What Are the Key Elements of Industry 4.0 in Manufacturing?
What Are the Key Elements of Industry 4.0 in Manufacturing
Key elements of Industry 4.0 in manufacturing include the integration of cyber-physical systems, the Internet of Things (IoT), and cloud computing to enable smart, connected factories. This involves the use of advanced technologies such as big data analytics, artificial intelligence, and machine learning to optimize production processes, improve efficiency, and enable predictive maintenance. Additionally, Industry 4.0 emphasizes the concept of decentralized decision-making and autonomous systems, leading to greater flexibility and agility in manufacturing operations. The emerging concept of Industry 5.0 takes this a step further, focusing on the harmonious collaboration between humans and machines for a more personalized and human-centered manufacturing approach, often highlighted in Industry 5.0 PPT presentations that showcase the potential for sustainable and socially responsible processes.
Industry 4.0 Examples
- Smart Factories: Factories equipped with interconnected sensors and devices that collect real-time data on machine performance, production processes, and inventory levels. This data is analyzed using advanced analytics and machine learning algorithms to optimize production schedules, reduce downtime, and minimize waste.
- Predictive Maintenance: Implementing predictive maintenance strategies using IoT sensors and data analytics to monitor equipment conditions and predict when maintenance is needed before failures occur. This approach helps minimize unplanned downtime, extend equipment lifespan, and optimize maintenance schedules, leading to cost savings and improved efficiency.
- Digital Twins: Creating digital replicas of physical assets, such as machines, production lines, or entire factories, using IoT data, simulation models, and real-time monitoring. Digital twins enable manufacturers to visualize and simulate processes, perform "what-if" analysis, and optimize operations in a virtual environment before implementing changes in the physical world, leading to improved product quality, reduced time-to-market, and increased productivity.
Industry 4.0 Technologies Examples
- Internet of Things (IoT): IoT technology involves connecting physical devices, sensors, and machines to the internet to collect and exchange data. In manufacturing, IoT enables real-time monitoring of equipment, predictive maintenance, and remote operation and control of machines, leading to improved efficiency and productivity.
- Artificial Intelligence (AI) and Machine Learning: AI and machine learning algorithms are used to analyze large datasets generated by industrial processes, identifying patterns, trends, and anomalies to optimize production, quality control, and supply chain management. AI-powered systems can also enable predictive maintenance, autonomous decision-making, and process optimization in manufacturing operations.
- Additive Manufacturing (3D Printing): Additive manufacturing technologies, such as 3D printing, allow for the production of complex and customized parts directly from digital designs. This technology enables manufacturers to create prototypes, tooling, and end-use parts with greater flexibility, reduced lead times, and minimal material waste compared to traditional manufacturing methods, driving innovation and agility in product development and production processes.
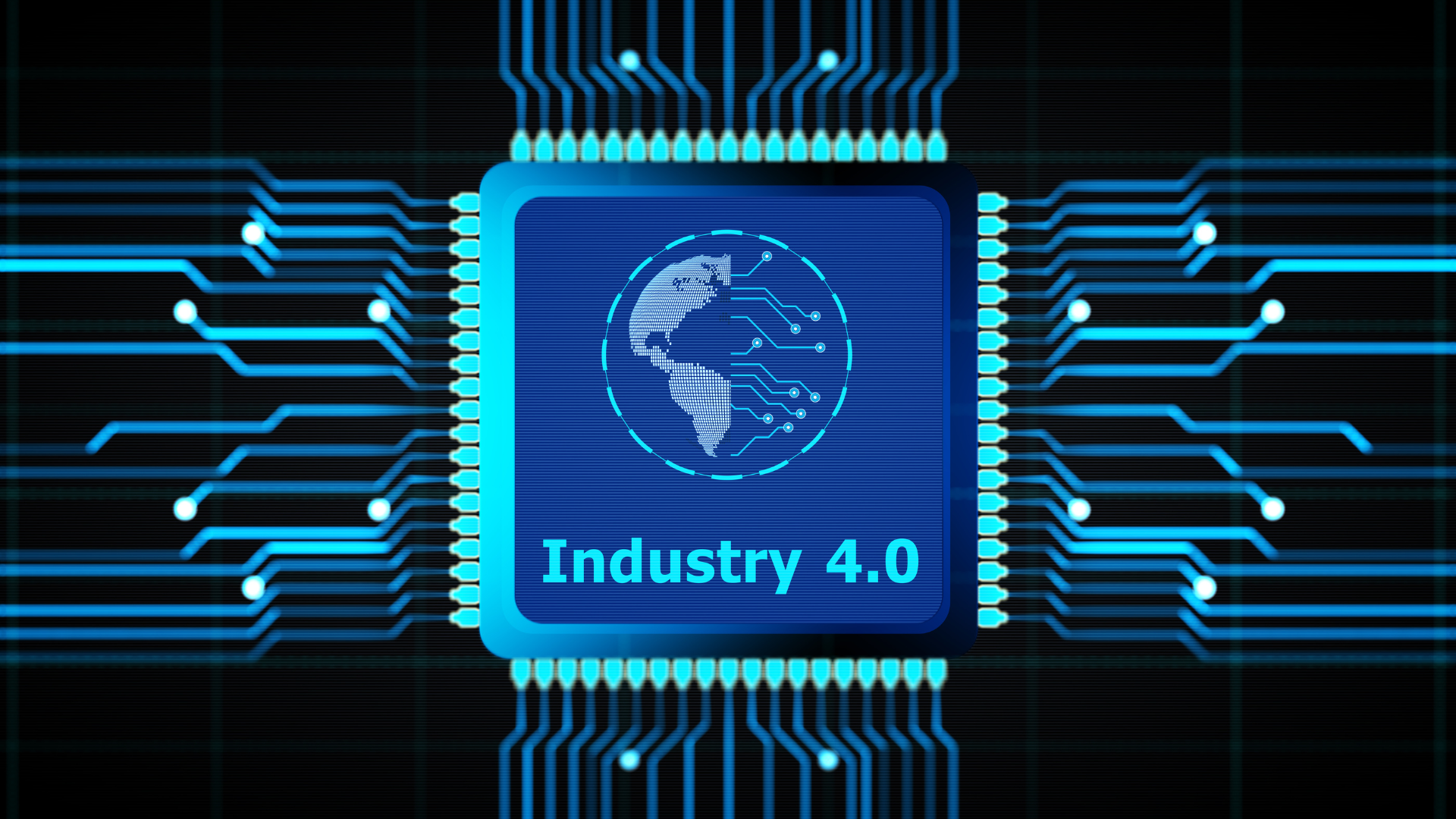
What Are the Key Points of Industry 4.0 Operations
The key points of Industry 4.0 operations encompass interconnectedness, data-driven decision-making, automation, flexibility, cybersecurity, and human-machine collaboration. This paradigm shift involves integrating cyber-physical systems, IoT devices, and advanced analytics to create interconnected production systems, enabling seamless communication and collaboration. Data analytics drives informed decision-making and process optimization, while automation and robotics streamline operations, increasing efficiency and productivity. Flexibility allows for rapid adaptation to changing market demands, with agile production systems and supply chains. Cybersecurity measures protect against cyber threats, ensuring data integrity and confidentiality. Human-machine collaboration fosters effective communication and skill development, maximizing the benefits of automation while maintaining human oversight and intervention. The concept of "Industry 5.0 PPT" emphasizes the transition from Industry 4.0 to a more human-centric approach in manufacturing, integrating human creativity and decision-making with advanced technologies to create personalized and socially responsible manufacturing processes.
Industry 4.0 operations key points includes:
- Interconnected Systems: Industry 4.0 operations involve the integration of cyber-physical systems, IoT devices, and data networks to create interconnected production systems. This allows for seamless communication and collaboration between machines, processes, and personnel.
- Data-driven Decision Making: Industry 4.0 operations rely on the collection, analysis, and utilization of vast amounts of data from sensors, machines, and production processes. Data analytics, machine learning, and artificial intelligence are used to derive insights, optimize operations, and enable predictive maintenance and quality control.
- Automation and Robotics: Industry 4.0 emphasizes the use of automation and robotics to streamline manufacturing processes, increase efficiency, and reduce labor-intensive tasks. Robots equipped with advanced sensors and AI capabilities can perform complex tasks with precision and speed, improving productivity and flexibility in production.
- Flexibility and Customization: Industry 4.0 operations prioritize flexibility and customization to meet changing market demands and individual customer requirements. This is achieved through agile production systems, digital manufacturing technologies, and modular production setups that can quickly adapt to varying production needs.
- Cybersecurity: With increased connectivity and digitalization comes the need for robust cybersecurity measures to protect sensitive data, intellectual property, and production systems from cyber threats. Industry 4.0 operations implement security protocols, encryption technologies, and access controls to safeguard critical assets and ensure data integrity and confidentiality.
What Are the Key Aspects of the Industry 4.0 Workplace
The key aspects of the Industry 4.0 workplace encompass interconnectedness, digitalization, flexibility, upskilling, safety, and collaboration. This modern workplace is characterized by interconnected systems and devices, facilitating seamless communication and data exchange across various stages of production. Digitalization drives efficiency and innovation, enabling real-time monitoring, analysis, and optimization of processes. Flexibility allows for agile responses to market demands and technological advancements, with adaptable production systems and workforce skillsets. Continuous upskilling and training ensure employees can effectively utilize advanced technologies and contribute to ongoing improvements. Safety remains paramount, with stringent protocols and technologies in place to protect workers and assets. Collaboration between humans and machines fosters a harmonious work environment where automation enhances productivity while human oversight ensures quality and decision-making. Together, these aspects create a dynamic and resilient Industry 4.0 workplace poised for success in the digital era.
Industry 4.0 workplace key aspects includes:
- Digitization and Connectivity: Industry 4.0 workplaces leverage digital technologies and connectivity to create smart and interconnected environments. This includes IoT devices, sensors, and networks that enable seamless communication and data exchange between machines, systems, and personnel.
- Automation and Robotics: Automation and robotics play a significant role in Industry 4.0 workplaces, performing repetitive or dangerous tasks with speed, precision, and consistency. Robots are integrated into production processes to enhance efficiency, productivity, and safety, while humans focus on more complex or creative tasks.
- Skill Upgradation: Industry 4.0 requires a workforce with updated skills in digital technologies, data analysis, and problem-solving. Employees need to adapt to new tools and technologies, undergo training in cybersecurity, data analytics, and AI, and embrace lifelong learning to stay relevant in rapidly evolving workplaces.
- Collaboration between Humans and Machines: Industry 4.0 workplaces emphasize collaboration between humans and machines, with humans overseeing and guiding automated processes. This requires effective communication, teamwork, and trust between human operators and intelligent machines to optimize performance and productivity.
- Flexibility and Adaptability: Industry 4.0 workplaces are designed to be flexible and adaptable to changing market demands and technological advancements. Modular production systems, agile manufacturing processes, and scalable infrastructure enable rapid reconfiguration and customization to meet evolving business needs.
- Focus on Safety and Well-being: Industry 4.0 workplaces prioritize employee safety and well-being, implementing safety protocols, ergonomic designs, and predictive maintenance strategies to ensure a safe and healthy work environment. Advanced technologies such as wearable devices and AI-driven safety systems further enhance workplace safety and reduce the risk of accidents.
Overall, the Industry 4.0 workplace is characterized by the integration of digital technologies, automation, skilled workforce, collaboration, flexibility, and a strong focus on safety and well-being to drive innovation, efficiency, and competitiveness in the global market.
What Are Industry 4.0 Manufacturing Principles
Industry 4.0 manufacturing principles revolve around interconnectedness, transparency, decentralized decision-making, virtualization, modularization, and resource efficiency. They emphasize the seamless integration and communication of machines, systems, and data throughout the manufacturing process, enabling real-time monitoring, analysis, and optimization. Decentralized decision-making empowers individual machines to autonomously respond to changing conditions, while virtualization techniques enable digital representations of physical assets for simulation and optimization. Modularization allows for flexible and adaptable production systems, while resource efficiency focuses on optimizing resource utilization and minimizing waste. By embracing these principles, companies can create agile, efficient, and sustainable manufacturing operations that drive innovation and competitiveness in the Industry 4.0 era.
What Are the Industry 4.0 Standards
Industry 4.0 standards encompass a set of guidelines and protocols that facilitate interoperability, security, and compatibility among digital technologies and systems in manufacturing. These standards cover various aspects such as communication protocols, data formats, cybersecurity measures, and interoperability frameworks to ensure seamless integration and communication between different components and stages of the manufacturing process. Examples of Industry 4.0 standards include communication protocols like OPC UA (Open Platform Communications Unified Architecture) and MQTT (Message Queuing Telemetry Transport), data exchange formats like JSON (JavaScript Object Notation) and XML (eXtensible Markup Language), and cybersecurity standards like IEC 62443. These standards provide a common language and framework for manufacturers to implement Industry 4.0 technologies effectively, enabling them to reap the benefits of increased efficiency, flexibility, and innovation while ensuring the security and integrity of their digital infrastructure.
What Is Industry 4.0 Meaning
Industry 4.0, often referred to as the fourth industrial revolution, signifies the integration of digital technologies into manufacturing processes to create smart, interconnected, and automated systems. This paradigm shift involves the convergence of cyber-physical systems, the Internet of Things (IoT), cloud computing, and artificial intelligence to optimize production efficiency, quality, and flexibility. Industry 4.0 encompasses concepts such as smart factories, predictive maintenance, autonomous robots, and data-driven decision-making, transforming traditional manufacturing operations into agile, responsive, and interconnected ecosystems. By leveraging advanced technologies and real-time data analytics, Industry 4.0 enables manufacturers to achieve greater productivity, customization, and innovation while driving sustainable growth and competitiveness in the global marketplace.
Industry 4.0 Technologies Meaning
Industry 4.0 technologies refer to a suite of advanced digital tools and systems that are revolutionizing manufacturing processes and operations in the fourth industrial revolution. These technologies include, but are not limited to, the Internet of Things (IoT), artificial intelligence (AI), big data analytics, cloud computing, additive manufacturing (3D printing), robotics, augmented reality (AR), and virtual reality (VR). By integrating these technologies into manufacturing environments, companies can create smart factories and supply chains that are interconnected, automated, and highly efficient. Industry 4.0 technologies enable real-time monitoring and control of production processes, predictive maintenance, agile production methods, customization of products, and data-driven decision-making, leading to increased productivity, reduced costs, improved quality, and enhanced competitiveness.
Industry 4.0 Technologies PDF
Industry 4.0, also termed the Fourth Industrial Revolution in manufacturing, presents an innovative paradigm reshaping the manufacturing landscape by incorporating advanced technologies into diverse processes. This progressive approach leverages automation, artificial intelligence, the Internet of Things (IoT), and other state-of-the-art tools to establish a highly efficient and interconnected environment. Embracing Industry 4.0 empowers manufacturers to optimize production processes, elevate product quality, curtail expenses, and enhance overall productivity. The seamless integration of these advanced technologies facilitates real-time data analysis and decision-making, predictive maintenance tactics, intelligent inventory management systems, and adaptable production techniques. Consequently, businesses can attain a competitive advantage in today's dynamic business realm while fostering sustainable growth prospects for the future, signifying a transition towards automated, data-driven, and intelligent systems promoting heightened efficiency and productivity across the industrial domain.
What Is Industry 4.0 in Simple Terms
Industry 4.0 is a term used to describe the latest stage in the evolution of how things are made. It's all about using new technology, like computers, robots, and data, to make factories smarter and more efficient. Imagine machines that can talk to each other and learn from each other, or products that can tell you when they need fixing before they break. Industry 4.0 is like taking everything we know about making things and making it even better by using technology in clever ways.
What Are the Key Elements of Industry 4.0 in Manufacturing
The key elements of Industry 4.0 in manufacturing, along with the evolving concepts of Industry 5.0 PPT, encompass interconnectedness, data-driven decision-making, automation, flexibility, cybersecurity, and human-machine collaboration. Industry 4.0 integrates cyber-physical systems, IoT devices, and advanced analytics to create interconnected production systems, enabling seamless communication and collaboration. Data analytics drives informed decision-making and process optimization, while automation and robotics streamline operations, increasing efficiency and productivity. Flexibility allows for rapid adaptation to changing market demands, with agile production systems and supply chains. Cybersecurity measures protect against cyber threats, ensuring data integrity and confidentiality. Human-machine collaboration fosters effective communication and skill development, maximizing the benefits of automation while maintaining human oversight and intervention. Industry 5.0 emphasizes a human-centric approach, integrating human creativity and decision-making with advanced technologies to create more personalized and sustainable manufacturing processes, driving innovation and competitiveness in the digital age.
Industry 4.0 in manufacturing key elements includes:
- Interconnected Systems: Industry 4.0 involves connecting machines, devices, and systems to create a networked environment where data can be shared and utilized across the entire production process.
- Data Analytics: Industry 4.0 relies on the collection and analysis of vast amounts of data generated by sensors and machines to gain insights into production processes, identify patterns, and optimize operations.
- Automation and Robotics: Industry 4.0 utilizes automation and robotics to streamline manufacturing processes, improve efficiency, and reduce human intervention in repetitive or dangerous tasks.
- Internet of Things (IoT): Industry 4.0 leverages IoT technologies to enable communication between physical devices and systems, allowing for remote monitoring, control, and optimization of manufacturing operations.
- Artificial Intelligence (AI) and Machine Learning: Industry 4.0 incorporates AI and machine learning algorithms to enable predictive maintenance, quality control, and decision-making based on real-time data.
- Additive Manufacturing (3D Printing): Industry 4.0 embraces additive manufacturing technologies to enable rapid prototyping, customization, and on-demand production of parts and products.
- Cybersecurity: Industry 4.0 emphasizes the importance of cybersecurity to protect manufacturing systems and data from cyber threats and ensure the integrity and confidentiality of sensitive information.
- Augmented Reality (AR) and Virtual Reality (VR): Industry 4.0 utilizes AR and VR technologies to provide immersive training, visualization, and simulation experiences for operators and maintenance personnel.
By integrating these key elements, Industry 4.0 aims to create smart, connected, and flexible manufacturing systems that can adapt to changing market demands, improve efficiency, and drive innovation.
You might also like
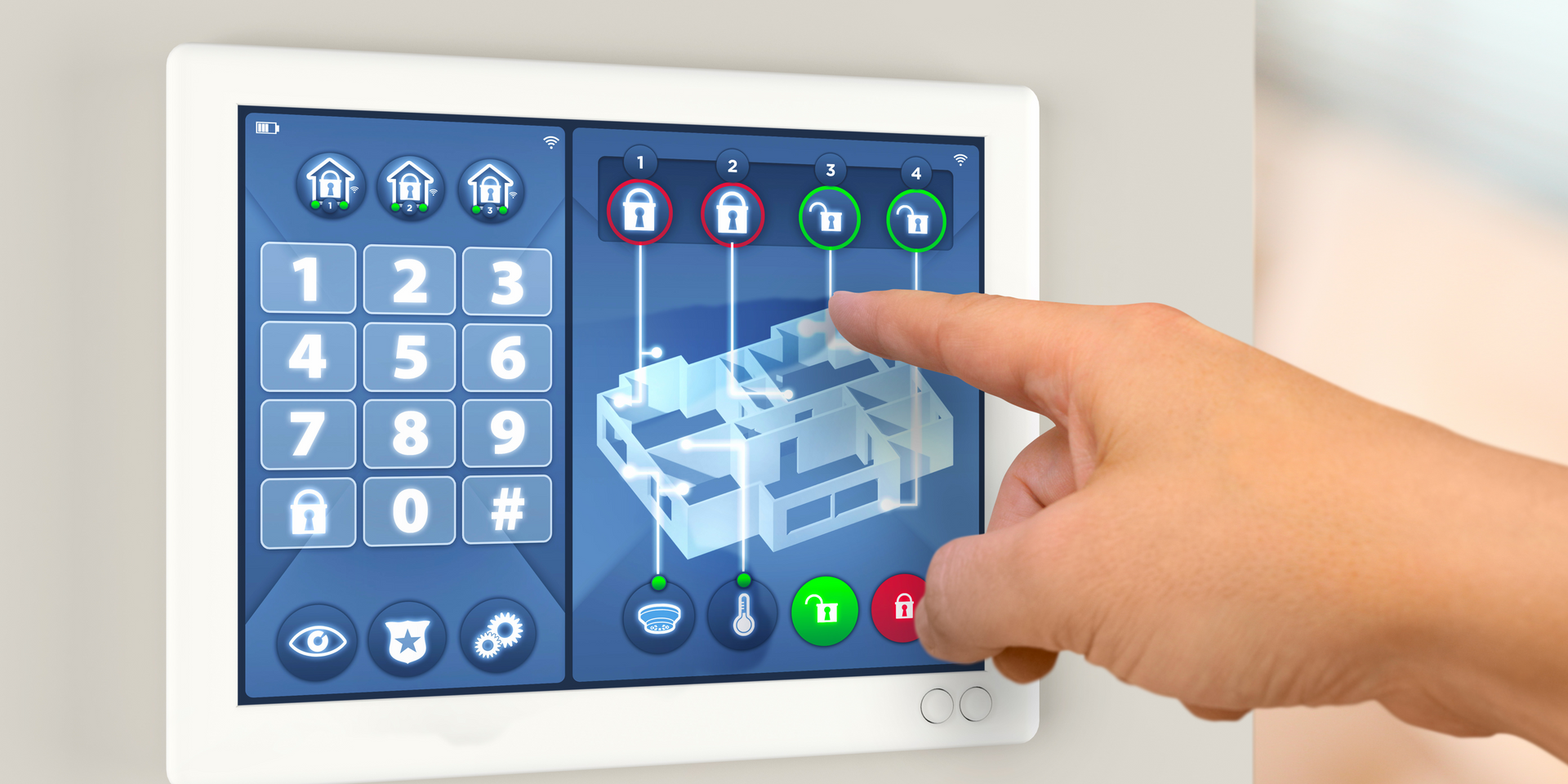
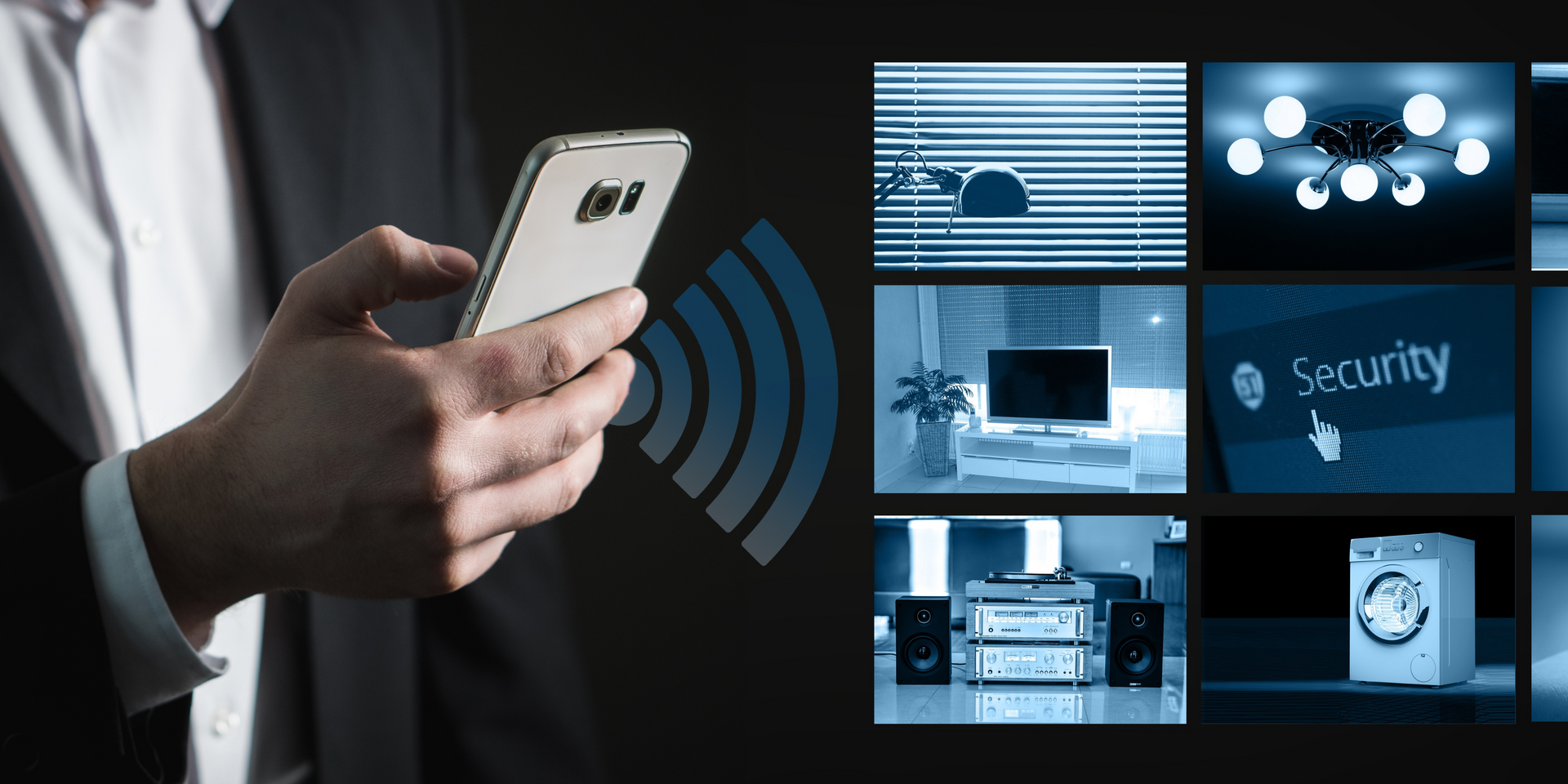
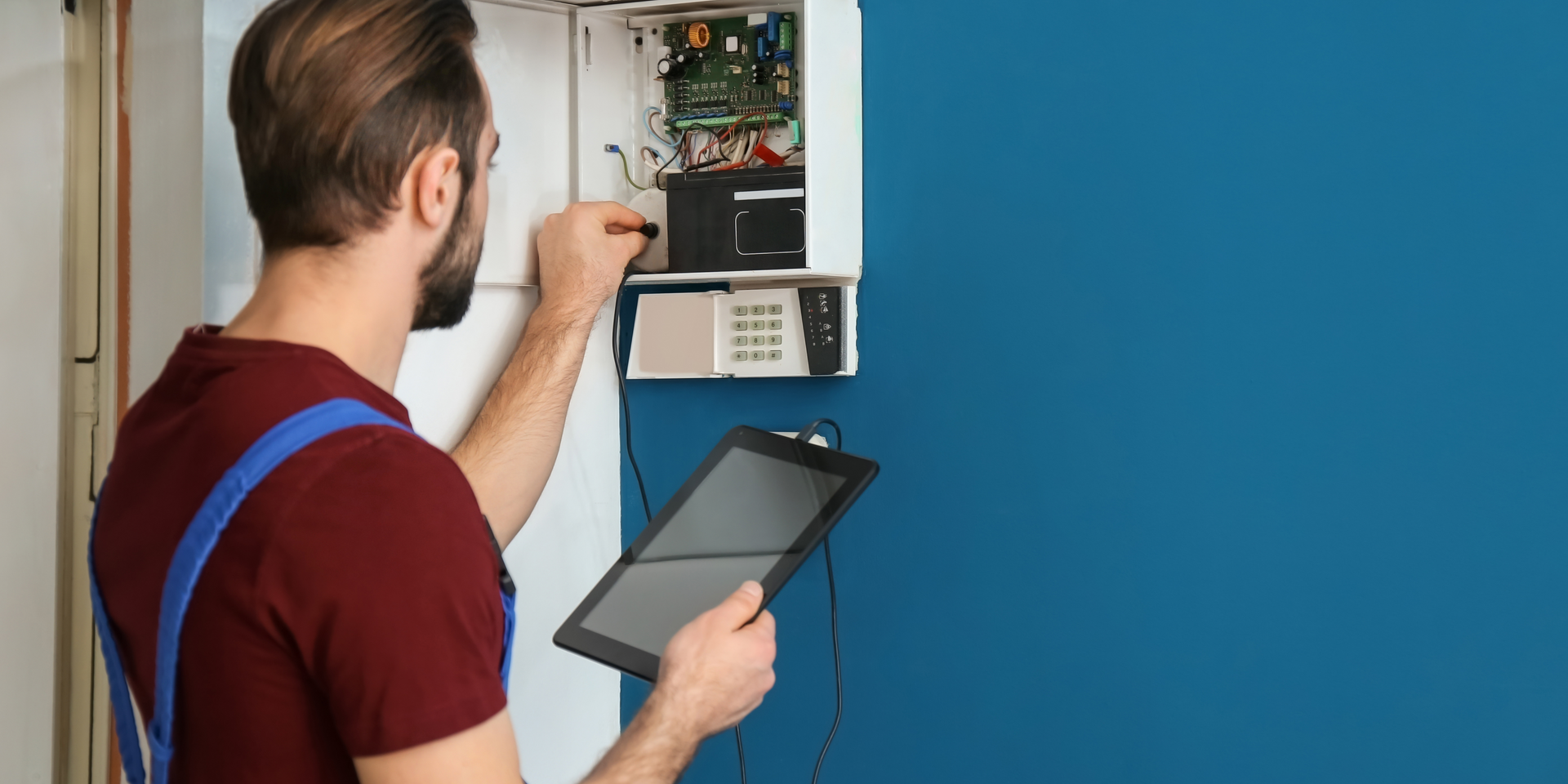