HMI PLC Combo
Why HMI is Not Communicating With PLC
HMI (Human-Machine Interface) may not be communicating with a PLC (Programmable Logic Controller) due to issues such as incompatible communication protocols, faulty wiring, or configuration errors in the system settings. Resolving these issues typically involves checking the connection settings and ensuring both devices are properly configured. When considering control systems, a common question arises: Which is better, HMI or SCADA? The answer depends on the specific needs of the application, as each system has its advantages.
HMI With Inbuilt PLC
HMI with an inbuilt PLC offers a seamless solution by combining control and visualization in a single unit, reducing the need for separate hardware components. This integration simplifies installation, programming, and maintenance, leading to cost savings and enhanced efficiency. It’s an ideal choice for smaller applications where space and budget are considerations without compromising on performance.
HMI and PLC Communication
Effective communication between HMI and PLC is crucial for real-time monitoring and control of industrial processes. This communication typically relies on established protocols like Modbus, Ethernet/IP, or Profibus, ensuring data is accurately exchanged between the devices. Proper configuration and testing are essential to maintain a stable connection, enabling operators to interact smoothly with the system and make informed decisions.
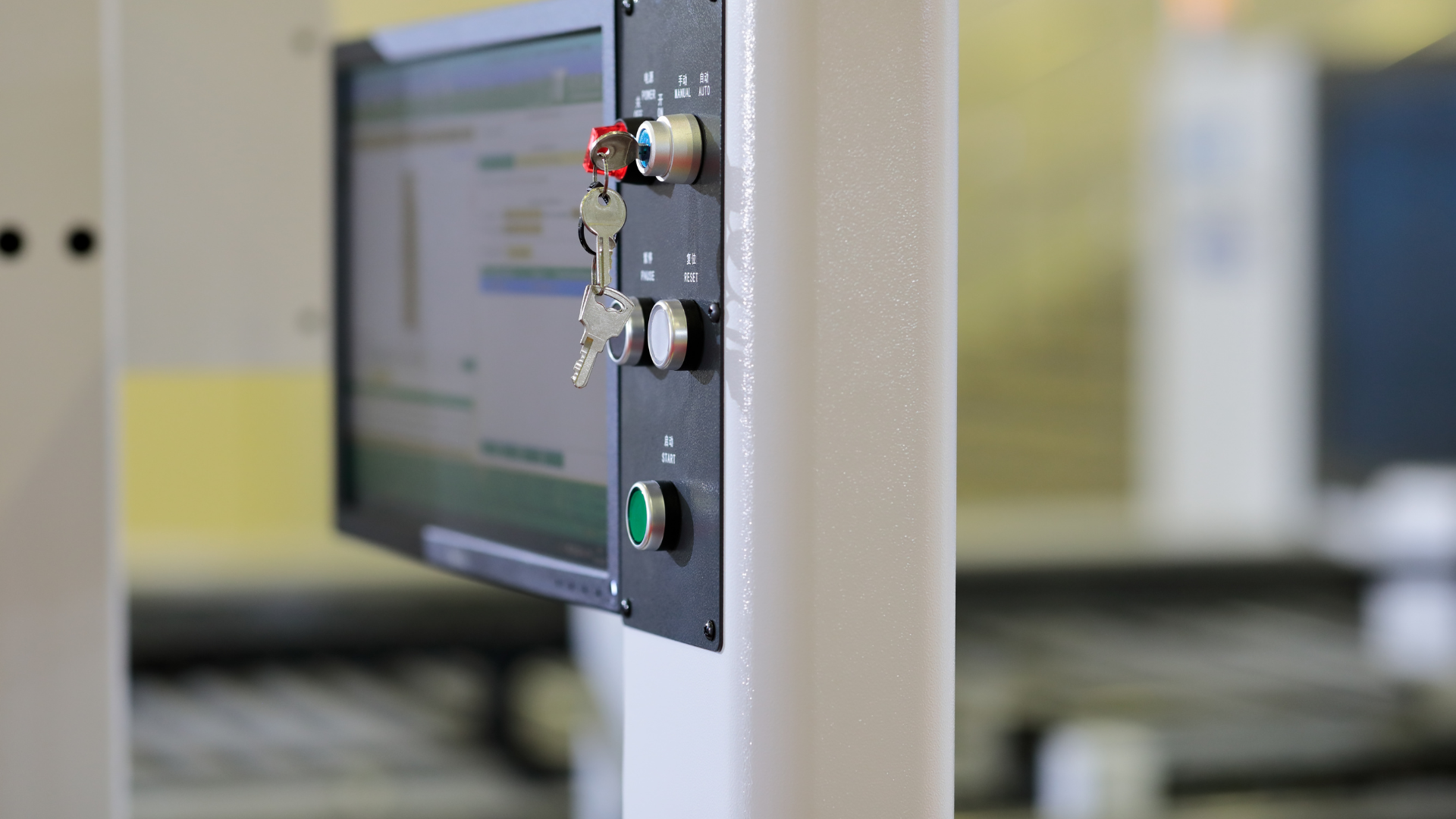
What Connection is Used Between an HMI and PLC
The connection between an HMI and PLC typically relies on communication protocols such as Modbus, Ethernet/IP, Profibus, or RS-232/485, depending on the system's requirements. These protocols ensure reliable data exchange, allowing the HMI to monitor and control the PLC's operations in real-time. Choosing the right connection type is crucial for maintaining efficient communication, minimizing latency, and ensuring the system operates smoothly.
HMI PLC All in One
An HMI PLC all-in-one system combines the functionalities of a Human-Machine Interface and a Programmable Logic Controller into a single, compact unit. This integration streamlines system design, reducing the need for separate components and simplifying the overall setup process. Ideal for smaller to medium-sized applications, it offers efficient control, monitoring, and visualization in a cost-effective and space-saving package.
Can HMI Work Without PLC
Yes, an HMI can work without a PLC in certain applications, especially when the HMI is integrated with its own control capabilities or is used solely for data visualization and monitoring. In such cases, the HMI can interface directly with sensors, drives, or other smart devices. However, for more complex control tasks, pairing the HMI with a PLC is essential to provide the necessary logic and automation capabilities.
Does an HMI Need Programming
Yes, an HMI needs programming to function effectively, as it requires configuration to display data, control processes, and interact with the connected devices. Programming an HMI typically involves designing screens, setting up communication protocols, and creating control logic or visual elements that allow operators to monitor and manage systems. The programming process is crucial for customizing the HMI to meet specific application needs.
PLC and HMI Programming
PLC and HMI programming are essential tasks that involve configuring both the control logic in the PLC and the user interface in the HMI. PLC programming focuses on creating sequences and operations that automate processes, while HMI programming involves designing interfaces that allow users to monitor and interact with these processes. Together, they form a cohesive system that ensures efficient control, visualization, and management of industrial operations.

Is an HMI a PLC
No, an HMI (Human-Machine Interface) is not a PLC (Programmable Logic Controller). An HMI is a user interface device that allows operators to interact with and monitor the processes controlled by the PLC. While an HMI provides visual representation and control inputs, the PLC is responsible for executing the automation logic and controlling the machinery or processes.
What is the Difference Between HMI and PLC
The primary difference between an HMI and a PLC lies in their functions. A PLC is a control device that runs automation logic, controlling machines and processes based on programmed instructions. In contrast, an HMI is a user interface that allows operators to interact with the PLC, providing visual displays of data and control inputs. While the PLC handles the logic and control, the HMI focuses on making the system user-friendly and accessible.
What is HMI and PLC
HMI (Human-Machine Interface) is a user interface that allows operators to interact with and monitor machinery or processes in an industrial environment. PLC (Programmable Logic Controller) is a specialized computer used to control automated systems and machinery by executing pre-programmed instructions. Together, HMIs and PLCs form the backbone of industrial automation, with the HMI providing a visual interface for real-time control and the PLC handling the underlying logic and operations.
HMI PLC Combo
An HMI PLC combo is a single device that combines the functionalities of both a Human-Machine Interface and a Programmable Logic Controller. This integration streamlines system design by reducing the need for separate components, making it easier to install, configure, and maintain. Ideal for compact and cost-effective automation solutions, the HMI PLC combo offers both control and visualization in one powerful package, simplifying the overall system architecture.
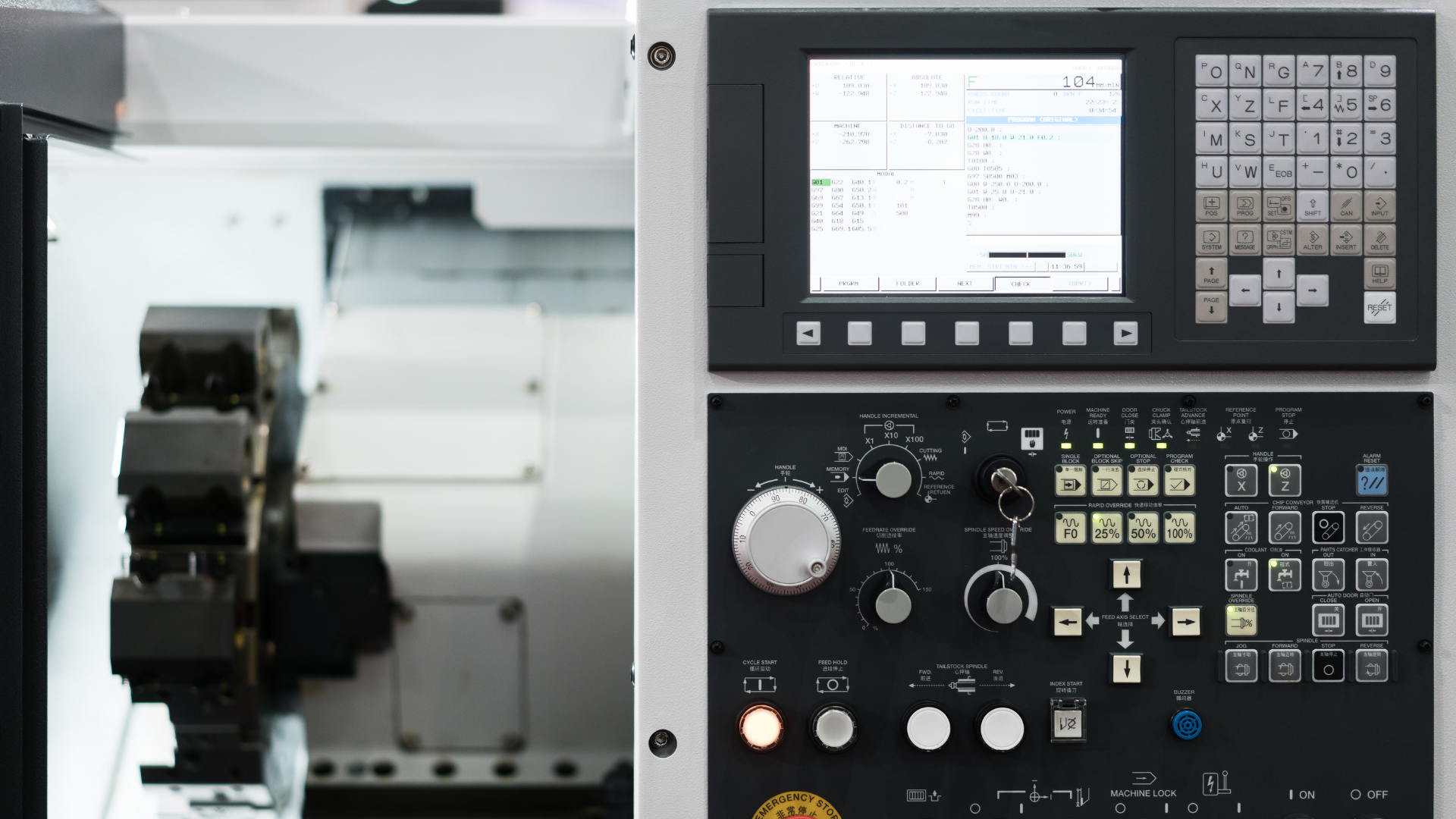
Are SCADA and HMI the Same
PLC vs DCS vs SCADA vs HMI
PLC (Programmable Logic Controller), DCS (Distributed Control System), SCADA (Supervisory Control and Data Acquisition), and HMI (Human-Machine Interface) each play distinct roles in industrial automation. A PLC is focused on executing specific control tasks, while a DCS manages complex processes across multiple locations with a high degree of coordination. SCADA systems provide comprehensive monitoring and control over large-scale operations, often integrating multiple PLCs and other devices. HMIs, on the other hand, serve as the user interface, allowing operators to interact with and manage these systems visually.
Difference Between HMI and SCADA
HMI and SCADA are both critical in industrial automation but serve different purposes. An HMI is primarily a user interface that allows operators to interact with machines and processes on a localized level, providing real-time data visualization and control. SCADA, however, is a broader system that includes not only HMIs but also data acquisition, processing, and supervisory control across multiple locations, enabling centralized monitoring and management of large-scale operations.
Can You Use an HMI Without a PLC
HMI Full Form
HMI stands for Human-Machine Interface, a technology that allows humans to interact with machines and industrial processes through graphical displays and control panels. It provides a user-friendly interface for monitoring data, controlling machinery, and visualizing system performance in real time. HMIs are essential in various industries, enabling efficient and intuitive operation of complex systems.
PLC Full Form
PLC stands for Programmable Logic Controller, a robust industrial computer used for automating electromechanical processes, such as controlling machinery, factory assembly lines, or production systems. PLCs are designed to handle complex control tasks with high reliability, making them a key component in industrial automation and process control. They are programmable, allowing customization to meet specific application requirements.
Can We Write a PLC Input From PLC
HMI PLC Combo Download
HMI PLC combo downloads typically include the necessary software tools for configuring both the HMI interface and the integrated PLC control logic. These downloads often come with pre-built templates, drivers, and libraries that simplify the setup process, enabling quick deployment of the all-in-one system. Ensuring you have the correct and latest version of the software is crucial for compatibility and optimal performance.
HMI PLC Combo Software
HMI PLC combo software provides a unified platform for programming and configuring the combined functionalities of both the HMI and PLC. This software allows users to design control logic, create user-friendly interfaces, and establish communication protocols within a single environment. It streamlines the development process, reduces complexity, and enhances the efficiency of setting up and maintaining integrated control systems.
How to Integrate PLC With HMI
PLC HMI
A PLC HMI system integrates a Programmable Logic Controller (PLC) with a Human-Machine Interface (HMI) to provide a comprehensive solution for industrial automation. The PLC handles the control logic and processes automation, while the HMI offers a user-friendly interface for monitoring and managing these processes. This combination enables real-time data visualization, control adjustments, and system diagnostics, improving operational efficiency and user interaction.
Low Cost PLC with HMI
A low-cost PLC with HMI offers a budget-friendly solution for industrial automation, combining control and visualization in a single, economical package. This integration simplifies the system setup and reduces the need for separate hardware components, making it ideal for smaller applications where cost is a primary concern. Despite the lower price point, these systems can still provide robust performance and essential functionalities for efficient process control.
What Can Be Used Instead of PLC
Instead of a traditional PLC, alternatives such as programmable logic controllers (PLCs) with integrated HMIs, distributed control systems (DCS), or microcontrollers can be used for automation and control tasks. These alternatives may offer different features or advantages depending on the application, such as reduced cost, increased flexibility, or more compact design. Evaluating the specific needs of the application will help determine the best substitute for a PLC.
You might also like
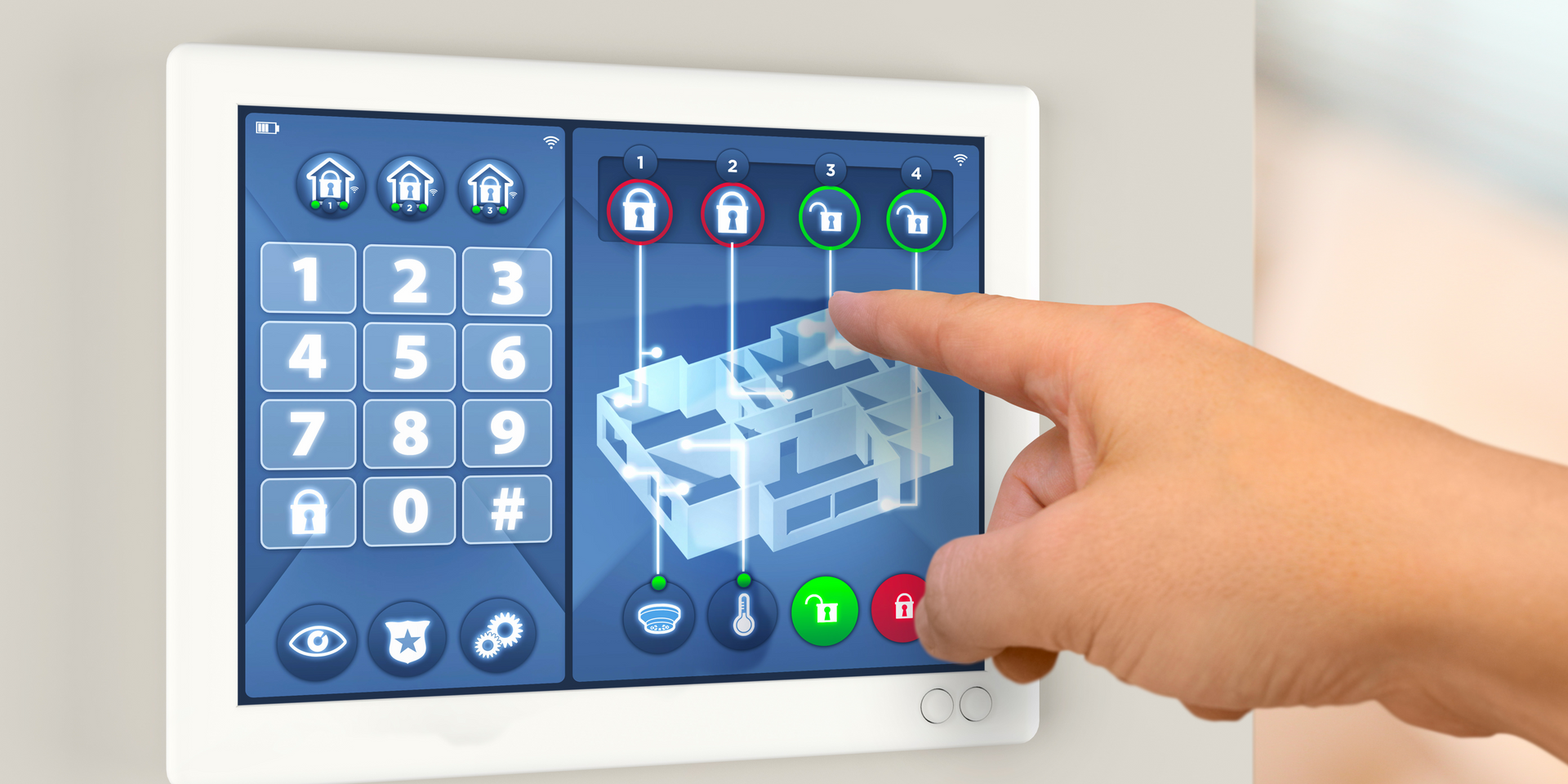
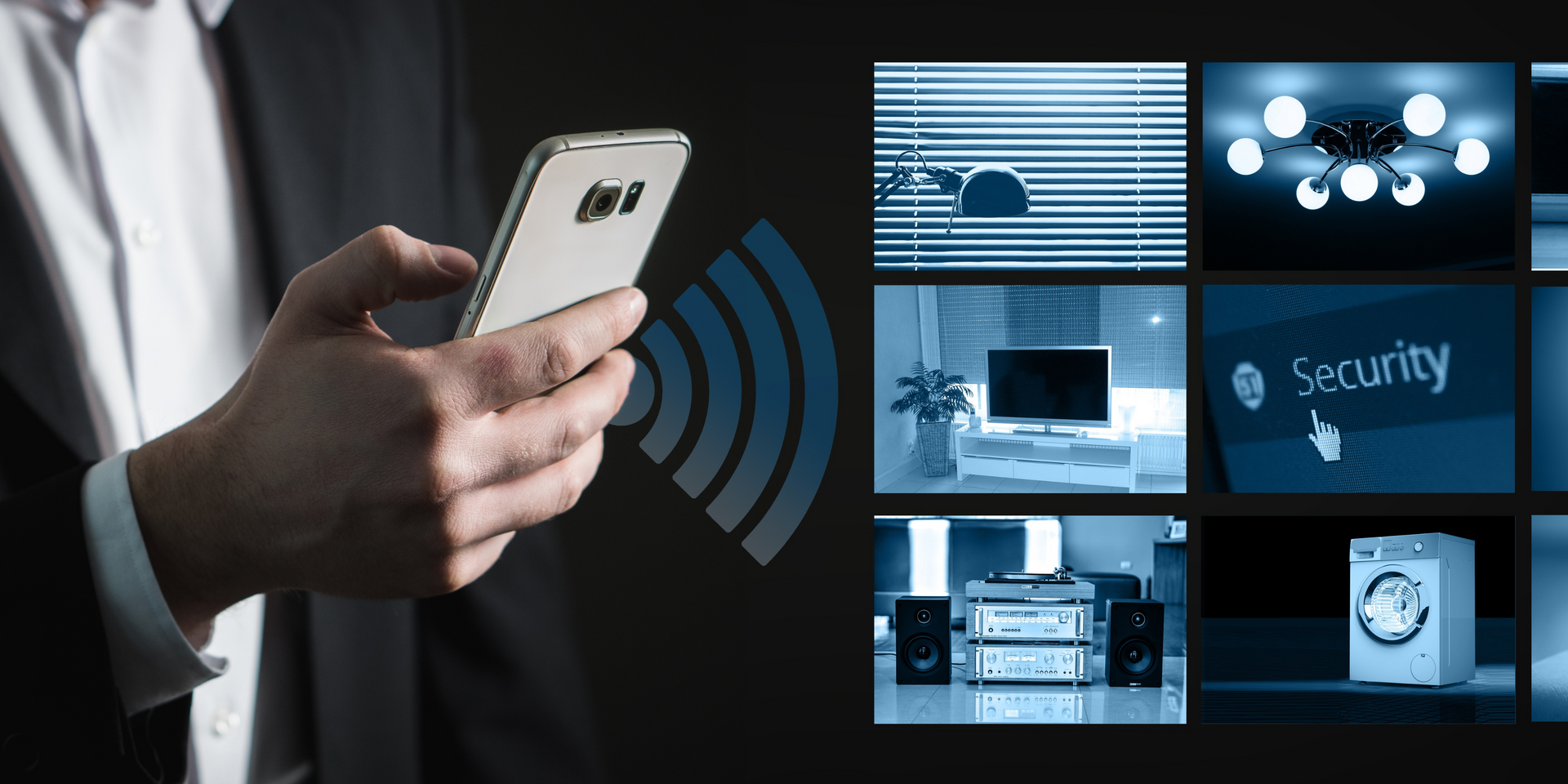
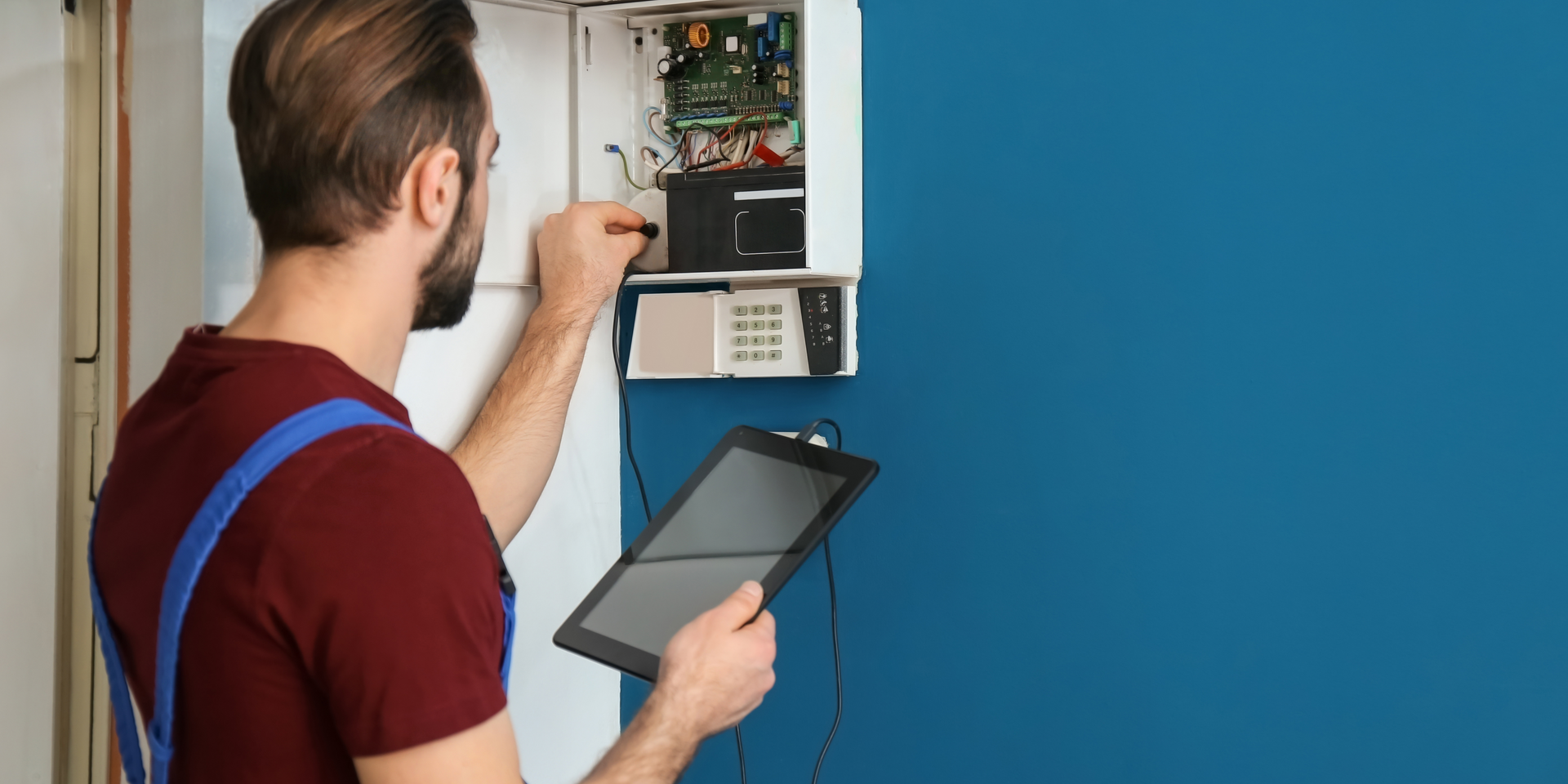