Manufacturing Execution System
What Is the Difference Between MES And ERP
MES vs. ERP
Manufacturing Execution Systems (MES) and Enterprise Resource Planning (ERP) systems are both critical to efficient operations but serve different purposes. MES systems focus on real-time monitoring and control of production processes, while ERP systems manage broader business functions such as finance, supply chain, and human resources. MES System examples illustrate how these systems excel in providing detailed insights into shop floor activities, which complements the high-level planning and resource management handled by ERP.
Manufacturing Execution System
Manufacturing Execution System (MES) plays a crucial role in optimizing production processes by providing real-time data and control over manufacturing operations. MES System examples include applications that track production performance, manage workflow, and ensure product quality on the shop floor. By integrating with other enterprise systems, an MES ensures seamless communication and coordination throughout the manufacturing process.
What Is the Difference Between MES and SAP
Manufacturing Execution System PDF
A Manufacturing Execution System (MES) PDF can provide detailed insights into how MES solutions streamline production processes and improve operational efficiency. These documents often include case studies, system features, and implementation guidelines that can be crucial for businesses considering MES integration. By reviewing an MES PDF, companies can better understand the potential impact on their production workflows.
Benefits of Manufacturing Execution System
Implementing a Manufacturing Execution System (MES) offers numerous benefits, including real-time monitoring, improved production efficiency, and enhanced product quality. An MES provides accurate data that helps in reducing waste, optimizing resources, and ensuring compliance with industry standards. Additionally, it enables better decision-making by providing actionable insights into every stage of the manufacturing process.
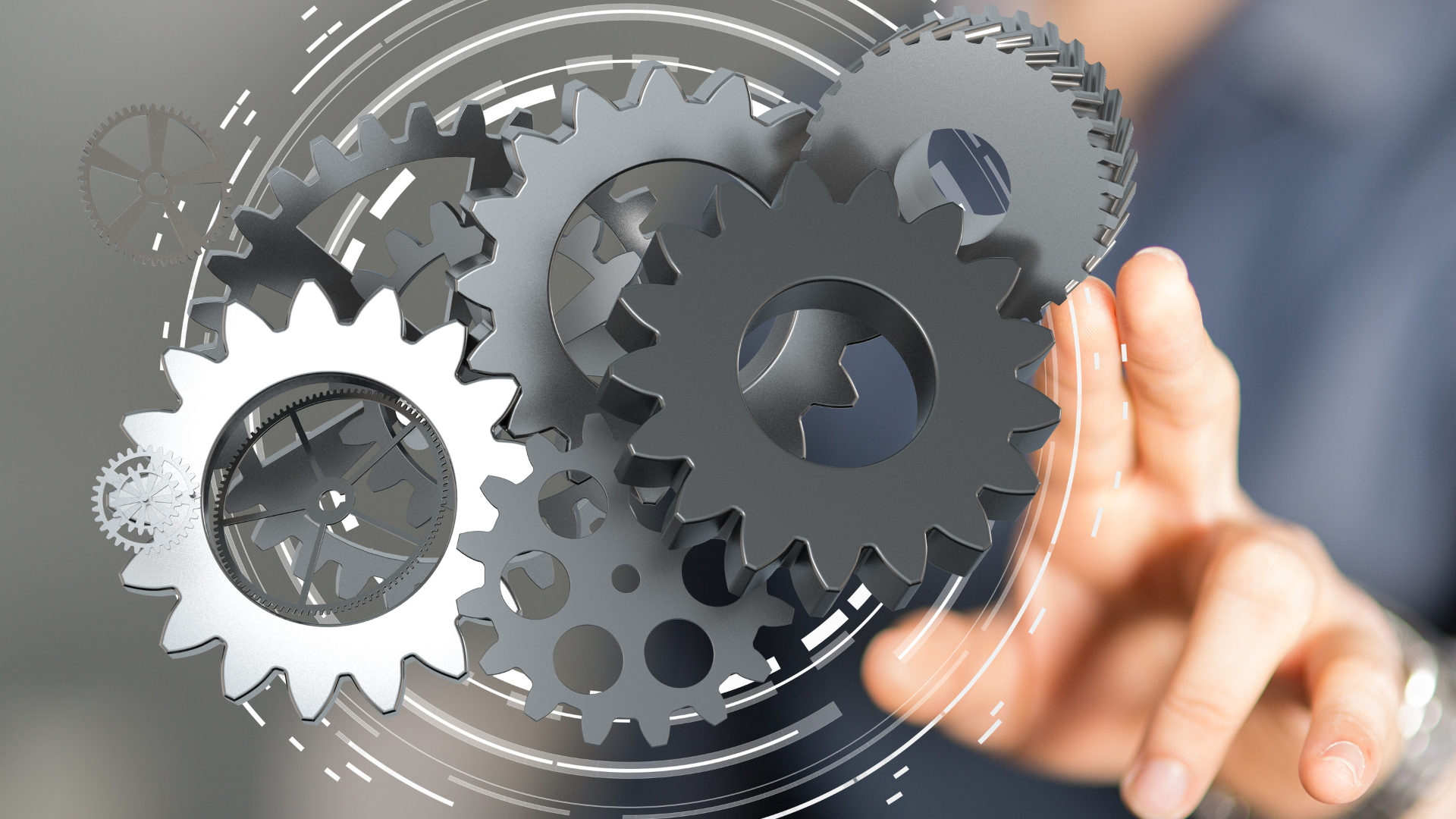
Is SAP an MES System
Leading MES Software Providers
Leading MES software providers include companies like Siemens, Rockwell Automation, and Honeywell, which offer comprehensive solutions for optimizing manufacturing processes. These providers deliver advanced features such as real-time data analytics, production tracking, and integration with other enterprise systems. By choosing a trusted MES provider, manufacturers can enhance efficiency, quality control, and overall operational performance.
Manufacturing Execution System Tools
Manufacturing Execution System (MES) tools are designed to streamline production processes, offering capabilities such as scheduling, workflow management, and quality control. These tools help manufacturers monitor operations in real-time, ensuring that every aspect of production is optimized for efficiency and accuracy. With the right MES tools, companies can reduce downtime, minimize waste, and achieve greater consistency in their manufacturing output.
What Is an Example of MES
Manufacturing Execution System Engineer
A Manufacturing Execution System (MES) Engineer specializes in designing, implementing, and maintaining MES solutions within a manufacturing environment. They play a crucial role in optimizing production processes by integrating MES with other enterprise systems, ensuring seamless data flow and real-time monitoring. MES Engineers are key to improving operational efficiency, product quality, and overall productivity on the shop floor.
Manufacturing Execution System Architecture
Manufacturing Execution System (MES) architecture refers to the structured framework that defines how MES components are organized and integrated within a manufacturing environment. This architecture typically includes modules for production scheduling, quality control, and data analytics, all working together to optimize the manufacturing process. A well-designed MES architecture ensures scalability, flexibility, and efficient communication between the shop floor and enterprise systems.
What is Common Manufacturing Execution System
Manufacturing Execution System Software List
A comprehensive list of Manufacturing Execution System (MES) software includes industry leaders like Siemens' SIMATIC IT, Rockwell Automation's FactoryTalk, and Honeywell's MES solutions. These software platforms offer a range of features such as real-time production tracking, quality management, and integration with other enterprise systems. Choosing the right MES software depends on a company's specific manufacturing needs, scalability requirements, and desired level of automation.
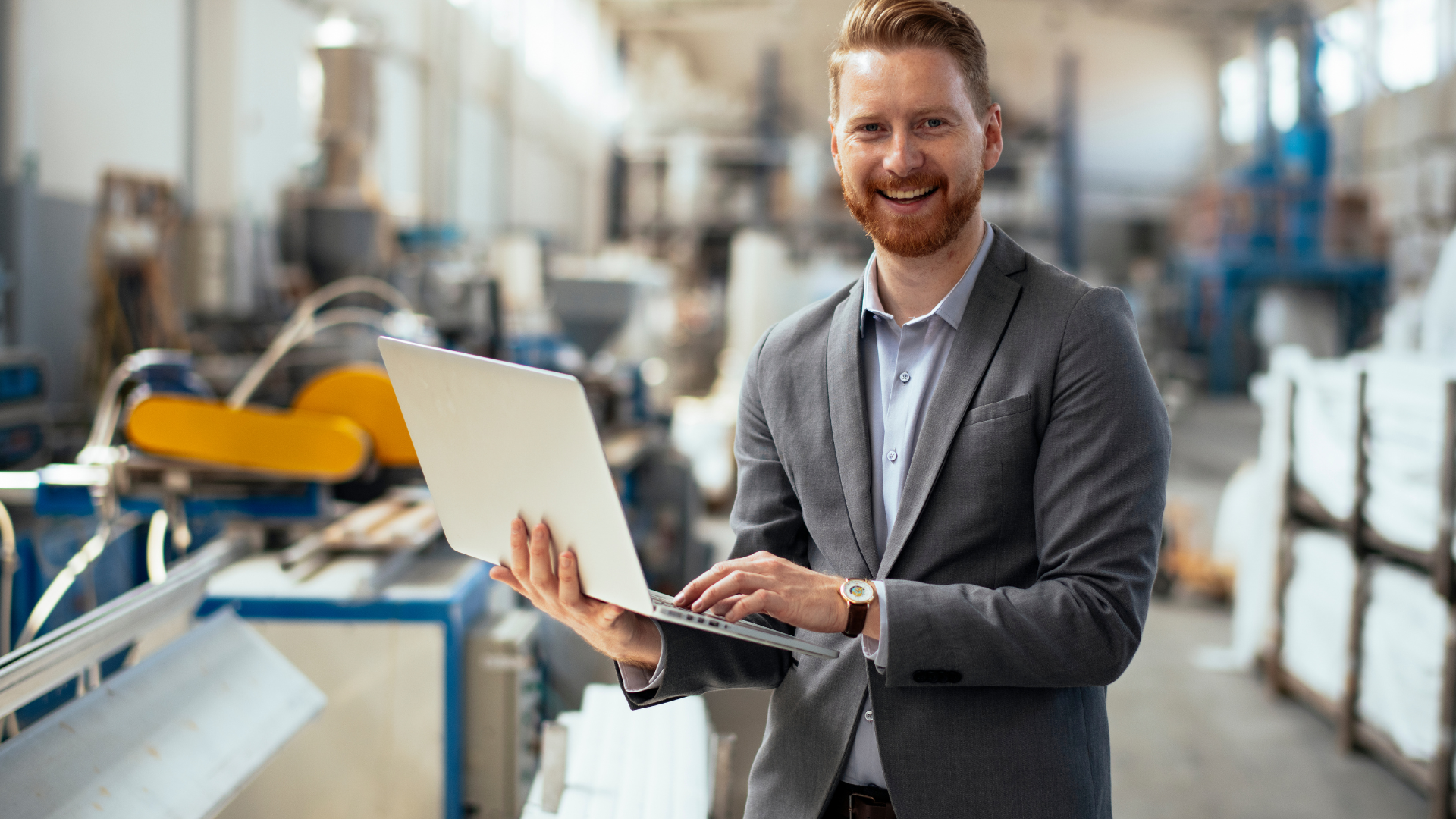
What Is the Difference Between MES and SCADA
Manufacturing Execution System Requirements
Implementing a Manufacturing Execution System (MES) requires a thorough understanding of the specific needs of the manufacturing process, including real-time data collection, process automation, and quality control. Key requirements often include robust integration capabilities with existing enterprise systems, user-friendly interfaces for operators, and scalability to accommodate future growth. Additionally, the MES must ensure secure data handling and compliance with industry standards to maintain operational efficiency and product quality.
You might also like
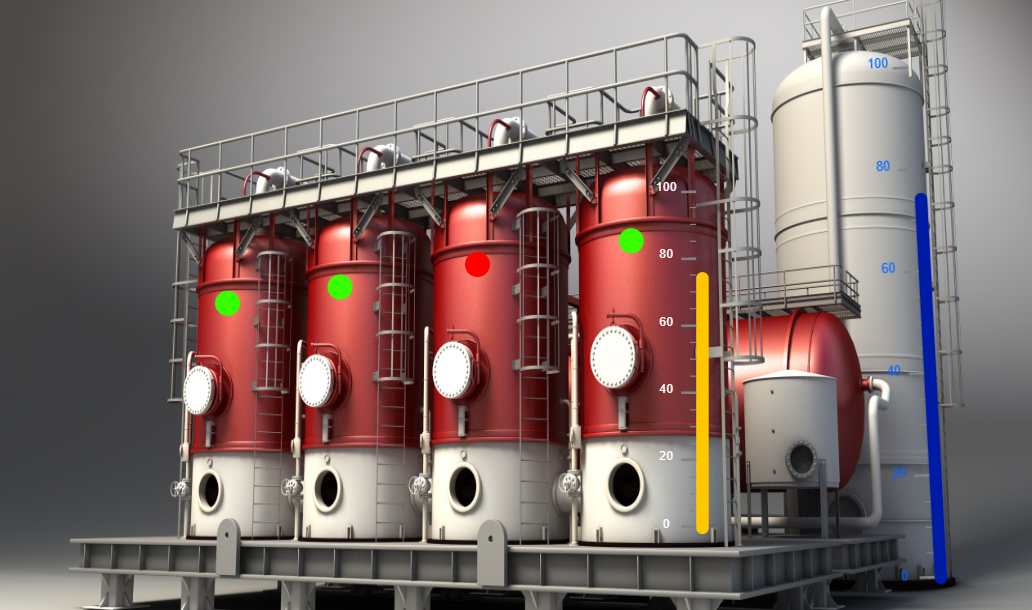
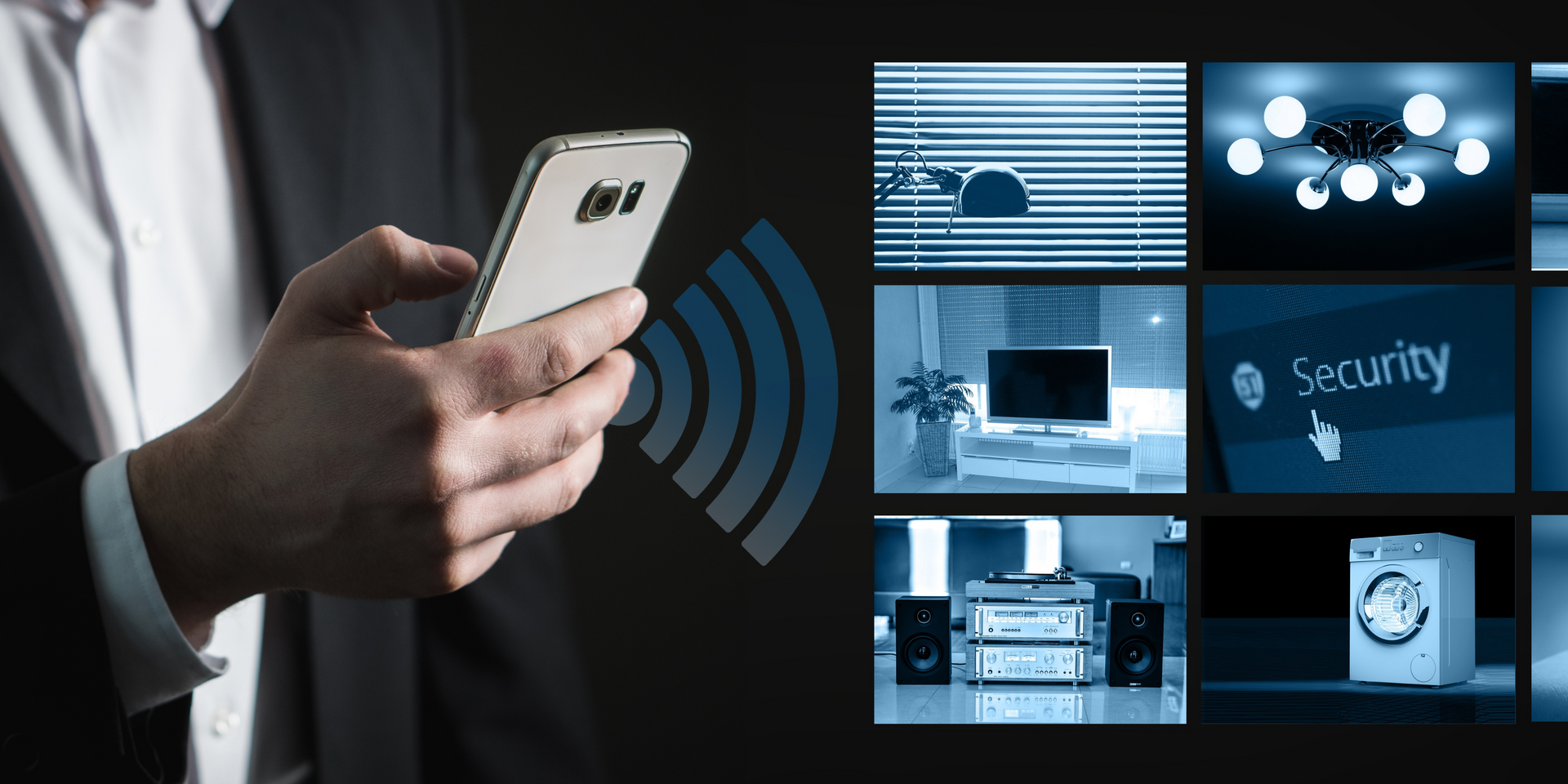
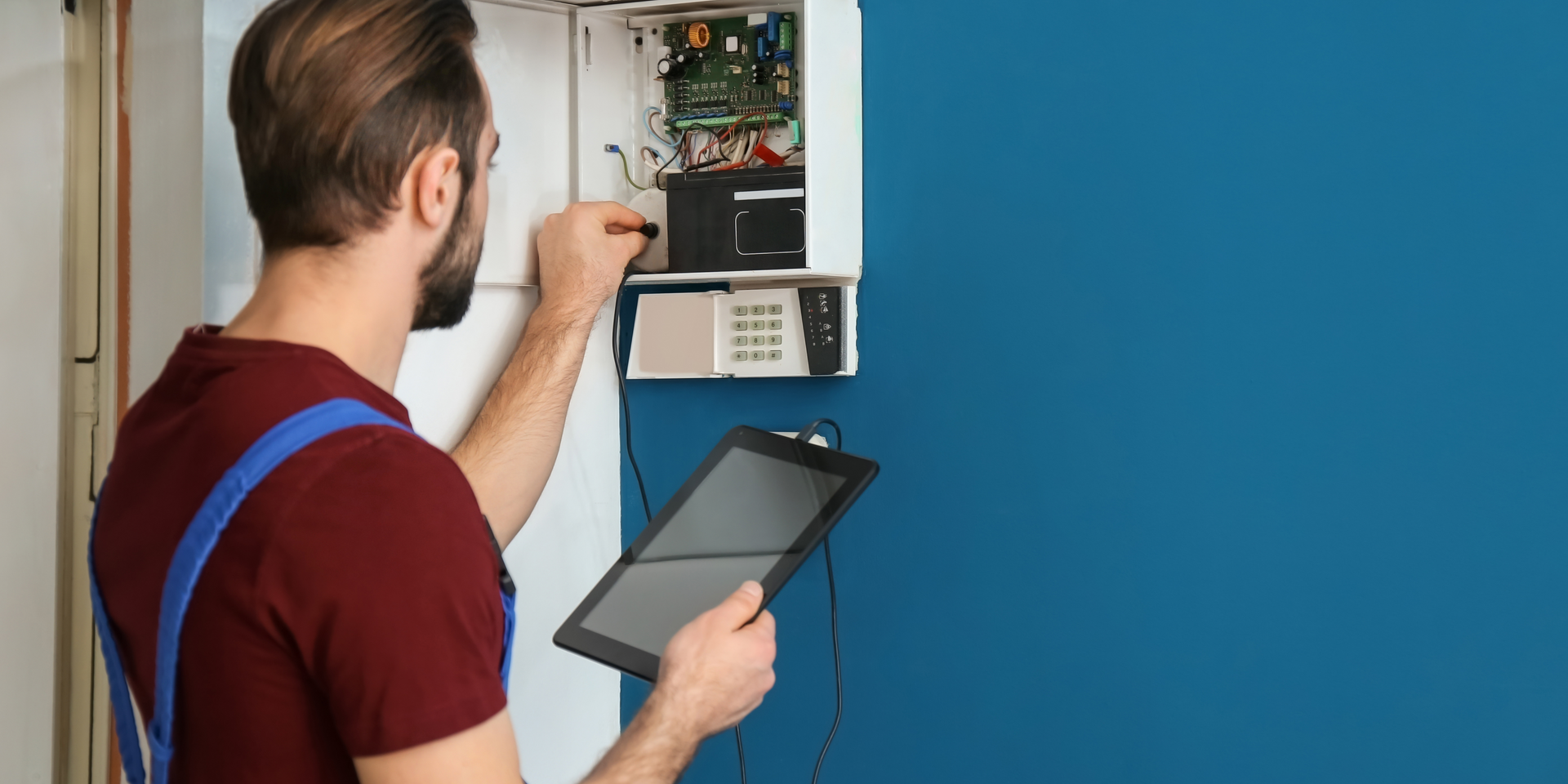