What is MES vs ERP vs SCADA?
MES (Manufacturing Execution System), ERP (Enterprise Resource Planning), and SCADA (Supervisory Control and Data Acquisition) are all critical systems in industrial operations, but they serve distinct purposes. Industrial MES focuses on real-time monitoring and control of manufacturing processes, tracking everything from raw materials to finished products to ensure efficient production. ERP systems, on the other hand, manage business-wide functions like finance, human resources, and inventory, providing a high-level view of operations. In industries such as energy and utilities, SCADA primarily controls and monitors industrial equipment and processes in real-time, providing data on machine performance and environmental conditions. While MES and SCADA deal more with production and operational control, ERP integrates business functions, offering a comprehensive view of the entire enterprise.
What is MES vs ERP vs SCADA?
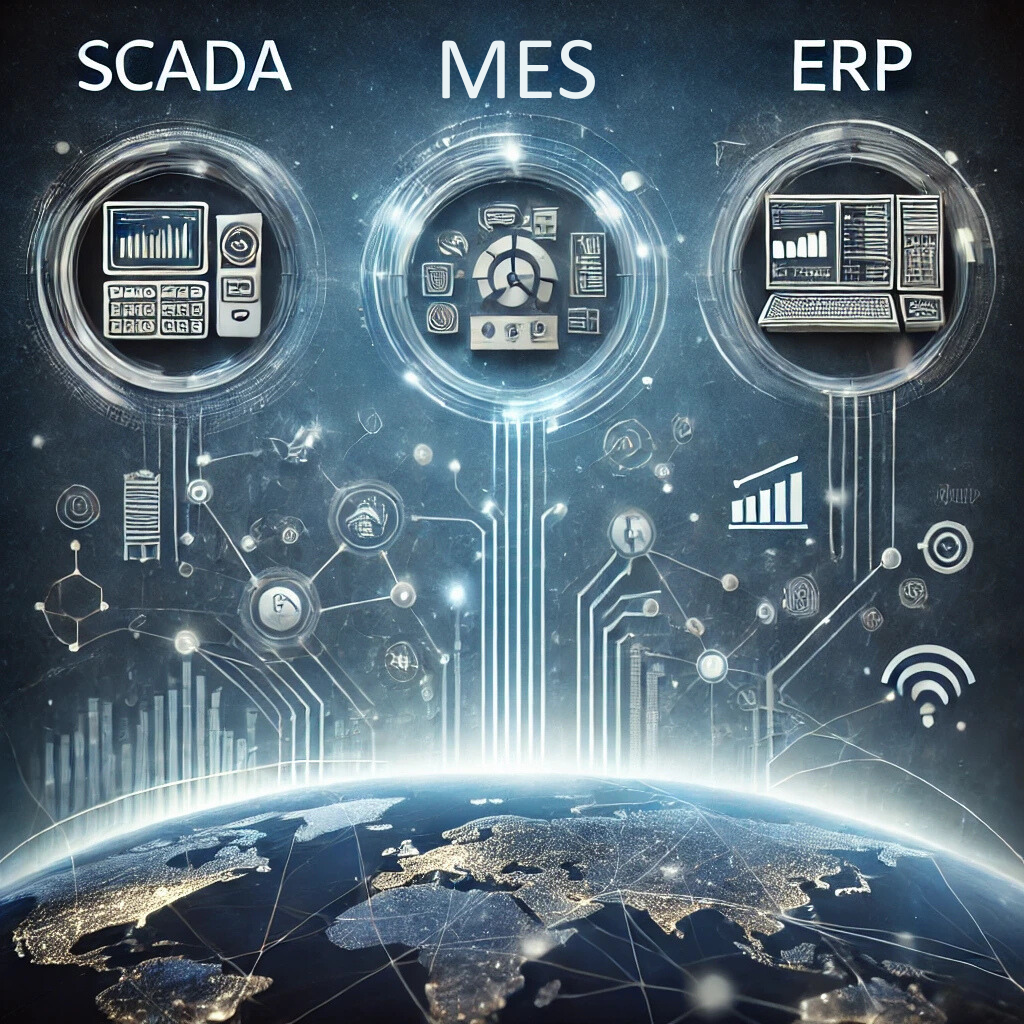
To understand MES, ERP, and SCADA, it’s important to know where these systems fit within the MES SCADA pyramid. This pyramid, also known as the automation pyramid, highlights the hierarchy and functionality of each system in a typical manufacturing environment.
- MES (Manufacturing Execution System): MES bridges the gap between business and plant-level systems. It focuses on real-time monitoring and management of manufacturing processes.
- ERP (Enterprise Resource Planning): ERP systems handle enterprise-wide data, managing everything from accounting to human resources and supply chain operations.
- SCADA (Supervisory Control and Data Acquisition): SCADA focuses on controlling and monitoring industrial equipment. It is a critical component for overseeing processes and collecting real-time data.
Understanding the interactions between SCADA vs MES vs ERP helps organizations optimize production efficiency and data flow, making these systems essential for modern manufacturing.
What is MES and SCADA?
An MES system is responsible for managing and monitoring production operations. It captures real-time data from the shop floor to optimize manufacturing performance. By integrating MES with other systems, companies can improve production planning and control, ensuring product quality and efficiency.
On the other hand, SCADA meaning refers to Supervisory Control and Data Acquisition. SCADA systems gather and analyze real-time data from industrial equipment, allowing operators to make informed decisions. While MES oversees the production process as a whole, SCADA focuses on controlling machinery and collecting data from the field. Together, these systems form a robust framework for monitoring and controlling industrial processes.
What is ERP in SCADA?
Integrating ERP with SCADA can enhance the efficiency and accuracy of data flow across an organization. SCADA MES ERP integration allows for seamless communication between the plant floor and enterprise systems. This integration ensures that real-time data collected by SCADA can be used for resource planning and management in ERP systems.
A comprehensive list of MES software includes popular options like Siemens Opcenter, Rockwell FactoryTalk, and Aveva MES. These tools help bridge the gap between operational technology and information technology, enhancing collaboration and data-driven decision-making.
What is MES and ERP Systems?
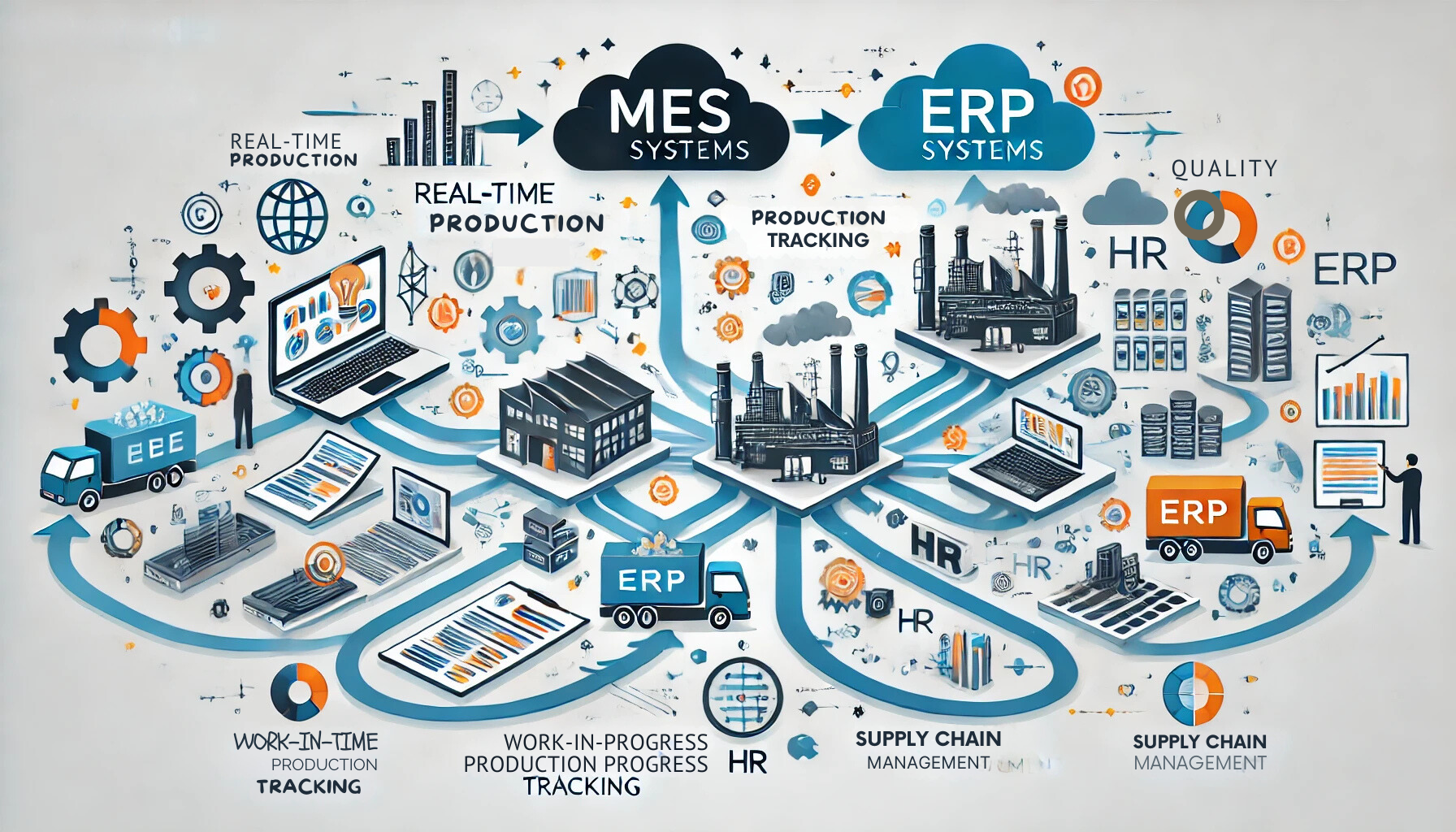
MES vs ERP often gets discussed when choosing solutions for manufacturing and business operations. While MES focuses on managing and optimizing production processes in real time, ERP deals with higher-level functions like finance, HR, and supply chain management. The integration of MES and ERP systems provides complete visibility into both manufacturing and enterprise operations, enabling businesses to be more agile and efficient.
What Does MES Stand For?
MES stands for Manufacturing Execution System. It operates at the production level, collecting and analyzing real-time data to improve manufacturing performance. This helps manufacturers manage and optimize every aspect of the production process, from scheduling to quality control. Coupled with SCADA, MES provides comprehensive monitoring and control capabilities.
The SCADA meaning, as mentioned earlier, involves monitoring and controlling industrial processes. While SCADA is more focused on data acquisition, MES adds a layer of management and execution, making it essential for end-to-end production oversight.
What is an Example of a SCADA System?
A practical example of SCADA software would be Ignition SCADA by Inductive Automation. Ignition SCADA is a popular choice for monitoring and controlling industrial operations. It provides a unified platform for real-time data collection, visualization, and analysis.
You might wonder, Is Ignition a SCADA or MES? Ignition primarily functions as a SCADA system, although it offers flexible capabilities that can be customized to work alongside MES solutions. This adaptability makes it a valuable tool for manufacturers seeking integrated automation solutions.
What Are the Three Types of SCADA?
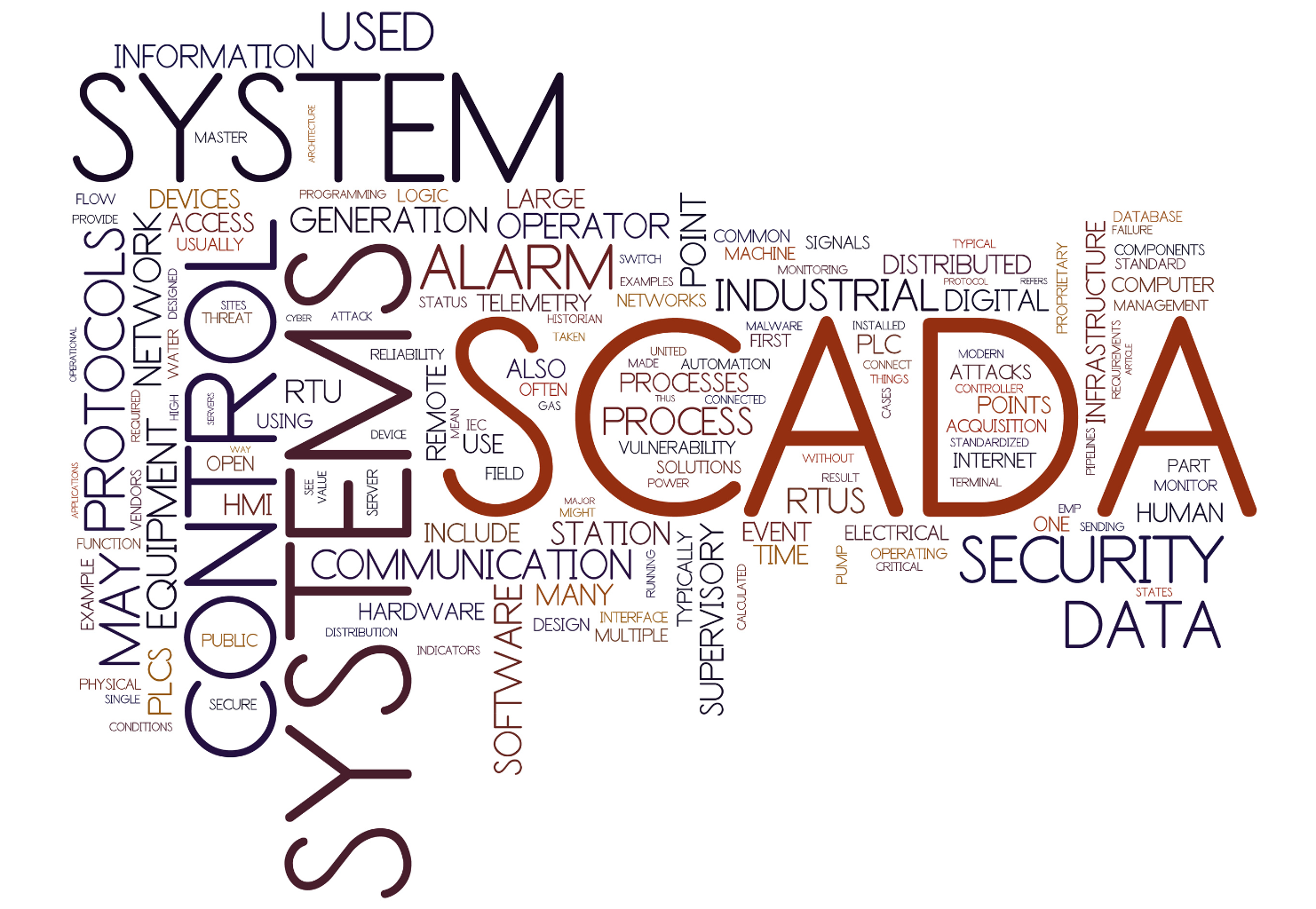
SCADA systems are categorized into three main types:
- Monolithic SCADA: These are standalone systems where data processing occurs on a single mainframe or server.
- Distributed SCADA: This type features multiple interconnected systems that share responsibilities, enhancing reliability and efficiency.
- Networked SCADA: Modern SCADA systems that leverage networked communications and cloud-based technology for real-time monitoring and control.
Each type serves different operational needs and can be tailored to suit specific industrial requirements.
Is SAP an ERP or MES?
SAP ERP is widely recognized for handling enterprise-level processes, such as finance, human resources, and supply chain management. On the other hand, SAP MES focuses on manufacturing execution, providing real-time visibility and control over production processes.
SAP offers both ERP and MES solutions, allowing businesses to streamline operations from top to bottom. Choosing between SAP ERP and SAP MES depends on an organization’s specific needs and integration goals.
What is the Difference Between MES and DCS?
When comparing MES vs DCS (Distributed Control System), it’s essential to note their distinct purposes. MES handles the execution of production activities and data management, while DCS is used for process automation and control. DCS systems are primarily employed in industries like oil and gas or chemical manufacturing to automate plant operations.
The combination of MES and DCS ensures both high-level execution and detailed control of industrial processes, creating a more efficient and responsive manufacturing environment.
What is SCADA and How It Works?
SCADA systems are essential for modern manufacturing, providing real-time monitoring and control. SCADA MES PLC integration allows data to be collected from programmable logic controllers (PLCs) and analyzed in real-time. This ensures that operators can monitor critical processes, detect issues quickly, and make data-driven decisions to improve performance.
SCADA systems work by collecting data from sensors and actuators, sending it to a central control unit, and displaying it for operators. This setup enables precise control and efficient management of industrial operations.
Conclusion
Understanding the differences and synergies between MES, ERP, and SCADA systems is vital for maximizing manufacturing efficiency. Each system has a unique role, and when integrated, they provide a comprehensive solution for both operational and enterprise needs. If you're looking to optimize your manufacturing processes, consider exploring solutions like Ignition SCADA and integrated SAP ERP/MES platforms.
For more insights and solutions tailored to your industrial needs, explore our resources or contact us for a personalized consultation.
You might also like
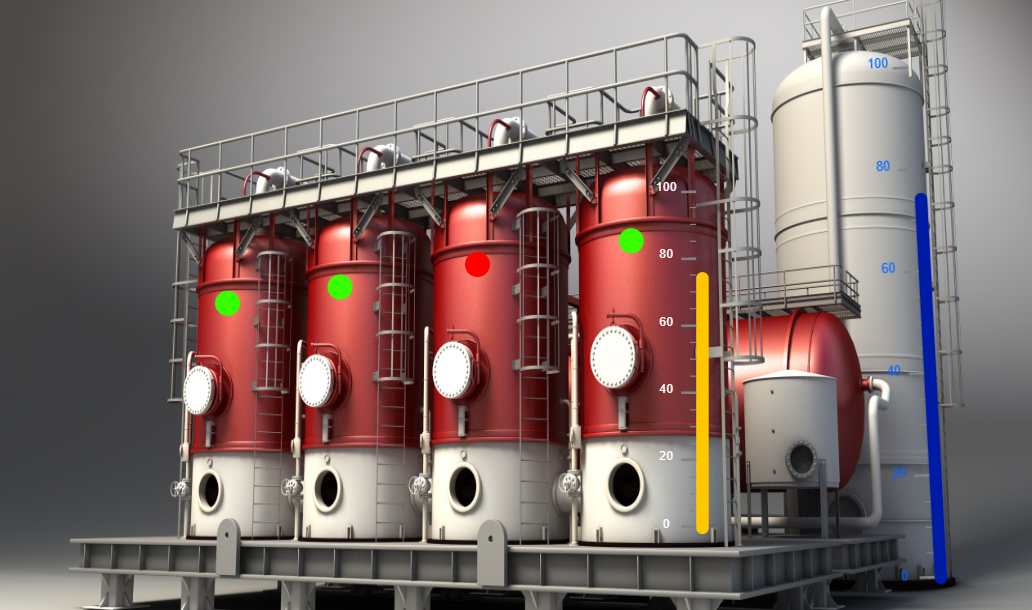
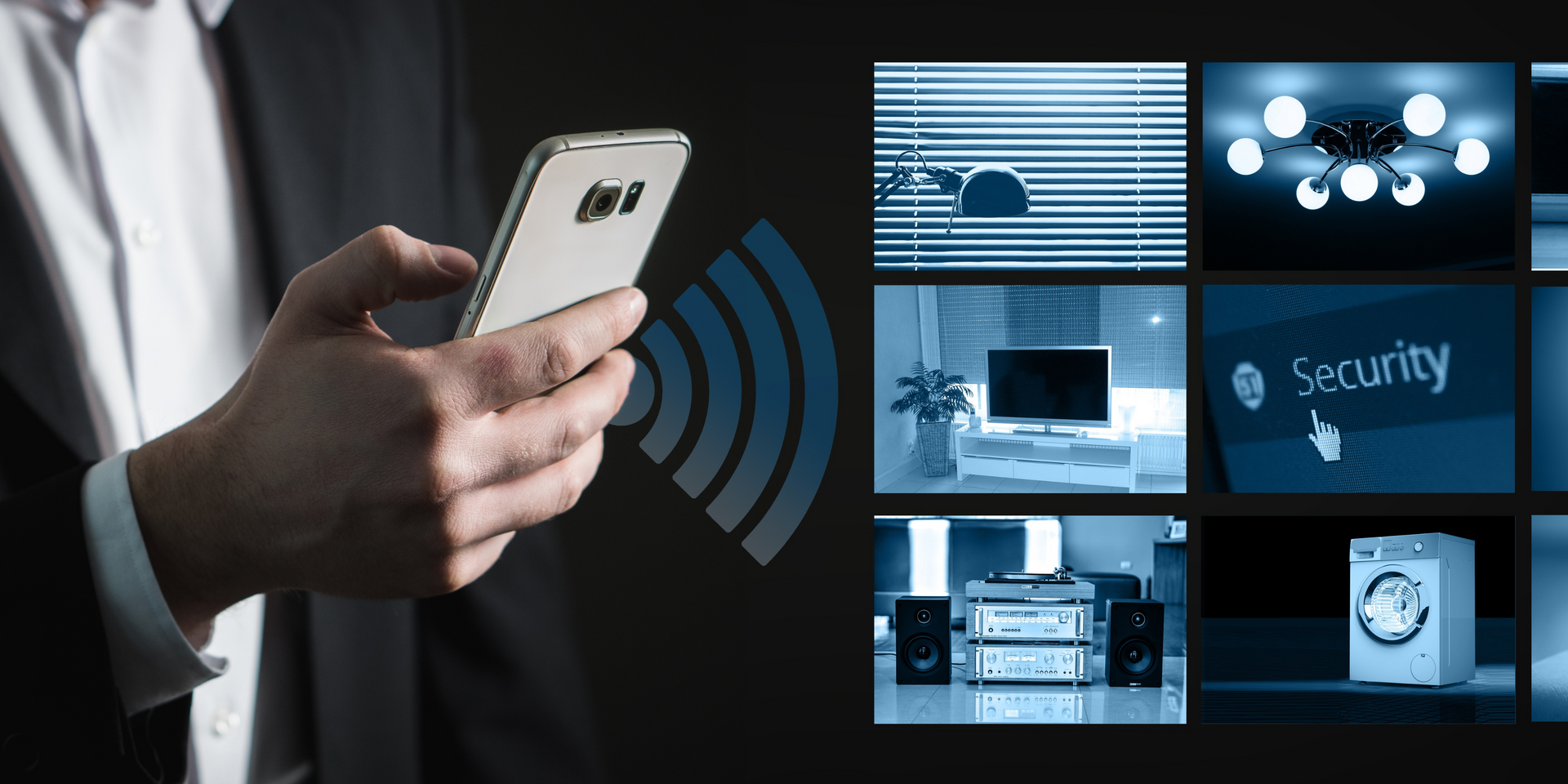
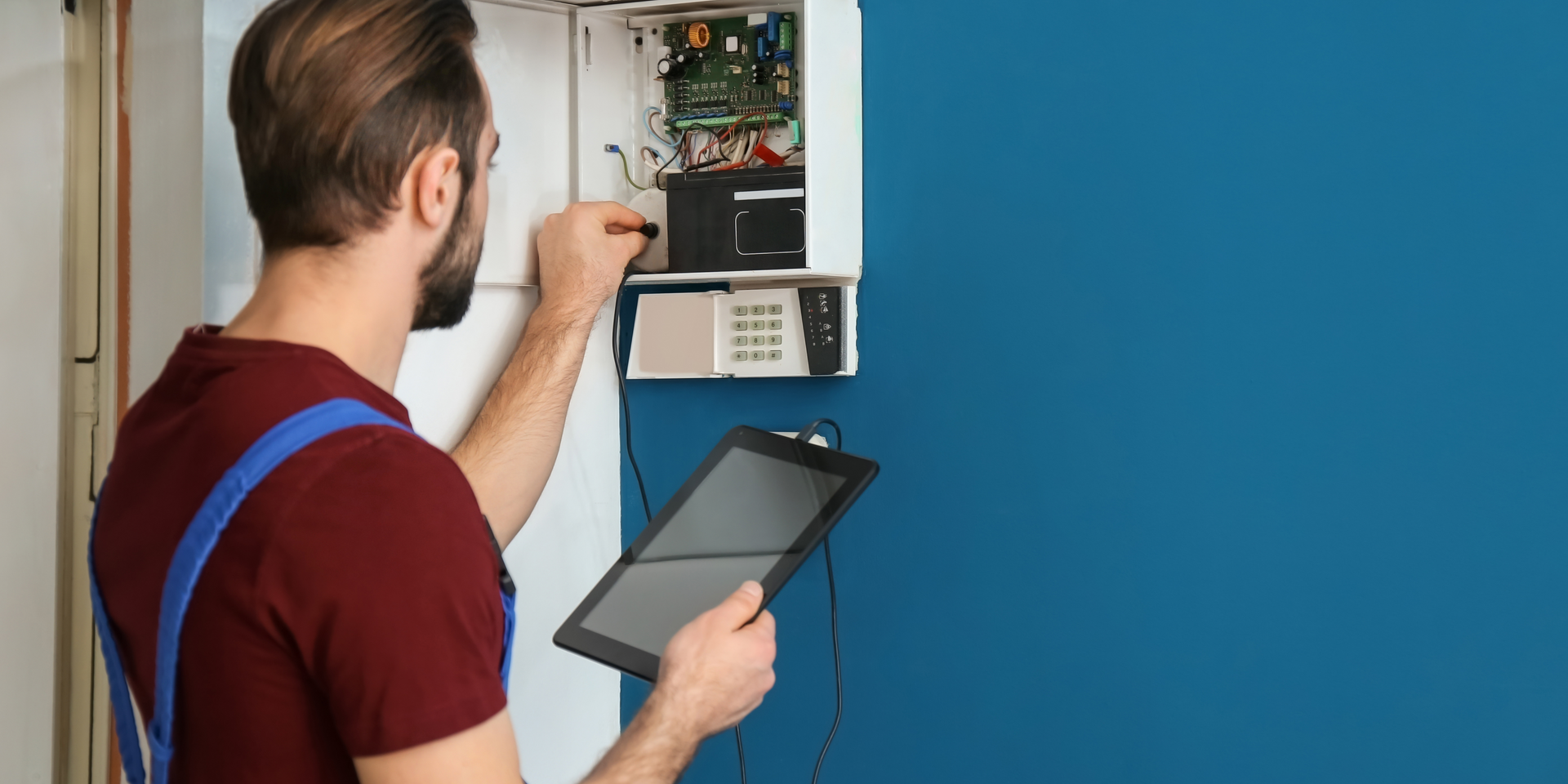