SCADA Full Form
What Is SCADA and How Does It Work
SCADA System PDF
A SCADA system PDF often provides detailed information about the architecture, functionality, and benefits of SCADA systems, including case studies and implementation guidelines. These documents can be essential for understanding how SCADA systems manage and control industrial processes remotely.
SCADA Full Form
The full form of SCADA is Supervisory Control and Data Acquisition. When evaluating system options, a common question is, "Which is better HMI or SCADA?" Understanding the full capabilities of SCADA systems can help determine their advantages over HMI (Human-Machine Interface) systems in complex industrial settings.
What Is the Difference Between PLC and SCADA
SCADA vs PLC
SCADA (Supervisory Control and Data Acquisition) systems and PLCs (Programmable Logic Controllers) serve different purposes in industrial automation. SCADA systems are designed for supervisory control and data acquisition over large-scale processes, providing real-time monitoring and control. In contrast, PLCs handle direct control and automation of specific machinery and processes, often serving as the operational backbone that SCADA systems oversee.
SCADA Programming
SCADA programming involves developing software that manages and supervises industrial processes from a central location. This includes creating control panels, configuring data acquisition, and integrating with PLCs to ensure seamless real-time monitoring and management. Effective SCADA programming enables operators to efficiently oversee and control complex systems.
PLC SCADA
PLC SCADA systems combine the direct control capabilities of PLCs with the supervisory and data acquisition features of SCADA systems. This integration allows for comprehensive management of industrial processes, with PLCs handling real-time automation tasks and SCADA systems providing a high-level overview and control interface. Together, they ensure both detailed control and broad oversight of industrial operations.
Difference Between PLC, SCADA, and DCS
PLCs (Programmable Logic Controllers) are used for real-time control of specific machinery and processes, focusing on direct automation tasks. SCADA (Supervisory Control and Data Acquisition) systems provide a high-level overview and monitoring capabilities, integrating data from various sources for comprehensive process management. DCS (Distributed Control Systems) offer a more integrated approach, managing complex processes with distributed control units that enable both local and centralized supervision.
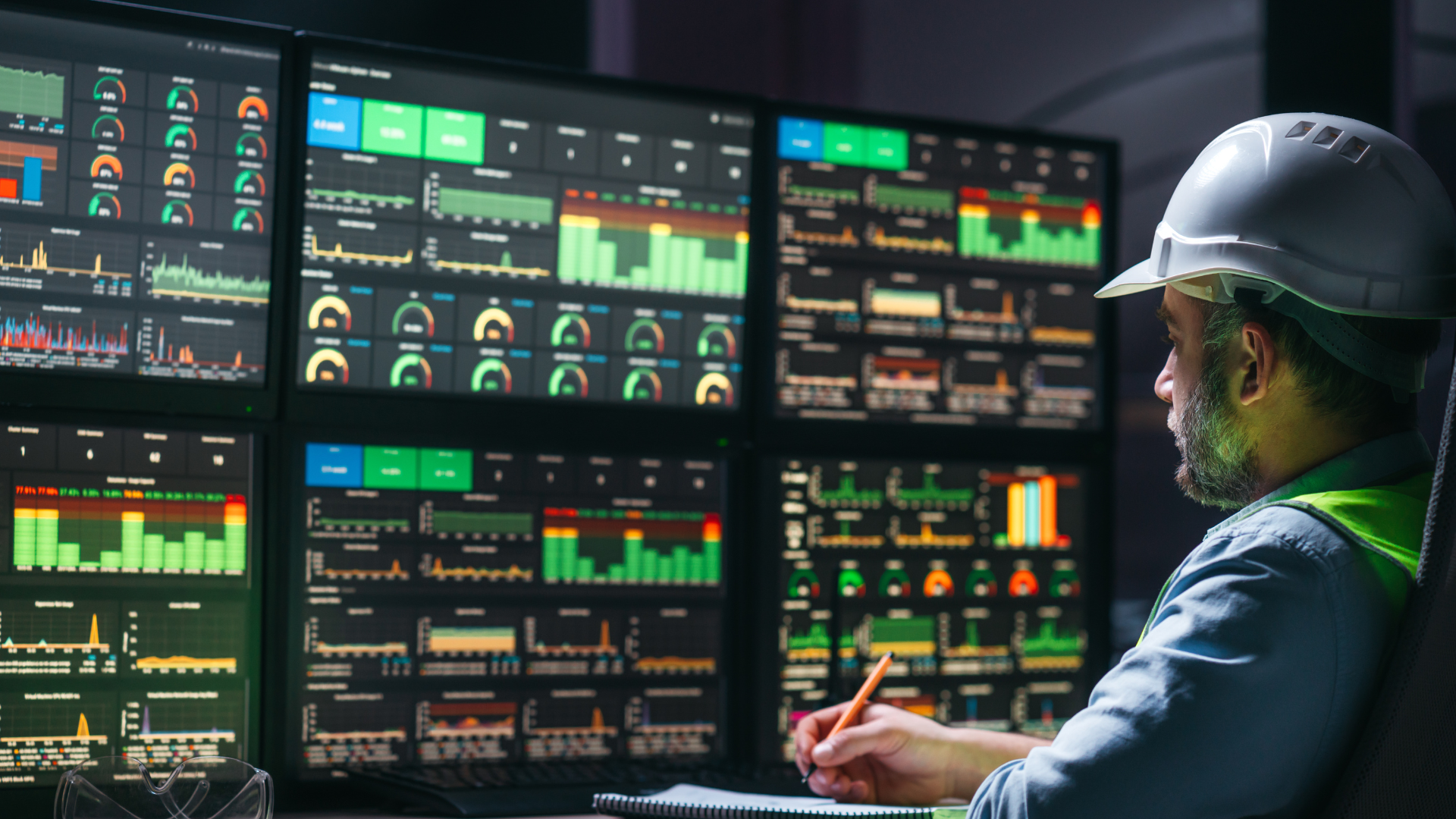
What Are the 3 Main Components of SCADA
SCADA Components
The three main components of SCADA (Supervisory Control and Data Acquisition) systems are the Human-Machine Interface (HMI), which provides a graphical interface for operators; the Remote Terminal Units (RTUs) or Programmable Logic Controllers (PLCs), which gather data and control processes; and the SCADA software, which processes data, generates reports, and facilitates communication between the HMI and field devices.
SCADA Meaning in Electrical
In electrical engineering, SCADA systems are used to monitor and control electrical grids and substations. They provide real-time data on electrical performance, help manage the distribution of power, and ensure the efficient operation of electrical infrastructure by integrating data from various sensors and control devices.
Introduction to SCADA
SCADA (Supervisory Control and Data Acquisition) systems are used for real-time monitoring and control of industrial processes. They enable operators to oversee operations from a central location, collect and analyze data from remote devices, and manage complex systems through a user-friendly interface. SCADA systems are essential for improving operational efficiency, ensuring system reliability, and enhancing decision-making.
What Is SCADA and How Does It Work
SCADA Architecture
SCADA architecture typically consists of several key layers: the field layer with sensors and control devices, the communication layer that transmits data between field devices and the central system, and the supervisory layer that includes the SCADA software for data visualization, analysis, and control. This architecture ensures that data flows seamlessly from the shop floor to the control center, enabling real-time monitoring and management.
SCADA Software
SCADA software provides a centralized platform for monitoring and controlling industrial processes. It includes features such as data acquisition, real-time visualization, alarm management, and historical data analysis, allowing operators to oversee operations efficiently and respond to issues promptly. SCADA software integrates with hardware components like PLCs and RTUs to facilitate comprehensive process management.
What Is SCADA Example
SCADA Architecture PDF
A SCADA architecture PDF provides a detailed overview of the structural components and design principles of SCADA systems. It typically includes diagrams and descriptions of the various layers, such as field devices, communication networks, and supervisory software, helping users understand how these elements interact to support real-time monitoring and control.
SCADA Applications
SCADA applications are used across various industries to manage and control complex processes such as manufacturing, energy distribution, and water treatment. These applications offer real-time data visualization, control capabilities, and analytical tools that enable operators to optimize performance, improve efficiency, and respond to system changes or issues quickly.
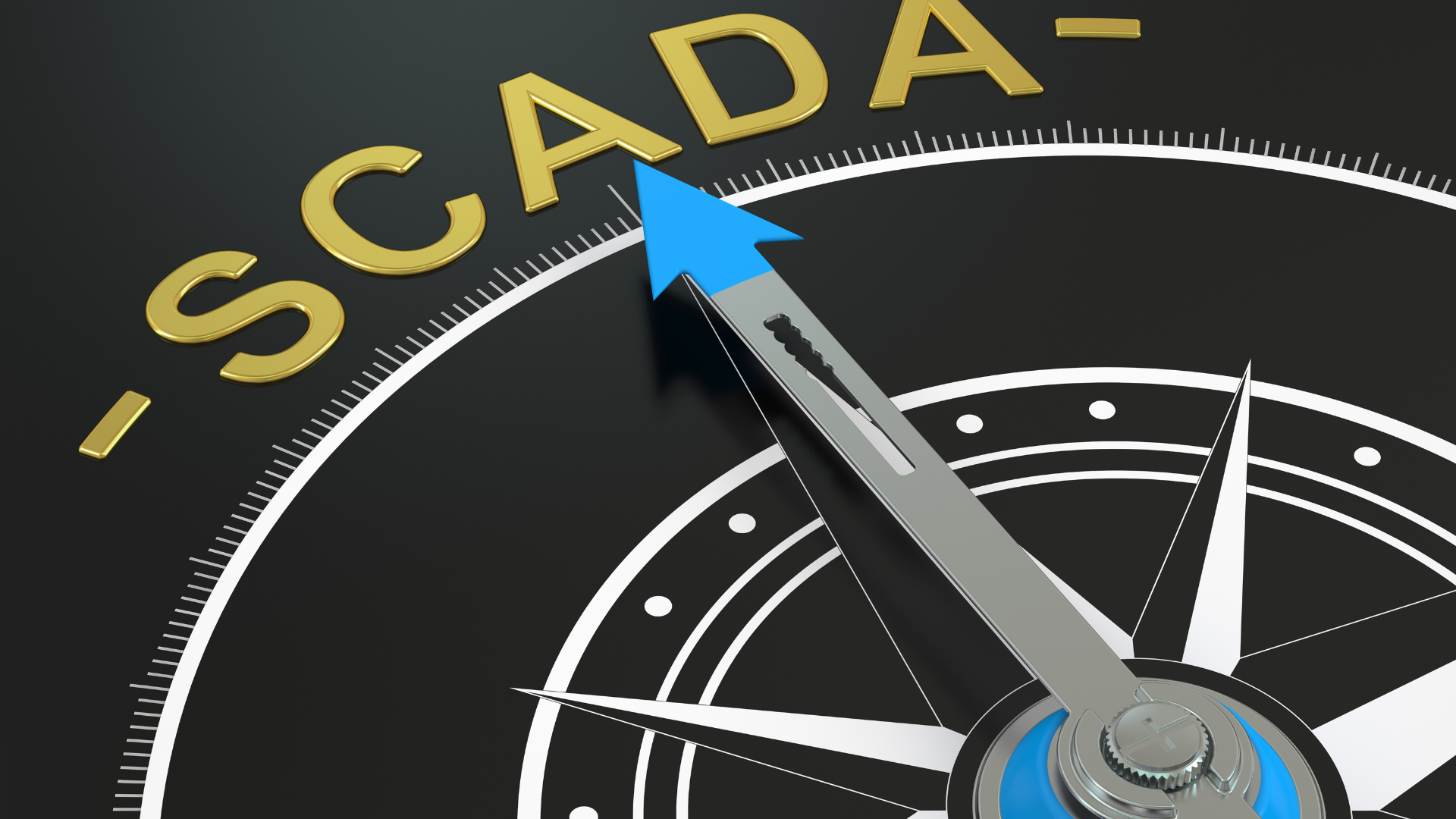
What Is SCADA and How It Works
PLC SCADA Jobs
PLC SCADA jobs involve working with both Programmable Logic Controllers (PLCs) and SCADA systems to manage and automate industrial processes. These roles typically require expertise in configuring, programming, and troubleshooting PLCs and integrating them with SCADA systems for real-time monitoring and control. Professionals in this field ensure that systems operate efficiently, troubleshoot issues, and optimize performance across various manufacturing and industrial environments.
SCADA HMI
SCADA HMI (Human-Machine Interface) is a crucial component of SCADA systems that provides a graphical interface for operators to interact with and control industrial processes. The HMI displays real-time data, system status, and alarm notifications, allowing users to monitor operations, make adjustments, and respond to issues effectively. A well-designed SCADA HMI enhances usability and operational efficiency by presenting complex data in an accessible and intuitive format.
You might also like
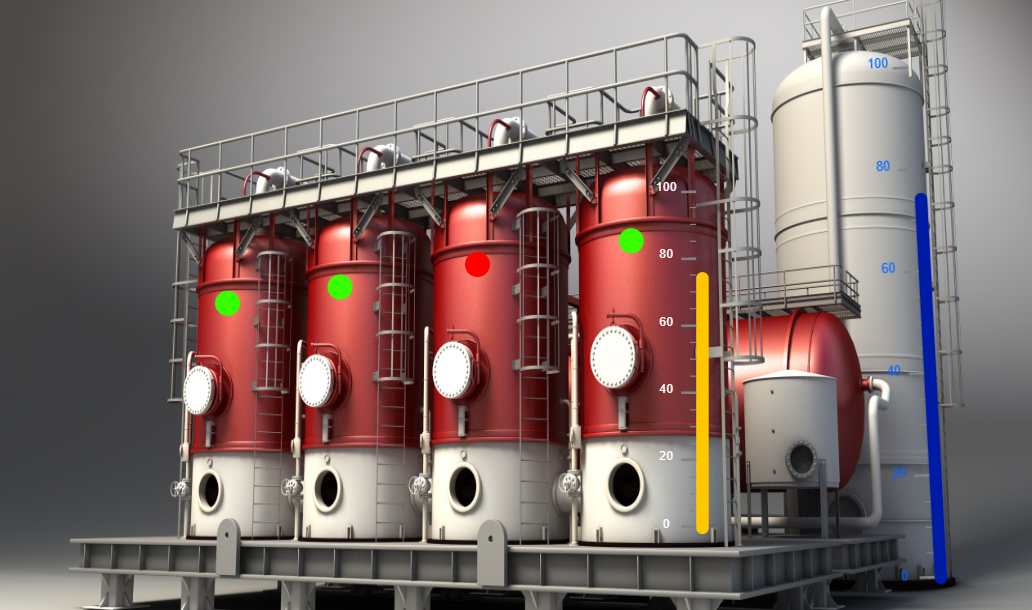
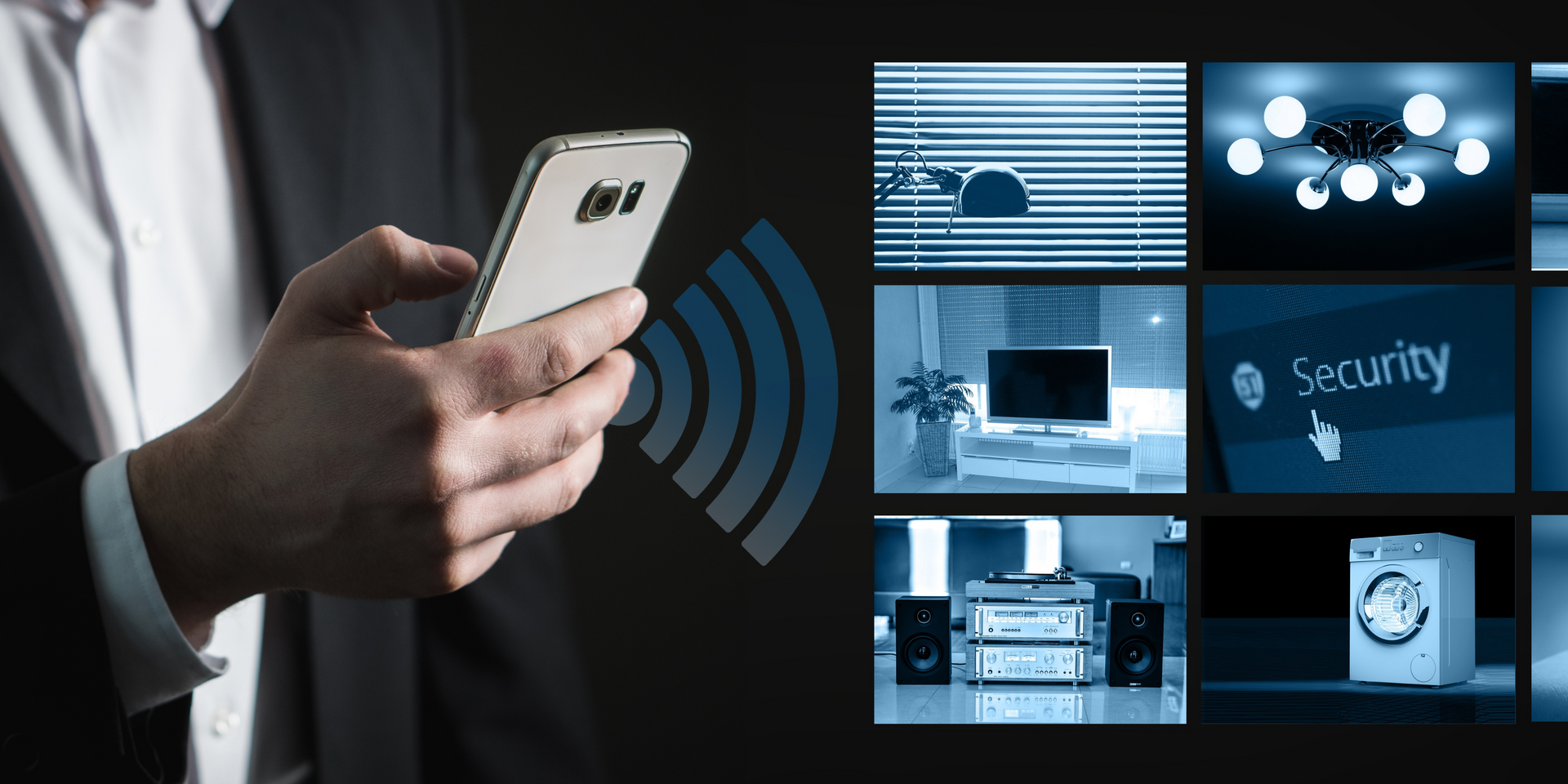
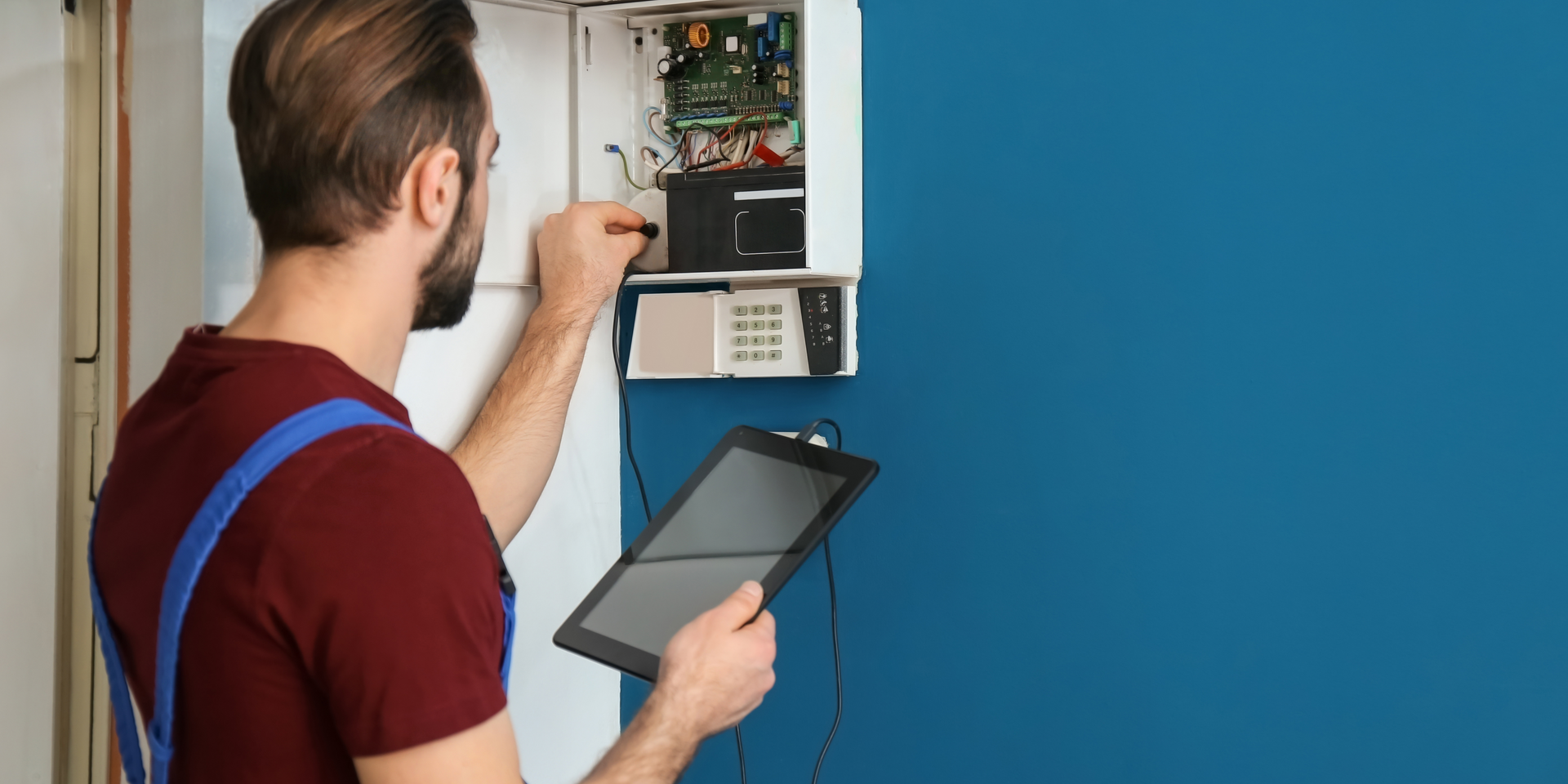