What Is the Five Layer Automation Pyramid?
What Is the Five Layer Automation Pyramid?
The Five-Layer Automation Pyramid represents the hierarchy of systems used in industrial automation, connecting the shop floor to enterprise management. At the base is the Field Level, which includes sensors and actuators interacting with physical equipment. Above this, the Control Level consists of PLCs (Programmable Logic Controllers) and DCS (Distributed Control Systems) that manage real-time machine control. The Supervisory Level is where SCADA (Supervisory Control and Data Acquisition) systems operate, providing real-time monitoring and control of industrial processes. A common question is, "Is SCADA an MES system?" The answer is no; SCADA focuses on process control, while MES (Manufacturing Execution Systems), located at the Planning/Execution Level, manages production operations, scheduling, and quality control. Finally, at the top is the Enterprise Level, where ERP (Enterprise Resource Planning) systems handle company-wide business functions like finance and inventory. This structure ensures seamless communication between production and enterprise management for optimized operations.
Automation Pyramid Levels
The Automation Pyramid Levels is a structured model used to describe the hierarchy of automation systems in industrial processes. It outlines how different technologies and systems interact to streamline operations, from the physical equipment on the shop floor to enterprise-wide management. The pyramid consists of five levels:
- Field Level: The base of the pyramid, comprising sensors and actuators that interact directly with machinery, collecting data and controlling processes.
- Control Level: This level includes PLCs (Programmable Logic Controllers) and DCS (Distributed Control Systems) that manage real-time machine control and automation.
- Supervisory Level: At this level, SCADA (Supervisory Control and Data Acquisition) systems provide real-time monitoring and control of production processes, offering a visual interface for operators to manage operations.
- Execution/Planning Level: The MES (Manufacturing Execution System) resides here, managing production schedules, material tracking, and quality control, bridging the gap between the shop floor and higher-level business systems.
- Enterprise Level: The top of the pyramid, where ERP (Enterprise Resource Planning) systems operate, overseeing the entire business operation, including finance, inventory, and supply chain management.
Each level of the pyramid interacts with the others to ensure efficient data flow and operational control, helping manufacturers optimize both production and business functions.

What Is Level 4 Layer in The Automation Pyramid?
What is The Automation Pyramid
The Automation Pyramid is a model that represents the hierarchy of systems in industrial automation, from the shop floor to enterprise management. It consists of five levels: the Field Level (sensors and actuators that gather real-time data), the Control Level (PLCs and DCS that manage machine control), the Supervisory Level (SCADA systems for monitoring and control), the Execution/Planning Level (MES for managing production workflows and quality), and the Enterprise Level (ERP systems for overseeing business operations like finance and supply chain). Together, these levels ensure seamless data flow and operational efficiency in manufacturing.
What Is The Industrial Automation Pyramid?
The Industrial Automation Pyramid is a hierarchical model that illustrates how different systems work together in automating industrial processes. It consists of five layers: the Field Level (sensors and actuators), the Control Level (PLCs and DCS for machine control), the Supervisory Level (SCADA systems for real-time monitoring), the Execution/Planning Level (MES for managing production), and the Enterprise Level (ERP for business management). This structure helps integrate shop floor operations with enterprise-wide processes for greater efficiency and control.
Industrial Automation Pyramid
The Industrial Automation Pyramid is a structured model that outlines the levels of automation in industrial processes. It consists of five key layers:
- Field Level: Involves sensors, actuators, and devices that gather data and control machinery.
- Control Level: Includes PLCs (Programmable Logic Controllers) and DCS (Distributed Control Systems) that manage machine operations.
- Supervisory Level: Features SCADA (Supervisory Control and Data Acquisition) systems for monitoring and controlling processes in real time.
- Execution/Planning Level: Houses MES (Manufacturing Execution Systems) to manage production, scheduling, and quality control.
- Enterprise Level: The top layer where ERP (Enterprise Resource Planning) systems oversee business-wide operations like finance, supply chain, and inventory management.
This pyramid ensures seamless communication and integration from shop floor operations to enterprise-level decision-making.
What is an Automation Pyramid?
The Automation Pyramid is a model that outlines the hierarchy of industrial automation systems, connecting shop floor activities to enterprise-level management. It includes five levels: the Field Level, where sensors and actuators collect data and control machinery; the Control Level, where PLCs and DCS handle real-time machine operations; the Supervisory Level, with SCADA systems for process monitoring and control; the Execution/Planning Level, where MES systems manage production and workflows; and the Enterprise Level, which uses ERP systems to oversee broader business functions like finance and supply chain. This structure facilitates seamless integration and efficiency between operational and business processes.
What Are The Layers of Automation?
The layers of automation typically refer to the levels of systems involved in automating industrial processes, from machine control to enterprise management. These layers are:
- Field Level: Includes sensors, actuators, and other devices that interact directly with machinery to collect data and control operations.
- Control Level: Consists of PLCs (Programmable Logic Controllers) and DCS (Distributed Control Systems) that manage real-time control and automation of machines and processes.
- Supervisory Level: Features SCADA (Supervisory Control and Data Acquisition) systems that provide real-time monitoring, visualization, and control of production processes.
- Execution/Planning Level: This layer is where MES (Manufacturing Execution Systems) operate, managing production scheduling, tracking, and quality control, bridging the gap between shop floor operations and business systems.
- Enterprise Level: The top layer, where ERP (Enterprise Resource Planning) systems oversee business-wide functions such as finance, supply chain, and resource management.
These layers work together to ensure efficient data flow, control, and decision-making from the shop floor to the executive level.
What Are The 5 Elements of Automation?
The 5 elements of automation are the key components that work together to create an effective automated system in industrial and manufacturing environments. These elements are:
- Sensors: Devices that collect data from the physical environment, such as temperature, pressure, speed, or position, providing real-time feedback for the system.
- Controllers: This element includes PLCs (Programmable Logic Controllers) and other control systems that process the data from sensors and send commands to actuators to manage machine operations.
- Actuators: Mechanical devices like motors, valves, or relays that receive signals from controllers to perform physical actions, such as moving parts or starting/stopping a process.
- Communication Systems: These ensure seamless data exchange between different automation components, allowing sensors, controllers, and actuators to communicate effectively, typically through wired or wireless networks.
- Human-Machine Interface (HMI): The interface that allows operators to interact with the automated system, monitor processes, and make adjustments when necessary, often through displays or control panels.
These elements work together to create a fully automated process, enhancing efficiency, accuracy, and productivity in industrial environments.
5 Levels of Automation In Manufacturing
The 5 levels of automation in manufacturing represent the hierarchy of systems that work together to streamline production processes from the ground level to enterprise-wide management. These levels are:
- Field Level: This is the base level, consisting of sensors and actuators that interact directly with machinery to collect data (e.g., temperature, pressure) and control physical operations (e.g., opening valves or starting motors).
- Control Level: At this level, PLCs (Programmable Logic Controllers) and DCS (Distributed Control Systems) manage real-time machine control and automation, using data from the field level to execute commands.
- Supervisory Level: The SCADA (Supervisory Control and Data Acquisition) systems operate here, providing real-time monitoring, visualization, and control over industrial processes, giving operators oversight of production.
- Execution/Planning Level: MES (Manufacturing Execution Systems) sit at this level, managing production workflows, scheduling, material tracking, and quality control, bridging the gap between shop floor operations and enterprise-level systems.
- Enterprise Level: The top level involves ERP (Enterprise Resource Planning) systems that manage broader business processes like finance, inventory, procurement, and supply chain, integrating manufacturing data with enterprise-level decision-making.
These five levels work together to ensure a seamless flow of information and control from the shop floor to the executive level, optimizing both manufacturing operations and overall business performance.

What Are The 4 Elements of Automation?
The 4 elements of automation in industrial systems are the core components that work together to automate processes efficiently. These elements are:
- Sensors: Devices that detect and measure physical parameters like temperature, pressure, flow, or position, providing real-time data to the system.
- Controllers: Systems such as PLCs (Programmable Logic Controllers) or DCS (Distributed Control Systems) that process the sensor data and make decisions based on predefined logic, sending commands to actuators.
- Actuators: Mechanical or electronic devices like motors, valves, or relays that execute the physical actions needed to control processes, based on signals from the controller.
- Human-Machine Interface (HMI): The interface through which operators can monitor and interact with the automated system, adjust settings, and troubleshoot issues, often using a control panel or display screen.
These four elements are the building blocks of industrial automation systems, working together to streamline and control processes, improve efficiency, and reduce the need for manual intervention.
Industry 4.0 Automation Pyramid
The Industry 4.0 Automation Pyramid is an evolved version of the traditional automation pyramid, incorporating advanced technologies to align with the principles of Industry 4.0, such as IoT, big data, and artificial intelligence. This model focuses on connecting and integrating all levels of the automation hierarchy, from physical equipment to cloud-based systems, for smarter and more efficient production. Here’s a breakdown of the layers:
- Field Level: Includes smart sensors and actuators embedded with IoT capabilities, collecting real-time data and interacting with machines in an interconnected way.
- Control Level: PLCs (Programmable Logic Controllers) and DCS (Distributed Control Systems) manage real-time control, now enhanced with increased connectivity and more flexible, autonomous operation due to Industry 4.0 technologies.
- Supervisory Level: SCADA (Supervisory Control and Data Acquisition) systems continue to provide monitoring and control but are now integrated with cloud computing and data analytics, enabling better decision-making through predictive insights.
- Execution/Planning Level: MES (Manufacturing Execution Systems) connect shop floor operations with higher-level systems, integrating real-time data with smart manufacturing technologies to optimize production, quality control, and resource management.
- Enterprise Level: ERP (Enterprise Resource Planning) manages the business side of operations, now with the added ability to connect with cloud services, advanced analytics, and AI-driven decision-making for enhanced efficiency across the organization.
The Industry 4.0 automation pyramid leverages the connectivity between these levels, enabling data to flow seamlessly from the shop floor to the cloud, enhancing productivity, flexibility, and real-time decision-making.
What Are 5 Different Types of Automation?
Here are five different types of automation commonly used in industries:
- Fixed (Hard) Automation: This type of automation is used for high-volume, repetitive tasks where the production process is predetermined and doesn't change. It involves custom-built machinery designed for specific tasks, such as assembly lines in automotive manufacturing. It is highly efficient for mass production but lacks flexibility for product variations.
- Programmable Automation: In this type, equipment can be reprogrammed to handle different tasks or products. It is suitable for batch production, where the production runs vary but are not constantly changing. Examples include CNC machines and robotic systems used in manufacturing various products.
- Flexible (Soft) Automation: This type allows for more adaptability in manufacturing, with systems capable of switching between different products without significant downtime. It is ideal for producing smaller batches with high product variety. Flexible automation is often seen in industries like electronics manufacturing, where customization is key.
- Integrated Automation: This involves integrating various automation systems across the entire production process, from raw materials to finished products. Systems like SCADA, MES, and ERP work together for a fully automated and controlled environment. Integrated automation is often found in complex manufacturing processes like pharmaceuticals or large-scale industrial operations.
- Robotic Process Automation (RPA): This type of automation is used in business processes rather than physical manufacturing. It involves using software robots to automate repetitive, rule-based tasks, such as data entry, customer service, or financial reporting. RPA is commonly used in sectors like finance, healthcare, and telecommunications.
Each type of automation offers distinct advantages depending on the production environment, volume, and the need for flexibility or customization.
Levels of Automation PDF
A Levels of Automation PDF provides a comprehensive overview of the different layers in industrial automation, explaining how each level works together to streamline operations. It typically covers the Field Level (sensors and actuators gathering real-time data), the Control Level (PLCs and DCS managing real-time processes), the Supervisory Level (SCADA systems for monitoring and control), the Execution/Planning Level (MES managing production and workflows), and the Enterprise Level (ERP handling business functions like finance and inventory). These PDFs often include diagrams, examples, and case studies to illustrate how these levels interact for efficient manufacturing and enterprise management.
What are the 5 Levels of Automation in Factory Operations?
The 5 levels of automation in factory operations include the Field Level, where sensors and actuators collect data and control machinery, and the Control Level, where PLCs and DCS manage real-time machine operations. The Supervisory Level involves SCADA systems for real-time monitoring and control of industrial processes, while the Execution/Planning Level uses MES to manage production workflows, scheduling, and quality control. At the top, the Enterprise Level features ERP systems that oversee business functions like finance, inventory, and supply chain, integrating data from all levels for efficient decision-making and operations.
Automation Pyramid of a Smart Factory
The Automation Pyramid of a Smart Factory adapts the traditional automation pyramid to include advanced technologies and connectivity principles of Industry 4.0, allowing for greater flexibility, real-time decision-making, and data integration. The layers are:
- Field Level: Includes smart sensors, actuators, and IoT devices that collect real-time data from machines and equipment, enabling seamless communication between physical processes and the digital environment.
- Control Level: Advanced PLCs (Programmable Logic Controllers) and DCS (Distributed Control Systems) manage real-time machine control and automation with enhanced connectivity, allowing for more dynamic operations and real-time adjustments.
- Supervisory Level: SCADA (Supervisory Control and Data Acquisition) systems provide real-time monitoring, visualization, and control, now integrated with cloud platforms and data analytics for predictive insights and process optimization.
- Execution/Planning Level: MES (Manufacturing Execution Systems) manage production schedules, workflows, material tracking, and quality control, using data from IoT-enabled devices to optimize factory operations in real time.
- Enterprise Level: ERP (Enterprise Resource Planning) systems at the top integrate factory data with business functions like finance, supply chain, and inventory management, enhanced by big data analytics, AI, and machine learning to drive strategic decision-making across the smart factory.
This structure ensures that all levels of a smart factory are interconnected, enabling better resource utilization, improved efficiency, and real-time decision-making.
What is Level 1 Level 2 Level 3 Automation?
Level 1, Level 2, and Level 3 automation represent different layers of automation in industrial processes, each with distinct functions and responsibilities. Here's a breakdown:
Level 1: Field Level
- Function: This is the base level, focused on the physical equipment in the plant, such as sensors, actuators, motors, and valves.
- Responsibilities: Collecting real-time data from machines and controlling basic operations.
- Example: Sensors detecting temperature or pressure, and actuators opening or closing valves based on control signals.
Level 2: Control Level
- Function: This level is responsible for real-time control of processes through Programmable Logic Controllers (PLCs) or Distributed Control Systems (DCS).
- Responsibilities: Managing the automation of specific machinery or processes by executing logic and control tasks based on data received from Level 1.
- Example: PLCs controlling machinery operations in a production line, ensuring machines follow predefined sequences.
Level 3: Supervisory Level
- Function: Level 3 includes Supervisory Control and Data Acquisition (SCADA) systems and Manufacturing Execution Systems (MES), responsible for monitoring, controlling, and managing production processes.
- Responsibilities: Providing real-time visibility of the production process, overseeing operational performance, tracking production data, and managing workflows.
- Example: SCADA systems visualizing machine performance and enabling operators to control processes, or MES managing production schedules and quality.
These levels work together, with data flowing from Level 1 (physical devices) up to Level 3 (supervisory systems), ensuring smooth and efficient industrial operations.
Automation Pyramid PDF
An Automation Pyramid PDF typically explains the hierarchy of industrial automation, showing how systems interact across five levels. At the Field Level, sensors and actuators collect real-time data from machines. The Control Level uses PLCs (Programmable Logic Controllers) and DCS (Distributed Control Systems) to manage machine operations. The Supervisory Level includes SCADA systems for real-time monitoring and control. The Execution/Planning Level involves MES (Manufacturing Execution Systems) to manage production workflows and quality. At the top, the Enterprise Level features ERP (Enterprise Resource Planning) systems, overseeing business functions like finance and inventory, integrating data from the lower levels for overall business management.
You might also like
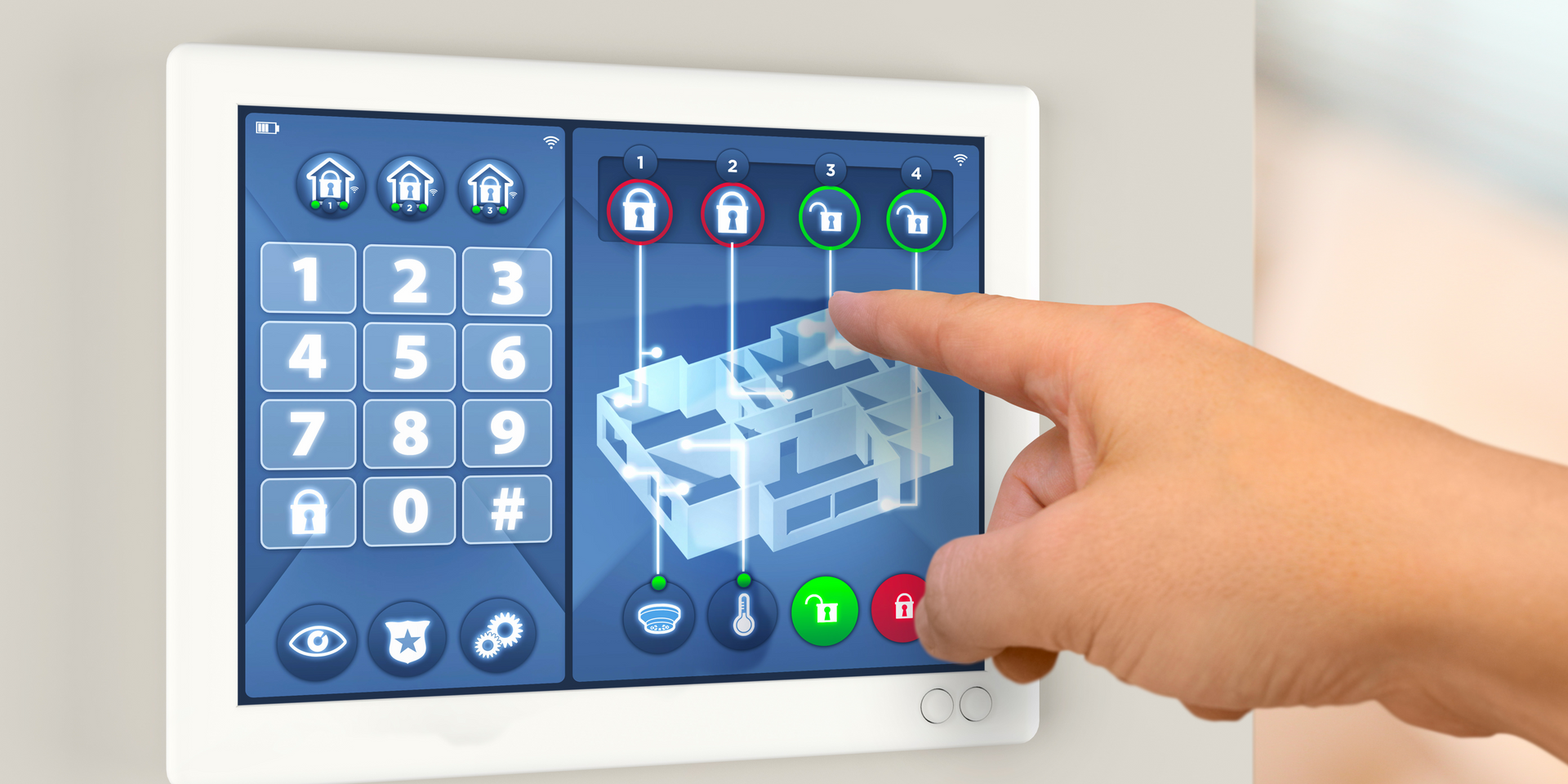
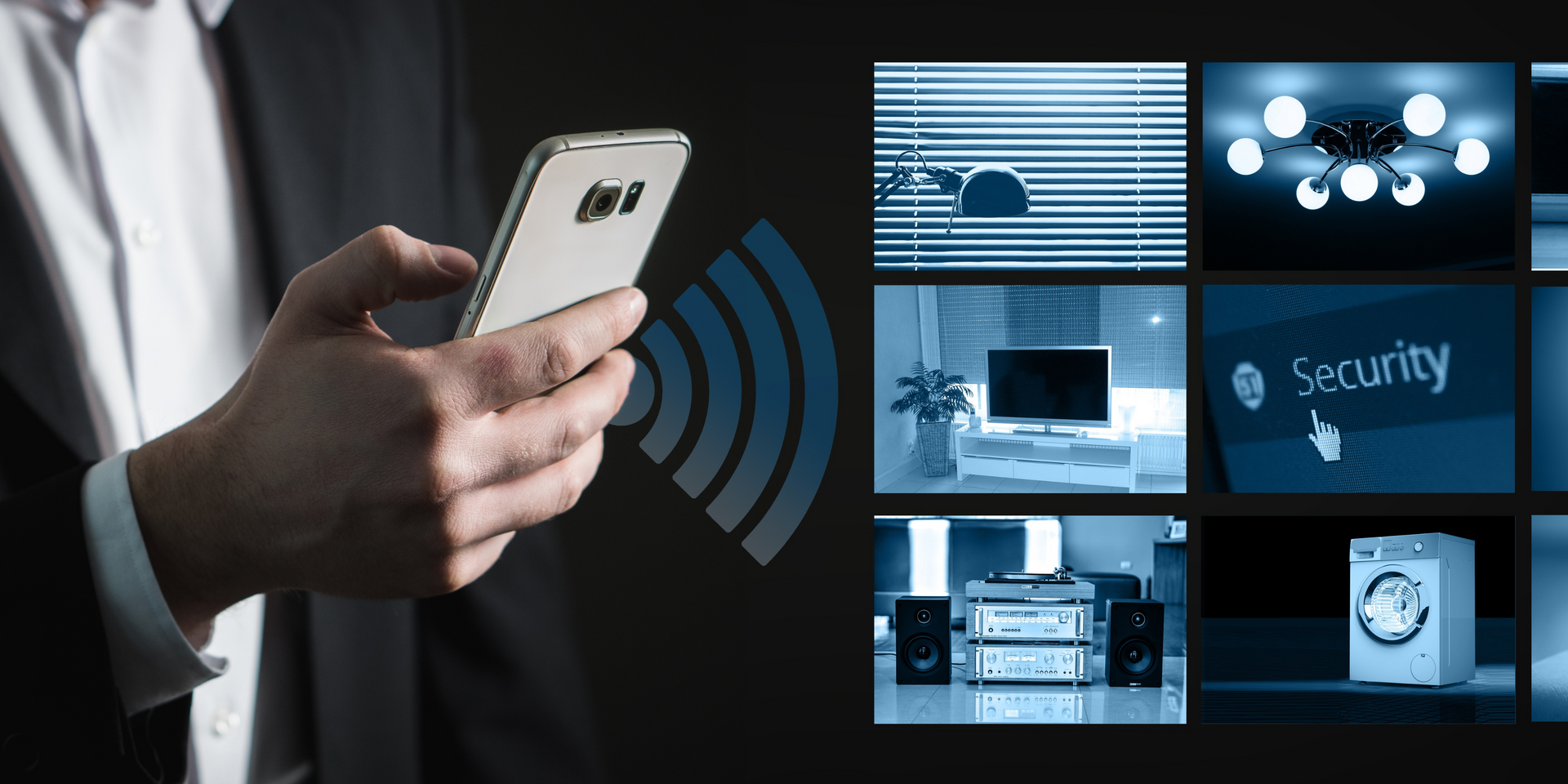
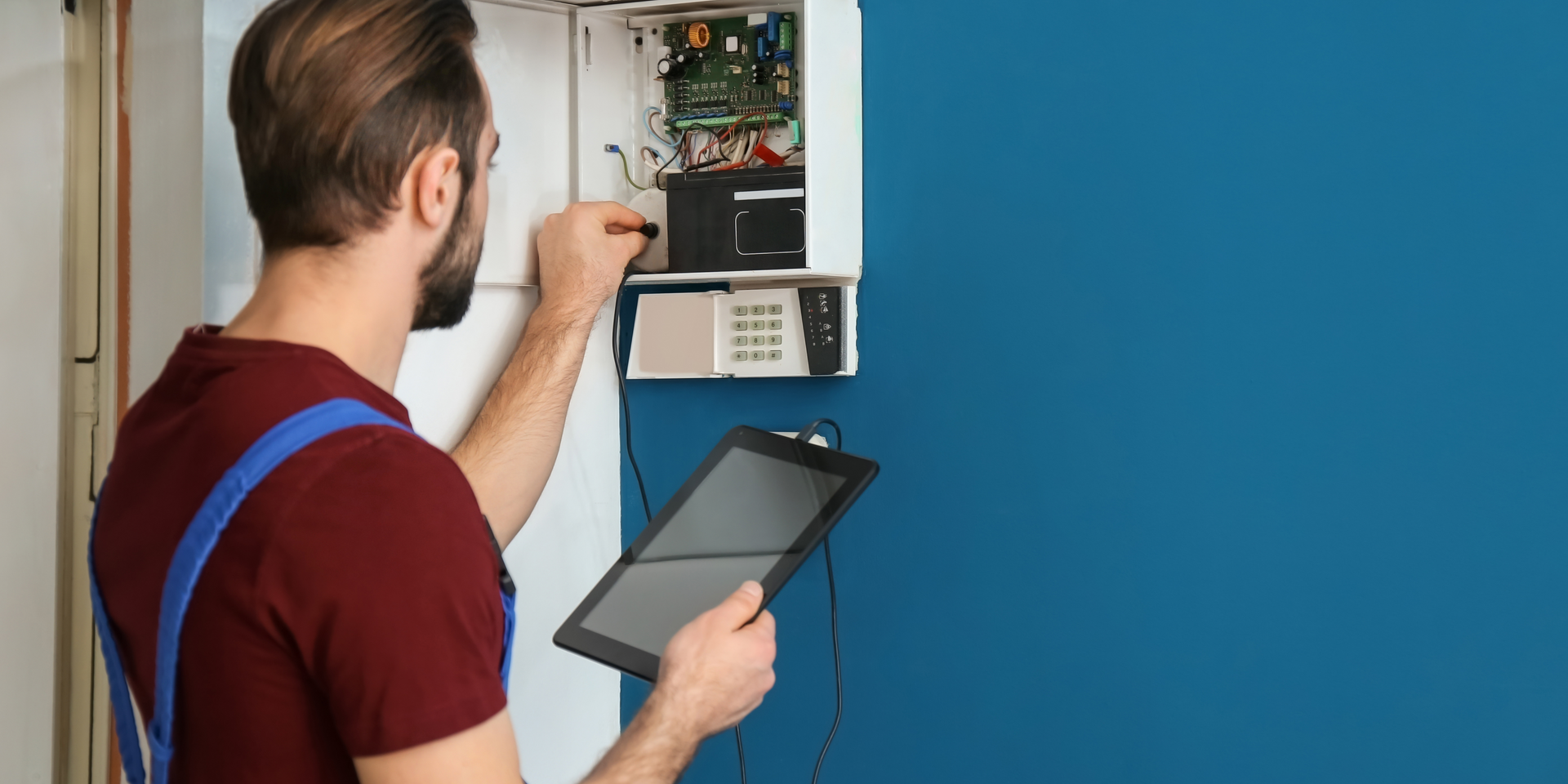