SCADA Applications
"What is a SCADA System?" one might ask. Supervisory Control and Data Acquisition (SCADA) systems stand at the forefront of industrial automation, providing pivotal control and monitoring capabilities. These systems are crucial for the seamless operation of various sectors, facilitating real-time data collection and control at the plant level, remote monitoring stations, or in hazardous environments. This article delves into the diverse applications of SCADA systems, highlighting how they significantly enhance operational efficiencies and safety across different industries.
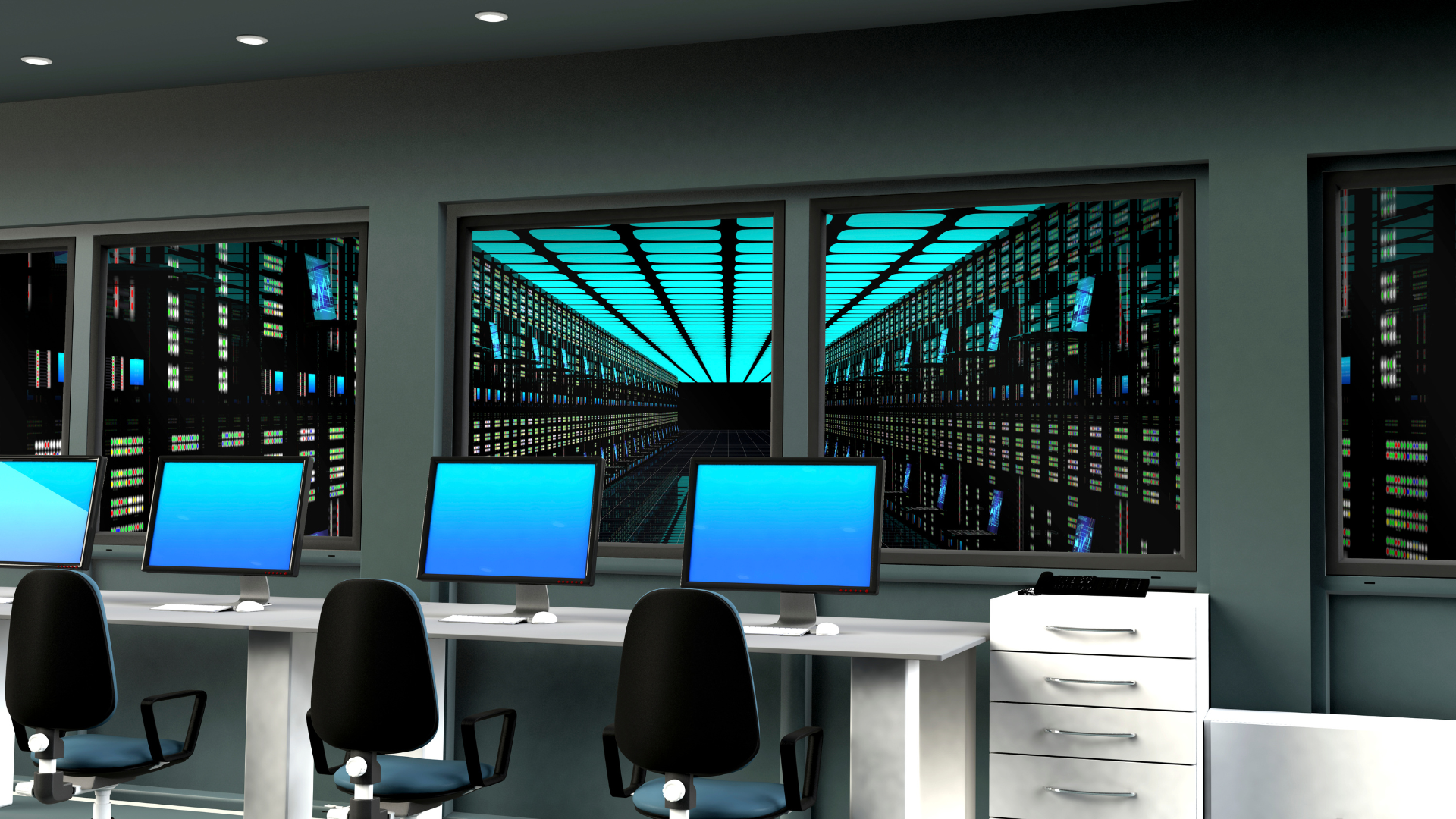
What Are the Applications of SCADA?
Application of SCADA in Industry
SCADA systems are extensively used in industries such as oil and gas, water treatment, and manufacturing. By enabling automated control and real-time data acquisition, SCADA systems improve process efficiencies, reduce costs, and enhance safety measures. They monitor machinery and production flows, ensuring that operations run smoothly and that any discrepancies are managed promptly.
Advantages of SCADA
One of the main advantages of SCADA is its ability to optimize operations and facilitate predictive maintenance. By analyzing data collected from various sensors, SCADA systems can predict equipment failures before they occur, minimizing downtime and extending the lifespan of machinery.
SCADA Applications PDF
For those looking to dive deeper into SCADA applications, numerous resources and PDF documents are available online. These documents provide detailed analyses and case studies on how SCADA systems are implemented across different sectors, offering valuable insights into their practical benefits and operational frameworks.
What Are the Applications of PLC and SCADA?
Applications of SCADA PDF
Complementing the earlier mention, further resources on SCADA applications can be explored through various PDFs available online. These resources detail the technical integration of SCADA with Programmable Logic Controllers (PLCs), highlighting case studies and technical specifications.
SCADA Programming
SCADA programming involves creating the software logic that controls and monitors industrial processes. This programming is crucial for customizing SCADA systems to meet specific operational needs, optimizing both performance and reliability.
SCADA Software
SCADA software plays a critical role in the functionality of these systems, providing the user interface, data handling, and control algorithms necessary for efficient operation. The choice of software can significantly affect the scalability, resilience, and security of a SCADA system.
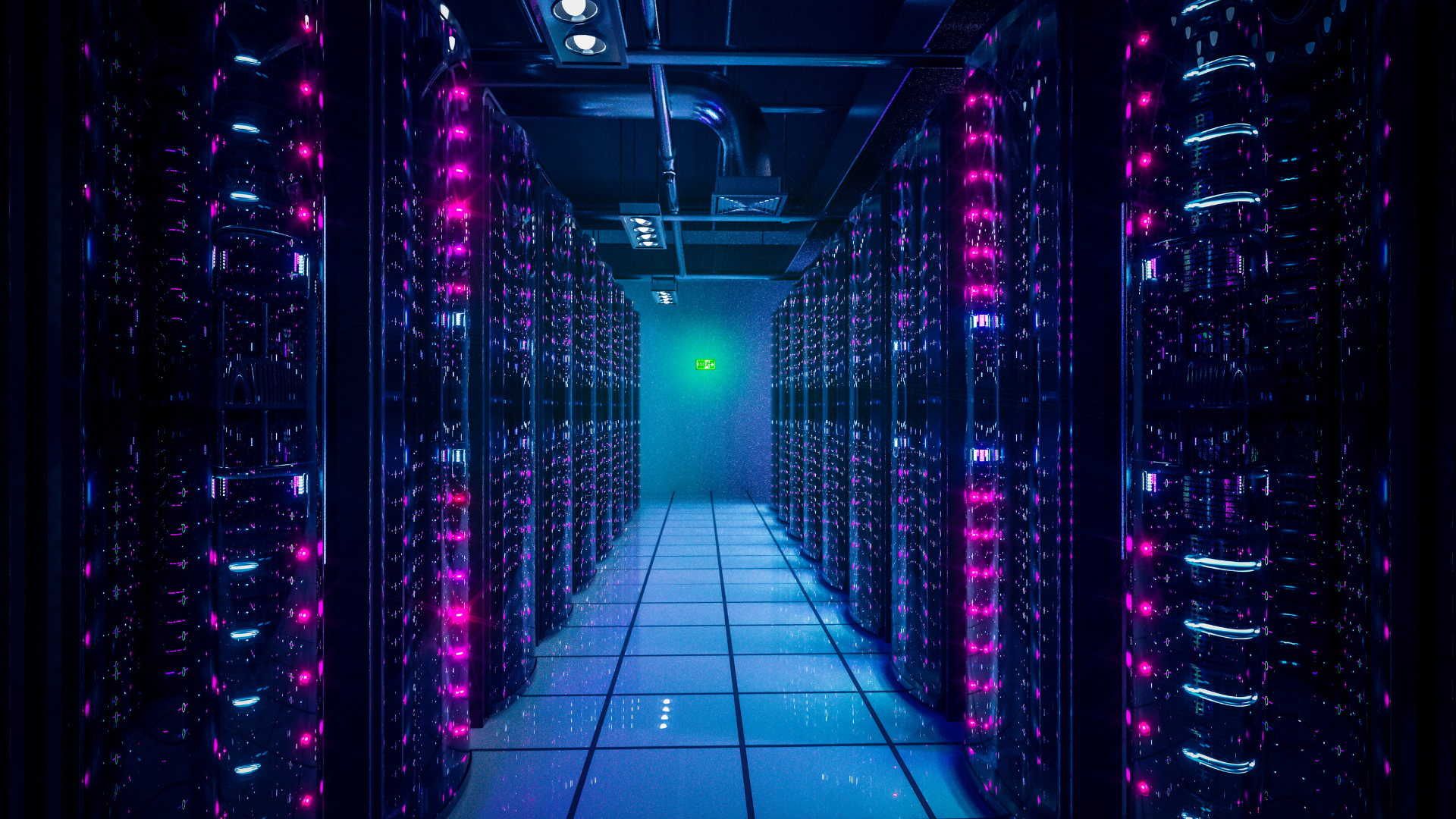
What is SCADA and How Does It Work?
Application of SCADA in Power System
In power systems, SCADA is utilized to monitor and control substations, grid status, and electricity distribution. It ensures the seamless operation of electrical grids, from generation to distribution, enhancing energy efficiency and grid reliability.
Application of SCADA in Food Industry
The food industry benefits from SCADA systems by ensuring consistent quality and compliance with health regulations. These systems monitor conditions such as temperature and humidity throughout the production process, crucial for maintaining product standards and safety.
What is an example of SCADA?
SCADA Applications Examples
Examples of SCADA applications include monitoring water levels in reservoirs, controlling the temperature in HVAC systems in buildings, and managing traffic lights in smart city infrastructures. Each application highlights SCADA's versatility in various sectors.
SCADA Architecture
SCADA architecture typically consists of sensors, controllers, networks, user interface (HMI), and communications equipment. This structured approach ensures that data flows seamlessly from the field to decision-makers, facilitating timely and informed decisions.
What is the Most Popular SCADA Software?
Popular SCADA software includes Siemens WinCC, Rockwell Automation’s FactoryTalk, Schneider Electric’s Wonderware, and GE Digital's iFIX. These platforms offer robust features for industrial applications, including real-time performance monitoring, alarm management, and data analytics.
Advantages of SCADA in Power Systems
In power systems, SCADA software not only helps in monitoring and controlling the system but also in enhancing the operational efficiency and reliability of power distribution networks.
SCADA Full Form
The full form of SCADA is Supervisory Control and Data Acquisition, which represents its primary functions in industrial and infrastructure management.
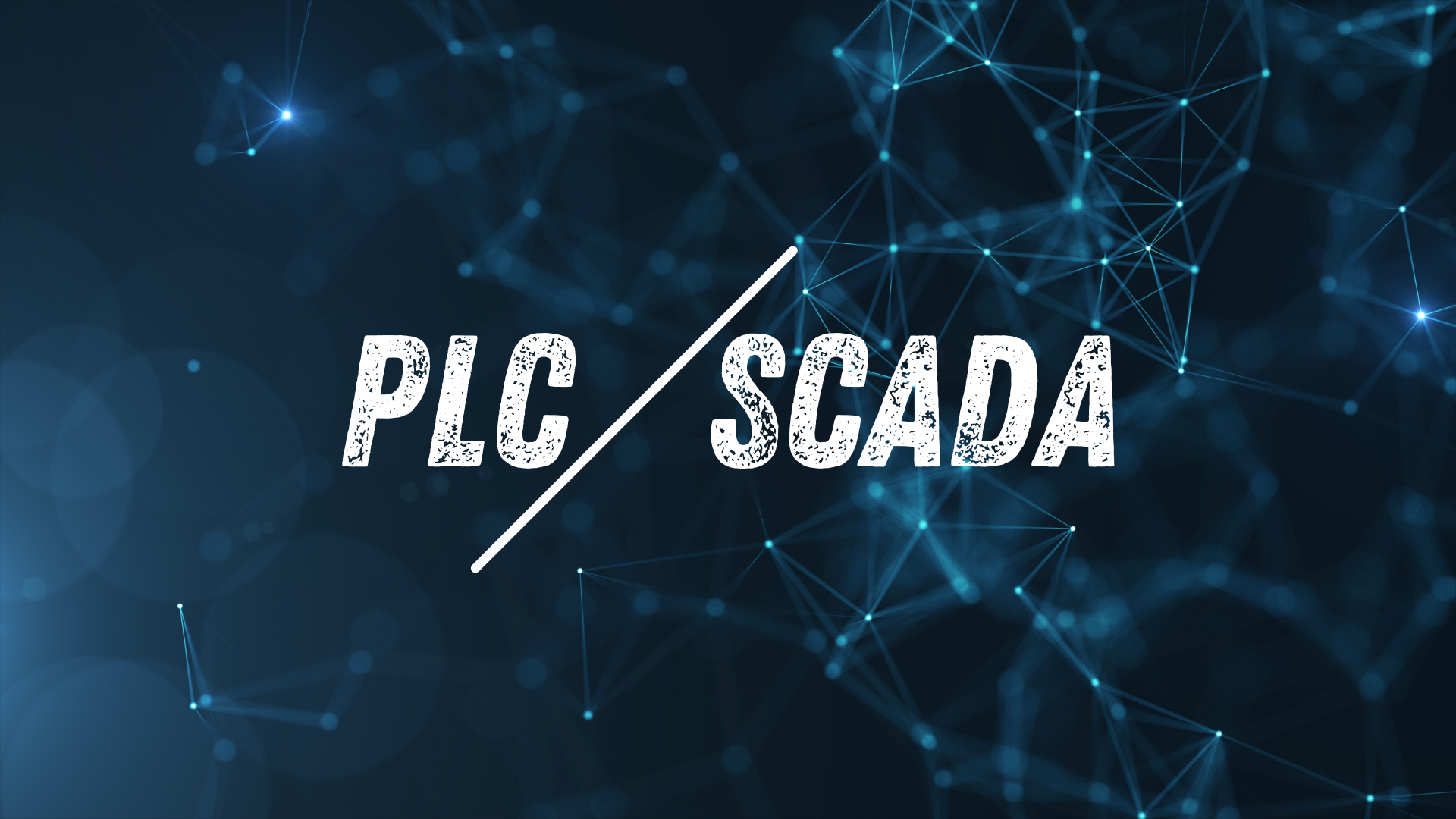
What is the Difference Between PLC and SCADA?
The main difference between PLC and SCADA is their role in automation. PLCs are hardware that control machinery and processes based on custom-written programs, while SCADA systems are software-based that provide centralized control and real-time data acquisition from PLCs and other field devices.
SCADA Software List
A variety of SCADA software options are available, ranging from Siemens WinCC to Rockwell Automation's FactoryTalk. Each software has its strengths and is chosen based on specific industry needs and system requirements.
SCADA Applications
The broad range of SCADA applications stretches from industrial manufacturing to smart city management, showcasing its importance in modern automation and monitoring systems.
What are the Three Types of SCADA?
There are typically three types of SCADA architectures: monolithic, distributed, and networked. Monolithic systems are centralized; distributed systems spread functionality across multiple locations; and networked systems use multiple computers to monitor and control subsystems through a LAN or WAN.
SCADA Full Form
Reiterating, SCADA stands for Supervisory Control and Data Acquisition.
SCADA Components
Key components of a SCADA system include the Human-Machine Interface (HMI), remote terminal units (RTUs), programmable logic controllers (PLCs), and communication infrastructure, which together ensure efficient and secure data acquisition and control.
Conclusion
SCADA systems are integral to the infrastructure of modern industries, providing critical data and control capabilities that enhance efficiency and safety. As technology advances, the scope of SCADA applications continues to expand, offering more sophisticated and integrated solutions for automated and remote monitoring systems.
For a deeper exploration of how SCADA systems can transform your operations or to discuss your specific needs with our experts, please visit our
website or
contact us directly. We're here to help you harness the full potential of SCADA technology for your business.
You might also like
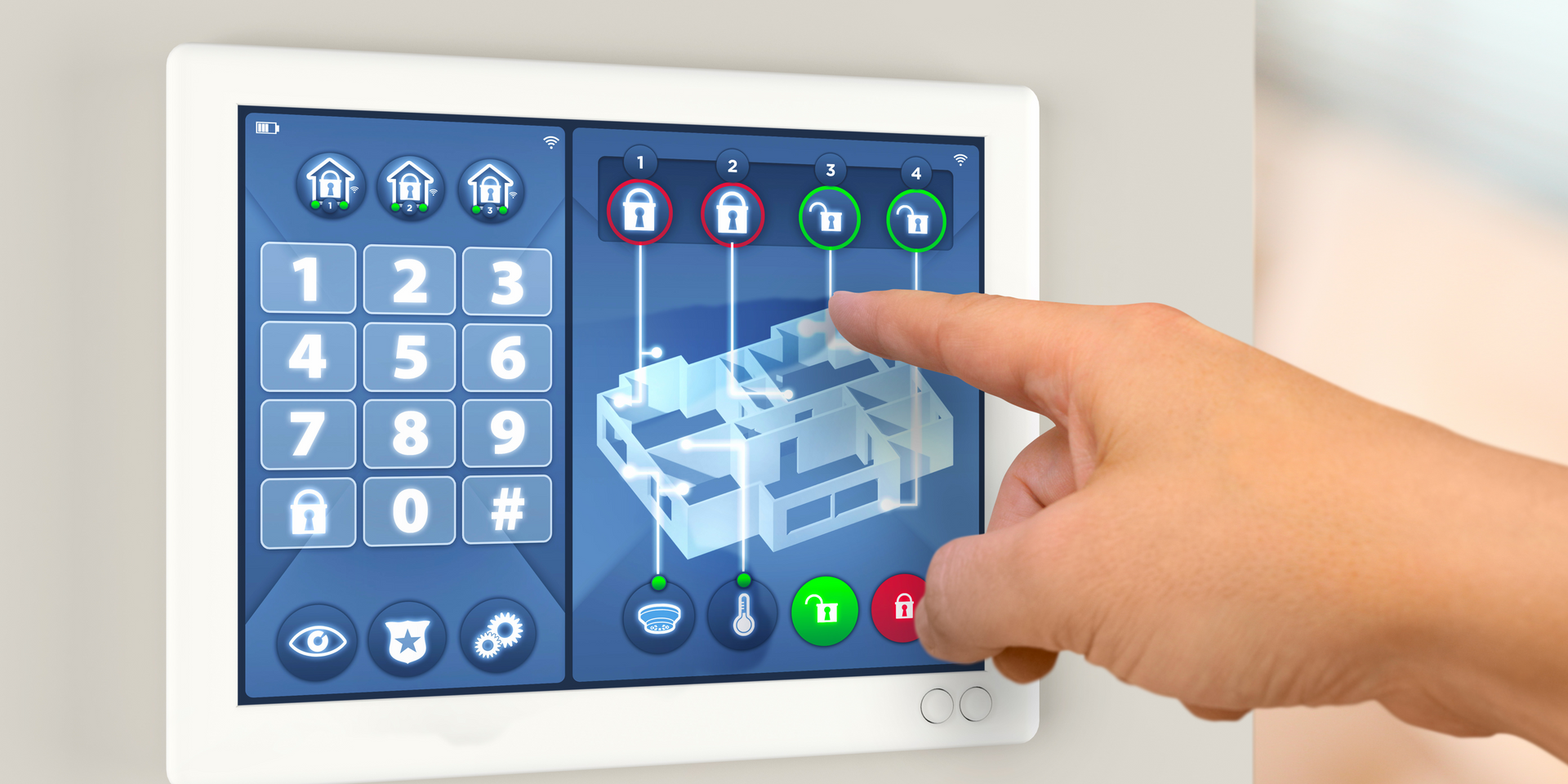
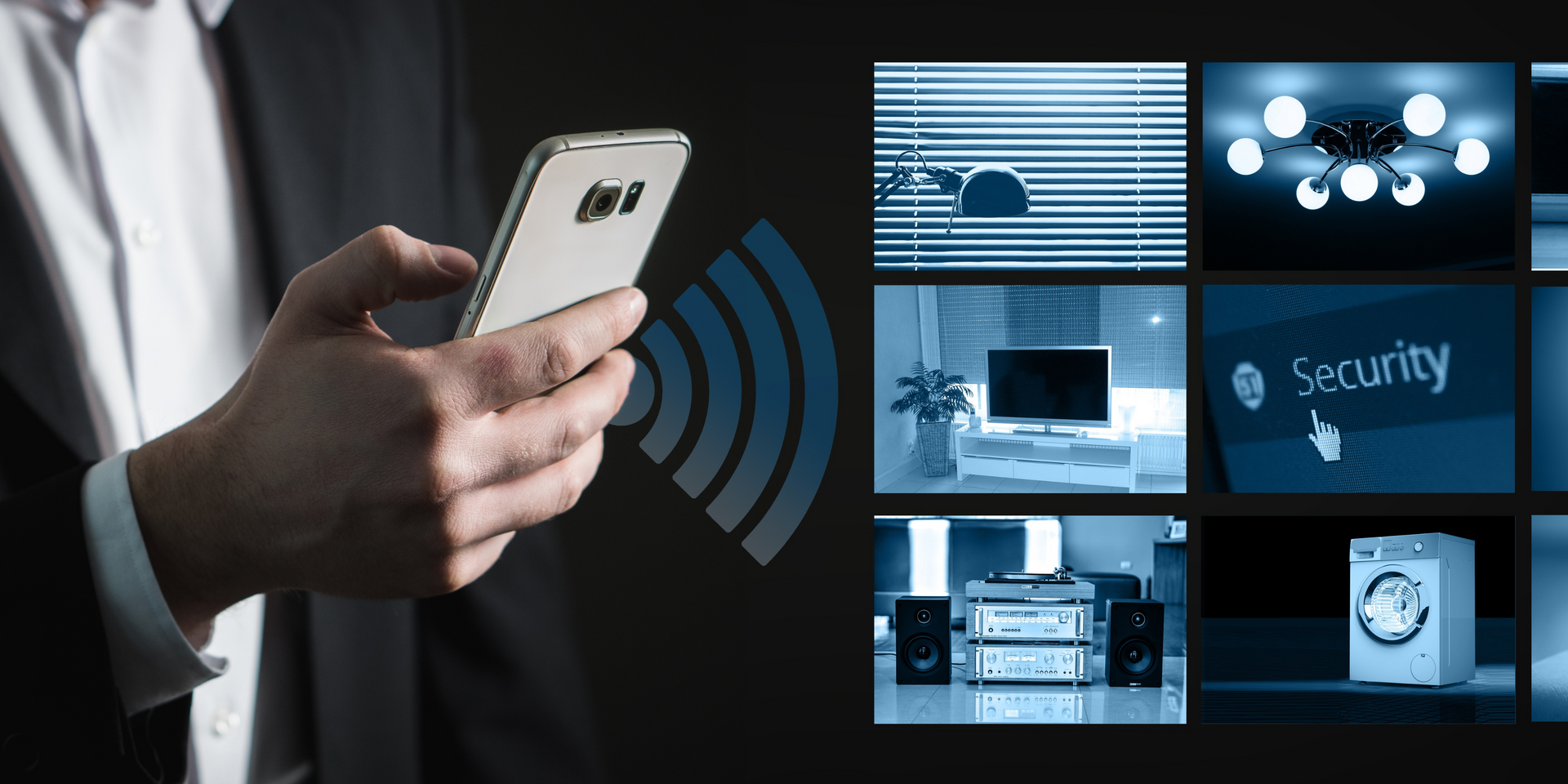
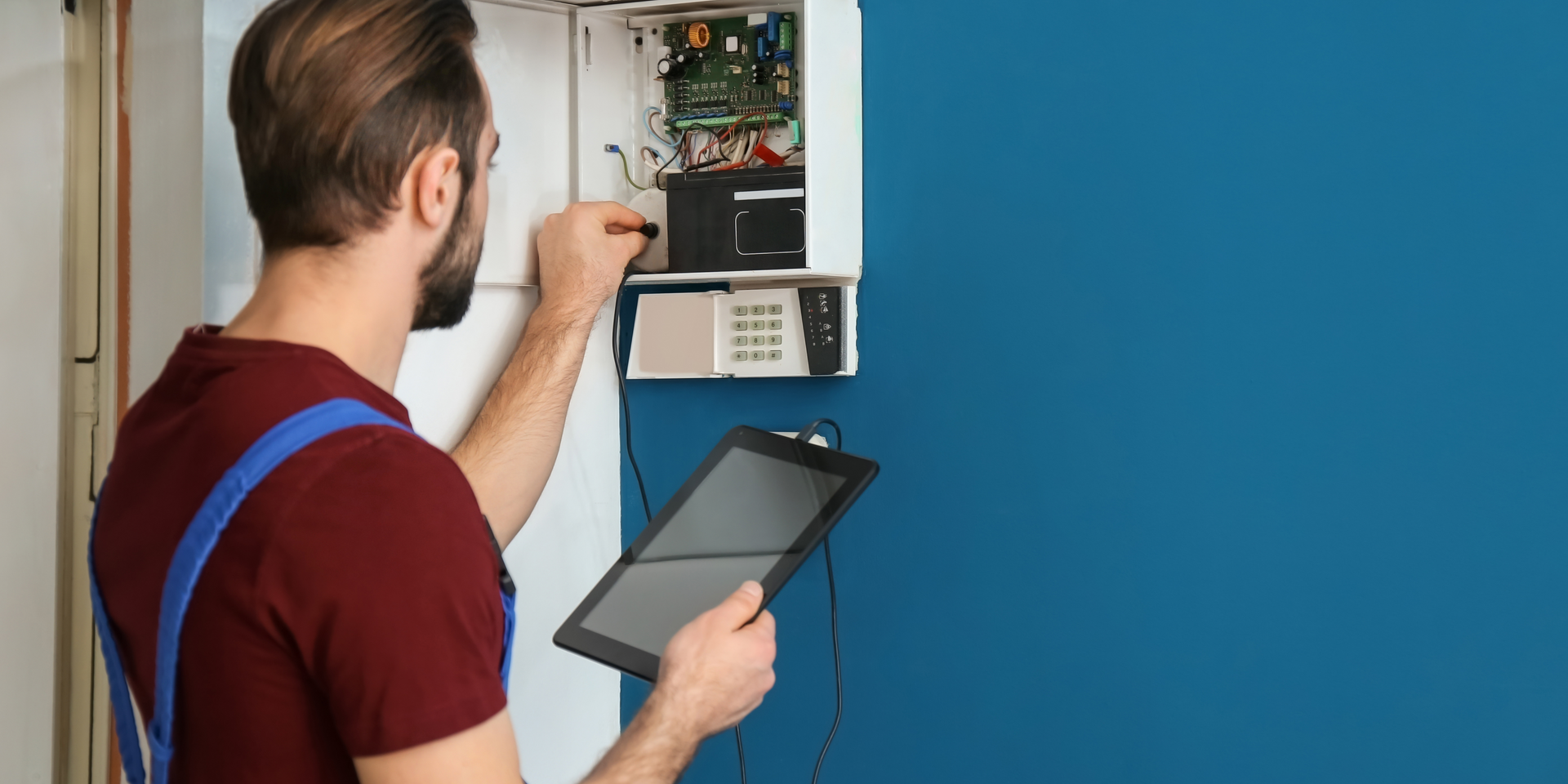