What Is the Meaning of MES?
MES Integration
MES System Integration is a crucial component in the digital transformation of modern manufacturing. This process involves the seamless incorporation of the Manufacturing Execution System (MES) into the broader technological framework of a company, ensuring a streamlined flow of information between the production floor and higher-level management systems. By integrating MES with other business systems, such as ERP (Enterprise Resource Planning) and SCM (Supply Chain Management), companies can achieve a holistic oversight of their operations, which is essential for making swift, informed decisions.
For instance, in sectors where detailed data analysis and real-time decision-making are vital—like property financing or wellness management—MES integration can significantly enhance operational efficiency. It enables a detailed tracking of every component or transaction, much like monitoring diverse projects or client engagements, ensuring that all parts of the manufacturing process align with corporate goals and comply with industry regulations. The result is not just improved productivity and reduced waste, but also a robust framework capable of supporting growth and adaptation in a fast-evolving business landscape.
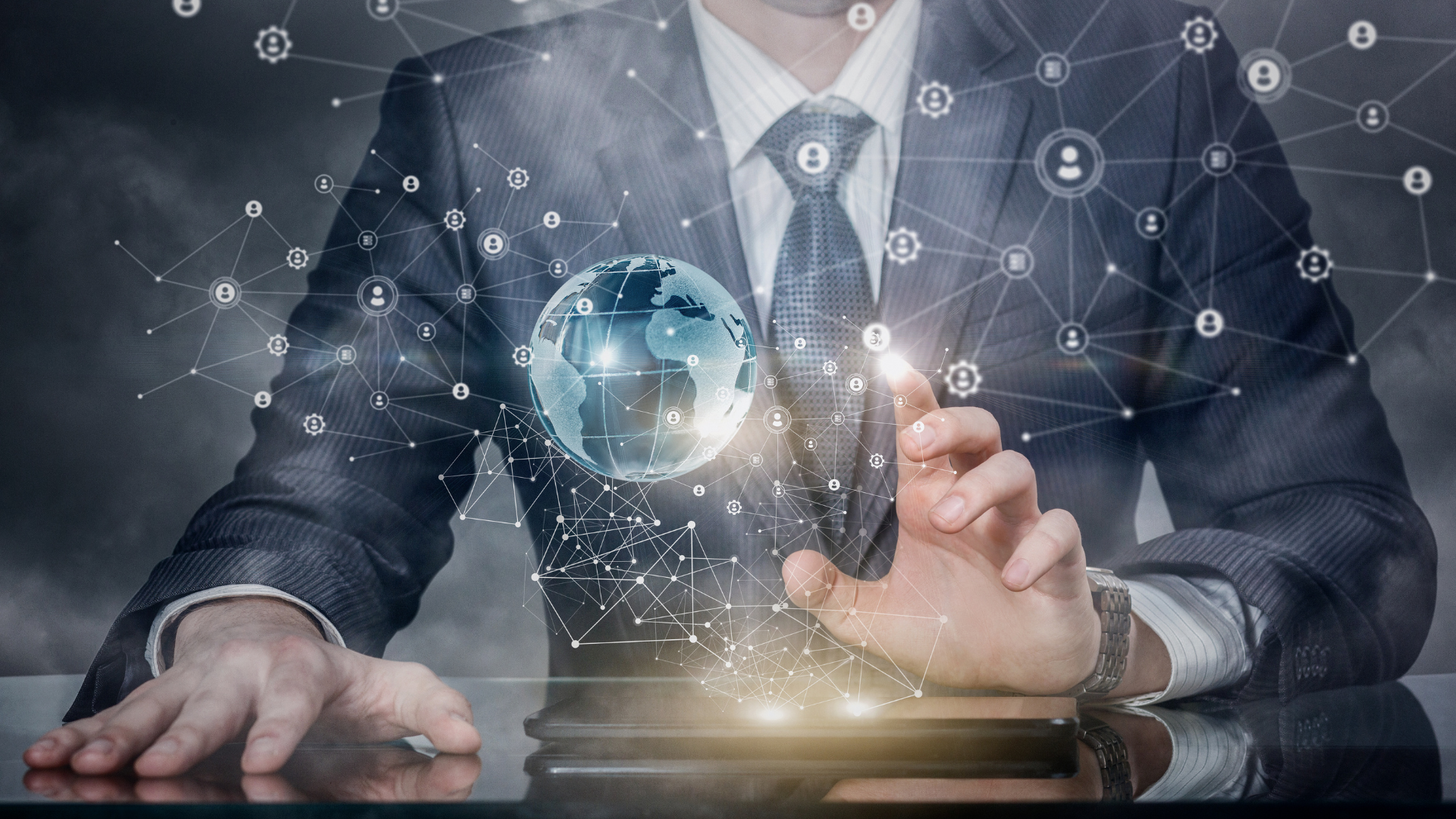
What is the meaning of MES?
The Manufacturing Execution System (MES) is a comprehensive technology framework that optimizes the execution phase of manufacturing operations. At its core, MES focuses on improving the effectiveness of production processes by monitoring and controlling the work in progress on the factory floor. This system provides a critical link between the planning stages managed by higher-level enterprise resources and the actual production activities, ensuring that everything from resource allocation to performance metrics aligns with operational goals.
MES enhances visibility into every aspect of manufacturing, from real-time data on machine utilization to tracking product quality and throughput rates. This granular insight allows businesses to fine-tune their production strategies, reduce inefficiencies, and respond more adeptly to market changes or production anomalies. Ultimately, MES serves as a pivotal element in bridging the gap between strategic planning and tangible, on-ground productivity, driving continuous improvement in industrial operations, and fostering an environment of enhanced decision-making and operational excellence.
What does the MES System do?
The MES system, or Manufacturing Execution System, serves as a dynamic backbone for manufacturing operations, focusing on the execution of manufacturing processes. This system orchestrates the minute-to-minute activities on the production floor, ensuring that every component of the manufacturing line is operating at peak efficiency. By collecting and analyzing data directly from production machinery and operators, an MES provides unparalleled transparency into all aspects of production. This includes tracking order status, monitoring machinery performance and condition, adhering to quality standards, and managing product lifecycles.
The MES system uses this information to identify areas that require improvement, predict potential disruptions, and propose optimizations. Essentially, it acts as the central hub for operational intelligence, empowering manufacturers to not only keep pace with but also anticipate the demands of modern production environments. This capability to actively manage and optimize production makes the MES system an indispensable tool for manufacturers aiming to enhance productivity, improve product quality, and increase operational efficiency.
What is a MES engineer?
An MES engineer, or Manufacturing Execution System engineer, plays a pivotal role in industrial manufacturing. Tasked with designing, implementing, and maintaining MES solutions, these engineers ensure that manufacturing processes are both efficient and technologically advanced. An MES engineer's primary responsibility is to integrate MES software with existing production systems to improve operational effectiveness and data transparency across the manufacturing floor. They work closely with other engineering teams and IT specialists to deploy systems that provide real-time feedback and analytics, crucial for making quick, data-driven decisions in dynamic production environments.
Moreover, MES engineers often lead troubleshooting and continuous improvement initiatives, refining systems to handle new production challenges and efficiency demands. Their work is critical not only for maintaining smooth operations, but also for driving innovations that keep manufacturing processes at the cutting edge of technology. In essence, an MES engineer is a linchpin in the manufacturing sector, crucial for any enterprise aiming to leverage technology for enhanced productivity and competitiveness.
What is the role of MES?
The role of MES, or Manufacturing Execution System, is central to modern manufacturing environments where efficiency, productivity, and quality are paramount. Essentially, MES functions as the operational brain, coordinating and optimizing the complex dance of manufacturing activities. It manages and monitors every step in the production process, from raw material input to finished product output, ensuring that each phase of production meets predetermined standards and timelines. An MES collects critical data from across the factory floor, delivering real-time insights that help manufacturers minimize downtime, optimize resource use, and accelerate production cycles.
Additionally, MES plays a crucial role in quality assurance, maintaining compliance with industry standards, and reducing the incidence of defects or non-compliance issues. By providing a detailed, bird’s-eye view of the production landscape, MES allows managers to make informed decisions quickly, adapt to market changes, and improve overall operational agility. In sum, the role of MES is to synchronize and streamline manufacturing processes, making it an indispensable tool for any manufacturing operation aiming to thrive in a competitive and demanding market environment.
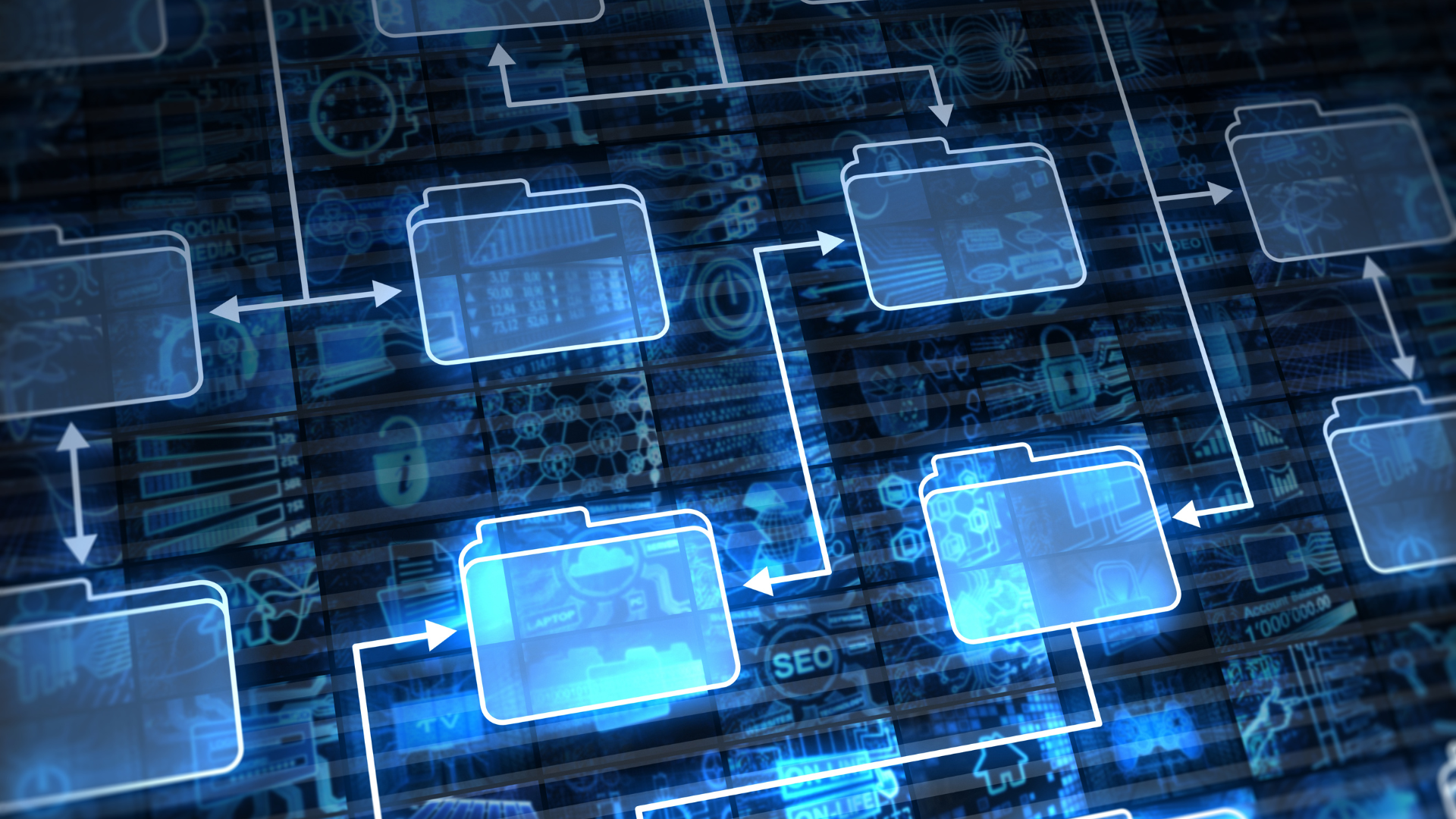
You might also like
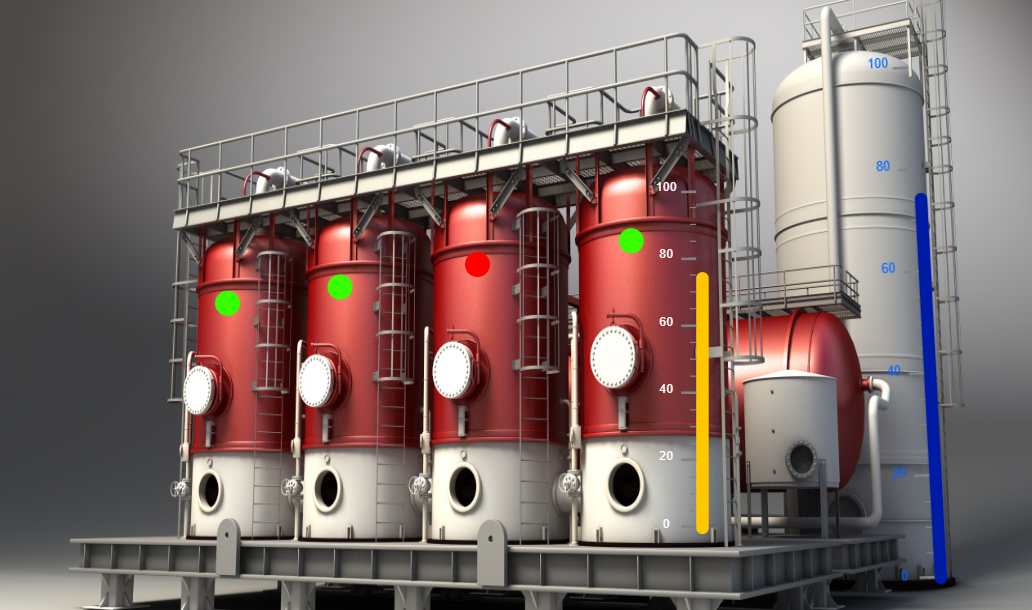
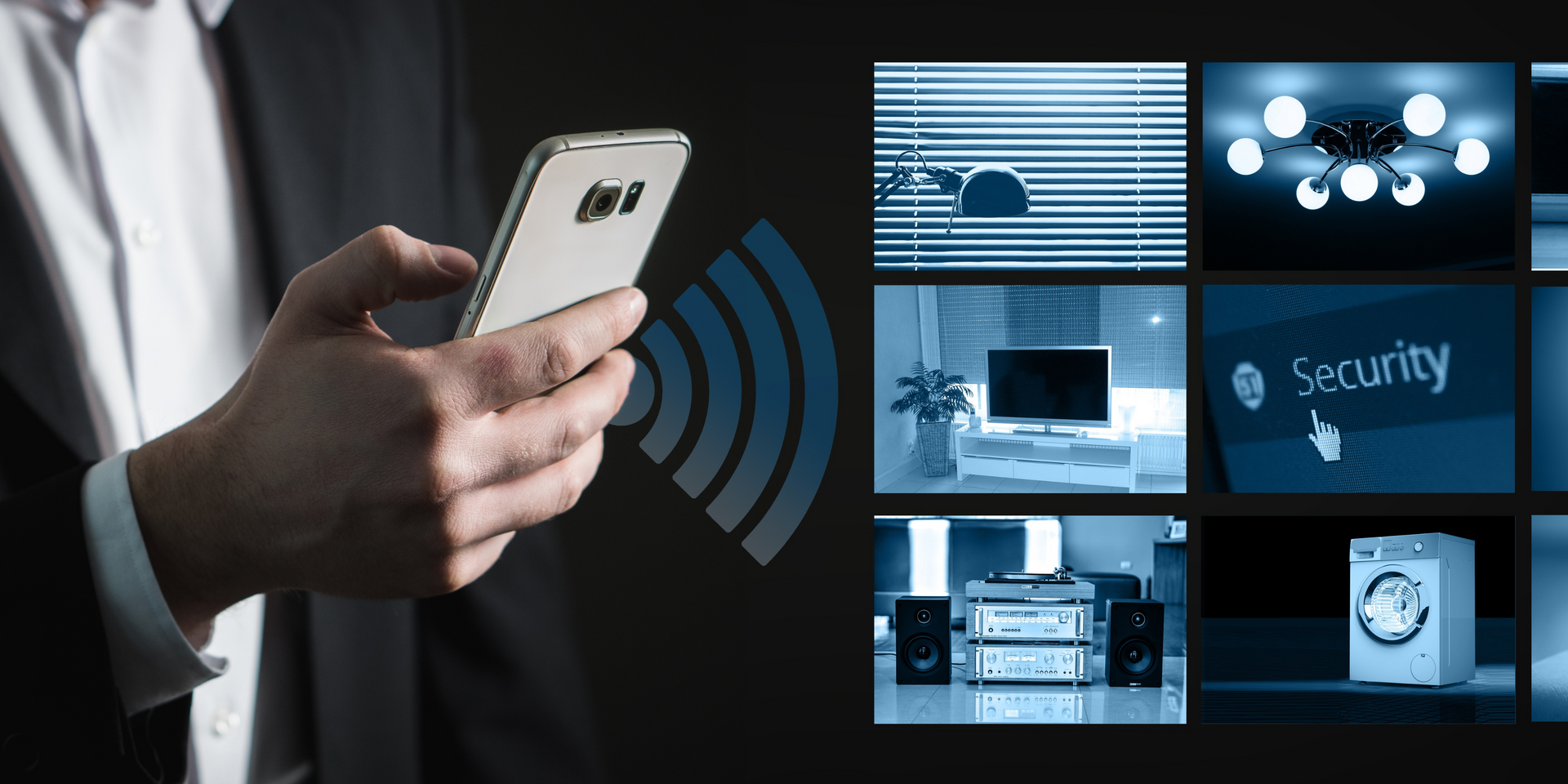
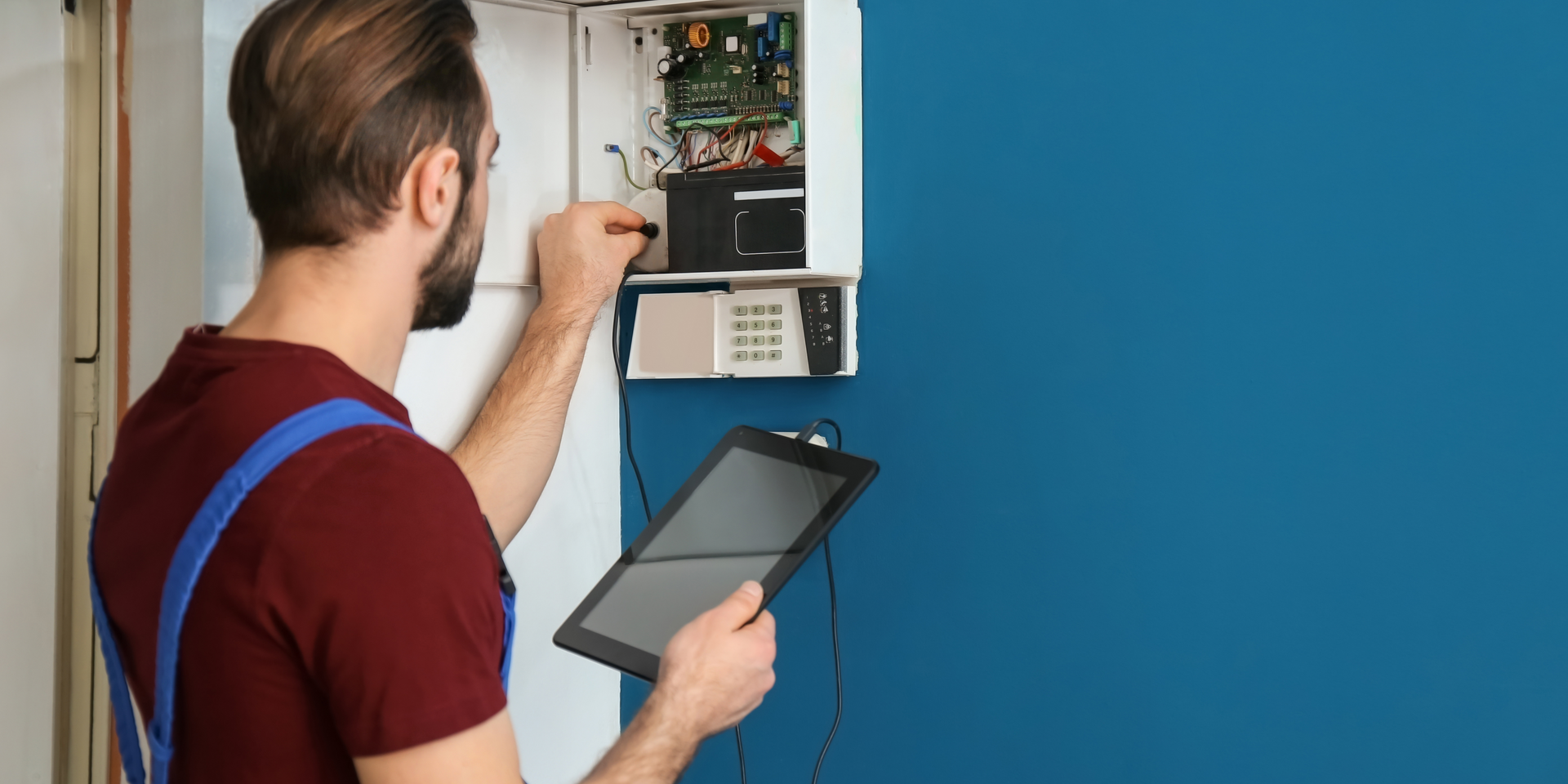