Is SCADA an MES System?
Is SCADA an MES System?
No, SCADA (Supervisory Control and Data Acquisition) is not an MES (Manufacturing Execution System). SCADA is a type of industrial control system used for monitoring and controlling industrial processes, typically in real-time, through hardware and software components. On the other hand, MES is a comprehensive system that manages and monitors manufacturing operations on the shop floor, ensuring efficient execution of production processes and improving production output. While SCADA focuses on real-time data acquisition and control, MES covers a broader range of functions, including production planning, inventory management, and quality control.
Is SAP an MES System?
MES system examples include platforms like SAP Manufacturing Execution. SAP is known for its comprehensive enterprise software solutions, and its Manufacturing Execution component specifically caters to managing and optimizing production processes on the shop floor. It integrates seamlessly with other SAP modules, providing real-time data and analytics to improve manufacturing efficiency, quality, and compliance. Thus, SAP Manufacturing Execution is indeed considered an MES system.
What is MES?
A Manufacturing Execution System (MES) is a software solution that monitors, manages, and synchronizes the execution of real-time physical processes involved in manufacturing. It provides a layer of systems that connect, monitor, and control complex manufacturing operations on the shop floor, ensuring effective production workflow and data management. MES systems help improve productivity, ensure quality control, and provide visibility into the manufacturing process by capturing data on production activities, resource utilization, and inventory management. They play a crucial role in integrating various aspects of the manufacturing process with enterprise resource planning (ERP) systems.
MES System
A Manufacturing Execution System (MES) is a dynamic software platform that manages and monitors manufacturing operations on the shop floor. It ensures that production processes are executed efficiently and effectively by providing real-time visibility, control, and optimization of manufacturing activities. MES systems capture data on production performance, quality, and inventory, integrating this information with higher-level enterprise resource planning (ERP) systems. This integration helps in streamlining workflows, reducing production costs, and improving overall product quality and compliance.
What is MES vs SCADA vs ERP?
MES (Manufacturing Execution System), SCADA (Supervisory Control and Data Acquisition), and ERP (Enterprise Resource Planning) serve distinct but complementary roles in industrial and manufacturing settings. MES focuses on managing and optimizing real-time production activities on the shop floor, ensuring efficient execution of manufacturing processes. SCADA is used for real-time monitoring and control of industrial processes, often involving data acquisition from sensors and control of equipment. ERP systems, on the other hand, provide a comprehensive platform for managing business operations, including finance, HR, supply chain, and inventory, integrating data across the entire organization to support strategic decision-making.
SCADA vs MES vs ERP
SCADA (Supervisory Control and Data Acquisition), MES (Manufacturing Execution System), and ERP (Enterprise Resource Planning) each serve unique functions in industrial and manufacturing environments. SCADA is used for real-time monitoring and control of industrial processes, gathering data from sensors and managing equipment operations. MES focuses on optimizing and managing shop floor production activities, ensuring efficient execution and capturing real-time data on production performance and quality. ERP systems provide a comprehensive platform for managing overall business operations, including finance, HR, supply chain, and inventory, integrating data across the organization for strategic decision-making.
SCADA Software
SCADA (Supervisory Control and Data Acquisition) software is designed for real-time monitoring and control of industrial processes. It collects data from sensors and devices on the production floor, providing operators with detailed insights into system performance and enabling remote control of equipment. SCADA systems help ensure the efficiency, safety, and reliability of industrial operations by detecting and responding to issues quickly. They are widely used in sectors such as manufacturing, energy, water management, and transportation to optimize process control and reduce downtime.
MES vs ERP
MES (Manufacturing Execution System) and ERP (Enterprise Resource Planning) serve different but complementary roles in an organization. MES focuses on managing and optimizing real-time production activities on the shop floor, capturing data on production performance, quality, and inventory. ERP, on the other hand, is a comprehensive system that integrates various business functions, such as finance, HR, supply chain, and inventory management, to provide a unified platform for strategic decision-making. While MES ensures efficient execution and control of manufacturing processes, ERP provides a broader view of the organization's resources and operations.
What is ERP vs SCADA vs MES?
ERP (Enterprise Resource Planning), SCADA (Supervisory Control and Data Acquisition), and MES (Manufacturing Execution System) each serve distinct roles in an industrial setting. ERP systems integrate and manage various business functions such as finance, HR, supply chain, and inventory, providing a unified platform for strategic decision-making across the organization. SCADA focuses on real-time monitoring and control of industrial processes, collecting data from sensors and enabling remote control of equipment. MES bridges the gap between ERP and SCADA by managing and optimizing real-time production activities on the shop floor, ensuring efficient execution and capturing data on production performance and quality.
MES SCADA Pyramid
The MES-SCADA pyramid represents the hierarchical structure of industrial automation systems. At the base, SCADA (Supervisory Control and Data Acquisition) handles real-time data collection and control from sensors and equipment, ensuring immediate process management. Above SCADA, the MES (Manufacturing Execution System) layer manages and optimizes production activities on the shop floor, using data from SCADA to improve efficiency and quality. At the top of the pyramid, ERP (Enterprise Resource Planning) systems integrate data from MES and other business functions to provide comprehensive strategic management and decision-making across the organization.
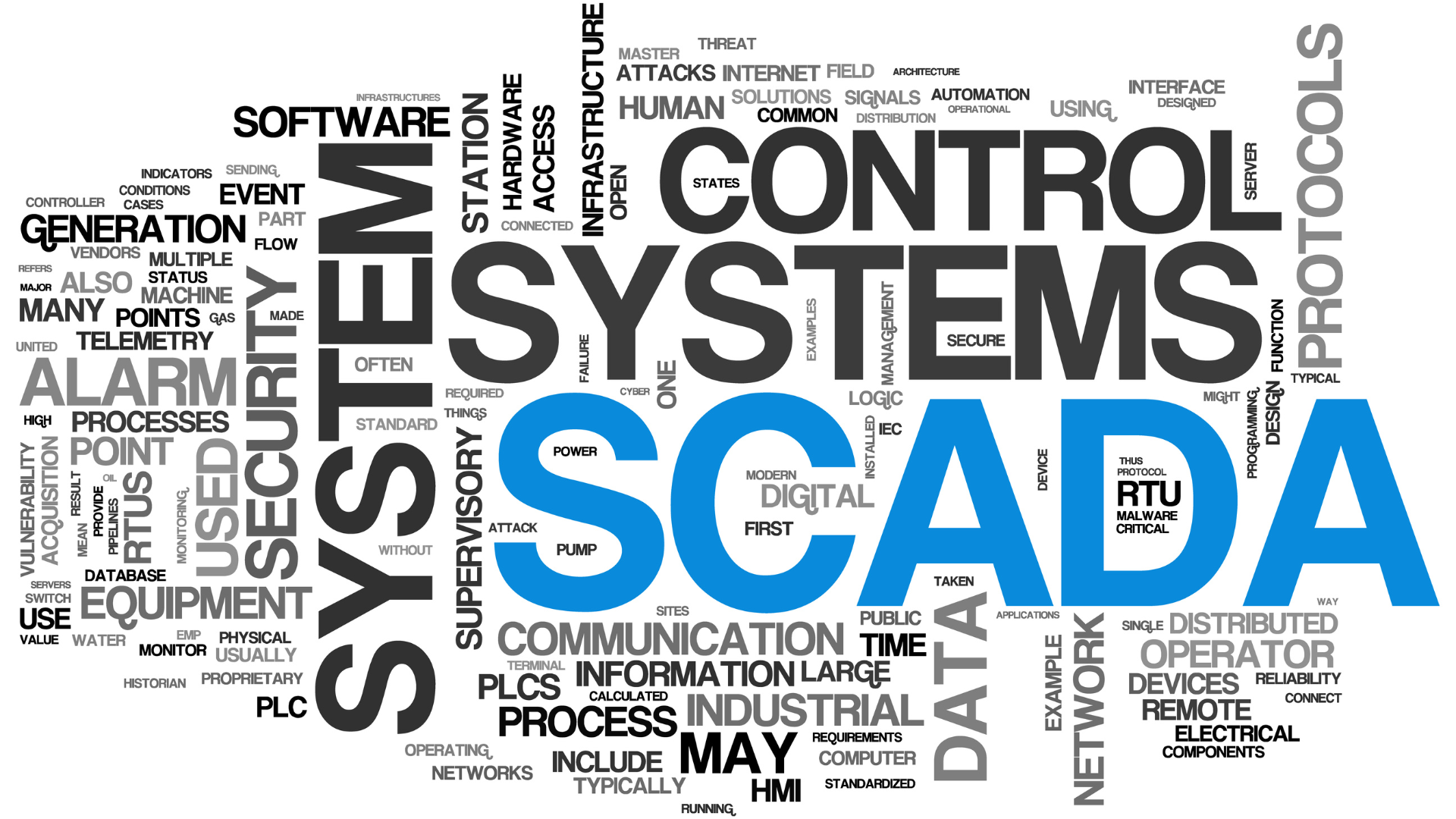
What is MES and PLC?
MES (Manufacturing Execution System) and PLC (Programmable Logic Controller) serve different functions in industrial automation. MES is a software system that manages and optimizes production activities on the shop floor, providing real-time data on production performance, quality, and inventory to ensure efficient manufacturing processes. PLC, on the other hand, is a hardware device used to control machinery and processes in real-time, executing programmed instructions to automate specific tasks and ensure precise control of industrial equipment. Together, MES and PLCs contribute to a cohesive manufacturing environment, with PLCs handling the control and automation and MES overseeing production management and optimization.
SCADA MES
SCADA (Supervisory Control and Data Acquisition) and MES (Manufacturing Execution System) are both essential in industrial automation but serve different roles. SCADA is used for real-time monitoring and control of industrial processes, gathering data from sensors and providing operators with tools to manage and control equipment remotely. MES, on the other hand, focuses on managing and optimizing production activities on the shop floor, ensuring efficient execution by using real-time data to monitor performance, quality, and inventory. While SCADA ensures immediate process control and data acquisition, MES integrates this data to improve overall production efficiency and effectiveness.
What Does MES Stand For?
MES stands for Manufacturing Execution System. It is a software solution designed to monitor, manage, and optimize production processes on the shop floor in real-time. MES systems capture data on production performance, quality, and inventory, helping to ensure efficient execution of manufacturing activities. By integrating with other enterprise systems, MES provides comprehensive insights and control over the entire manufacturing lifecycle, improving productivity and quality.
What is the Difference Between MES and PLC?
MES (Manufacturing Execution System) and PLC (Programmable Logic Controller) serve distinct roles in manufacturing. MES is a software platform that manages and optimizes production activities on the shop floor, providing real-time data on production performance, quality, and inventory. In contrast, a PLC is a hardware device used to control machinery and industrial processes by executing programmed instructions for tasks like automation and process control. While MES focuses on overall production management and efficiency, PLCs are responsible for the direct control and automation of specific equipment and processes within the production environment.
What are the 3 types of SCADA?
The three main types of SCADA systems are Monolithic, Distributed, and Networked. Monolithic SCADA systems, also known as standalone SCADA, were the earliest type, designed to work on a single computer system without network connectivity. Distributed SCADA systems came next, incorporating multiple systems connected through a LAN, allowing for better data sharing and redundancy. Networked SCADA systems are the most advanced, using modern network technologies, including the internet, to connect geographically dispersed systems, enhancing scalability, flexibility, and remote monitoring capabilities.
SCADA System
A SCADA (Supervisory Control and Data Acquisition) system is a comprehensive industrial control system used for real-time monitoring and control of various processes. It collects data from sensors and devices, providing operators with a centralized interface to manage equipment and processes remotely. SCADA systems ensure the efficient, safe, and reliable operation of industrial environments by enabling quick response to issues and optimizing process performance. They are widely utilized in industries such as manufacturing, energy, water management, and transportation.
SCADA Software List
SCADA software encompasses a variety of platforms designed for industrial control and monitoring. Prominent examples include Wonderware by AVEVA, known for its user-friendly interface and robust features; Ignition by Inductive Automation, which offers a modular approach and strong scalability; and GE Digital’s iFIX, which provides advanced data visualization and process control capabilities. These platforms are widely used across industries for real-time data acquisition, process automation, and system management, ensuring efficient and reliable operation of industrial processes.
Ignition SCADA
Ignition SCADA, developed by Inductive Automation, is a versatile and scalable industrial control software platform. It offers real-time monitoring, data acquisition, and process control, all within a modular architecture that allows for easy customization and expansion. Ignition is known for its web-based deployment, enabling remote access and management through a standard web browser, and its compatibility with various industrial protocols and databases. This flexibility makes Ignition a popular choice for industries looking to optimize their automation systems and improve operational efficiency.
You might also like
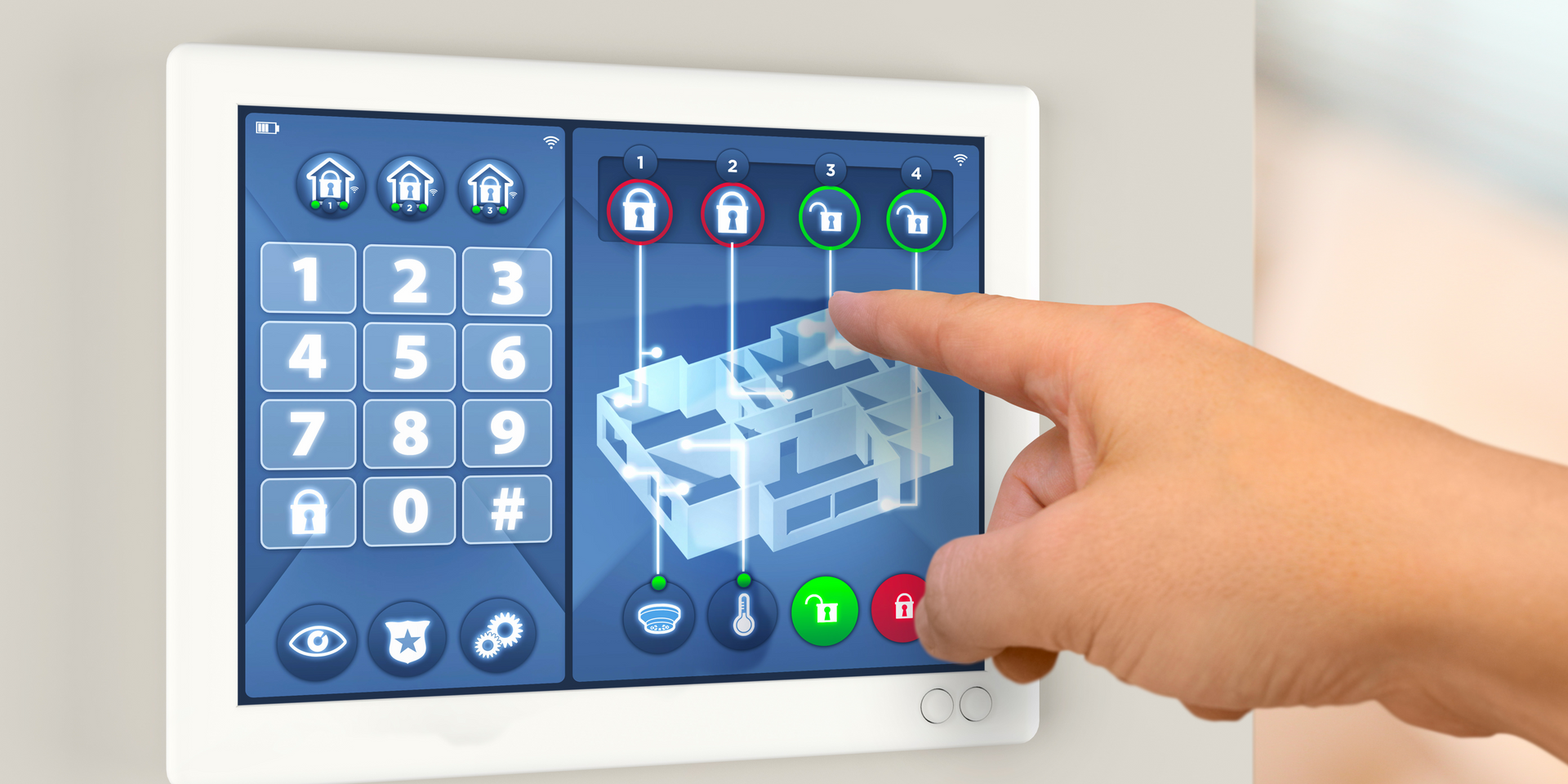
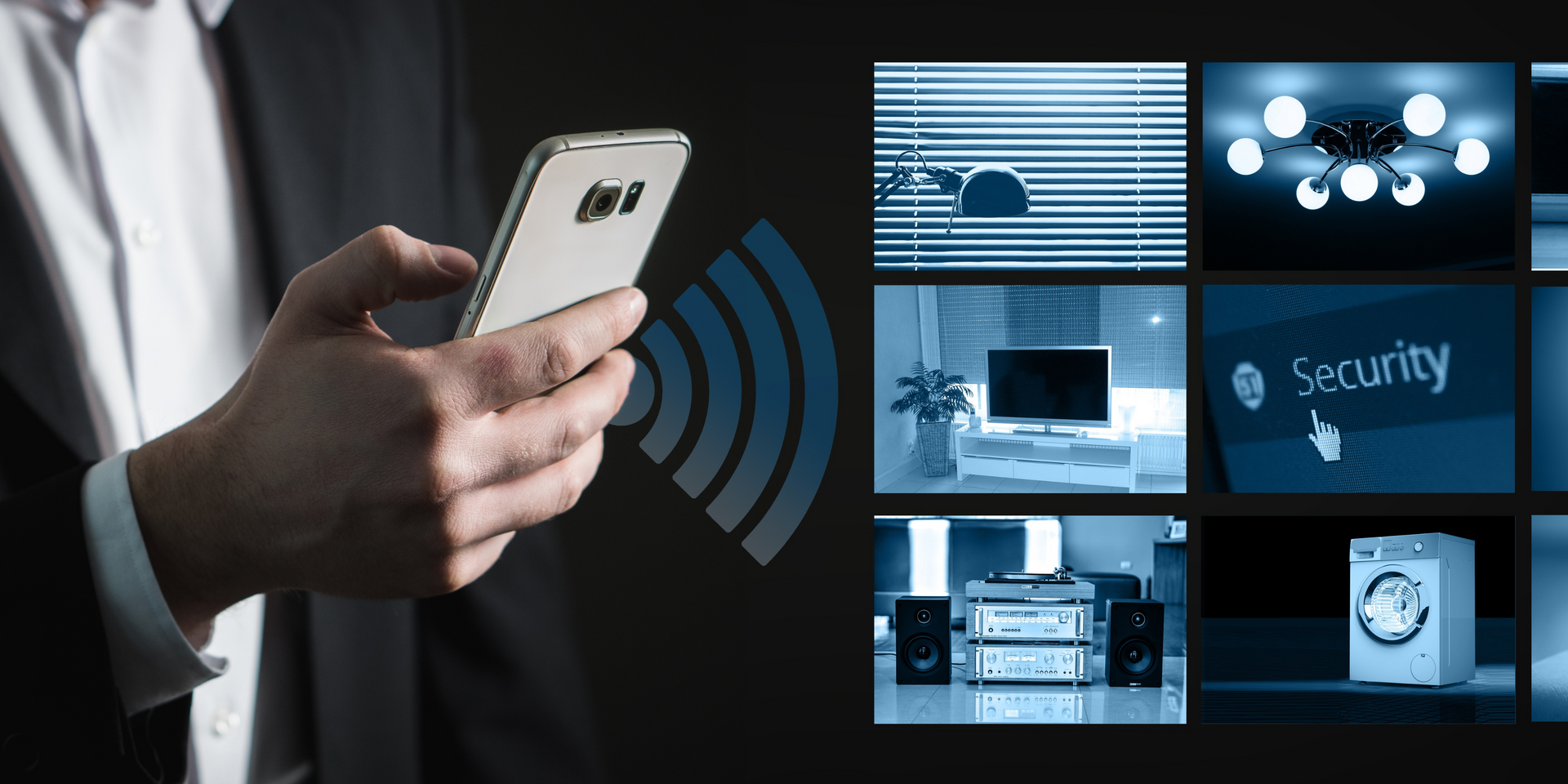
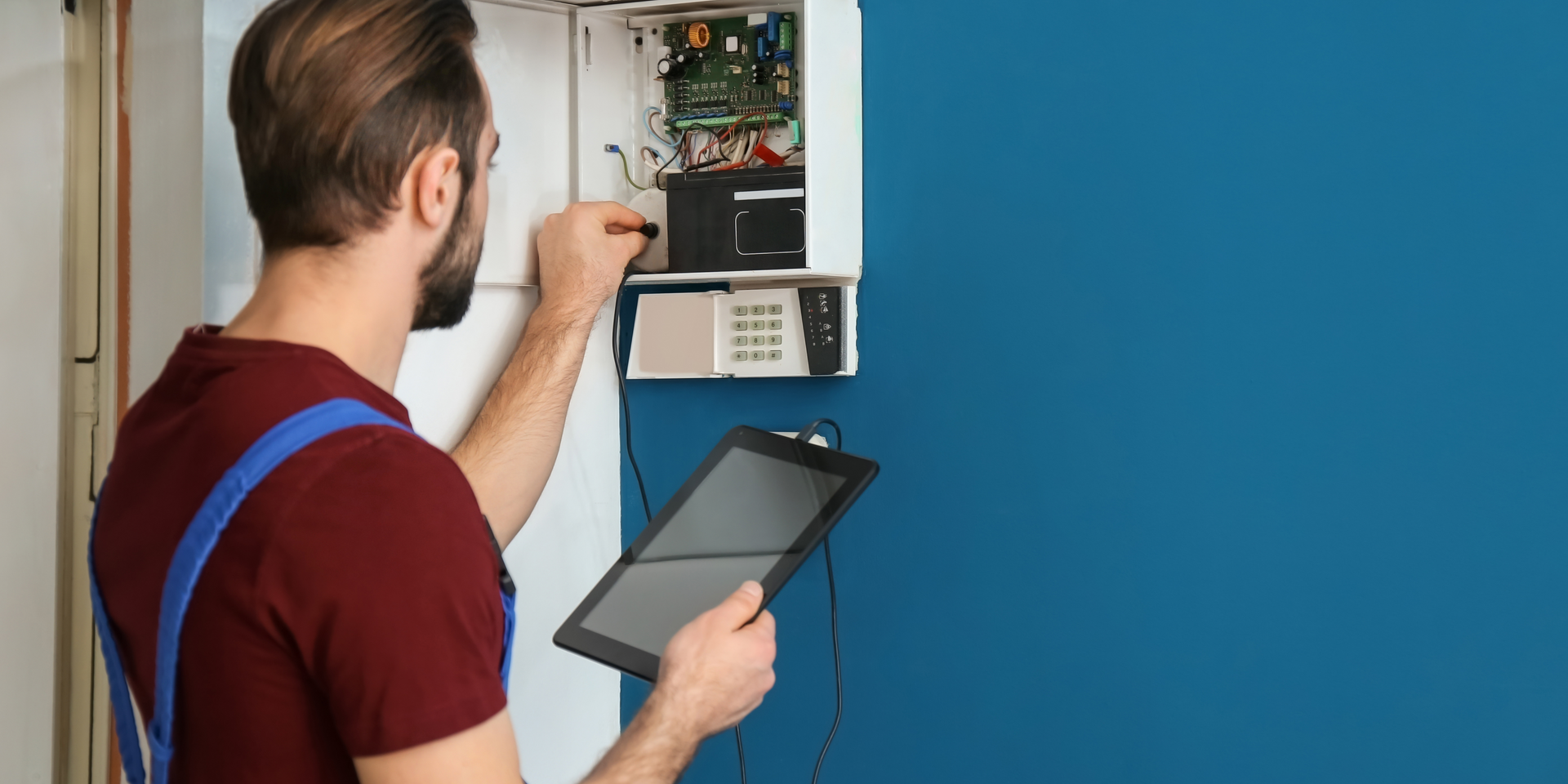