What Does MES Stand for in the Industry?
What Is The Difference Between MES and SAP?
Industrial MES (Manufacturing Execution Systems) and SAP (Systems, Applications, and Products in Data Processing) serve distinct yet complementary roles in manufacturing and business operations. MES focuses on real-time monitoring, control, and optimization of production processes on the shop floor, providing detailed insights into manufacturing activities. On the other hand, SAP is a comprehensive enterprise resource planning (ERP) system that manages broader business processes, such as finance, human resources, and supply chain management. While MES handles the intricate details of production, SAP integrates this data into the overall business framework, enabling strategic decision-making and resource planning across the enterprise.
SAP MES
SAP MES combines SAP's enterprise resource planning (ERP) capabilities with manufacturing execution system (MES) functionalities. It helps manage and monitor production processes in real-time, ensuring a smooth flow of information between the shop floor and business operations. By integrating SAP with MES, companies can optimize production, reduce downtime, and improve overall efficiency. SAP offers solutions like SAP Manufacturing Integration and Intelligence (SAP MII) to bridge the gap between planning and execution, providing a comprehensive approach to manufacturing management.
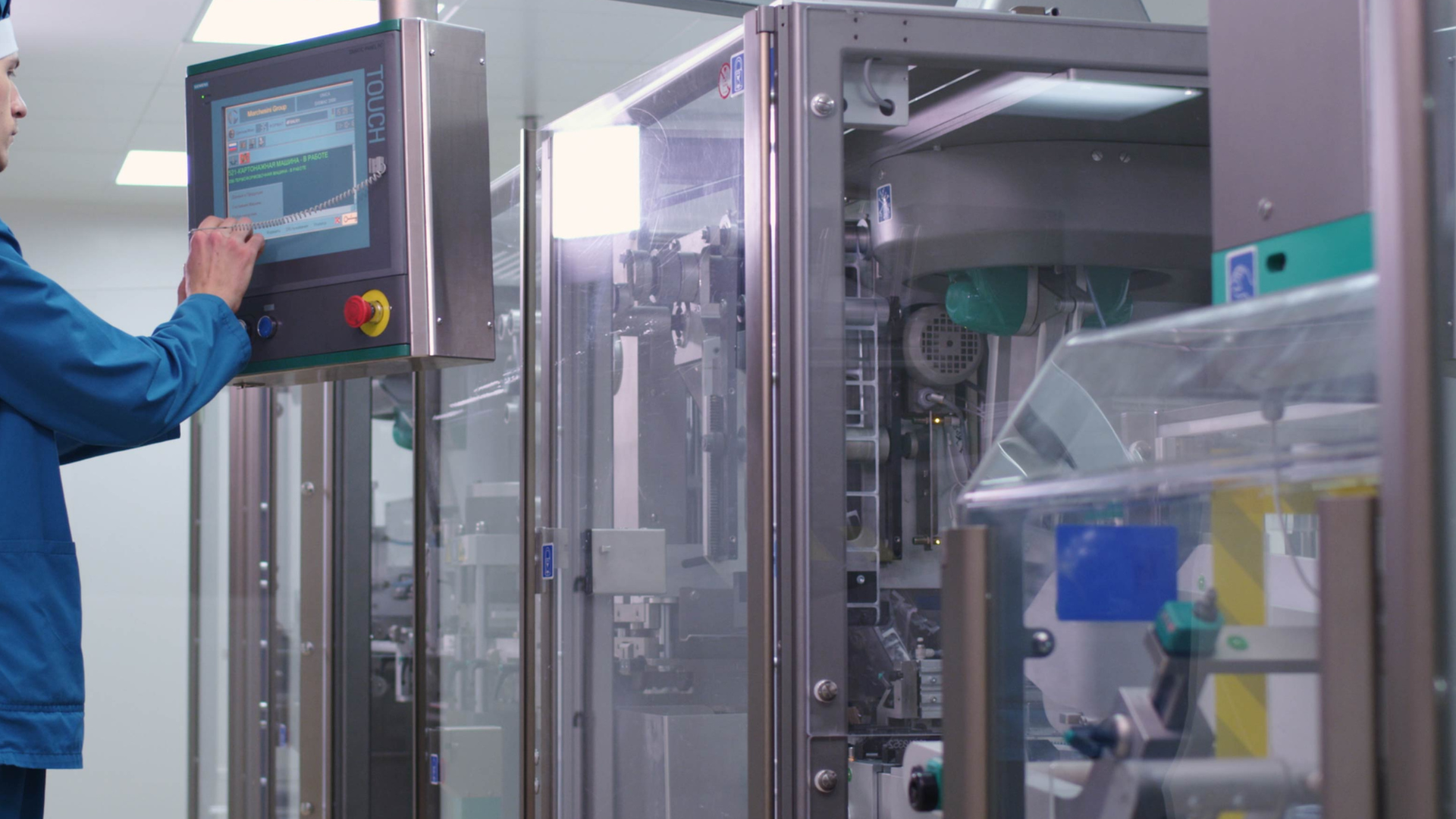
What Is The Difference Between MES and ERP?
MES Software
MES software, or Manufacturing Execution System software, is a powerful tool designed to optimize and manage production processes on the factory floor. It provides real-time data, enabling manufacturers to monitor, control, and streamline operations, ensuring that production runs smoothly and efficiently. By integrating with other enterprise systems, MES software bridges the gap between the shop floor and higher-level business management, offering detailed insights into production performance, improving quality control, and reducing downtime. This ultimately leads to increased productivity and a more agile manufacturing environment.
ERP System
An ERP system, or Enterprise Resource Planning system, is an integrated software solution that helps organizations manage and automate various business processes across departments. It centralizes data from areas like finance, human resources, supply chain, and customer relationship management, providing a unified view of operations. By streamlining these processes, an ERP system enhances efficiency, reduces operational costs, and supports informed decision-making. This comprehensive approach enables businesses to optimize resource use, improve collaboration, and maintain a competitive edge in the market.
What Is The Role of MES?
The role of a Manufacturing Execution System (MES) is to oversee and manage production operations on the factory floor. It serves as the critical link between the physical manufacturing process and the overarching business systems, providing real-time data and control over various production activities. An MES tracks the flow of raw materials, work-in-progress, and finished goods, ensuring that manufacturing processes are executed efficiently and according to plan. It helps in optimizing production schedules, maintaining product quality, reducing downtime, and enabling traceability and compliance with industry standards. By integrating with other enterprise systems like ERP, an MES ensures that production aligns with broader business goals, driving overall operational efficiency and effectiveness.
What Is The Difference Between MES and PLC?
MES (Manufacturing Execution System) and PLC (Programmable Logic Controller) serve different roles in manufacturing. A PLC controls specific machinery and automates tasks on the production line, executing pre-programmed instructions. In contrast, MES manages and optimizes the entire production process, using data from PLCs and other sources to monitor workflow, track materials, and ensure product quality. While PLCs handle machine-level control, MES oversees the broader manufacturing operation, aligning it with business goals.
How Much Do MES Engineers Make?
The salary of MES (Manufacturing Execution System) engineers varies based on experience, location, and industry. On average, MES engineers in the United States can expect to earn between $70,000 and $110,000 per year. Entry-level positions may start on the lower end of this range, while experienced engineers with specialized skills or those working in high-demand industries can earn salaries at the higher end or even exceed it. Additionally, factors like certifications, advanced degrees, and specific expertise in certain MES platforms can further influence an MES engineer's earning potential.
MES Engineer Salary
MES engineers typically earn competitive salaries, with pay varying based on experience, location, and industry. Experienced professionals, especially those with specialized skills, often command higher salaries, reflecting their critical role in optimizing manufacturing processes.
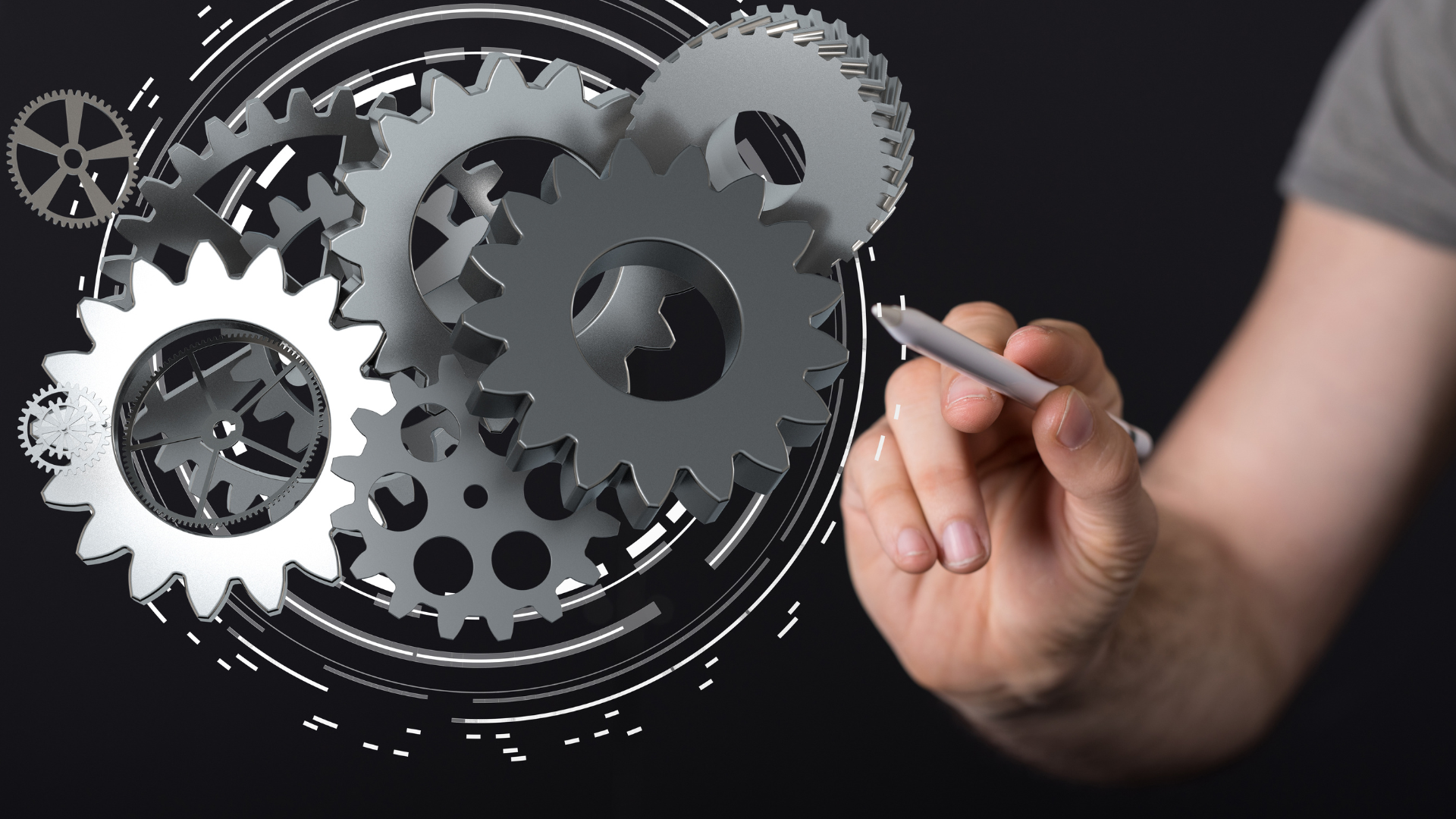
What Is The Difference Between SAP MII and ME?
SAP MII (Manufacturing Integration and Intelligence) and SAP ME (Manufacturing Execution) are both tools within SAP's manufacturing suite but serve different purposes. SAP MII focuses on integrating and visualizing data from various systems to provide real-time insights into manufacturing processes, helping to optimize performance and decision-making. SAP ME, on the other hand, is a Manufacturing Execution System that directly manages and controls production processes on the shop floor, ensuring that manufacturing operations are executed efficiently. While SAP MII provides data integration and analytics, SAP ME handles the execution and monitoring of production activities.
What Does MES Stand For In The Industry
In the industry, MES stands for Manufacturing Execution System. It is a software solution that manages, monitors, and optimizes production processes on the factory floor, ensuring efficient and accurate manufacturing operations.
Manufacturing Execution System
A Manufacturing Execution System (MES) is a software platform that manages and controls production processes in real time on the factory floor. It bridges the gap between business-level ERP systems and the operational control systems, providing visibility, tracking, and optimization of manufacturing activities. By coordinating everything from order management to production scheduling, quality control, and performance analysis, MES ensures that manufacturing operations are efficient, consistent, and aligned with business objectives.
What Does an MES Do?
An MES (Manufacturing Execution System) monitors, controls, and optimizes production processes in real-time on the factory floor. It tracks the flow of materials, manages production schedules, ensures product quality, and provides visibility into the entire manufacturing process. By integrating with other systems like ERP, an MES ensures that manufacturing operations are efficient, consistent, and aligned with business goals.
MES Meaning
An MES (Manufacturing Execution System) monitors, controls, and optimizes production processes in real-time on the factory floor. It tracks the flow of materials, manages production schedules, ensures product quality, and provides visibility into the entire manufacturing process. By integrating with other systems like ERP, an MES ensures that manufacturing operations are efficient, consistent, and aligned with business goals.
How Is ERP Different From MIS?
ERP (Enterprise Resource Planning) automates and integrates core business processes across departments, while MIS (Management Information Systems) focuses on providing data and reports to support management decisions. ERP streamlines operations, whereas MIS aids in decision-making through information analysis.
What Do You Need To Be A MES Engineer?
To become an MES engineer, you typically need a background in engineering, computer science, or a related field. Key skills include knowledge of manufacturing processes, experience with MES software, and proficiency in programming and database management. Additionally, strong problem-solving abilities and experience with system integration are essential.
what is MES and PLC?
MES (Manufacturing Execution System) and PLC (Programmable Logic Controller) are both crucial in manufacturing, but they serve different roles. MES is software that manages and optimizes production processes across the factory floor, providing real-time data and control. PLC, on the other hand, is hardware that controls specific machinery and automation tasks on the production line. While PLCs handle machine-level control, MES coordinates the entire production process to ensure efficiency and quality.
You might also like
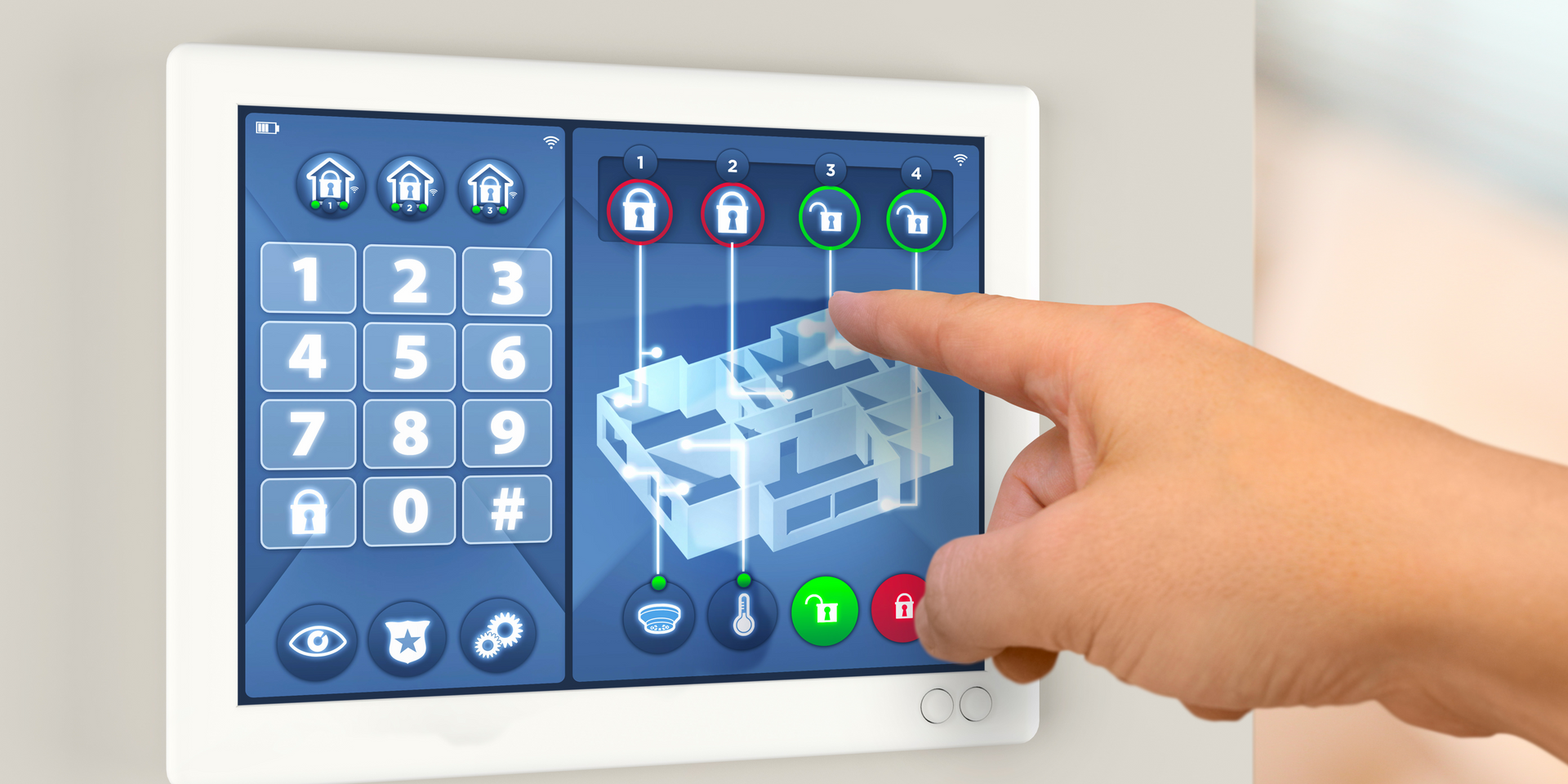
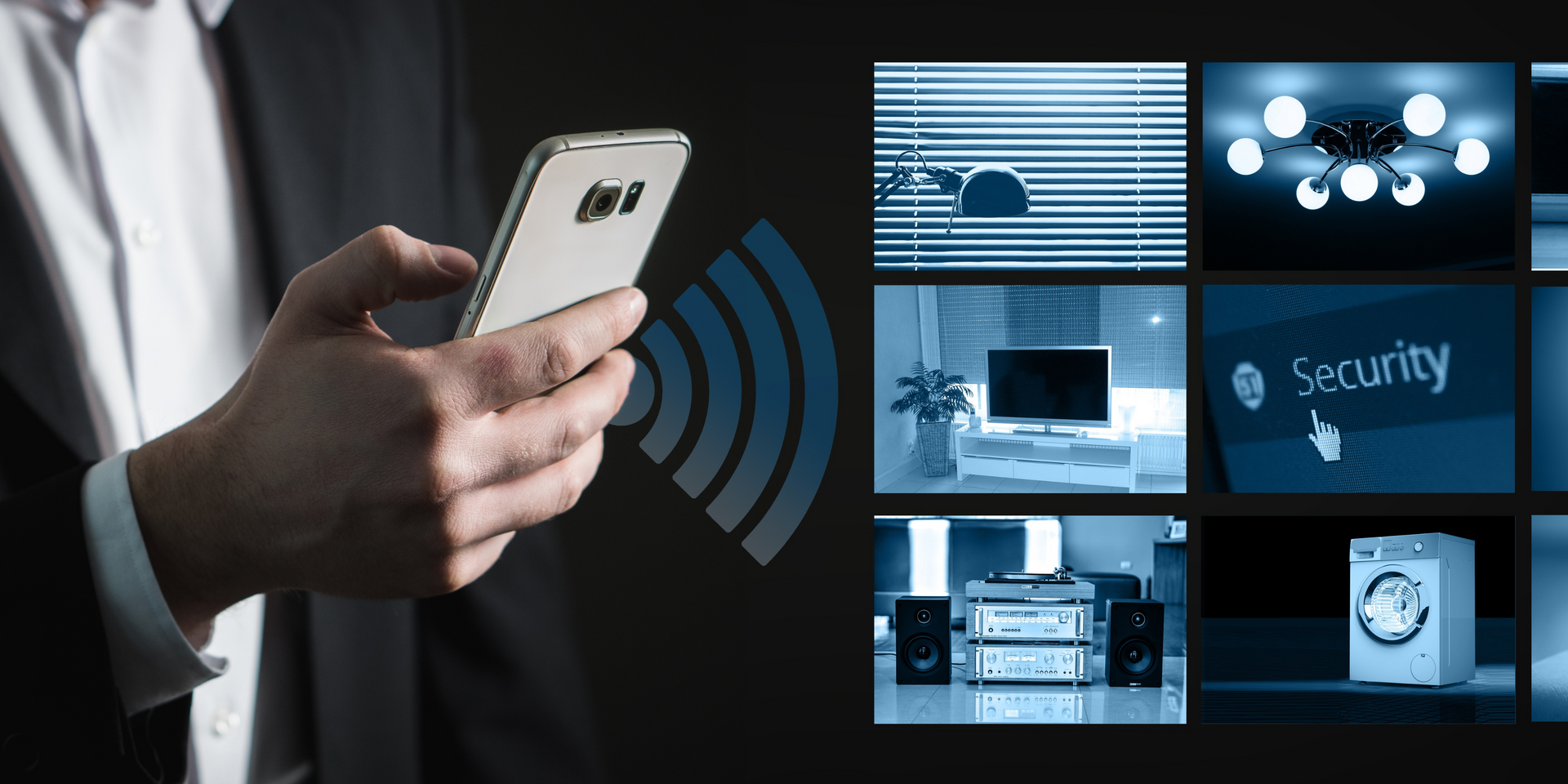
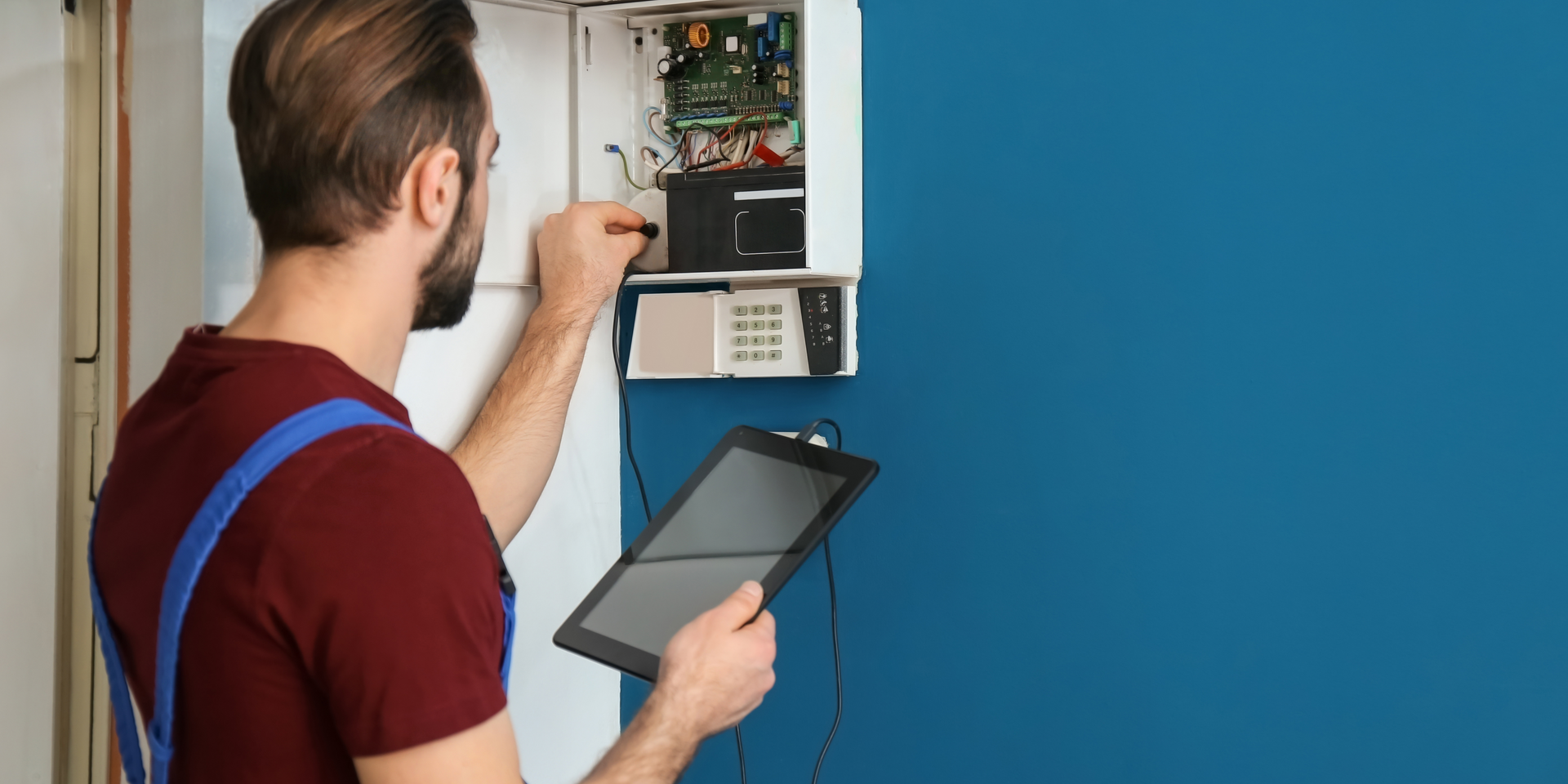