What Are The 4 Types Of Automation?
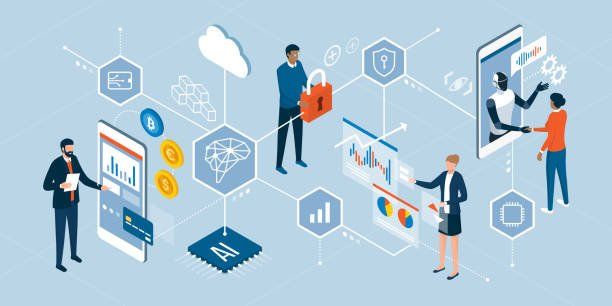
Industrial automation, this type of automation refers to the use of control systems such as computers, robots, and information technology (IT) to control various processes and equipment in an industry in order to replace humans. Industrial automation is the process of increasing the flexibility and simplification of industrial manufacturing processes with greater efficiency. With programmable automation systems, it is possible to make changes to a product or process by changing the control program. Reprogramming equipment in flexible automation takes place offline; that is, programming is done on a computer terminal without using the production equipment itself.
With flexible automation, the range of products is very limited and equipment changes can be carried out very quickly and automatically. For these approaches to be successful; the variety of parts that can be produced in a flexible automated manufacturing system is often more limited than in a system controlled by programmable automation. In the case of fixed automation, the machining or assembly operations in the system are fixed by the equipment configuration, while in the case of programmable automation, the production equipment can change the sequence of operations to be able to handle different product configurations. .Flexible automation is an enhancement to programmable automation, where computerized manufacturing systems are able to change production schedules and physical configurations of machines or cells with minimal loss of production time.
In a factory, we can automate production machines and tools, material handling equipment, control equipment, and even computer systems that control production operations. At the same time, the entire production process (including production, planning and control) is automated using machine tools with numerical control, industrial robots and other types of automation tools. This automation combines CNC machines, industrial robots and other programmable Logic controllers automation equipment into one integrated system. Automation systems are computer-controlled machines that use computers to perform control operations by collecting, processing, calculating, and controlling process variables.
Robots can perform many industrial robotic tasks, including welding, material handling, assembly, palletizing, and painting. This type of automation can include technologies such as flexible handling systems, automated material handling, and automated manufacturing. The industry uses a number of automation technologies, such as numerically controlled equipment, automated industrial robots, flexible manufacturing systems, automated manufacturing, and so on. Integrated automation. Integrated automation is a complex system that automates the entire production process using computer control.
Automation is a technique that uses a wide range of automated activities and machines to increase productivity and make business easier. Examples of stationary automation systems include automated assembly machines, chemical manufacturing processes, material handling conveyor systems, paint and coating automation processes, robotic pick and place, and process lines. All automated systems are divided into fixed, programmable and flexible, but there are many other global and automation-specific applications. Flexible automation. Flexible automation systems are based on programmable systems and include CNC machining centers and industrial robots.
You might also like
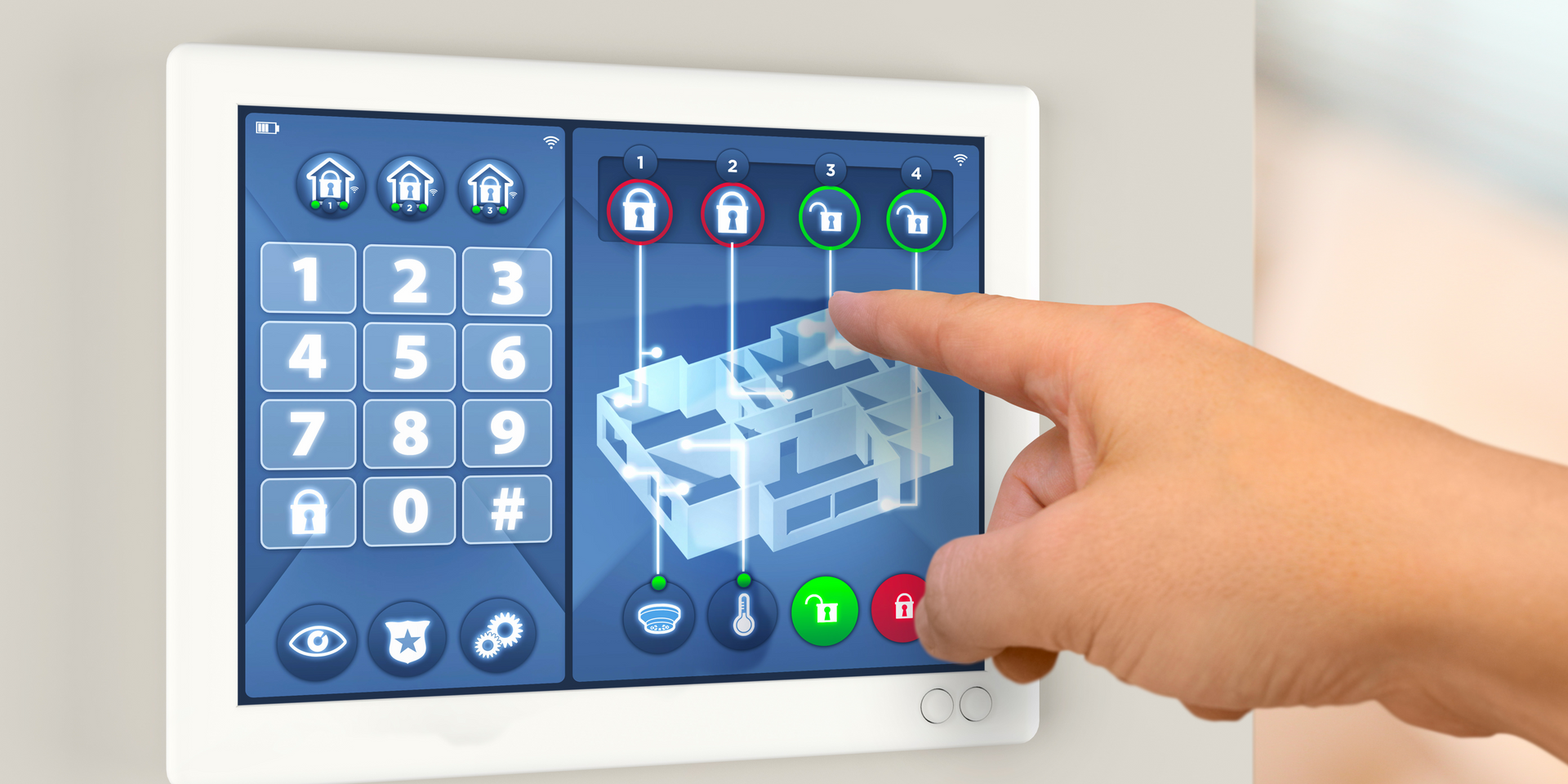
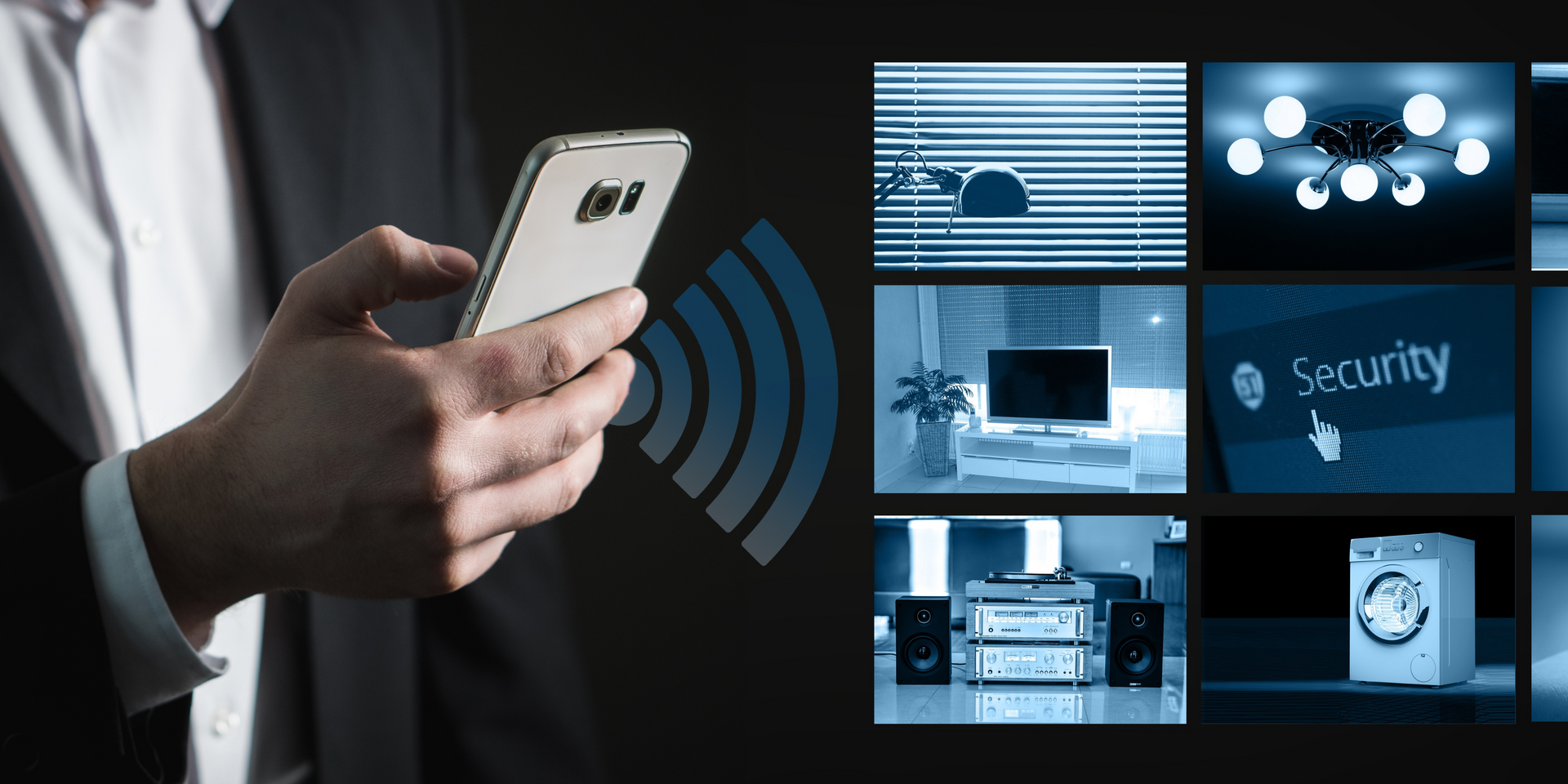
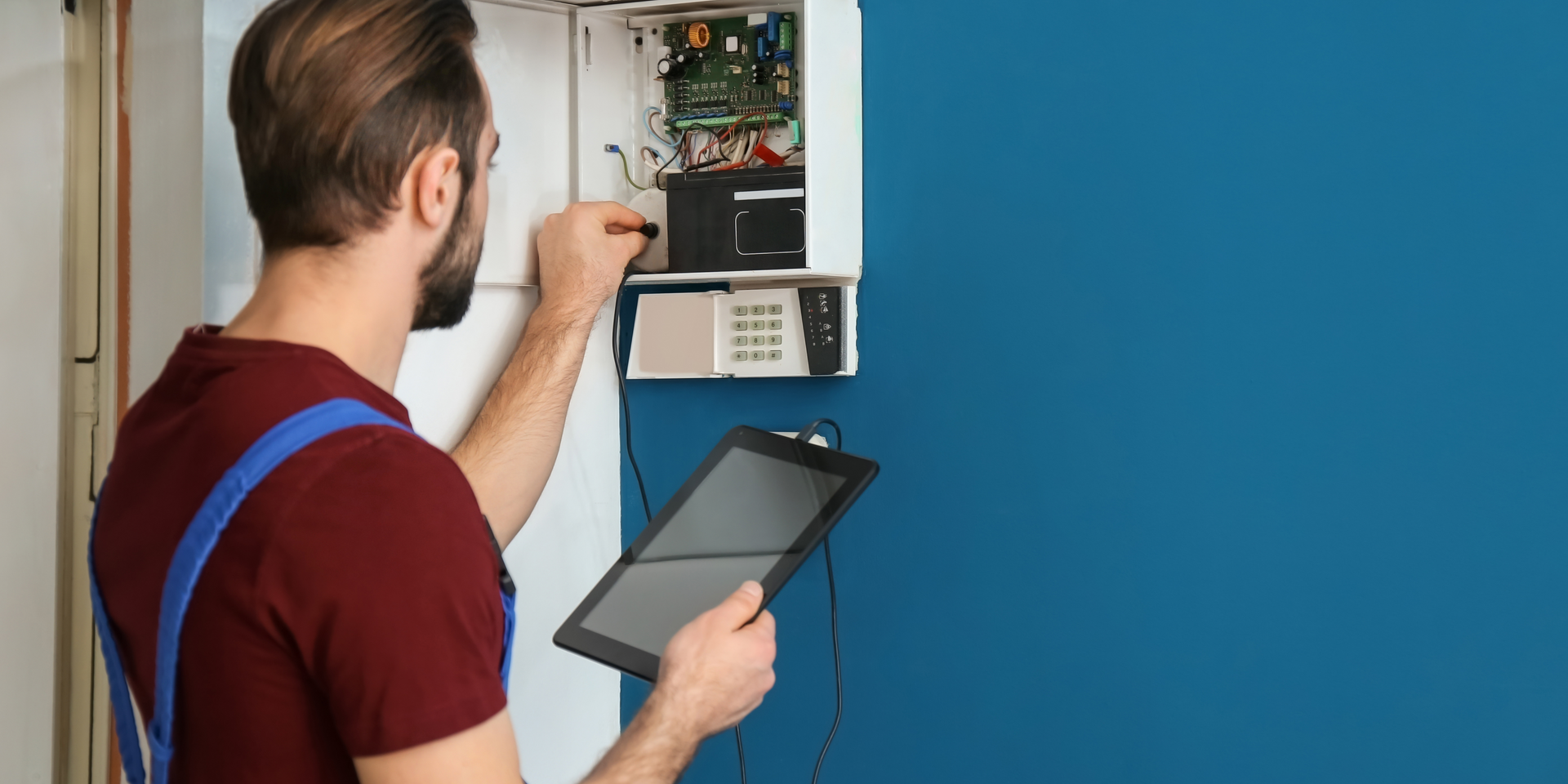