What is MES Software?
Manufacturing Execution System (MES) software is a powerful tool that bridges the gap between enterprise-level planning and shop floor operations. It helps manufacturers manage, monitor, and optimize production processes in real time. Specifically designed for industrial settings, industrial MES software offers capabilities such as tracking raw materials, work-in-progress, and finished goods, and ensures efficient meeting of production schedules. By providing detailed insights into production performance, MES systems help improve product quality, reduce downtime, and optimize overall efficiency in industries such as automotive, electronics, and pharmaceuticals.
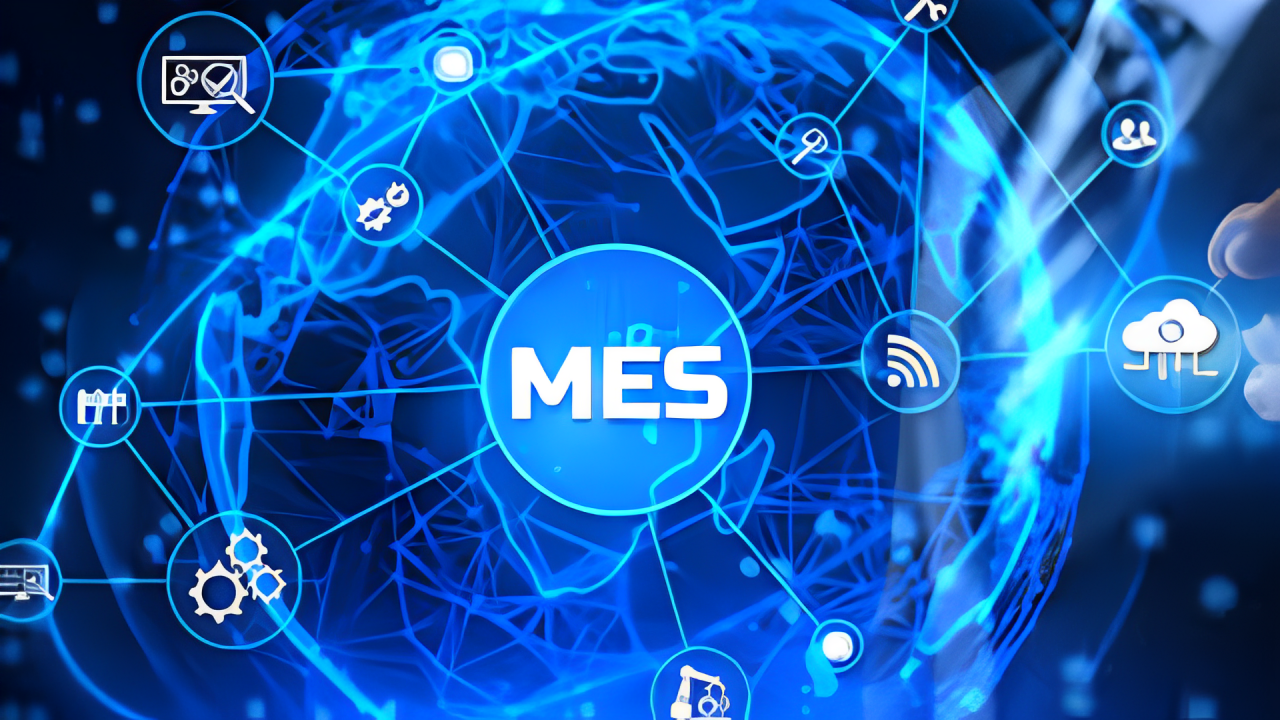
What is MES software used for?
MES software, or Manufacturing Execution System software, plays a crucial role in the manufacturing sector by streamlining and controlling production processes. It provides real-time monitoring and data collection, helping manufacturers optimize operations, maintain product quality, and minimize downtime.
Popular options for MES software include Rockwell Automation's FactoryTalk, which offers robust data visibility and operational control; Siemens' SIMATIC IT, known for its integration with automation technologies; and Honeywell's POMSnet, which excels in regulatory compliance and quality management. These tools are vital for enhancing manufacturing efficiency and productivity.
What is an example of MES?
An example of MES (Manufacturing Execution System) software is Rockwell Automation's FactoryTalk. It is designed to monitor and synchronize manufacturing operations, from the production floor to enterprise-level decision-making. Other examples include Siemens' SIMATIC IT, which integrates seamlessly with industrial automation systems, and Honeywell's POMSnet, which is particularly strong in ensuring compliance and quality control in regulated industries. These systems help streamline production processes, improve efficiency, and maintain product quality across various manufacturing environments.
What is the difference between MES and ERP?
MES (manufacturing execution system) and ERP (enterprise resource planning) systems are both crucial in modern business operations but serve different functions. MES focuses on the real-time monitoring and control of manufacturing processes on the production floor, optimizing efficiency and productivity, and ensuring quality and compliance. It handles everything from the ordering of materials to the final steps of production. On the other hand, ERP systems manage broader business processes across an organization, integrating areas such as finance, human resources, sales, and supply chain management. ERP provides a centralized platform to streamline information and processes across various departments, facilitating better planning, resource allocation, and decision-making. Essentially, while MES manages the production line, ERP oversees the entire operation from a higher level.
dv
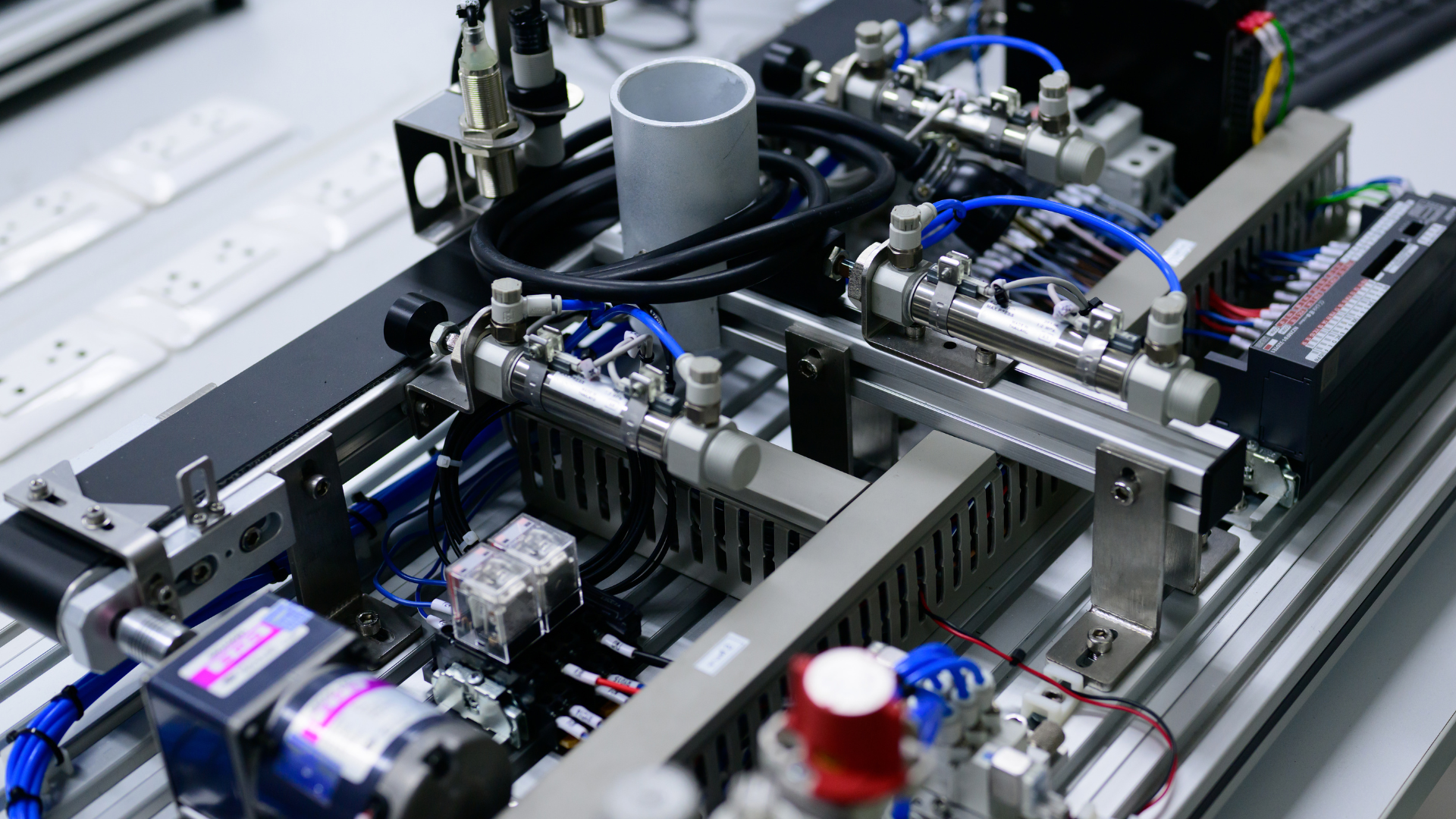
What is the difference between MES and SAP?
MES (Manufacturing Execution System) and SAP, commonly linked with its ERP (Enterprise Resource Planning) solutions, address distinct facets of business operations. Manufacturing settings specifically design MES to manage and optimize the production process. It focuses on real-time monitoring, control of the shop floor, and ensuring efficient execution of the manufacturing operations, from tracking raw materials to finished goods.
SAP, on the other hand, offers a range of software products, including ERP systems, which provide a comprehensive suite for managing an entire organization’s operations and resources. SAP ERP systems integrate core business processes such as finance, HR, supply chain, and customer relations management across the organization, aiming for overall efficiency and data consistency across departments. While MES deals with the manufacturing specifics, SAP's ERP solutions manage broader enterprise functions, supporting strategic planning and resource management at a higher level.
What is MES software?
MES (Manufacturing Execution System) software is a technology solution that manages, monitors, and controls complex manufacturing systems and data flows on the factory floor. The primary goal of MES is to ensure effective execution of manufacturing operations and improve production output. It bridges the gap between plant-level operations and a company’s enterprise systems, providing real-time data about production activities. This allows manufacturers to optimize production processes, enhance efficiency, maintain quality control, reduce downtime, and manage inventory effectively.
Who uses MES software?
Manufacturing companies across various industries primarily use MES software to improve their production efficiency and operational visibility. Key users include:
- Plant Managers: They rely on MES to get real-time data about the production process, helping them make informed decisions to optimize productivity.
- Quality managers use MES to ensure products meet quality standards by tracking compliance and monitoring production anomalies.
- Maintenance Teams: MES helps them schedule maintenance tasks based on real-time production data, reducing downtime and increasing machine availability.
- Operators on the Manufacturing Floor: MES provides them with up-to-date work instructions, production schedules, and safety guidelines.
Industries that typically use MES include automotive, pharmaceuticals, electronics, food and beverage, and aerospace, where maintaining high efficiency, compliance, and quality are critical.
What does MES stand for in software?
In software, MES stands for Manufacturing Execution System. This type of system is designed to monitor, control, and optimize production processes in manufacturing environments.
What is MES vs ERP vs SCADA?
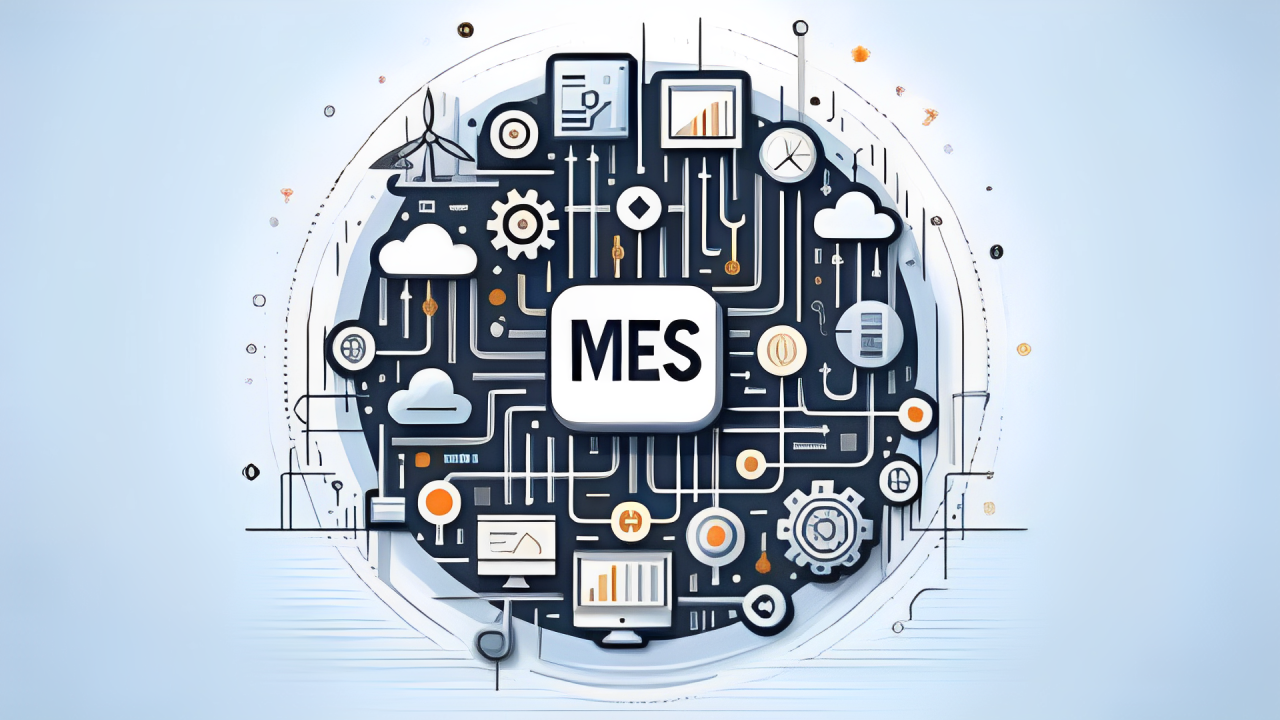
MES (Manufacturing Execution System), ERP (Enterprise Resource Planning), and SCADA (Supervisory Control and Data Acquisition) are critical systems utilized in industrial operations, each serving distinct purposes and operating at different organizational levels.
- MES (Manufacturing Execution System): This system focuses on the actual production process in a manufacturing setting. MES tracks and documents the transformation of raw materials to finished goods, providing real-time data and control over the production floor. It helps optimize manufacturing operations, manage production schedules, maintain product quality, and integrate with equipment and labor on the shop floor.
- ERP (Enterprise Resource Planning): ERP systems manage the broader business processes across an entire organization. They integrate various functions like finance, HR, sales, supply chain management, and more into a single system to streamline processes and data across the enterprise. ERP systems help with resource planning, financial forecasting, and overall strategic management, operating at a higher level than MES.
- SCADA (Supervisory Control and Data Acquisition): SCADA systems primarily monitor and control industrial processes remotely, usually at the infrastructure level, including water treatment facilities, power generation, and oil and gas pipelines. SCADA systems collect real-time data from sensors and equipment located at various points of a process and provide centralized monitoring and control.
Unlike MES, which integrates deeply into manufacturing processes, SCADA primarily focuses on overseeing and adjusting process controls across large distances and multiple locations.
Each system plays a distinct role in industrial and manufacturing operations, with MES focusing on the production line, ERP overseeing broader business functions, and SCADA managing remote monitoring and process control.
Conclusion
MES (Manufacturing Execution System) software plays a crucial role in modern manufacturing, enhancing production efficiency and ensuring high-quality outputs through real-time monitoring and control of manufacturing processes. Leading providers such as Siemens, Rockwell Automation, and SAP offer sophisticated MES solutions that integrate seamlessly with broader ERP systems, supporting comprehensive business strategies. SAP, known for its robust MES capabilities, serves as an example of how such software can synchronize with enterprise-level functionalities to optimize overall operations. For manufacturers looking to adopt or upgrade their MES systems, resources like Manufacturing Execution System PPTs can provide valuable insights, helping to navigate the selection process among various reputable MES software vendors effectively.
Contact us today to learn how MES software can optimize your manufacturing operations and transform your production processes!
You might also like
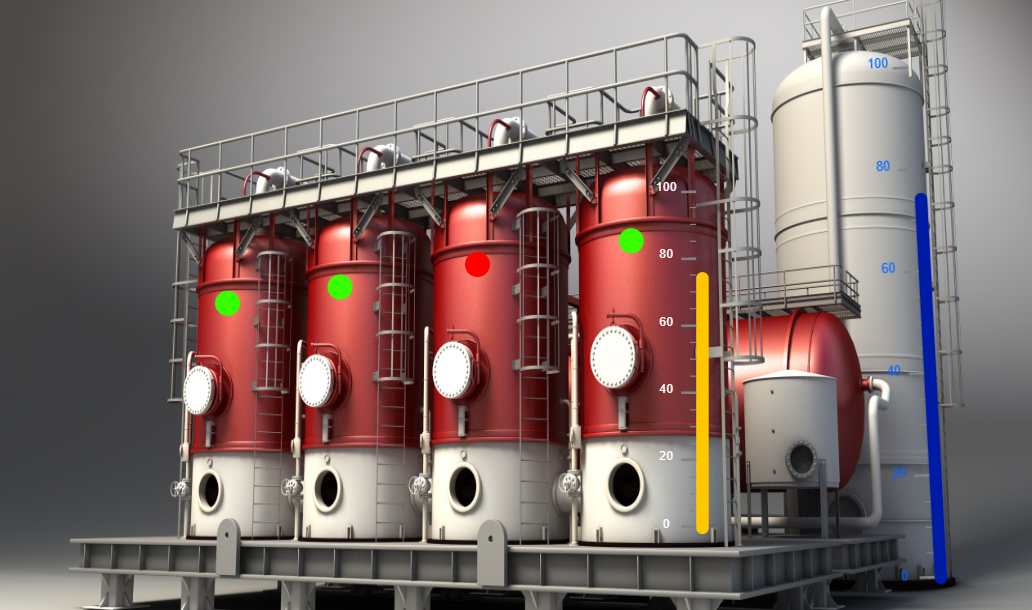
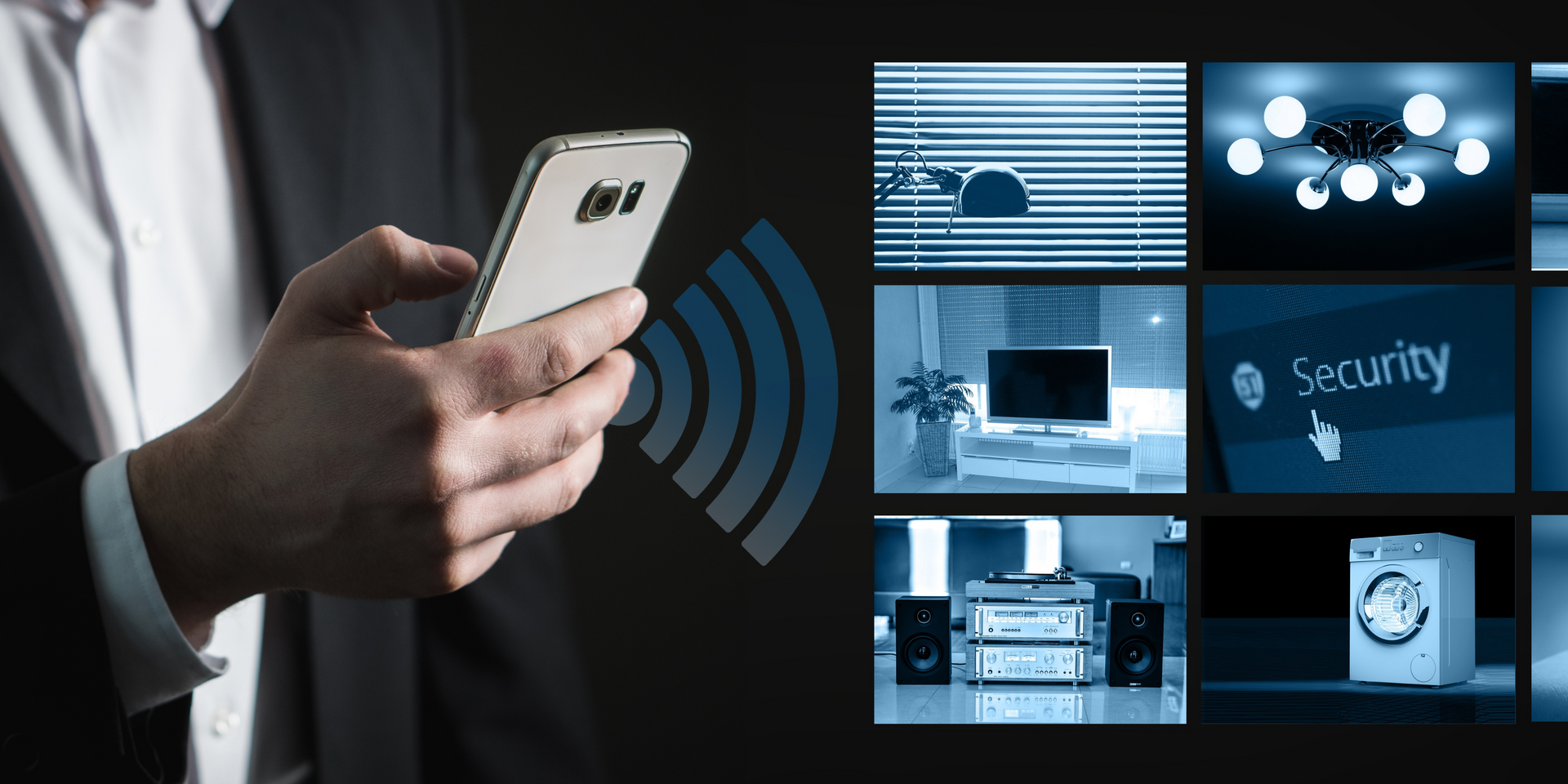
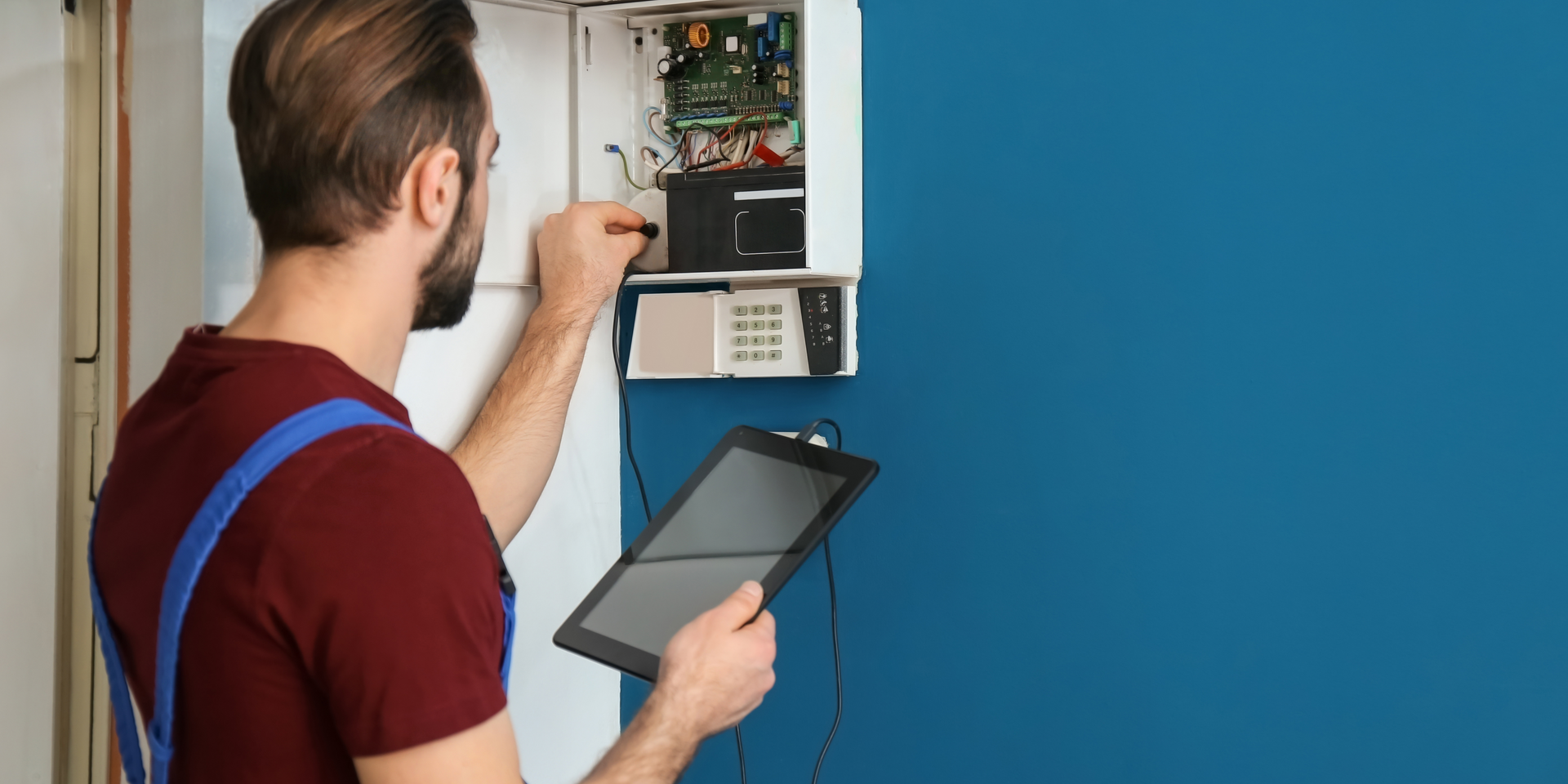