What Are The 3 Types Of Automation?
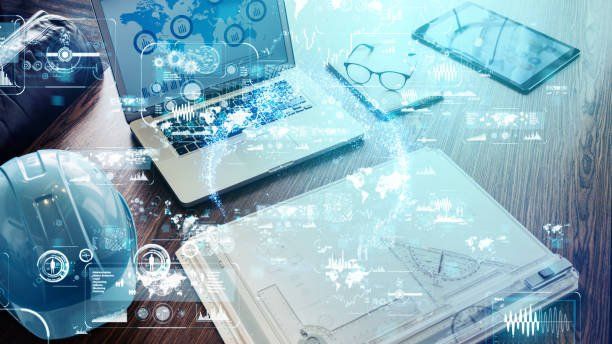
This type of industrial automation can include technologies such as flexible handling systems, automated material handling, and automated manufacturing. With programmable automation systems, it is possible to make changes to a product or process by changing the control program. Programmable automation is really flexible to process different soft products, the productivity will be minimal, different mixtures of products can be produced. This type of automation, called software automation, is used in computer-controlled flexible manufacturing systems and enables more flexible production.
At the same time, the entire production process (including production, planning and control) is automated using machine tools with numerical control, industrial robots and other types of automation tools. Unlike the equipment used in the stationary automation process, the equipment used in the second type of automation is specifically designed to make changes to the product. Stationary automation systems are mainly used in discrete mass production systems and continuous flow systems such as paint shops, distillation processes, transfer lines and conveyor belts. Since this type of automation is designed for a specific task, stationary automation systems can provide high performance and increase efficiency.
Essentially, stationary automation can be thought of as a combination or integration of different operations in a single piece of equipment, which would make the system very complex. An example of fixed automation equipment would be an automated conveyor system designed to increase efficiency by moving objects from point A to point B with minimal effort. This type of automation is typically used in batch processes and workshops with a wide variety of products and low to medium volume of work, such as in the textile industry.
A flexible automation system can efficiently produce different combinations of products without separating them into different batches, as is required in mass production. In essence, flexible automation allows you to produce different types of products without wasting time on reprogramming. As the name suggests, agile automation is a manufacturing technique designed to easily adapt and respond to changing manufacturing needs such as product type and quantity.
Flexible automation is an enhancement to programmable automation, in which computerized manufacturing systems are able to change production schedules and the physical configuration of machines or cells with minimal loss of production time. In the case of fixed automation, the machining or assembly operations in the system are fixed by the equipment configuration, while in the case of programmable automation, the production equipment can change the sequence of operations to be able to handle different product configurations. . Stationary automation, also known as "hard automation", refers to automated manufacturing facilities in which the sequence of machining operations is determined by equipment configuration.
An important feature of stationary automation is that the sequence of production operations is fixed by the design of the production equipment, and therefore the sequence cannot be easily changed at a later stage in the product life cycle. In-sequence operations for rigid automation are usually simple in the sense that they include simple linear motion and rotational motion. Stationary / complex automation. Stationary automation systems involve the use of stationary production or special equipment to perform repetitive stationary sets of operations or actions.
You might also like
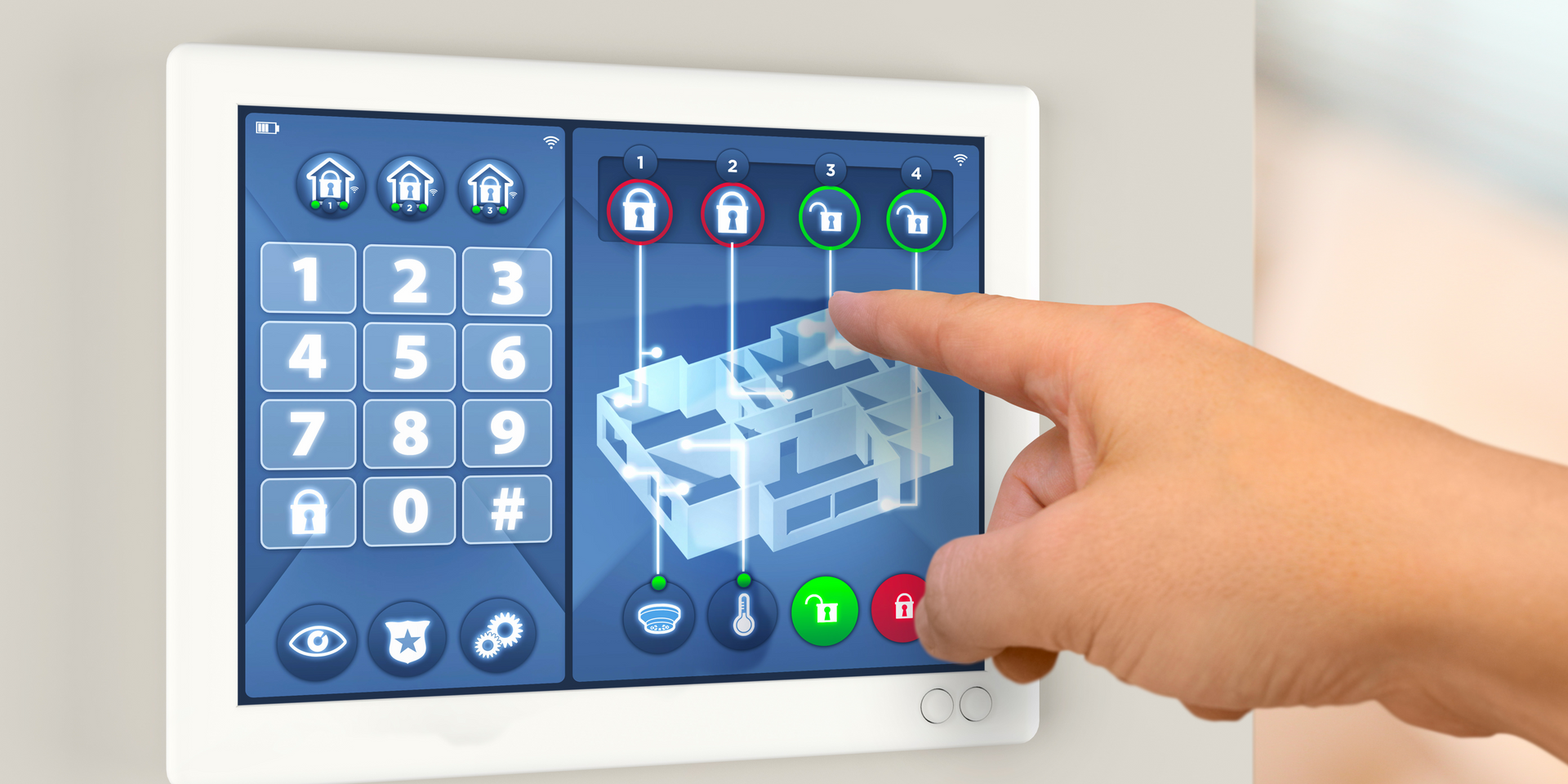
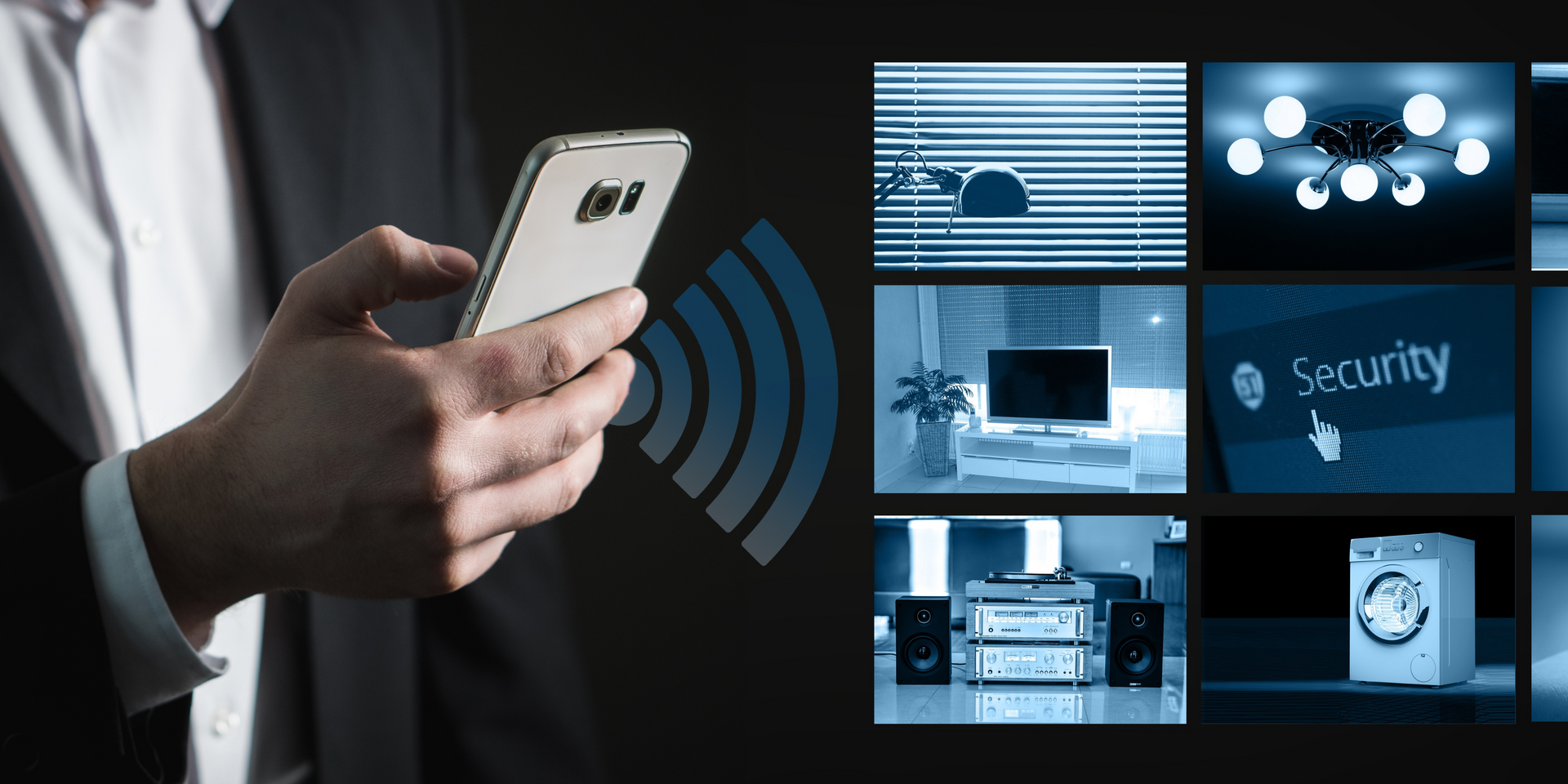
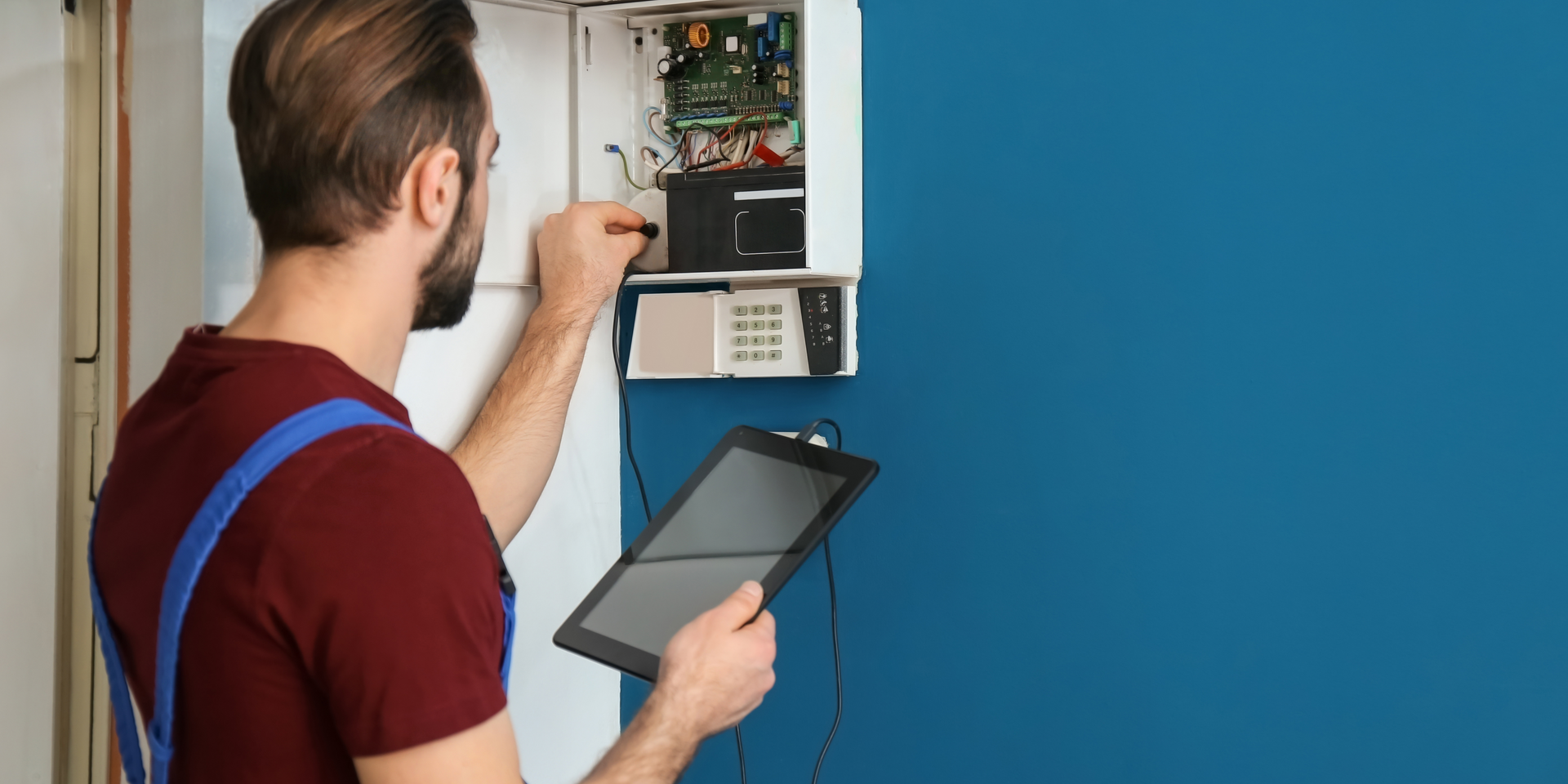