Programmable Logic Controllers (PLCs) find extensive usage across industries for automating processes and controlling machinery. PLCs excel in tasks requiring precise timing, logic operations, and reliability, making them indispensable in manufacturing, energy, and transportation sectors. Examples of PLC applications in real life include controlling assembly lines in manufacturing plants, managing traffic signals in transportation systems, and regulating temperature and humidity levels in HVAC systems. Comprehensive guides and manuals in PDF format offer detailed insights into PLC programming, operation, and maintenance, serving as valuable resources for engineers and technicians.
Programmable Logic
What is a Programmable Logic Device?
A
Programmable Logic Device (PLD) refers to a digital integrated circuit that can be programmed to perform specific logic functions. These devices are widely used in various applications where flexibility and reconfigurability are essential. PLDs are classified into several types, including Complex Programmable Logic Devices (CPLDs) and Field-Programmable Gate Arrays (FPGAs), each offering different levels of complexity and capabilities. Programming languages such as VHDL and Verilog are commonly used to design and implement logic functions within PLDs. Additionally, Programmable Logic Arrays (PLAs) are a type of PLD consisting of an array of AND gates feeding a fixed array of OR gates, providing a flexible yet structured approach to logic implementation.
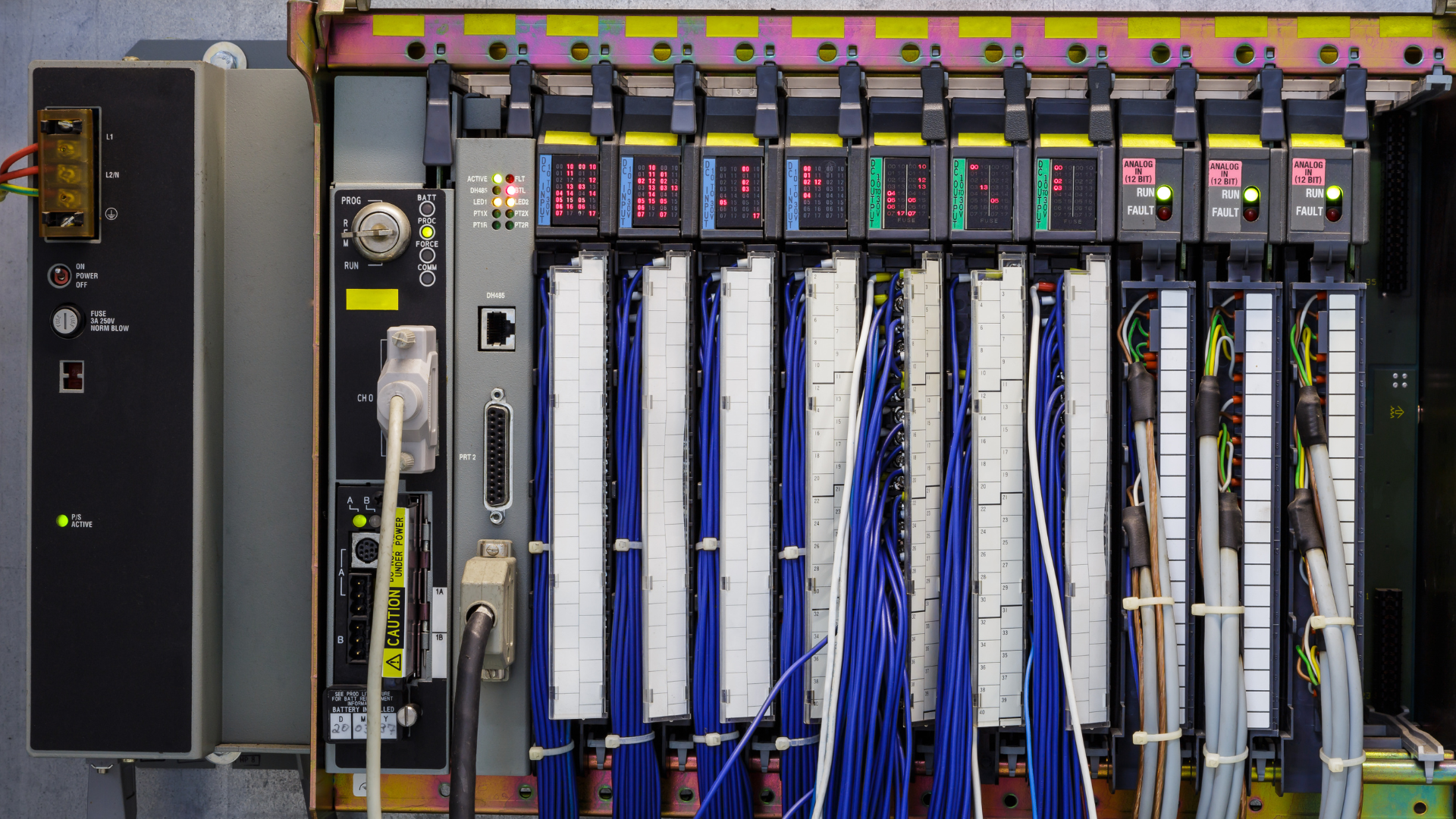
What is an Example of Programmable Logic?
Programmable Logic Devices (PLDs) encompass a wide range of examples, including CPLDs and FPGAs. These devices are utilized in various industries such as telecommunications, automotive, and consumer electronics. Presentations (PPTs) on Programmable Logic Devices provide insights into their functionalities and applications, offering valuable resources for understanding their capabilities. Five common applications of Programmable Logic Controllers (PLCs) include industrial automation, robotics, process control, automotive systems, and home automation. Components of PLCs typically include a CPU, input/output modules, memory, and communication interfaces, forming the backbone of automated control systems.
What are Logic Devices Examples?
The term PLC stands for Programmable Logic Controller, a critical component in industrial automation systems. Various reputable brands produce PLCs, including Siemens, Allen-Bradley, and Mitsubishi Electric, offering a wide selection of features and capabilities to suit different application requirements. A Programmable Logic Array (PLA) serves as a fundamental building block in digital logic design, featuring an array of programmable AND gates feeding into a fixed array of OR gates. Resources such as Programmable Logic Devices PDFs provide comprehensive documentation and information on PLDs, aiding in their understanding and utilization.
What are PLCs Used For?
Is A Raspberry Pi A PLC?
While both Raspberry Pi and Programmable Logic Controllers (PLCs) are programmable devices, they serve different purposes and operate in distinct environments. Raspberry Pi is a versatile single-board computer primarily used for educational, hobbyist, and prototyping purposes, offering flexibility in software development and connectivity options. On the other hand, PLCs are specifically designed for industrial automation, featuring rugged construction, real-time operation, and compatibility with industrial protocols. While it's possible to use a Raspberry Pi for certain control tasks, it lacks the reliability and determinism required in critical industrial applications typically addressed by PLCs.
You might also like
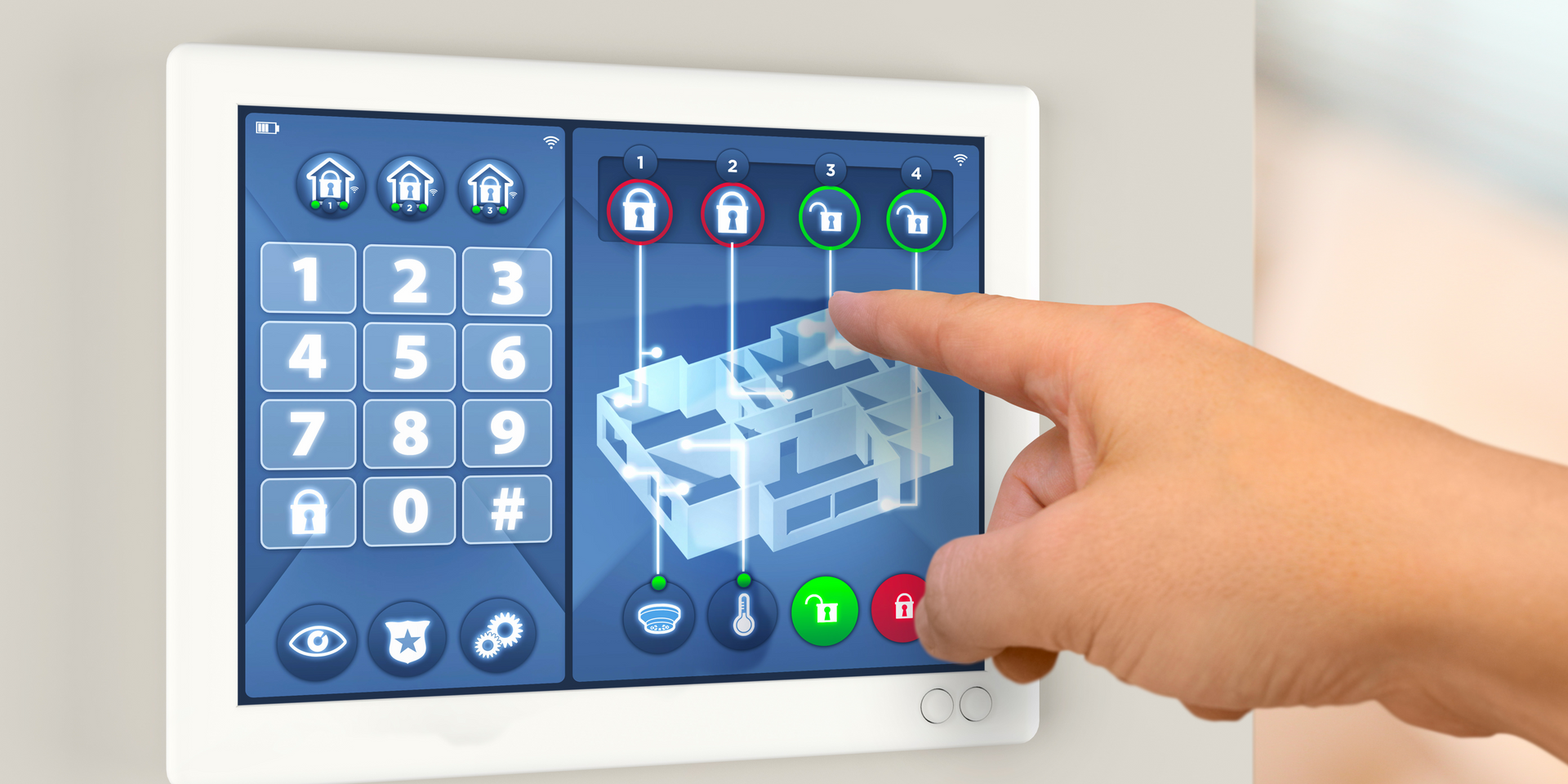
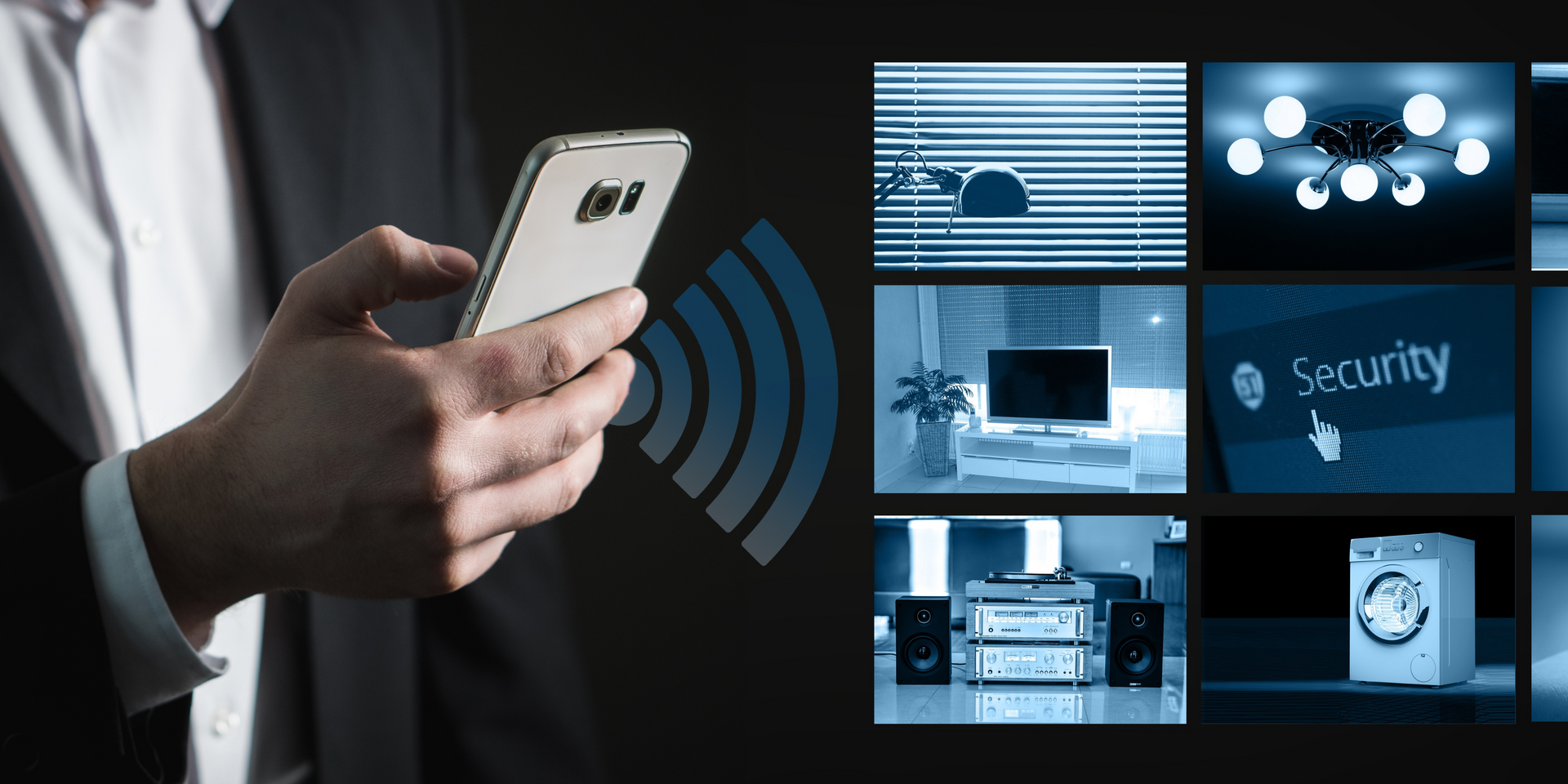
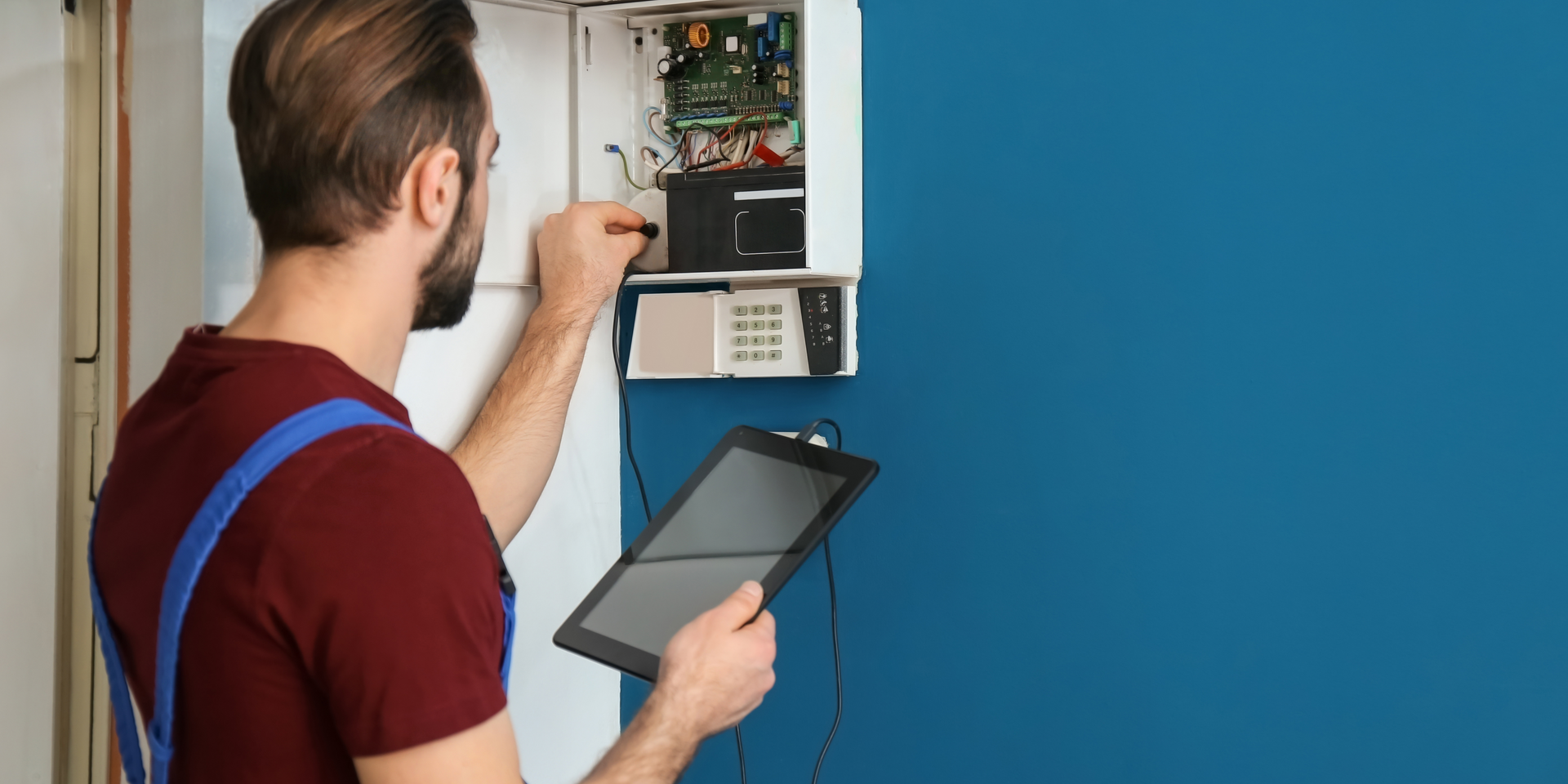