Difference Between HMI and SCADA
What is the Main Difference Between SCADA and HMI
Which is Better HMI or SCADA? Both play crucial roles in industrial automation, but they serve different purposes. The main difference between SCADA (Supervisory Control and Data Acquisition) and HMI (Human-Machine Interface) is that SCADA is a comprehensive control system that collects data from various sensors and equipment across a facility to monitor and control processes in real-time, while HMI is the user interface that allows operators to interact with the SCADA system, visualize data, and manage the control processes. Essentially, HMI is the interface component, and SCADA is the overarching system that utilizes the data provided by HMI and other sources to manage and control industrial operations.
Difference Between HMI and SCADA
HMI (Human-Machine Interface) and SCADA (Supervisory Control and Data Acquisition) differ mainly in scope and functionality. HMI is a user interface that enables operators to interact directly with machinery, providing real-time data visualization and control for specific processes. SCADA, on the other hand, is a comprehensive system designed for remote monitoring and control of entire industrial processes, integrating data from multiple sources, including various HMIs. While HMI focuses on the direct interaction between humans and machines, SCADA offers a broader overview and management of complex operations.
What is the Key Difference Between HMI and SCADA?
The key difference between HMI (Human-Machine Interface) and SCADA (Supervisory Control and Data Acquisition) lies in their scope and functionality. HMI is primarily a user interface that allows operators to interact directly with machinery, providing real-time data visualization and control for specific processes. SCADA, however, is a comprehensive system designed for remote monitoring and control of entire industrial processes, integrating data from multiple sources, including various HMIs. Essentially, HMI focuses on direct machine interaction, while SCADA provides a broader, system-wide overview and management.
Difference Between HMI and SCADA
HMI (Human-Machine Interface) and SCADA (Supervisory Control and Data Acquisition) differ mainly in scope and functionality. HMI is a user interface that enables operators to interact directly with machinery, providing real-time data visualization and control for specific processes. SCADA, on the other hand, is a comprehensive system designed for remote monitoring and control of entire industrial processes, integrating data from multiple sources, including various HMIs. While HMI focuses on the direct interaction between humans and machines, SCADA offers a broader overview and management of complex operations.
What is HMI in SCADA?
In SCADA (Supervisory Control and Data Acquisition) systems, HMI (Human-Machine Interface) is a crucial component that provides the interface through which operators interact with the SCADA system. HMI displays real-time data from the SCADA system, allowing operators to monitor and control machinery and processes. It translates complex data into visual representations, such as graphs and diagrams, making it easier for operators to understand and respond to system conditions. Essentially, HMI serves as the user-friendly front end of a SCADA system, facilitating efficient human interaction with the automated processes.
How do you Differentiate Between PLC, SCADA, DCS, and HMI?
PLC (Programmable Logic Controller) is a hardware device used for automating control processes in industrial environments, executing pre-programmed instructions to manage machinery and equipment. SCADA (Supervisory Control and Data Acquisition) is a comprehensive system for remote monitoring and controlling industrial processes, integrating data from multiple sources, including PLCs, for a wide-area overview. DCS (Distributed Control System) is similar to SCADA but is typically used for centralized control in continuous processes within a single location, focusing on real-time data processing and control. HMI (Human-Machine Interface) is a user interface that allows operators to interact with machines and control systems, providing real-time data visualization and control capabilities for both PLCs and SCADA systems.
Difference Between PLC and SCADA?
PLC (Programmable Logic Controller) is a hardware device used for automating control processes by executing programmed instructions to manage machinery and equipment in real-time. SCADA (Supervisory Control and Data Acquisition), on the other hand, is a comprehensive software system designed for remote monitoring and control of industrial processes, integrating data from multiple PLCs and other devices to provide a wide-area overview. While PLCs focus on executing control tasks at the machine level, SCADA provides higher-level supervision, data analysis, and management of entire systems. Essentially, PLCs perform direct control functions, whereas SCADA oversees and coordinates these functions across a broader network.
Difference Between SCADA and DCS?
SCADA (Supervisory Control and Data Acquisition) and DCS (Distributed Control System) both manage industrial processes, but they differ in scope and architecture. SCADA is designed for remote monitoring and control across multiple locations, integrating data from various sources to provide a comprehensive overview of wide-area operations. DCS, however, is typically used for centralized control within a single location, focusing on real-time data processing and control for continuous processes. While SCADA excels in supervisory functions and wide-area data integration, DCS is optimized for precise, real-time control and automation of complex processes within a confined area.
What is HMI in PLC?
In the context of PLC (Programmable Logic Controller) systems, HMI (Human-Machine Interface) is a user interface that allows operators to interact directly with the PLC-controlled machinery and processes. The HMI provides real-time data visualization, enabling operators to monitor system performance, adjust settings, and control operations. It translates complex data from the PLC into easy-to-understand graphical displays, such as touchscreens or computer interfaces. Essentially, HMI serves as the bridge between human operators and the automated control functions managed by the PLC.
Difference Between HMI and PLC?
HMI (Human-Machine Interface) and PLC (Programmable Logic Controller) serve different roles in industrial automation. HMI is a user interface that allows operators to interact with and control machinery, providing real-time data visualization and control capabilities. PLC, on the other hand, is a hardware device that executes programmed instructions to automate control processes and manage machinery operations. While the PLC handles the actual control tasks and decision-making, the HMI provides the interface for human operators to monitor and adjust these operations.
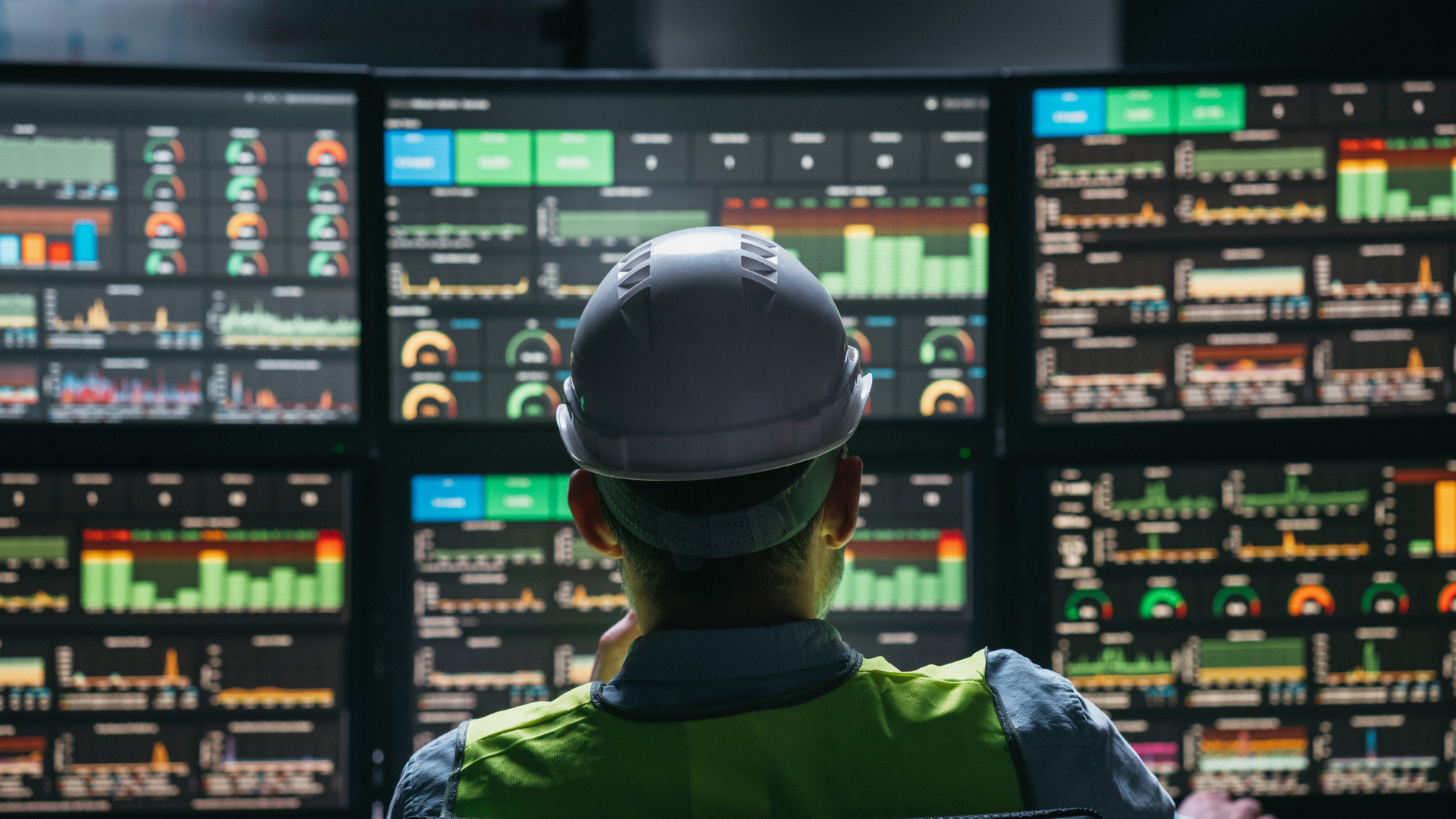
Which is Better HMI or SCADA?
HMI (Human-Machine Interface) and SCADA (Supervisory Control and Data Acquisition) are not directly comparable in terms of "better" because they serve different purposes and are often used together. HMI is focused on providing a user-friendly interface for operators to interact with machinery and control systems, offering real-time data visualization and control at a local level. SCADA, however, is a broader system designed for remote monitoring and control of entire industrial processes, integrating data from multiple sources, including HMIs, for wide-area supervision and data analysis. The choice between HMI and SCADA depends on the specific needs of the application: HMIs for localized control and SCADA for comprehensive, remote monitoring and management.
HMISCADA Software
HMISCADA software combines the functionalities of both HMI (Human-Machine Interface) and SCADA (Supervisory Control and Data Acquisition) systems. This integrated solution provides a unified platform for operators to interact with machinery, monitor real-time data, and control industrial processes. By combining the detailed visualization and control capabilities of HMI with the wide-area monitoring and data analysis features of SCADA, HMISCADA software enhances operational efficiency and decision-making. Examples of such integrated solutions include Wonderware by AVEVA and Ignition by Inductive Automation.
Difference Between HMI and PLC?
HMI (Human-Machine Interface) and PLC (Programmable Logic Controller) serve different functions in industrial automation. HMI is a user interface that allows operators to interact with machinery, providing real-time data visualization and control capabilities. PLC, on the other hand, is a hardware device that executes programmed instructions to automate control processes and manage machinery operations. While the PLC handles the actual control tasks and decision-making, the HMI provides the interface for human operators to monitor and adjust these operations.
Difference Between SCADA and PLC?
SCADA (Supervisory Control and Data Acquisition) and PLC (Programmable Logic Controller) serve distinct but complementary roles in industrial automation. SCADA is a comprehensive system designed for remote monitoring, data collection, and control of industrial processes across wide areas, integrating information from multiple sources to provide an overall system overview. PLC, on the other hand, is a specialized hardware device used for automating control processes by executing programmed instructions to manage machinery and equipment in real-time. While PLCs handle specific control tasks at the machine level, SCADA oversees and coordinates these tasks across the entire network, providing higher-level supervision and data analysis.
You might also like
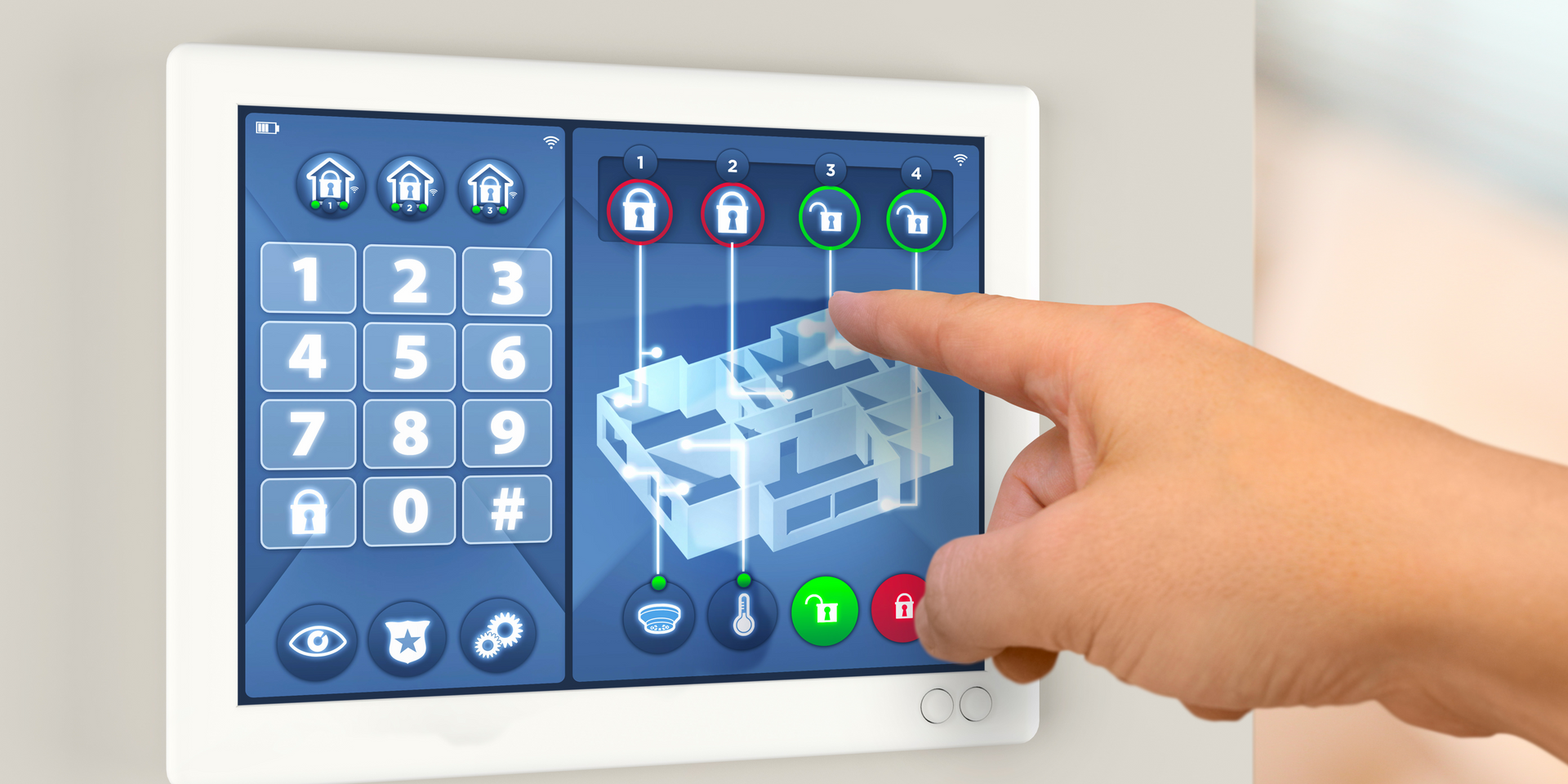
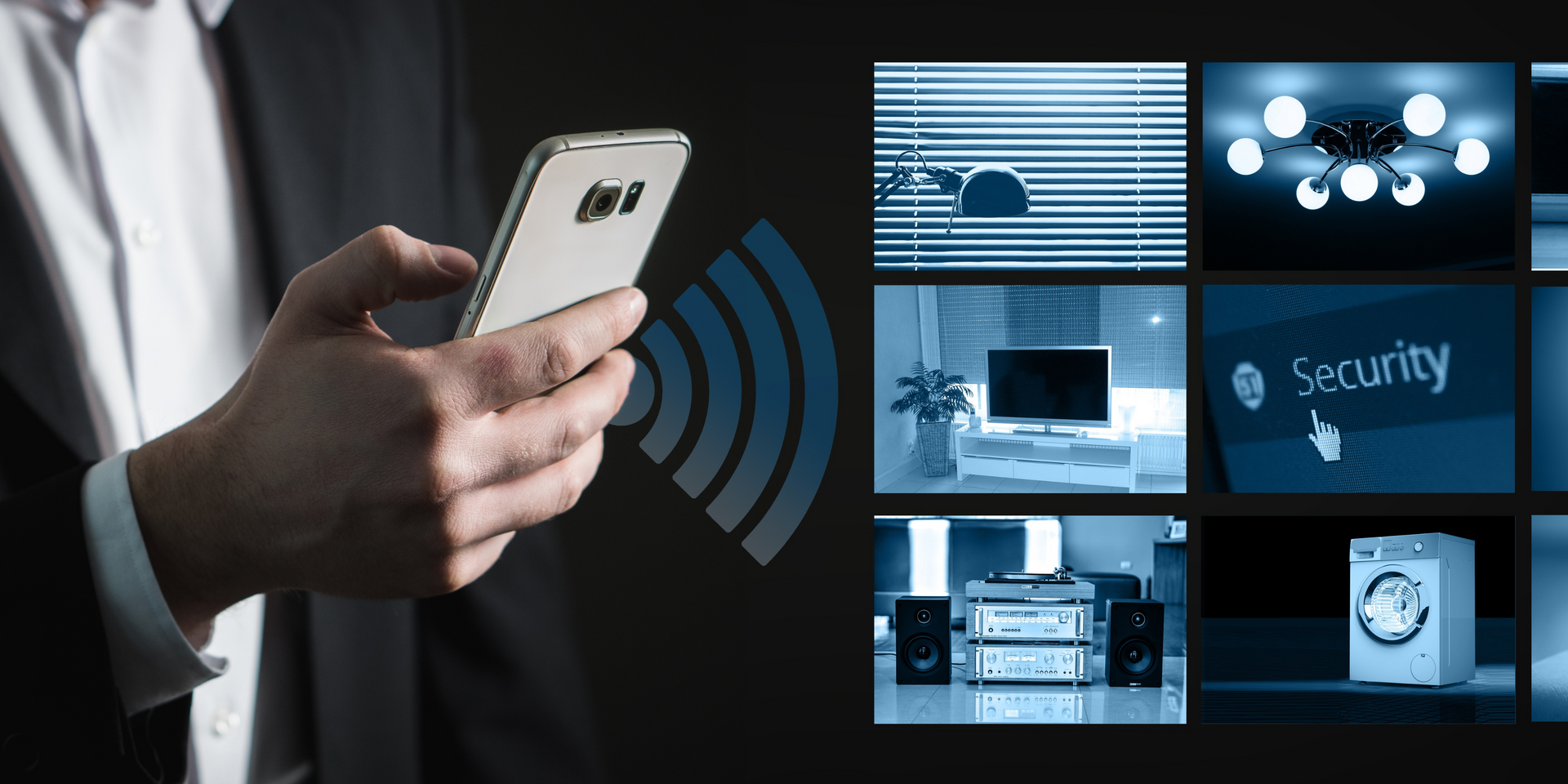
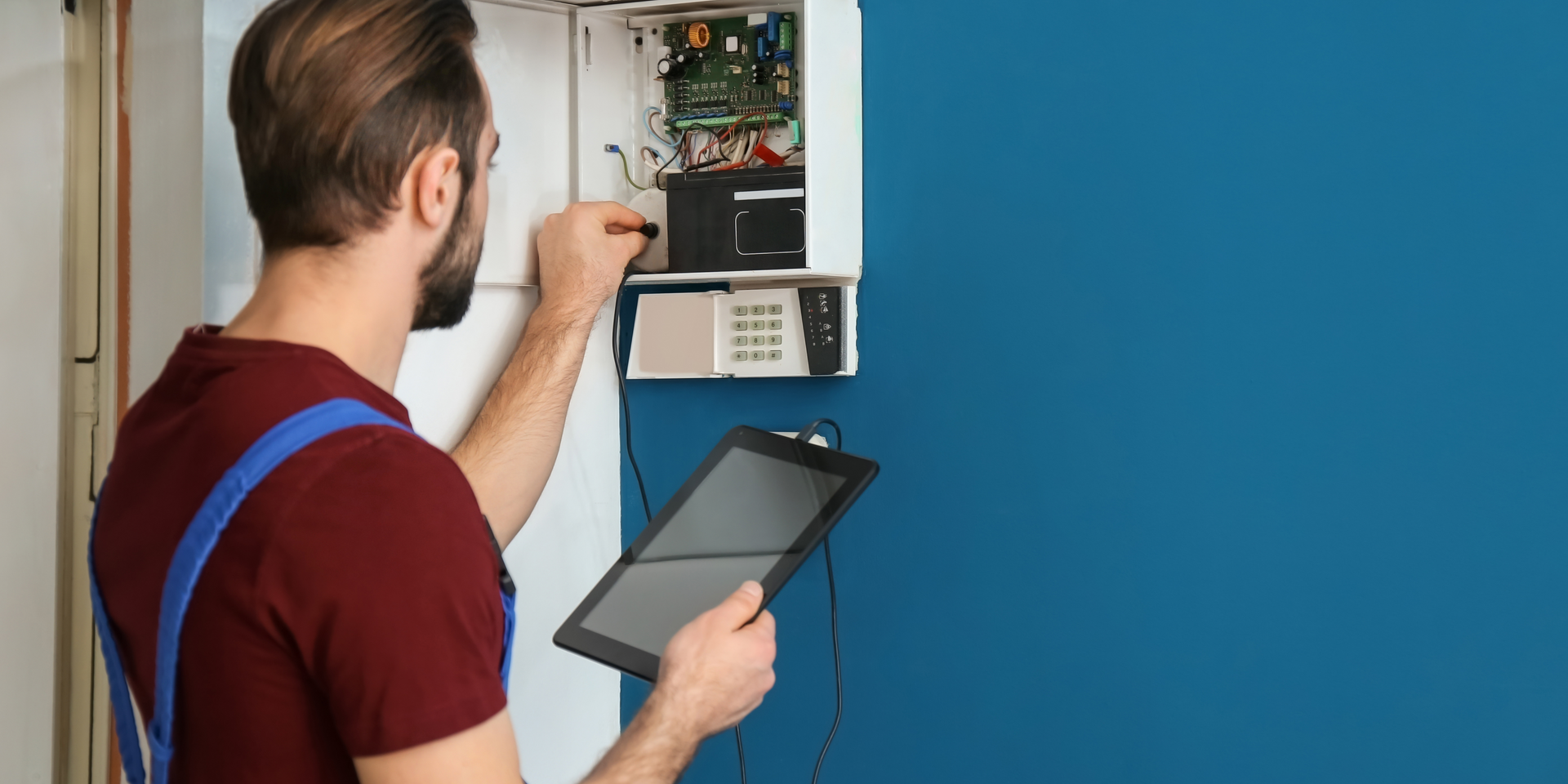