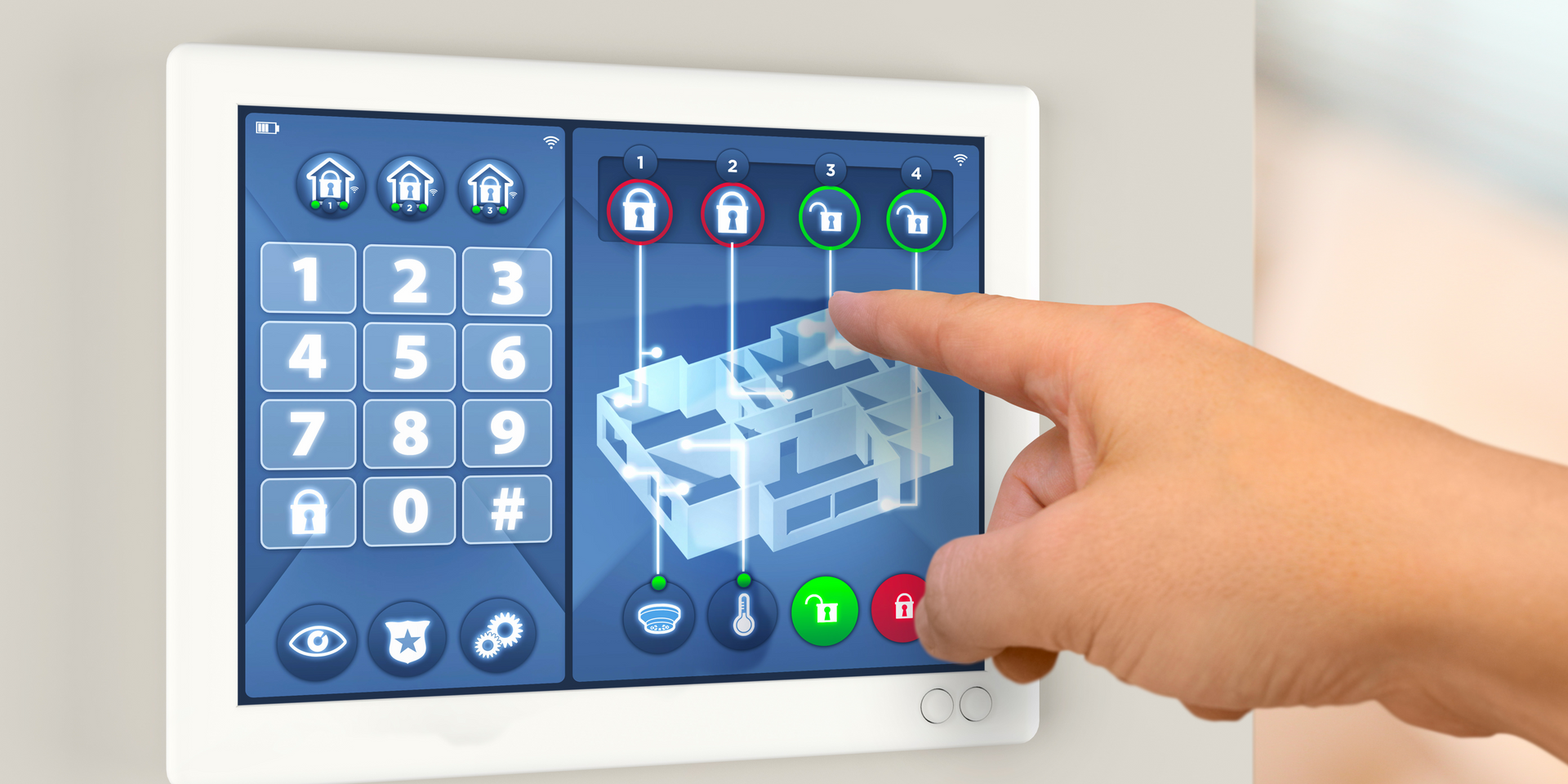
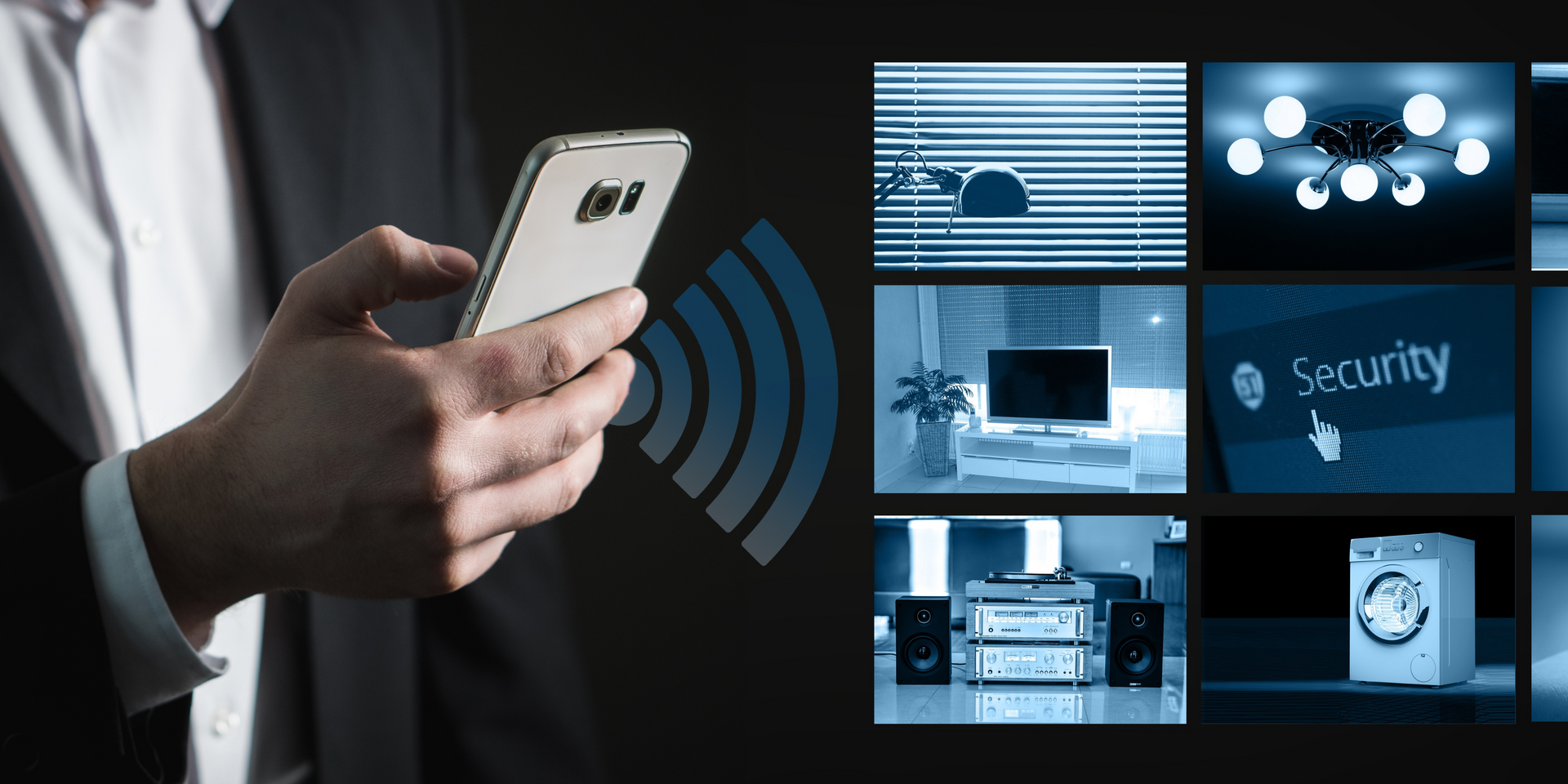
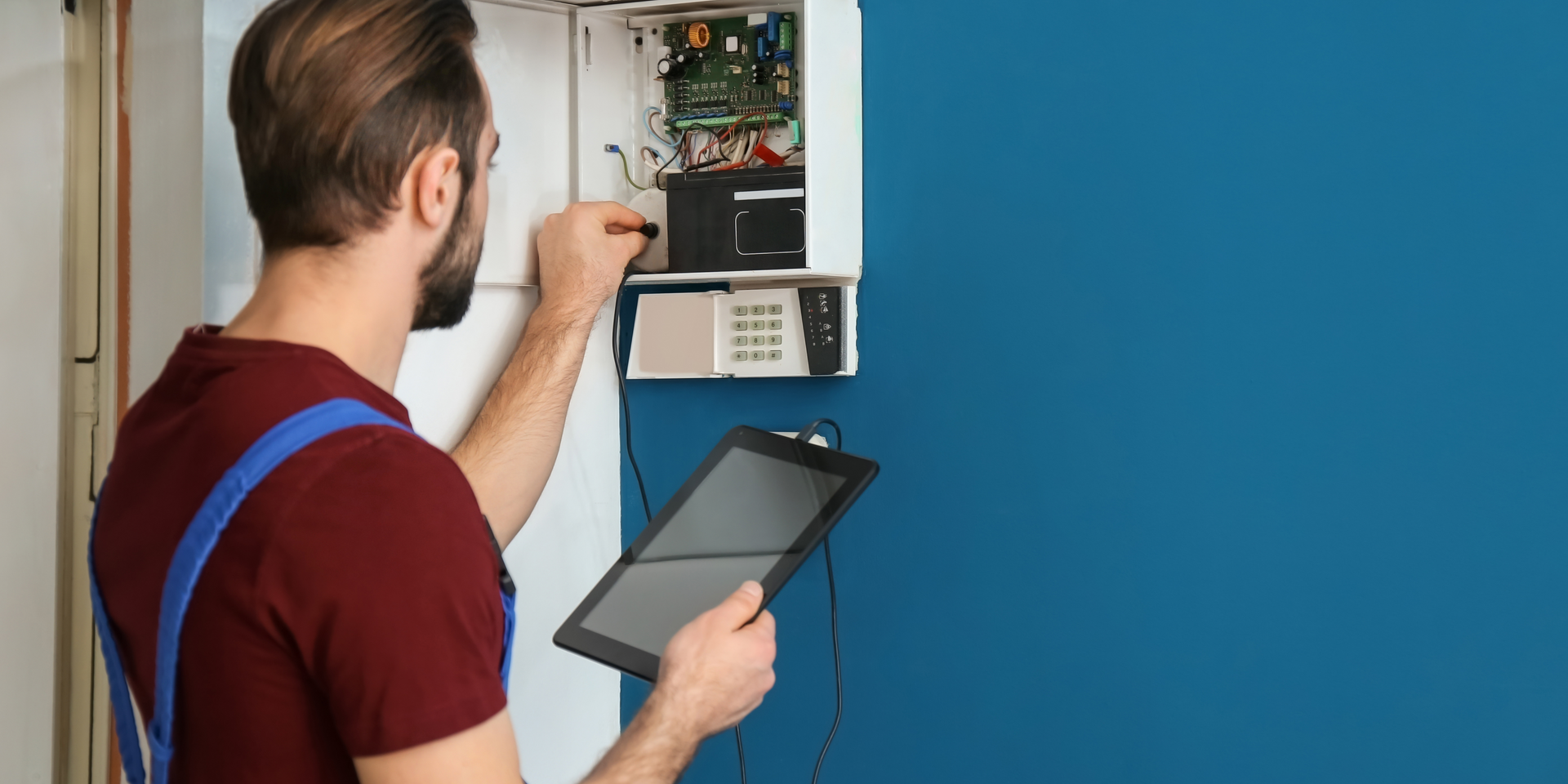