PLC vs. DCS vs. SCADA vs. HMI
Which is Better PLC or DCS or SCADA?
The choice between PLC, DCS, and SCADA depends on the specific needs of the industrial application. PLCs are ideal for discrete control and automation tasks in smaller, more straightforward systems due to their simplicity and cost-effectiveness. DCS is better suited for large, complex, and continuous processes, providing centralized control and high reliability. SCADA excels in systems requiring extensive real-time monitoring and remote control capabilities across geographically dispersed locations. As for "Which is Better HMI or SCADA", it depends on the context; HMI is a user interface for operator interaction, while SCADA encompasses a broader system for data acquisition and control, often including multiple HMIs within its architecture.
PLC DCS SCADA PDF
A PDF on PLC (Programmable Logic Controller), DCS (Distributed Control System), and SCADA (Supervisory Control and Data Acquisition) would provide a detailed overview of these key industrial automation technologies. PLCs are used for automating specific tasks and controlling machinery through programmed instructions. DCS offers centralized control for complex and continuous processes by distributing control functions across multiple controllers within a plant. SCADA systems focus on real-time monitoring and remote control of industrial processes, collecting data from sensors and providing a centralized interface for managing operations. The PDF would likely explore the unique features, applications, and benefits of each system, helping readers understand their roles and integration in industrial environments.
Which is Better HMI or SCADA?
"Which is better, HMI or SCADA?" depends on the specific requirements of the industrial application. HMI (Human-Machine Interface) is focused on providing a user-friendly interface for operators to interact with and control machinery and processes, displaying real-time data and control options. SCADA (Supervisory Control and Data Acquisition), on the other hand, encompasses a broader system that includes not only HMIs but also extensive data acquisition, process monitoring, and control capabilities across multiple locations. If you need comprehensive process control and data analysis, SCADA is the better choice; however, for straightforward, localized operator interface, an HMI might be sufficient.
What is HMI?
HMI (Human-Machine Interface) is a user interface that connects operators with the machinery and processes they control. It provides a graphical display of system data, allowing users to monitor real-time performance, issue commands, and adjust settings. HMIs are essential for simplifying complex industrial processes, making it easier for operators to interact with and manage equipment. They are widely used in various industries to enhance efficiency, safety, and ease of operation.
Why DCS is Preferred Over PLC?
DCS (Distributed Control System) is preferred over PLC (Programmable Logic Controller) in large-scale, complex, and continuous industrial processes due to its centralized control and high reliability. DCS integrates multiple controllers and distributes control functions across the system, providing seamless coordination and redundancy. This centralized approach enhances system stability, simplifies management of extensive processes, and allows for sophisticated control strategies. Additionally, DCS systems often offer better scalability and integration with other enterprise systems, making them ideal for complex operations.
DCS vs PLC
DCS (Distributed Control System) and PLC (Programmable Logic Controller) serve different purposes in industrial automation. DCS is designed for complex, large-scale, and continuous processes, providing centralized control and high reliability by distributing control functions across multiple controllers. It excels at managing extensive processes with seamless integration and sophisticated control strategies. In contrast, PLCs are ideal for discrete control tasks and smaller, more straightforward automation applications, offering simplicity, cost-effectiveness, and flexibility for specific machine or process control needs.
Difference Between SCADA and DCS?
SCADA (Supervisory Control and Data Acquisition) and DCS (Distributed Control System) are both used for process control but have different focuses. SCADA is primarily designed for real-time monitoring and remote control of industrial processes across geographically dispersed locations, providing a centralized interface for data acquisition and management. DCS, on the other hand, is used for centralized control of complex, continuous processes within a single facility or plant, distributing control functions across multiple controllers for enhanced reliability and integration. While SCADA is ideal for large-scale monitoring and remote operations, DCS excels in managing intricate, localized processes with high stability and coordination.
Can SCADA and DCS Work Together?
Yes, SCADA and DCS can work together to enhance industrial automation and control. By integrating SCADA's real-time monitoring and remote control capabilities with DCS's centralized and distributed control functions, organizations can achieve comprehensive oversight and management of both local and remote processes. This collaboration allows for seamless data sharing, improved system efficiency, and enhanced decision-making by combining the strengths of both systems. The integration ensures that complex processes are managed effectively while also allowing for remote supervision and control.
Difference Between PLC SCADA and DCS PPT?
A PowerPoint presentation on the difference between PLC, SCADA, and DCS would outline the distinct roles and applications of each system in industrial automation. PLC (Programmable Logic Controller) is highlighted for its role in automating specific tasks and controlling machinery through pre-programmed instructions, making it ideal for discrete and small-scale processes. SCADA (Supervisory Control and Data Acquisition) is emphasized for its capabilities in real-time monitoring, data acquisition, and remote control across geographically dispersed locations. DCS (Distributed Control System) is described for its centralized management of complex, continuous processes within a single facility, distributing control functions across multiple controllers for enhanced reliability and integration.
How Do You Differentiate Between PLC SCADA DCS and HMI?
PLC (Programmable Logic Controller), SCADA (Supervisory Control and Data Acquisition), DCS (Distributed Control System), and HMI (Human-Machine Interface) each serve distinct roles in industrial automation. PLCs are hardware devices used to automate specific processes and control machinery through programmed instructions. SCADA systems provide real-time monitoring and remote control of industrial processes, collecting data from sensors and managing operations across large geographic areas. DCS offers centralized control for complex and continuous processes within a single facility, distributing control functions across multiple controllers for improved reliability. HMIs are user interfaces that allow operators to interact with and control machinery, displaying real-time data and system status for efficient operation.
PLC vs DCS vs SCADA vs HMI
PLC (Programmable Logic Controller), DCS (Distributed Control System), SCADA (Supervisory Control and Data Acquisition), and HMI (Human-Machine Interface) each serve unique functions in industrial automation. PLCs are hardware devices that automate specific tasks and control machinery through pre-programmed instructions, making them ideal for discrete processes. DCS is designed for centralized control of complex, continuous processes within a facility, distributing control functions across multiple controllers for high reliability. SCADA systems provide real-time monitoring and remote control of industrial processes over large geographic areas, while HMIs serve as user interfaces that allow operators to interact with and control these systems, displaying real-time data and system status for efficient operation.
Is HMI and PLC the Same?
No, HMI (Human-Machine Interface) and PLC (Programmable Logic Controller) are not the same. A PLC is a hardware device used to automate specific processes and control machinery by executing pre-programmed instructions. In contrast, an HMI is a user interface that allows operators to interact with and control machinery, displaying real-time data and system status. While a PLC controls the automation processes, an HMI provides the visual interface for users to monitor and manage those processes effectively.
PLC and HMI Programming
PLC and HMI programming are essential components of industrial automation. PLC programming involves writing code, typically in ladder logic or other programming languages, to automate specific tasks and control machinery. This programming defines how the PLC will respond to various inputs and control outputs to execute the desired operations. HMI programming, on the other hand, focuses on designing user interfaces that allow operators to interact with the PLC-controlled processes, providing real-time data visualization, control options, and system feedback through graphical displays. Together, these programs ensure efficient and intuitive control of automated systems.
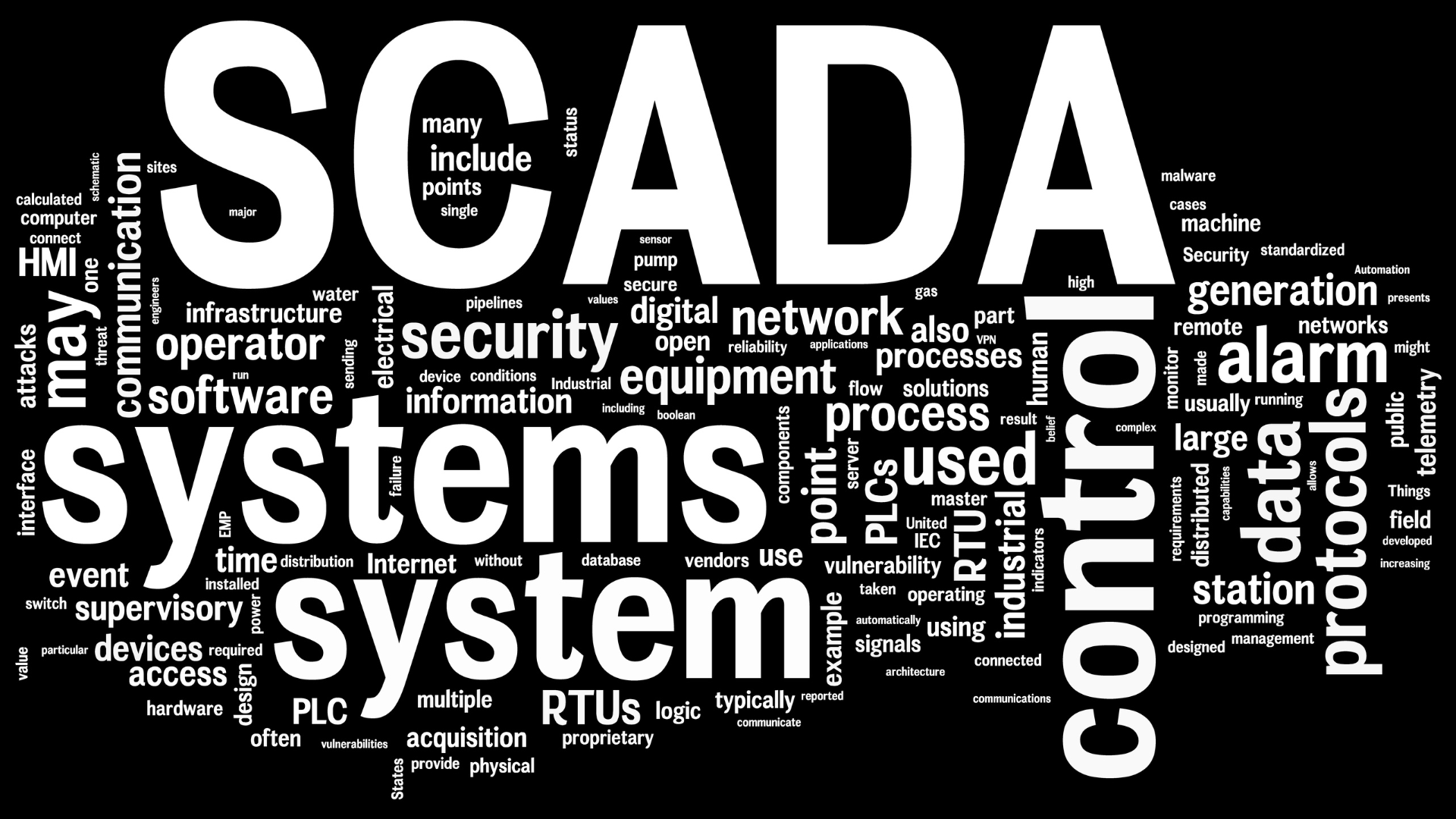
What is SCADA, PLC and DCS?
SCADA (Supervisory Control and Data Acquisition) is a system used for monitoring and controlling industrial processes. It collects data from sensors and instruments located at remote sites and transmits this data to a central computer, where it is processed and displayed for human operators to monitor and control.
PLC (Programmable Logic Controller) is a type of computer used in industrial automation to control machinery and processes. It is designed for real-time use and can be programmed to perform specific functions, such as timing, counting, and sequencing operations.
DCS (Distributed Control System) is an automated control system that distributes control functions throughout a plant or factory, rather than having them centralized. It consists of multiple controllers distributed throughout the system, each responsible for controlling different parts of the process, providing higher reliability and scalability.
DCS vs SCADA
DCS (Distributed Control System) and SCADA (Supervisory Control and Data Acquisition) are both used for industrial process control, but they have different focuses. DCS is designed for complex, continuous processes within a plant, with control functions distributed across various controllers for high reliability and real-time control. SCADA, on the other hand, is used for monitoring and controlling processes over large geographic areas, such as utilities and infrastructure, emphasizing remote data collection, centralized monitoring, and supervisory control. While DCS is more focused on process control and automation within a facility, SCADA is geared towards data acquisition and remote process management.
PLC vs SCADA
PLC (Programmable Logic Controller) and SCADA (Supervisory Control and Data Acquisition) serve different roles in industrial automation. A PLC is a rugged, real-time computer used to control machinery and processes by executing programmed instructions for tasks like timing, counting, and sequencing. SCADA, on the other hand, is a system used for remote monitoring and control, gathering data from various sensors and devices and providing a centralized interface for operators to oversee and manage processes. While PLCs handle the direct control and automation at the machine level, SCADA systems provide the overarching supervisory control and data analysis across broader operations.
What Should I Learn First SCADA or PLC?
It's generally recommended to learn PLCs (Programmable Logic Controllers) first because they form the foundational building blocks of industrial automation. Understanding PLCs will give you insights into how control systems operate, as they are directly involved in managing machinery and processes. Once you have a solid grasp of PLCs, learning SCADA (Supervisory Control and Data Acquisition) will be easier, as it builds on the concepts of monitoring and controlling these systems on a larger scale, providing a comprehensive view and control of the entire process.
PLC SCADA HMI Course
Here are a few sample courses for learning PLC, SCADA, and HMI:
- PLC Programming for Beginners: This course introduces the basics of PLC programming, covering ladder logic, input/output devices, timers, and counters. It is designed for those new to industrial automation and provides hands-on exercises to build practical skills.
- SCADA Systems Fundamentals: This course covers the essentials of SCADA systems, including architecture, communication protocols, and real-time data acquisition. It focuses on the implementation and management of SCADA for monitoring and controlling industrial processes.
- HMI Design and Implementation: This course teaches the principles of Human-Machine Interface (HMI) design, including screen layout, user interaction, and visualization techniques. Students learn to create effective HMI applications that improve operator efficiency and system monitoring.
Difference Between PLC and SCADA?
PLC (Programmable Logic Controller) is a hardware-based system used to control machinery and processes in real-time through programmed instructions. It operates at the machine level, executing tasks such as timing, counting, and sequencing. SCADA (Supervisory Control and Data Acquisition), on the other hand, is a software-based system used for remote monitoring and control of industrial processes over large areas. It collects data from various sensors and devices, providing a centralized interface for operators to monitor, analyze, and control the processes.
PLC SCADA DCS Interview Questions
What is the main function of a PLC in industrial automation?
- A PLC (Programmable Logic Controller) is used to automate machinery and processes in industrial settings. It executes programmed instructions to control inputs and outputs, performing tasks such as timing, counting, and sequencing operations in real-time.
How does SCADA improve process control in industrial environments?
- SCADA (Supervisory Control and Data Acquisition) improves process control by providing real-time monitoring and control over industrial processes across large geographic areas. It collects data from various sensors and devices, allowing operators to supervise, analyze, and make informed decisions to optimize efficiency and address issues promptly.
What distinguishes DCS from SCADA in terms of system architecture?
- DCS (Distributed Control System) distributes control functions across multiple controllers within a plant, ensuring high reliability and real-time control of complex processes. In contrast, SCADA focuses on centralized monitoring and control, primarily used for overseeing processes over vast areas, making it suitable for utilities and infrastructure management.
PLC DCS and SCADA
PLC (Programmable Logic Controller) is a specialized computer used in industrial automation to control machinery and processes in real-time through programmed instructions. DCS (Distributed Control System) is designed for managing complex, continuous processes within a plant, distributing control functions across multiple controllers for high reliability and real-time control. SCADA (Supervisory Control and Data Acquisition) systems focus on remote monitoring and control of industrial processes over large geographic areas, collecting and analyzing real-time data from various sensors to provide centralized supervision. Together, these systems enhance industrial automation by improving process control, efficiency, and reliability.
PLC DCS SCADA Difference
PLC (Programmable Logic Controller) is a hardware-based system used for controlling individual machinery and processes in real-time with programmed logic. DCS (Distributed Control System) manages complex, continuous processes within a plant by distributing control functions across multiple controllers, providing high reliability and real-time control. SCADA (Supervisory Control and Data Acquisition) is a software-based system used for remote monitoring and control of industrial processes over large areas, emphasizing centralized data collection and supervision. While PLCs focus on direct machine control, DCS is geared towards integrated plant control, and SCADA provides overarching supervisory control and data analysis.
DCS Full Form
DCS stands for Distributed Control System. It is an automated control system that distributes control functions across multiple controllers throughout a plant or industrial facility. This architecture enhances system reliability and allows for real-time control and monitoring of complex, continuous processes. DCS is commonly used in industries like oil and gas, chemical, and power generation to manage and optimize production processes.
You might also like
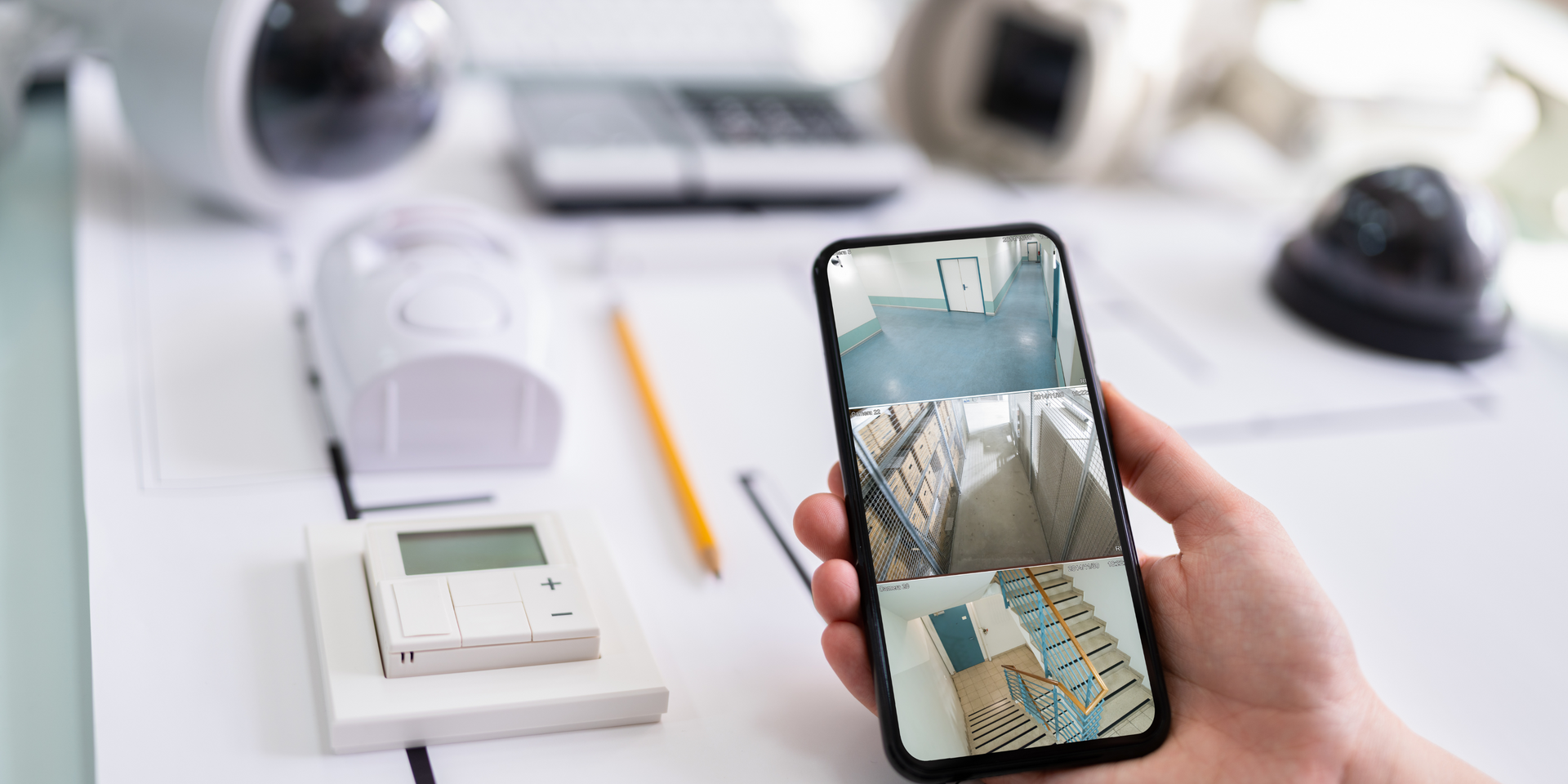
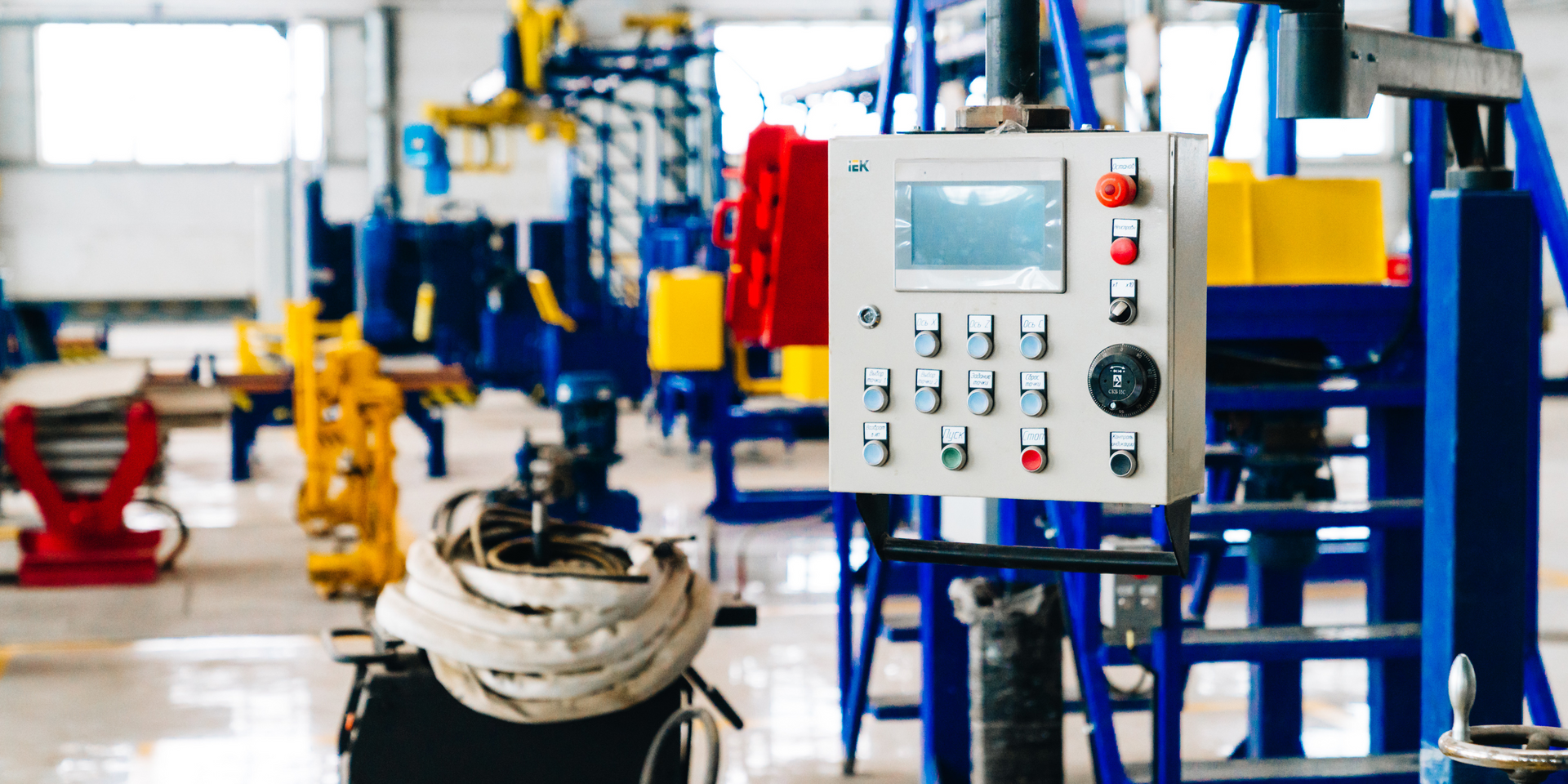
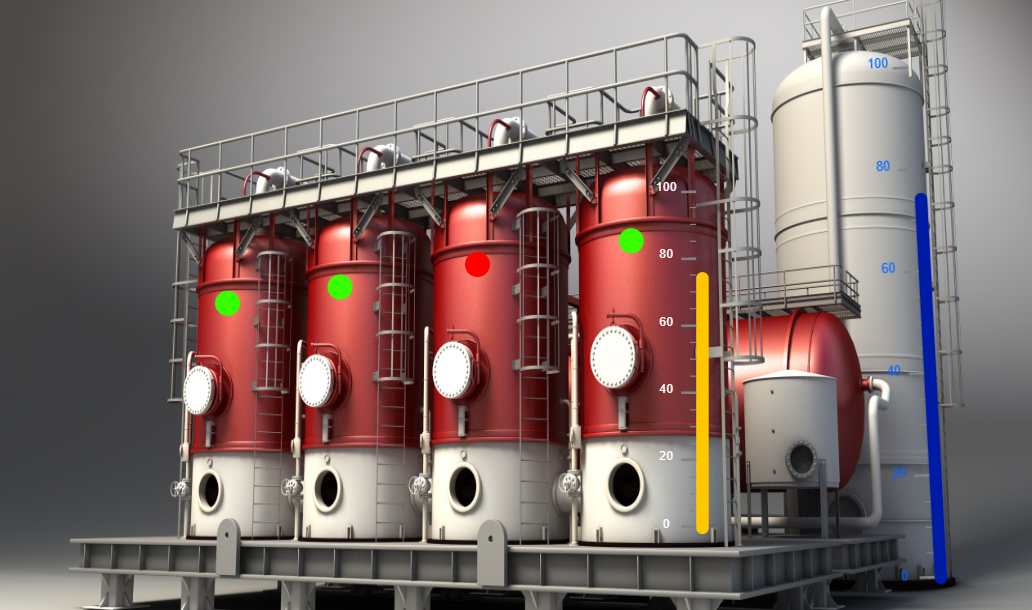