What Is The Difference Between MES And PLC?
What Is The Difference Between MES And PLC?
An MES (Manufacturing Execution System) manages and monitors production processes on a factory floor, providing real-time data to optimize operations. A PLC (Programmable Logic Controller), on the other hand, is a hardware device used to control machinery and automation processes. While MES operates at a broader system level, PLCs focus on specific machine-level tasks.
Industrial MES systems integrate real-time production data with business systems to optimize plant operations, while PLCs control the actual physical machinery.
Difference Between Microprocessor And Microcontroller
A microprocessor is the central processing unit (CPU) used in computers to perform arithmetic and logic operations, requiring external components like memory and input/output devices. A microcontroller is an integrated circuit that contains a CPU, memory, and I/O peripherals on a single chip, designed for controlling specific applications in embedded systems.
What Is The Difference Between MES And DCS?
A MES (Manufacturing Execution System) focuses on production management and optimizing manufacturing processes. A DCS (Distributed Control System) is a control architecture that manages process control in industrial environments, where multiple controllers are distributed across the plant to control different processes.
Difference Between PLC And ECU
A PLC (Programmable Logic Controller) is designed for industrial automation, controlling machinery and production lines. An ECU (Electronic Control Unit) is used in automotive systems to control functions like engine management or transmission control, focusing on vehicular electronics rather than industrial automation.
What Is The difference Between PLC And Microprocessor?
A PLC is a rugged, industrial device designed specifically for automation and control, with built-in inputs and outputs. A microprocessor is a general-purpose processing unit used in computers and electronic devices, not inherently designed for industrial environments without additional components.
Difference Between PLC and Microprocessor
The difference between a PLC and a microprocessor is that PLCs are designed for harsh industrial conditions, with pre-configured I/O ports, while a microprocessor requires additional hardware for inputs/outputs and environmental adaptation.
What Is The Difference Between A Controller And A PLC?
A controller is a generic term for any device or system that manages the behavior of other devices. A PLC is a specific type of controller designed for industrial automation, providing reliable control over machinery and processes. PLCs are built to withstand harsh environments and offer advanced programmability for complex tasks.
What Is The Difference Between A PLC And A Microcontroller?
A PLC is an industrial device used to control automation systems, often involving complex processes. A microcontroller is a smaller, embedded device that controls specific applications in electronics, such as home appliances or vehicles. PLCs are more robust and scalable for larger systems, while microcontrollers handle simpler, task-specific operations.
Microcontroller And PLC Book PDF
There are many resources available that provide comprehensive guides on microcontrollers and PLCs, including books that can be found in PDF format. These resources offer insights into their differences, applications, and programming methods. They are useful for students and professionals seeking to deepen their understanding of automation and control systems.
PLC And Microcontroller Difference
The key difference between a PLC and a microcontroller is that PLCs are designed for industrial applications, with the capability to handle complex automation tasks. Microcontrollers are designed for more focused tasks in embedded systems, such as controlling a specific device or function. While PLCs are robust and suited for large-scale operations, microcontrollers are used for simpler, more specific tasks.
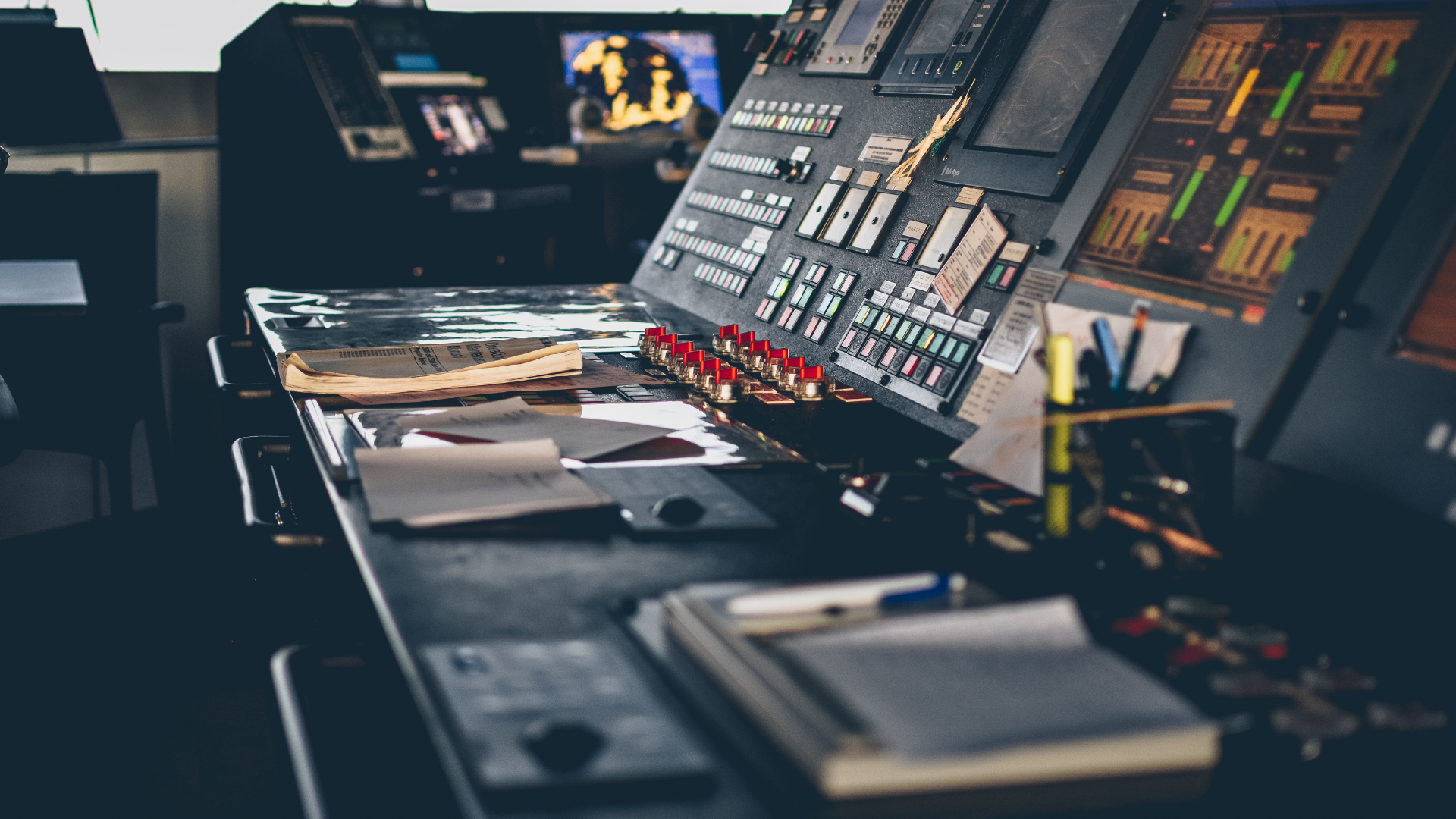
What Is The Difference Between A Control System And A Microcontroller?
A control system is a broader term referring to any system that manages, commands, or regulates other systems. A microcontroller is a specific hardware component used to control particular functions within a device or system. While a control system can involve multiple devices, a microcontroller is typically used to control one dedicated function within an embedded system.
PLC Vs Microcontroller Vs Microprocessor
A PLC is a rugged industrial device used for automation and process control, while a microcontroller is a smaller integrated circuit used in embedded systems for specific tasks. A microprocessor is the CPU used in computers, requiring additional components to function in control applications. Each of these devices has a unique application, with PLCs focused on industrial tasks, microcontrollers on embedded systems, and microprocessors on general computing.
What Does MES Stand For?
MES stands for Manufacturing Execution System, a software platform used to manage and monitor the production process on a factory floor. MES provides real-time data that helps optimize production efficiency and performance.
Manufacturing Execution System
A Manufacturing Execution System (MES) is a software tool used to oversee and manage the entire production process, from raw materials to finished goods. It tracks and controls manufacturing in real-time, improving efficiency, product quality, and operational performance. MES integrates with other systems to provide a holistic view of production operations.
List Of MES Software
Popular MES software includes:
- Siemens SIMATIC IT
- Rockwell FactoryTalk
- Honeywell MES
- Wonderware MES
- SAP Manufacturing Execution: These systems provide comprehensive solutions for managing and optimizing production processes.
What Microprocessors Are Used In PLC?
Microprocessors commonly used in PLCs include ARM-based processors and Intel Atom processors. These microprocessors provide the necessary computational power for real-time control and automation in industrial environments.
Can Microcontroller Replace PLC?
In certain cases, a microcontroller can replace a PLC for simpler applications. However, microcontrollers are generally not as robust or adaptable as PLCs for larger industrial tasks. PLCs are designed for harsh environments and complex automation, making them more suitable for extensive industrial control.
What Is MES And PLC?
An MES (Manufacturing Execution System) is a software solution that optimizes production, while a PLC (Programmable Logic Controller) is a hardware device that controls specific machines and automation processes. MES manages production efficiency, while PLCs execute control commands for machinery.
Why PLC Is So Important For Microprocessor
A PLC is essential for a microprocessor in industrial settings because it allows the microprocessor to perform control tasks in real-time. The PLC’s rugged design and adaptability make it suitable for environments where reliability and fast processing are crucial. It ensures the microprocessor can manage automation without external interference.
How Is MES Different From SCADA?
MES (Manufacturing Execution System) focuses on managing the overall production process, while SCADA (Supervisory Control and Data Acquisition) is used for real-time monitoring and control of machinery and systems. SCADA collects data from machines, while MES interprets that data to optimize production performance and efficiency.
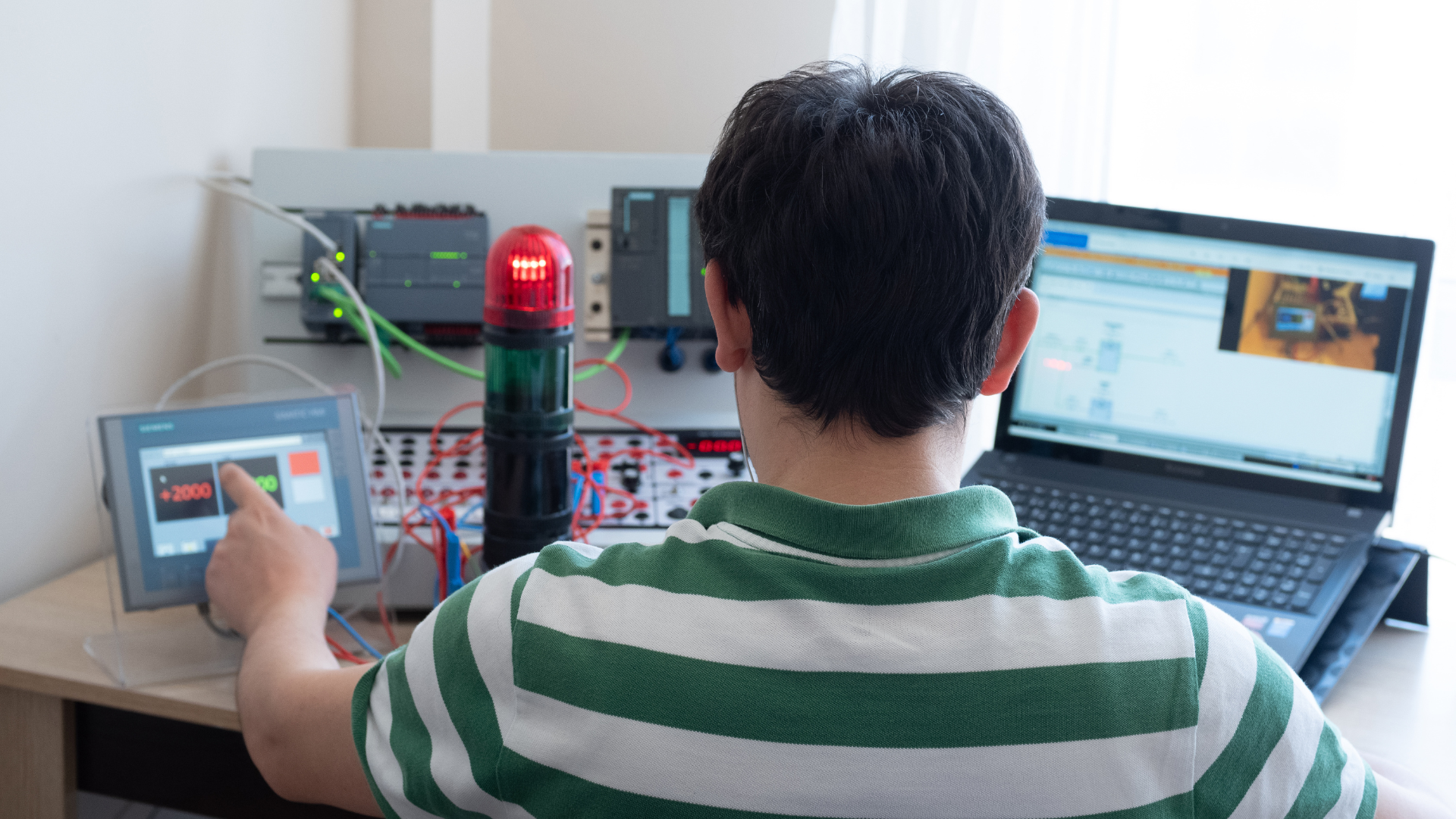