What are Manufacturing Execution Systems?
In today’s fast-paced industrial environment, Manufacturing Execution Systems (MES) play a pivotal role in streamlining manufacturing operations. These systems, often integral to what might be termed 'industrial MES,' bridge the strategic management at the corporate level with the operational processes on the factory floor. By providing precise, real-time data insights, they significantly enhance both efficiency and product quality.
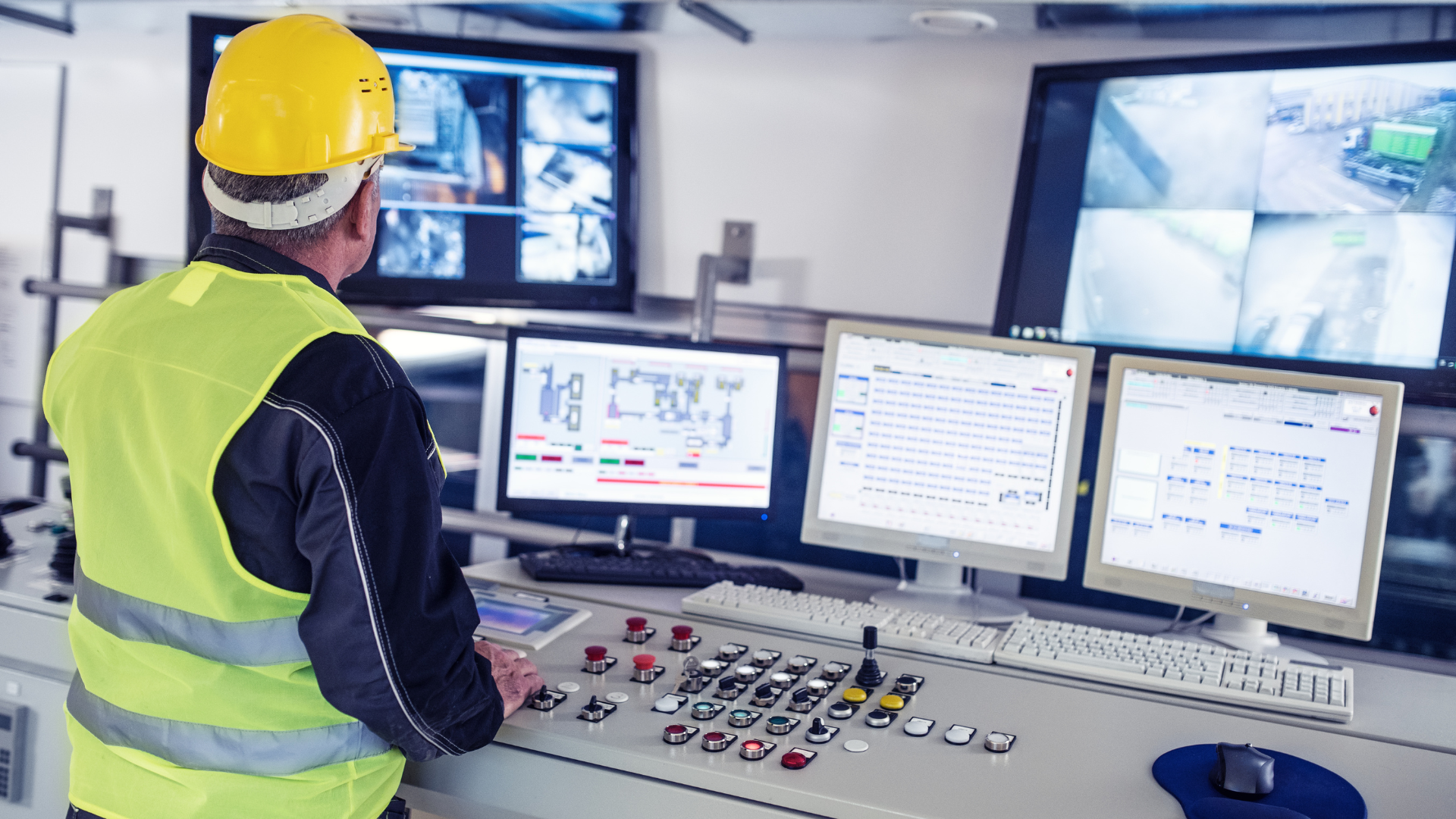
What Are Manufacturing Execution Systems?
Manufacturing Execution System Architecture
The architecture of an MES integrates various functional modules that cover everything from production scheduling and resource allocation to real-time process monitoring and quality control. This holistic integration enables manufacturers to optimize each step of the production process, ensuring maximum efficiency and compliance with industry standards.
Manufacturing Execution System PDF
A wealth of detailed MES resources are available in PDF format, offering in-depth discussions on system capabilities, implementation strategies, and the tangible benefits they bring to manufacturing operations. These resources are invaluable for decision-makers evaluating the potential impact of MES on their processes.
How Much Does an MES System Cost?
Manufacturing Execution System Software List
Investing in an MES can involve significant financial outlay, with costs varying widely depending on the system’s complexity and customization level. A comprehensive list of MES software, complete with pricing and features, can guide potential buyers in selecting a system that best fits their budget and manufacturing needs.
Gartner Magic Quadrant for Manufacturing Execution Systems
This analytical tool provides a detailed comparison of leading MES vendors, showcasing their ability to execute and their completeness of vision. It assists businesses in navigating the complex MES market, highlighting those vendors that lead the pack in innovation and reliability.
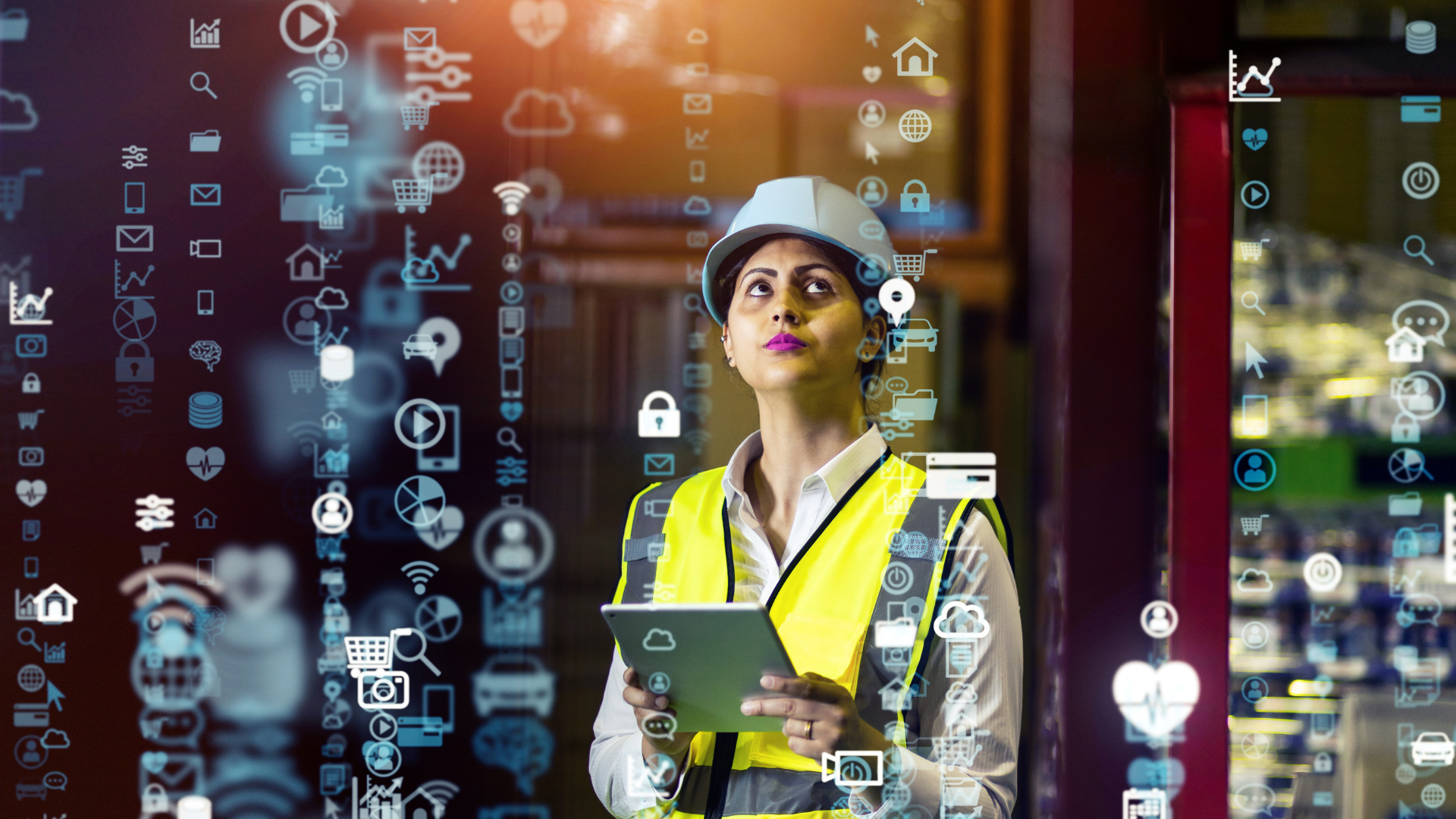
What is the Difference Between MES and ERP?
MES vs ERP
MES systems are designed to optimize manufacturing operations by providing real-time monitoring and control over the production process. In contrast, ERP systems handle broader administrative functions such as finance, human resources, and supply chain management. When MES is integrated with ERP, it creates a powerful tool that synchronizes manufacturing operations with business processes, improving overall organizational efficiency.
Leading MES Software Providers
- Rockwell Automation offers FactoryTalk ProductionCentre, which integrates seamlessly with automation and third-party systems.
- Siemens AG provides SIMATIC IT MES, supporting a wide range of manufacturing modalities.
- General Electric (GE) Digital: Features Proficy MES, enhancing production efficiency and quality insights.
- SAP SE: SAP MES is part of the Digital Manufacturing Cloud, streamlining manufacturing and enterprise operations.
- Dassault Systèmes delivers DELMIA Apriso, extending MES capabilities to include process planning and quality assurance.
What is the Difference Between MES and QMS?
List of MES Software
- FactoryTalk ProductionCentre by Rockwell Automation
- SIMATIC IT MES by Siemens AG
- Proficy MES by General Electric (GE) Digital
- SAP MES by SAP SE
- DELMIA Apriso by Dassault Systèmes
- Oracle Manufacturing Execution System (MES) by Oracle
- Plex Manufacturing Cloud by Plex Systems
- Honeywell Forge for Industrial by Honeywell
Top MES Systems
- FactoryTalk Production Centre is widely recognized for its integration capabilities and robust data management.
- SIMATIC IT MES: Known for its flexibility across various manufacturing types and comprehensive analytics.
- Proficy MES: Prized for its adaptability and strong emphasis on improving production efficiency.
- SAP MES is valued for its integration with SAP’s enterprise resources and scalability.
- DELMIA Apriso is renowned for its extensive functionality that covers global manufacturing operations and real-time visibility.
What is the Difference Between MES and SAP?
SAP MES
SAP offers a specialized MES suite that is tightly integrated with its ERP solutions, enabling seamless data flow and process management across all levels of a manufacturing organization.
What is the Difference Between MES and DCS?
Unlike DCS (Distributed Control Systems), which are primarily concerned with the continuous control of manufacturing processes, MES provides a broader range of functionalities, including but not limited to production scheduling, quality management, and compliance tracking, making it suitable for both discrete and process manufacturing environments.
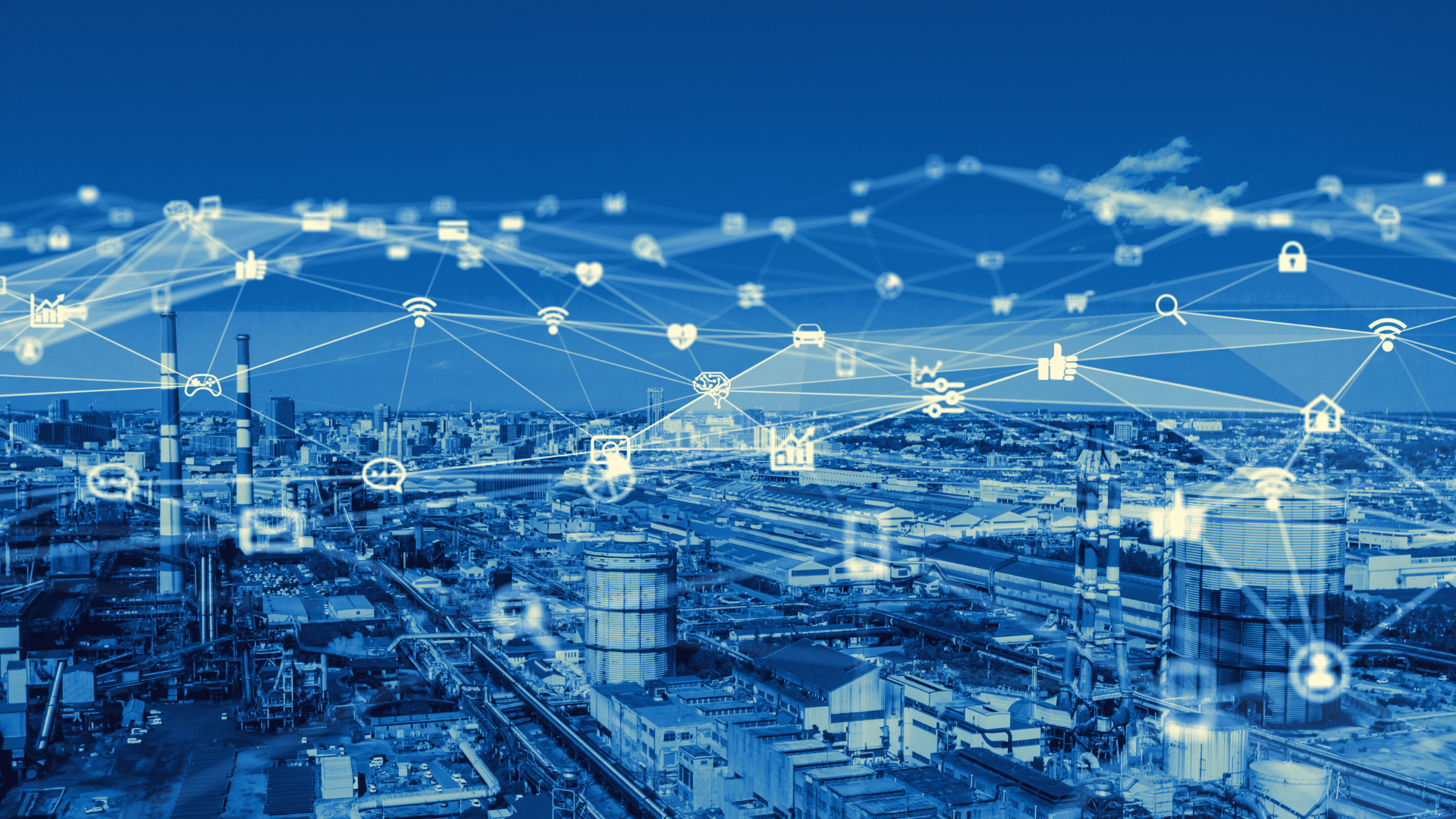
What Does a Manufacturing Execution System Do?
MES enhances operational efficiency by enabling precise control over manufacturing resources, minimizing waste, and reducing downtime. It facilitates a responsive manufacturing environment capable of quickly adapting to market changes or production issues.
What is Manufacturing Execution System Software?
Benefits of Manufacturing Execution System: Implementing MES software leads to numerous operational benefits, including increased productivity, enhanced quality control, reduced operational costs, and improved compliance with environmental and safety regulations.
Conclusion
As industries continue to evolve towards more digitized and integrated operations, MES stands as a crucial technology that can significantly enhance manufacturing capabilities. Understanding and implementing an MES can lead to substantial improvements in efficiency and product quality.
To learn more about how MES can revolutionize your manufacturing operations, contact us today.