MES Integration
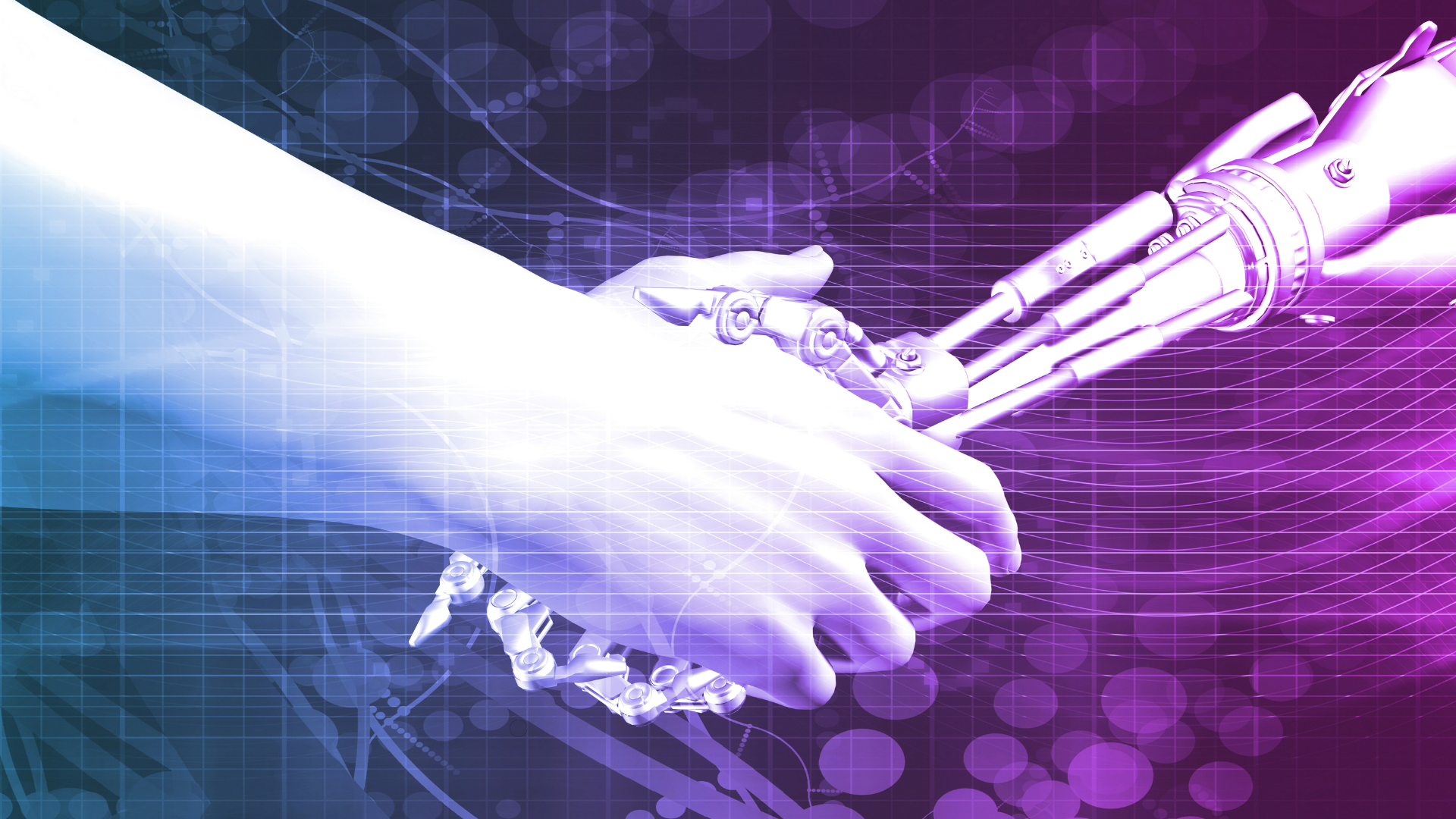
What does MES stand for?
MES stands for Manufacturing Execution System, a vital technology framework used extensively in the manufacturing sector to control and manage the production process at a granular level. This system serves as an operational nerve center, orchestrating the flow of information and coordinating production activities from the top floor to the shop floor. The essence of an MES lies in its ability to transform raw data from the production line into actionable insights, facilitating a seamless transition from planned production activities to actual execution.
The primary goal of an MES is to improve manufacturing efficiencies by providing real-time monitoring and control of all aspects of production. It meticulously captures every detail of the manufacturing process, from the initiation of an order to the final steps of production, ensuring that each component is produced at the right cost, quality, and schedule. The system's ability to monitor real-time data about plant activities makes it a critical tool for managers who need to make quick decisions based on accurate information.
An MES can significantly reduce the production cycle time by effectively eliminating unnecessary downtime and minimizing transitions between production phases. It provides manufacturers with the agility to respond to changes in demand or production conditions almost instantaneously, enhancing their ability to compete in dynamic markets. By integrating data from various sources, such as inventory levels, workforce allocation, and machinery efficiency, an MES allows for a holistic view of the production landscape, enabling optimized resource management and reduced waste.
Moreover, MES supports quality assurance processes by tracking compliance with industry standards and specifications throughout the production cycle. This ensures that every product meets strict quality guidelines, thereby reducing the risk of defects and subsequent rework or recalls. This tracking capability is especially crucial in highly regulated industries, such as pharmaceuticals, food and beverage, and automotive, where adherence to safety and quality standards is paramount.
In today’s digital era, an MES often incorporates advanced technologies such as IoT (Internet of Things), AI (Artificial Intelligence), and predictive analytics to enhance its capabilities. These technologies enable predictive maintenance, which anticipates equipment failures before they occur, and adaptive control, which adjusts production parameters in real-time for optimal performance. The integration of these technologies into an MES framework not only boosts productivity but also propels the manufacturing process into the future, aligning with the goals of Industry 4.0.
In essence, an MES is not just about executing manufacturing orders; it’s about doing so in the most efficient, productive, and cost-effective manner possible. It provides a clear and concise view of all manufacturing activities and offers tools to perform detailed analysis, which helps in continuous improvement and operational excellence. As manufacturers continue to navigate the complexities of modern production environments, the role of an MES in achieving streamlined operations and sustaining competitive advantage becomes ever more critical. In sum, MES stands for more than just a system; it is a comprehensive approach to achieving peak operational performance and strategic execution on the manufacturing floor.
What are MES Interfaces?
MES interfaces, short for Manufacturing Execution System interfaces, are fundamental components in modern manufacturing processes that act as bridges connecting the MES with a variety of other technological systems within a manufacturing environment. These interfaces allow for a two-way flow of data and commands between the MES, the operational hardware on the shop floor, and the software systems that manage broader business processes. This connection is vital for streamlining production operations and achieving higher efficiency and productivity.
An MES's primary function is to manage and monitor the complex manufacturing processes, from raw material input to finished product output. However, for an MES to function optimally, it needs to integrate seamlessly with other systems. This is where MES interfaces come into play. They guarantee the accurate and real-time sharing of data, including production schedules, material usage, machine status, quality control, and product output, with other systems like ERP (Enterprise Resource Planning), SCM (Supply Chain Management), and CRM (Customer Relationship Management) software.
One of the primary advantages of MES interfaces is their ability to facilitate real-time data acquisition and dissemination. This real-time capability allows manufacturing managers to make informed decisions quickly, adapting to changes in production demands or addressing potential issues before they escalate into more significant problems. For example, if a piece of equipment begins to show signs of failure, the MES interface can immediately alert maintenance personnel to address the issue, minimizing downtime and maintaining production flow.
Furthermore, MES interfaces promote the standardization and centralization of manufacturing data. By consolidating data from various sources into a single system, MES interfaces reduce inconsistencies and errors that can occur when handling information manually or through disparate systems. This centralization not only improves data accuracy but also enhances the analytical capabilities of the MES, allowing for more sophisticated analyses such as predictive maintenance, quality trend forecasting, and optimization of resource allocation.
In addition to operational benefits, MES interfaces play a crucial role in regulatory compliance. Strict standards govern many manufacturing sectors, necessitating meticulous record-keeping and process monitoring. MES interfaces guarantee the capture and prompt reporting of all necessary data to adhere to regulations like ISO standards, FDA requirements, and environmental protections.
MES interfaces are highly adaptable to accommodate the diverse needs of various manufacturing technologies and legacy systems. They are designed to support multiple communication protocols and data formats, from older, more established standards to the latest IoT (Internet of Things) technologies. This adaptability makes MES interfaces an essential part of not only maintaining current operational efficiencies but also enabling future technological integrations and upgrades without significant system overhauls.
The development and implementation of MES interfaces require a deep understanding of both the specific manufacturing processes and the general technology landscape. As such, creating effective MES interfaces often involves a collaborative effort among system engineers, IT specialists, and operational managers to ensure that the interfaces align perfectly with both the technical requirements and the strategic goals of the manufacturing enterprise.
In conclusion, MES interfaces are more than just data conduits; they are integral to the modern manufacturing infrastructure, enhancing operational visibility, efficiency, and decision-making capabilities. They ensure that manufacturing systems can operate at their peak and adapt to evolving industry demands, making them indispensable in the drive toward smarter, more responsive manufacturing operations.
What is the MES Concept?
The MES concept, or Manufacturing Execution System concept, is a strategic approach to industrial production that aims to connect, monitor, and control complex manufacturing systems and data flows on the factory floor. An MES's primary goal is to ensure effective execution of manufacturing operations and improve production output. By deploying an MES, companies can gain real-time insights into their operations, allowing them to optimize processes, increase productivity, and ensure product quality.
At its core, the MES concept revolves around providing a comprehensive overview of all manufacturing operations. It integrates with various sensors and machines on the production line to collect real-time data. This data might include information about machine efficiency, production rates, quality control metrics, and inventory levels. Sophisticated software algorithms then process and analyze this data to identify patterns, predict potential issues, and facilitate decision-making processes.
An MES acts as the glue that binds various stages of production. It connects disparate systems that traditionally operate in silos—such as planning systems, quality management, and maintenance management—into a cohesive unit. This comprehensive integration guarantees the collection and dissemination of information among all pertinent departments, thereby boosting collaboration and coordination within the organization.
Furthermore, the MES concept extends beyond mere data collection and dissemination. It entails dynamic control of production activities. The MES can make real-time adjustments to production processes based on the analyzed data. For instance, the MES can reroute tasks to other machines, optimizing the overall flow and minimizing downtime, if it detects a bottleneck in one part of the production line. Similarly, it can adjust production schedules in response to changes in inventory levels or urgent customer demands.
Another critical aspect of the MES concept is its role in enforcing regulatory compliance and quality standards. By maintaining detailed records of all operations and ensuring that processes adhere to predefined standards, an MES helps manufacturers comply with industry regulations and maintain high-quality outputs. This is particularly crucial in industries such as pharmaceuticals, food and beverage, and aerospace, where product quality and safety are paramount.
The adaptability of the MES is also a key feature, allowing it to support a wide range of manufacturing environments and technologies. A company specializing in discrete manufacturing of parts and components or one engaged in continuous material production can tailor the MES to meet specific operational needs. This flexibility ensures that, regardless of the scale or scope of operations, the MES can provide effective management and control.
In conclusion, the MES concept is an integral part of modern manufacturing strategies. It not only optimizes production processes but also enhances product quality, improves operational efficiency, and ensures compliance with regulatory standards. By providing a real-time snapshot of the production landscape and facilitating immediate corrective actions, an MES empowers manufacturers to stay competitive in a rapidly evolving industrial world. As industries continue to embrace digital transformation, the role of MES in achieving operational excellence becomes increasingly significant, marking it as a cornerstone of industrial management systems.
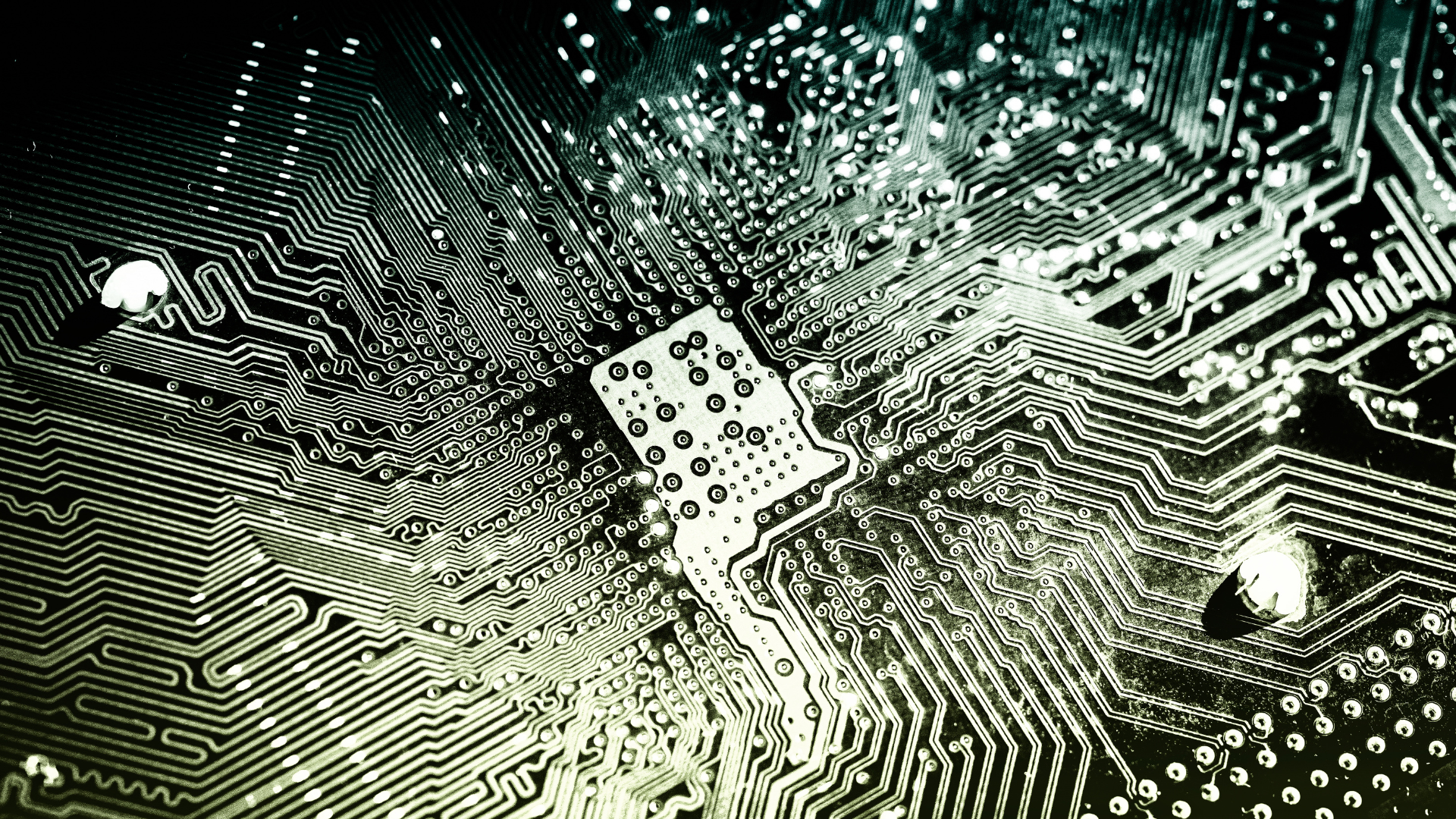
You might also like
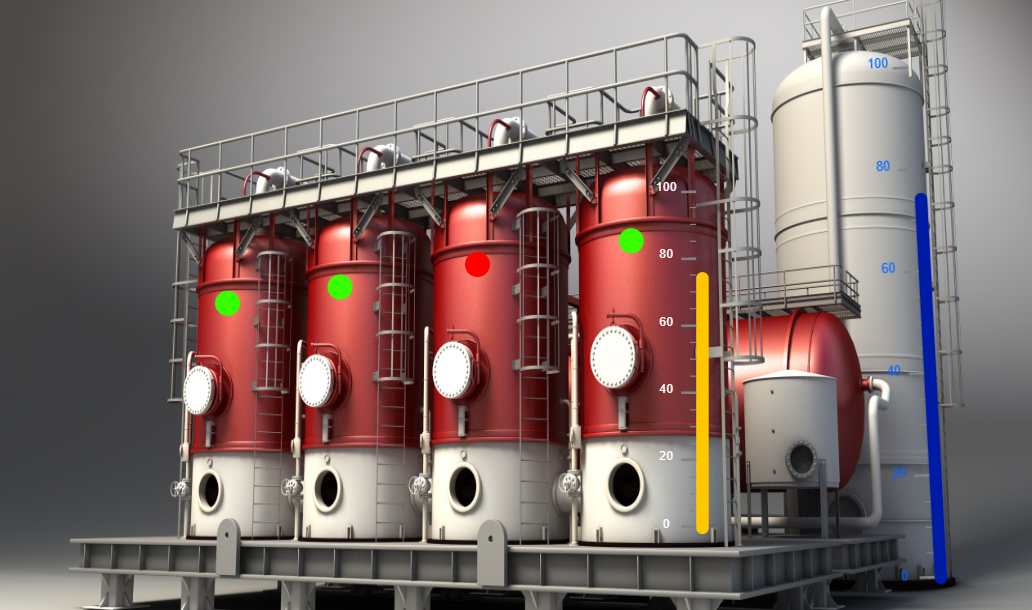
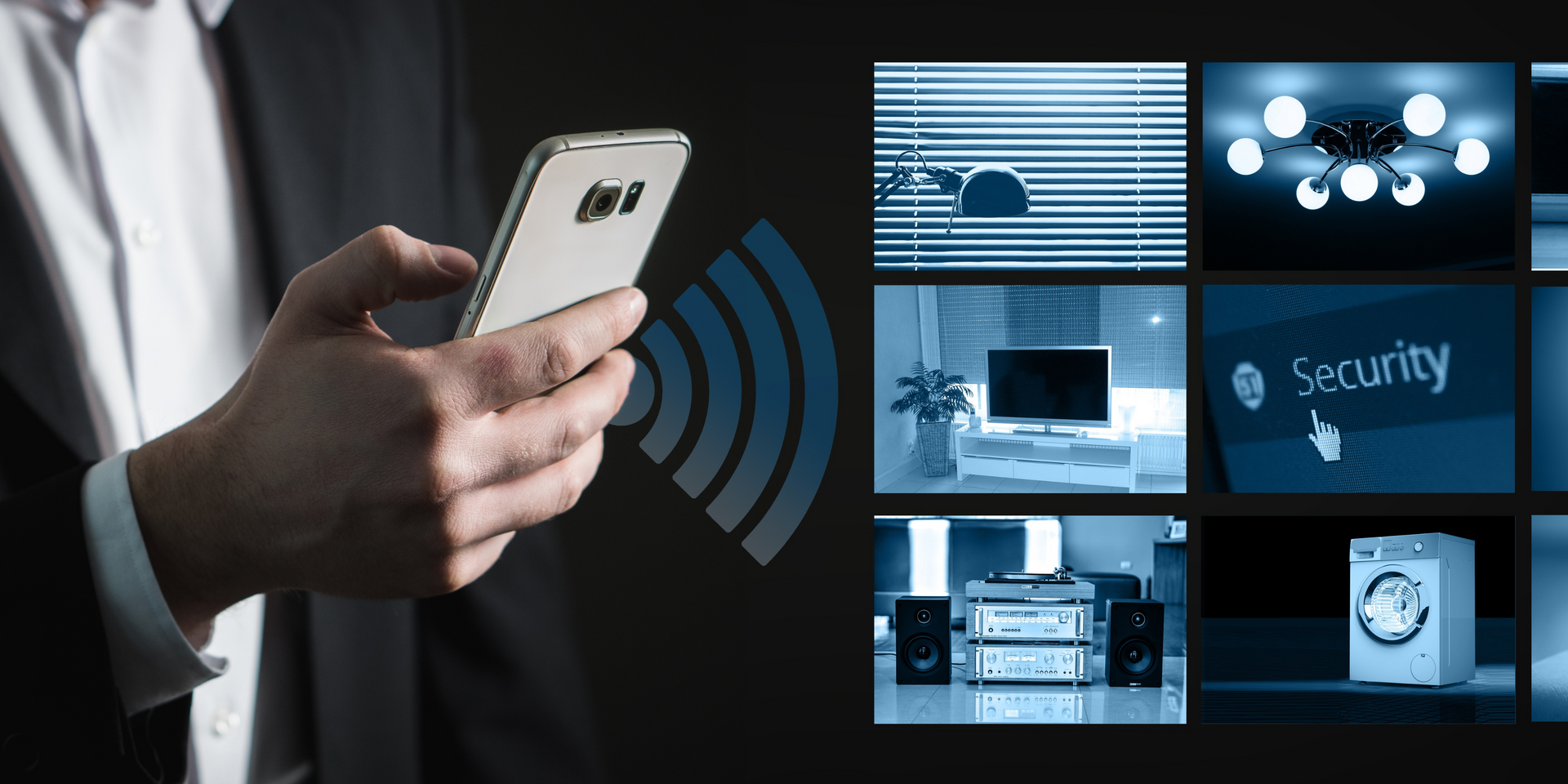
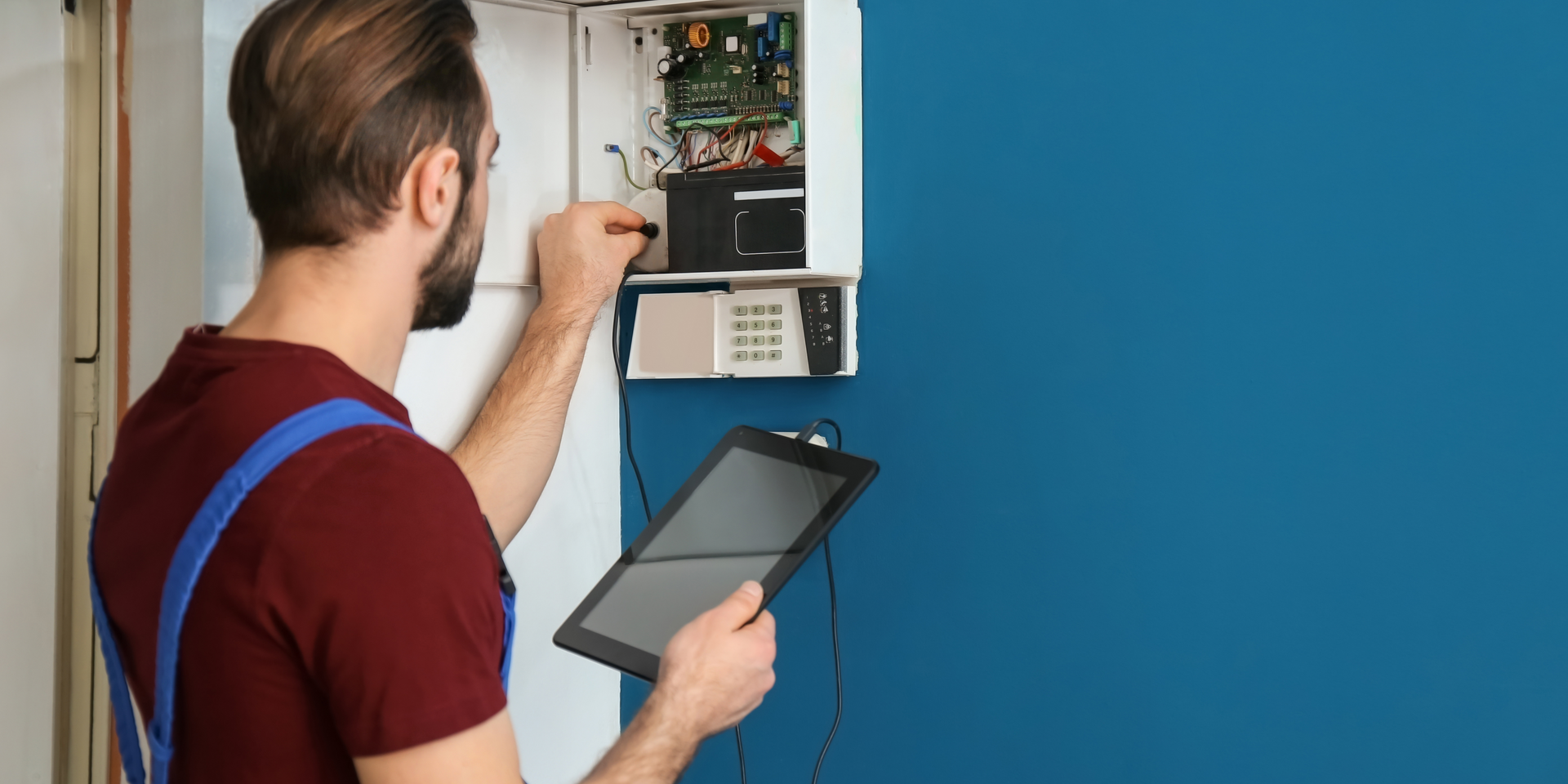