How IoT Reduces Downtime in Industry with Empowered Automation
One of the most frustrating things factoring, food processing, warehousing, etc. face is unplanned downtime. You never see an unexpected stop, whether it’s moving boxes, baking, or wind turbine manufacturing. Empowered automation IoT Reduces Downtime.
What is Industrial IoT?
We could be talking about the Internet of Things, but it has a different effect when it comes to industries that have a different way of working. Smart devices and sensors add up, including capturing information for the life of production. It also includes the identification of the facility that focuses on the risks of unplanned downtime.
Different problems add to the production problems that manufacturing companies must avoid. The solutions Internet of things can help in the manufacturing process and at the same time reducing any problems.
Risk-Audit Undertakes
One of the fastest and most effective ways to achieve minimal downtime is with risk auditing. It is an ideal way to access the significant risks that may fall on-site for operations. This system requires advances with manufacturers that generally occur for old machines.
In addition to this, manufacturing is generally not supported at all, which makes it a bit unwieldy for businesses. The solutions for retailers understand that there are many times when the parts are not available and delivery took about weeks. In such a case, the availability of equipment and the support network can make a big difference in downtime. Apart from this, it also includes quality, security, and protection errors.
Predictive-Maintenance
Low-cost sensors are the main problem in the data-driven world. Companies rely on inexpensive sensors to ensure the factory floor lives up to prevention, detection, and reduction of downtime. The sensors are made in such a way that they allow e-commerce retail solutions to estimate temperature, vibration, light, and heat conditions that signal equipment failure or damage.
The data is then moved to the central point that notifies the manager of any future failures. However, in the event of failure, operations are processed in such a way that damaged equipment works for industries. This is the easiest way to work during downtime and be alerted beforehand to avoid major problems in the future. The best part is that it saves a lot of battery life and is cheap with a machine. In addition to this, there is only a small amount of initial investment to ensure that no problems occur.
Automation Equipment and Systems
The great thing about automation is that it tends to ensure that manufacturers can take advantage of it. It helps small or large-scale companies to take a step forward to work in the time that can occur with different suppliers. The IoT application development company has worked on the advancements of maintenance and operations that are handled by technicians.
This helps to ensure that a system’s software and hardware are easily maintained to the best of their abilities. It also includes the challenging part of spare parts that can be overwhelming in the overall system. This tends to cover up replacement, repairs, maintenance, scheduling, upgrades, and system integration. This provides services available to the industry to avoid any failure in implementation or even support.
Preventive-Maintenance Program IoT Reduces Downtime
The best way to work in downtime is to make sure manufacturing is not interrupted due to breakdowns. There is no doubt that at one point the equipment will lose its ability to work and therefore the life schedule must be maintained. This can be prevented with the help of maintenance which can help reduce downtime and failures. Helps improve system efficiency, productivity, and security.
Internet of Things solutions is included in the process to get things a little further east for businesses to tackle the system. This has a success rate of more than 80% and it is only 20% of the cases that can have problems. Run to failure can be gruesome for the system to work on the reactive approach.
Conclusion
Relative humidity and compatible temperature play a vital role when it comes to retail IT solutions. It can avoid errors and easily transmit the data with the smart sensors to focus the monitoring application. This can lead to unplanned downtime to get the best possible solution.
You might also like
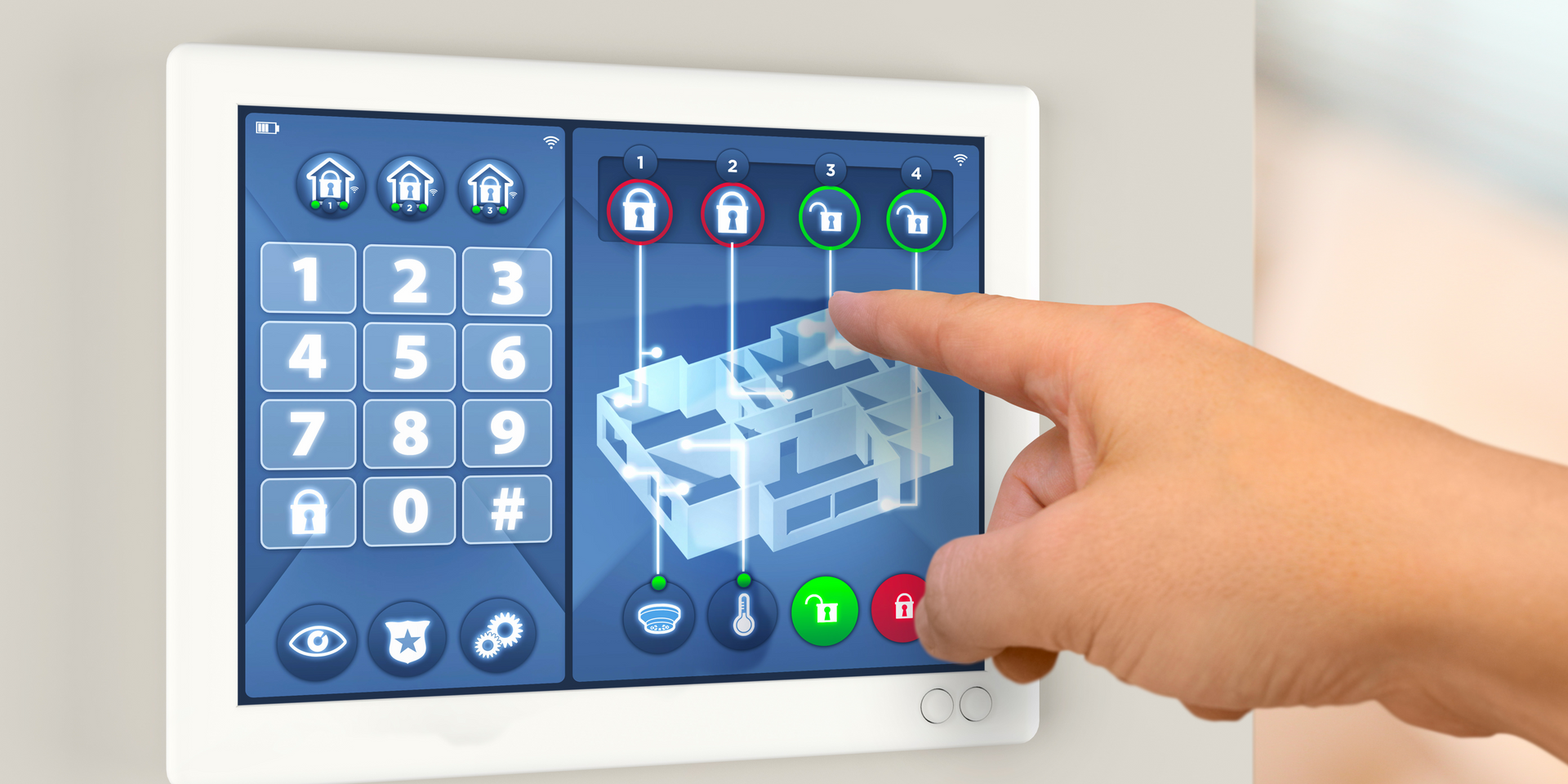
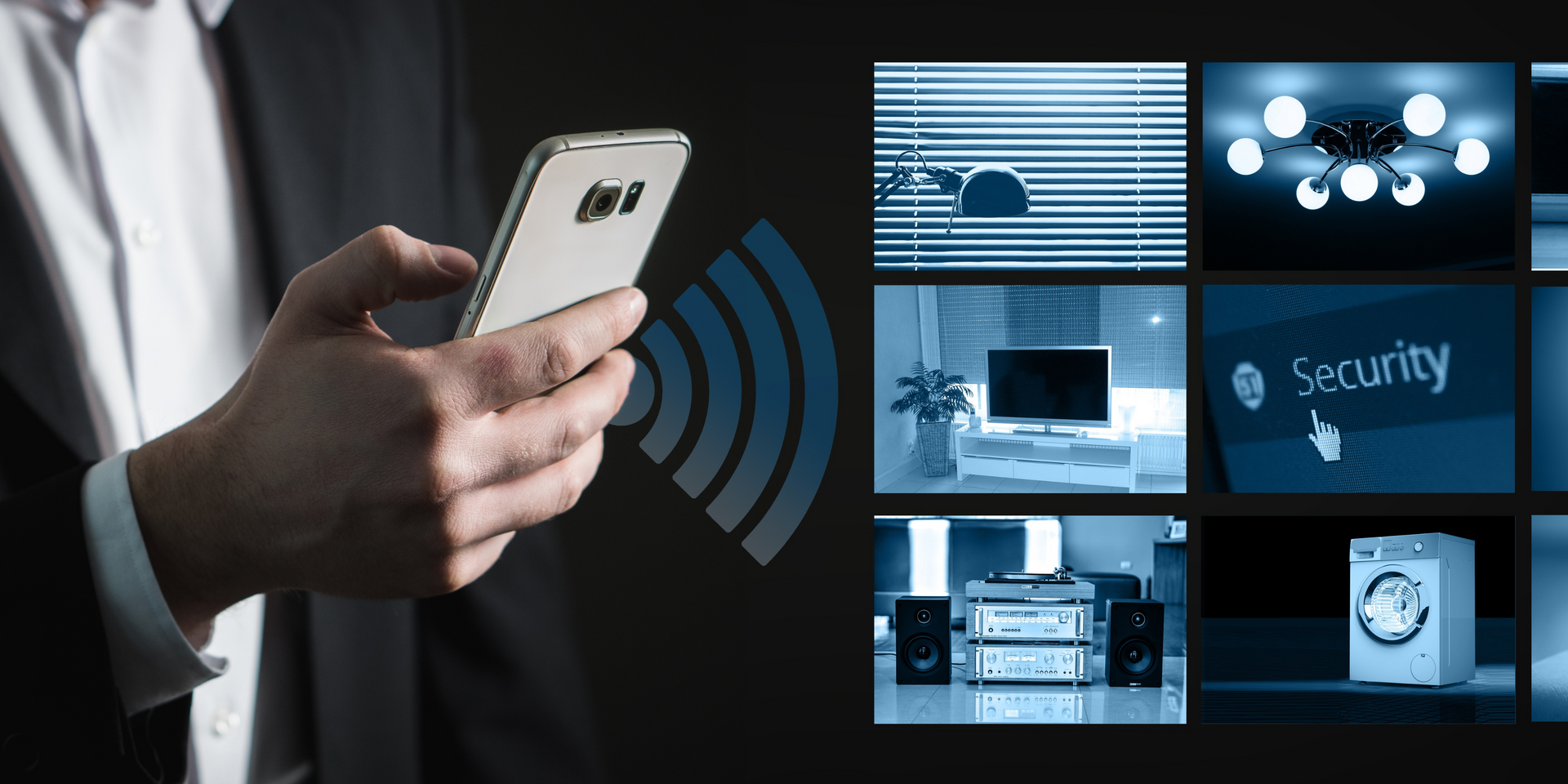
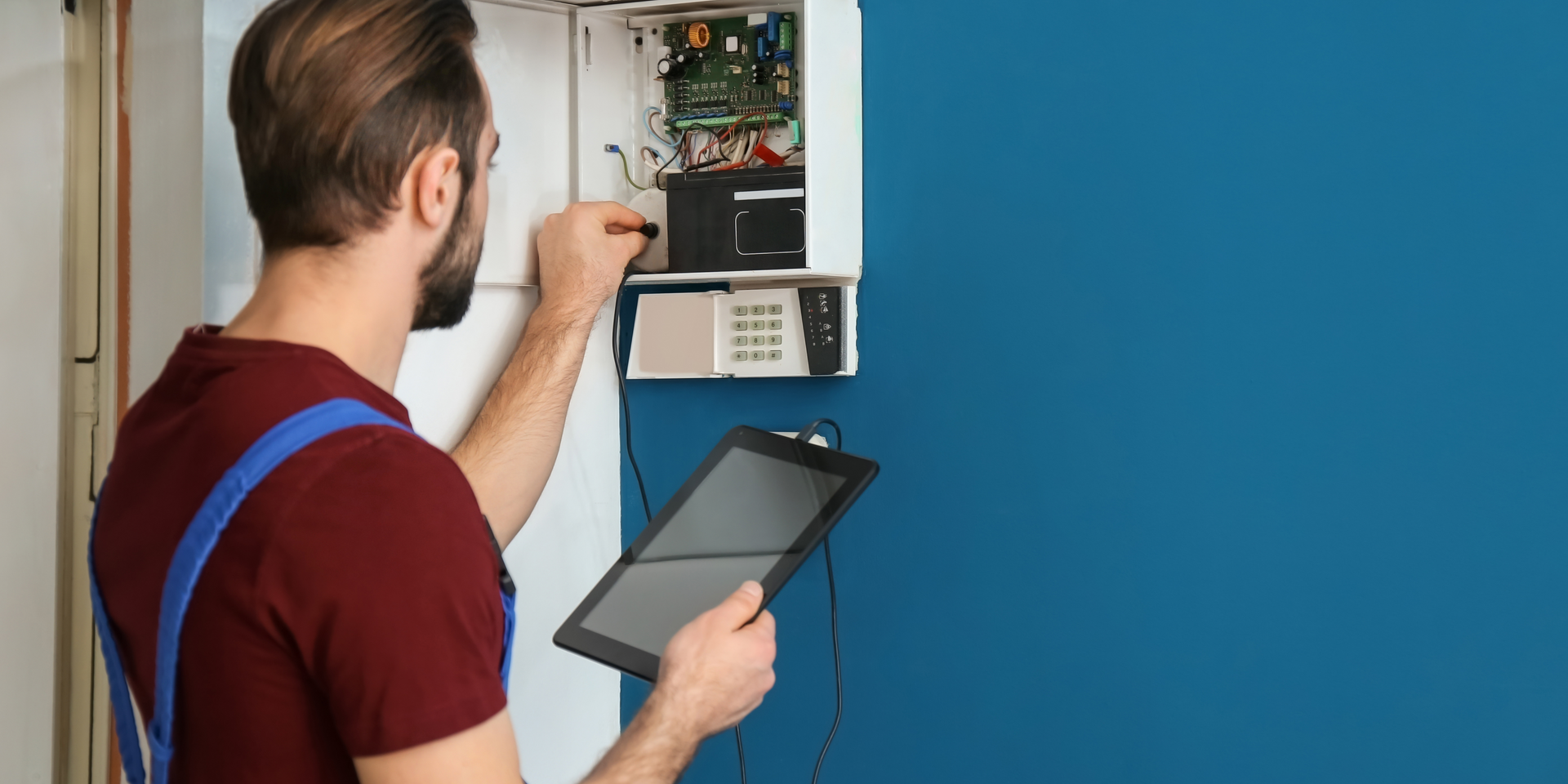