What is the difference between MES and ERP?
What is the difference between MES and ERP?
The primary difference between MES (Manufacturing Execution System) and ERP (Enterprise Resource Planning) lies in their scope and functionality. ERP systems focus on managing and integrating business processes such as finance, HR, and the supply chain, providing an overview of the entire organization. Specifically designed to monitor and control production processes in real time, industrial MES software tracks everything from raw materials to finished goods. While ERP systems handle higher-level tasks, MES offers detailed insights into day-to-day operations on the shop floor, helping optimize production efficiency and product quality. Together, they complement each other, with MES focusing on production-level data and ERP managing broader business functions.
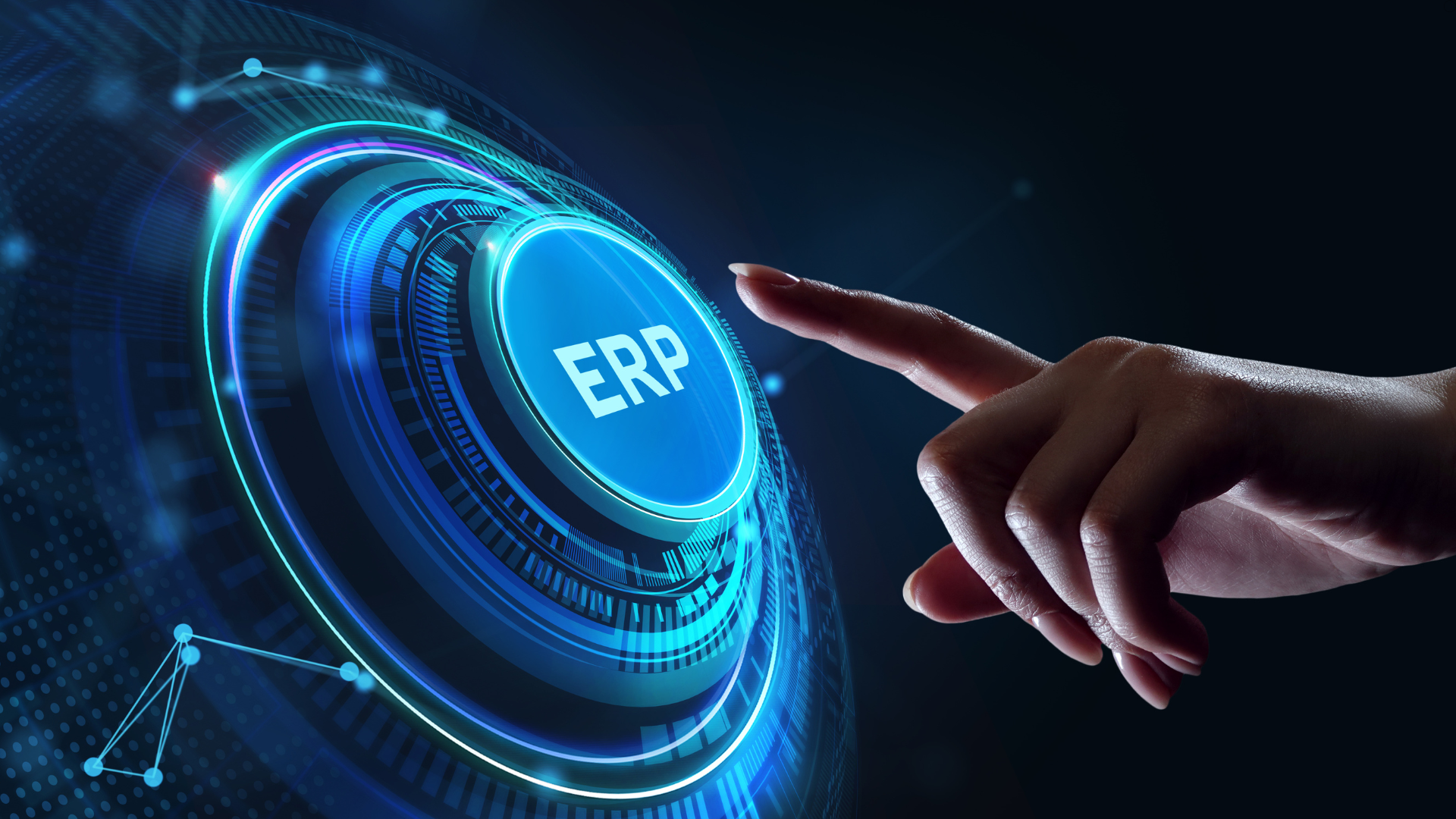
What is the difference between MES and SAP?
Both MES (Manufacturing Execution System) and SAP, commonly referred to as ERP software from SAP SE, are essential tools in industrial operations, albeit with distinct functions. MES specifically targets the shop floor level, managing and optimizing the real-time production processes in manufacturing. It provides detailed insights into machine operations, production rates, and quality control, aiming to improve manufacturing efficiency and effectiveness. On the other hand, SAP, as an ERP (enterprise resource planning) solution, offers a broader suite of business applications. It integrates various business processes across the organization, from finance and human resources to supply chain management, providing a unified view to help plan, manage, and analyze business operations more comprehensively. Essentially, MES works at the production level, while SAP aims to integrate and manage all business processes at a higher level.
What is the difference between MES and ERP?
The primary difference between MES (manufacturing execution system) and ERP (enterprise resource planning) lies in their operational focus and scope. MES systems specifically aim to manage and optimize production floor activities in real-time, thereby enhancing the efficiency and effectiveness of manufacturing operations. In contrast, ERP systems provide a broader, integrated management solution that oversees a range of business processes across the entire organization, from financials and HR to supply chain management, aiming to streamline operations and enhance decision-making across various departments.
What is the interaction between MES and ERP?
The interaction between MES (Manufacturing Execution System) and ERP (Enterprise Resource Planning) is crucial for streamlined operations in manufacturing businesses. MES manages detailed, real-time data at the shop floor level, including production scheduling, quality control, and machine efficiency. The ERP system then receives this data and integrates it with broader organizational functions like finance, procurement, and human resources. This integration allows for a more comprehensive overview of both production and business operations, facilitating better strategic planning and resource allocation. Essentially, the MES ensures production efficiency, while the ERP system helps optimize the overall business performance by using the insights provided by the MES.
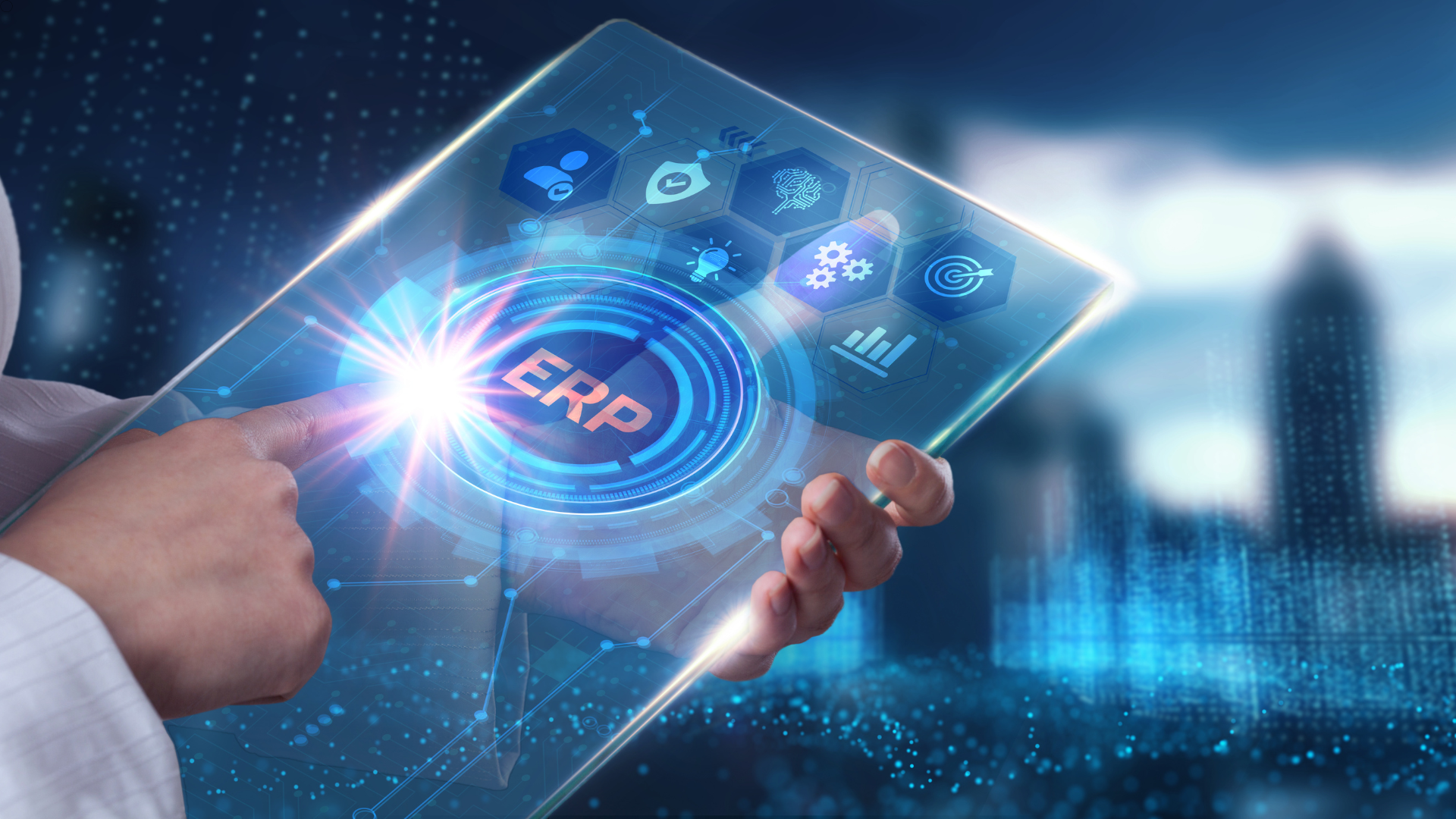
What is the difference between ERP and Professional Services Automation?
ERP (Enterprise Resource Planning) systems, when integrated with MES (Manufacturing Execution Systems), enhance manufacturing operations by linking shop floor data with wider business processes like finance and supply chain management. This integration allows seamless information flow, improving decision-making and operational efficiency across the enterprise.
Professional Services Automation (PSA) software, on the other hand, caters to service industries like consulting and IT services, emphasizing project management, resource allocation, and billing. PSA optimizes project delivery and resource use, ensuring projects meet budgets and deadlines, which is critical for client satisfaction and profitability.
What does ERP stand for in manufacturing?
In the manufacturing sector,
ERP stands for
"Enterprise Resource Planning." Manufacturers use ERP systems, integrated software platforms, to manage and automate various business processes across their organization. This includes everything from supply chain management and procurement to production planning, finance, and human resources. By centralizing data from these diverse functions, ERP systems enable manufacturers to improve operational efficiency, enhance data visibility, and make better-informed decisions.
What is MES vs ERP vs Scada?
MES (Manufacturing Execution System), ERP (Enterprise Resource Planning), and SCADA (Supervisory Control and Data Acquisition) each serve distinct roles in manufacturing. MES focuses on managing and optimizing real-time production activities, providing insights into machine performance, quality, and scheduling to ensure efficient manufacturing processes.
ERP systems, on the other hand, manage broader business functions like finance, HR, and supply chain, integrating data across the organization to streamline operations. Meanwhile, SCADA ensures the safe and effective operation of industrial equipment and processes by providing real-time monitoring and control, often at the hardware level. Together, these systems can provide a comprehensive solution for both operational and business management in manufacturing environments.
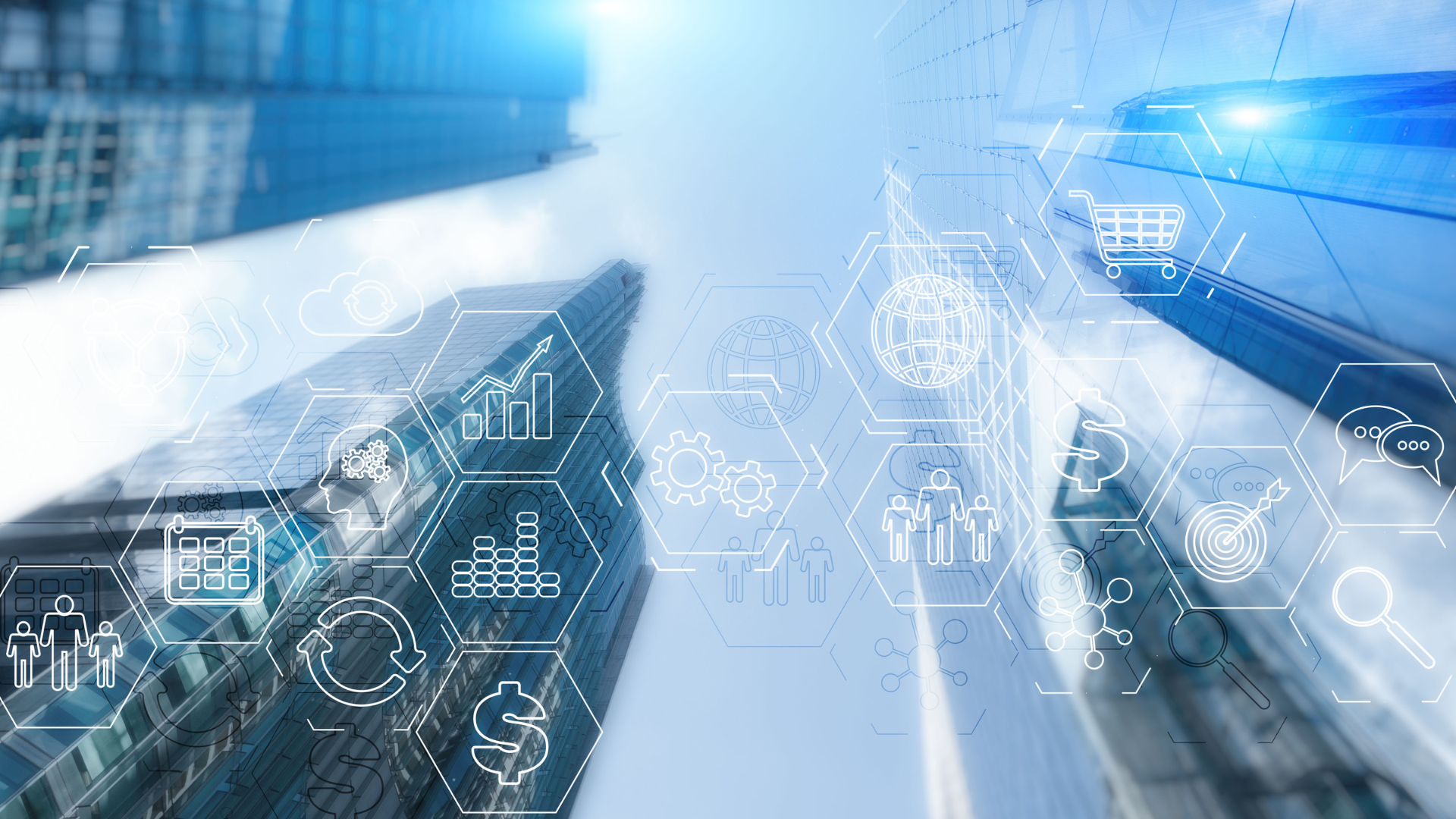
How is ERP different from MIS?
ERP (Enterprise Resource Planning) and MIS (Management Information System) differ in their scope and functionality. ERP is an integrated software solution that manages and automates a wide range of business processes across an entire organization, such as finance, human resources, inventory, and supply chain. It provides a unified platform for data, facilitating seamless communication between departments and improving overall efficiency.
MIS, on the other hand, focuses primarily on collecting, processing, and presenting information to support management decision-making. It’s more about providing reports and data insights rather than managing or automating business processes. While ERP systems can include MIS capabilities, MIS generally has a narrower focus, emphasizing data analysis rather than process integration.
Conclusion
ERP and MES systems each serve unique but complementary roles in business and manufacturing environments. ERP provides a comprehensive approach to managing various organizational functions, like finance, HR, and supply chains, while MES focuses on optimizing and controlling real-time production activities. Understanding the MES ERP meaning and how these systems interact is crucial for businesses looking to improve both operational efficiency and strategic planning. By exploring a list of MES software options, companies can find the right solution to enhance their shop floor management while seamlessly integrating with ERP for streamlined, data-driven operations. Ultimately, leveraging the differences between ERP and MES can lead to more efficient, well-coordinated processes across the entire organization.
Contact us today to discover how understanding the difference between MES and ERP can help you streamline your manufacturing processes and enhance overall business efficiency!
You might also like
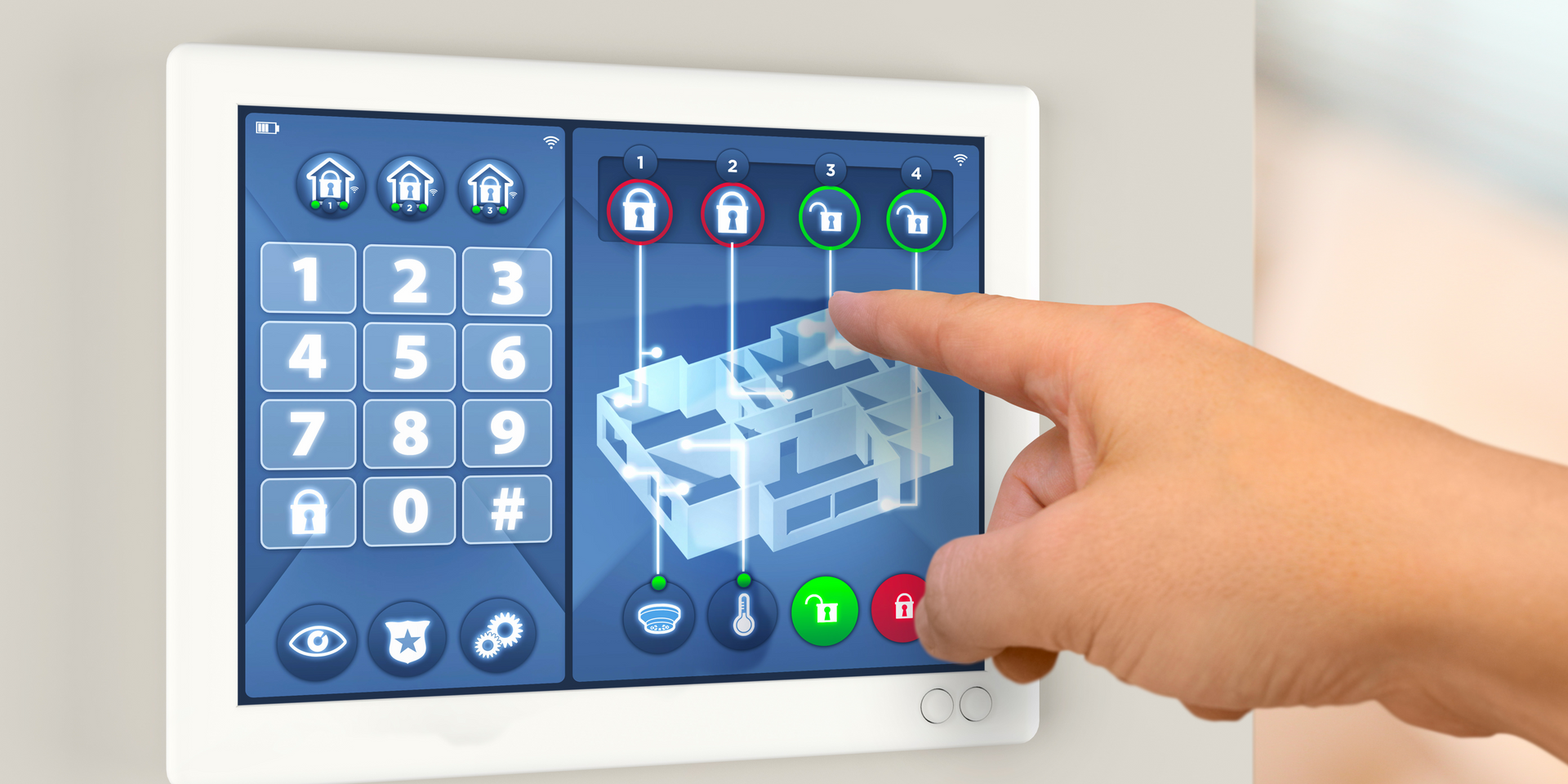
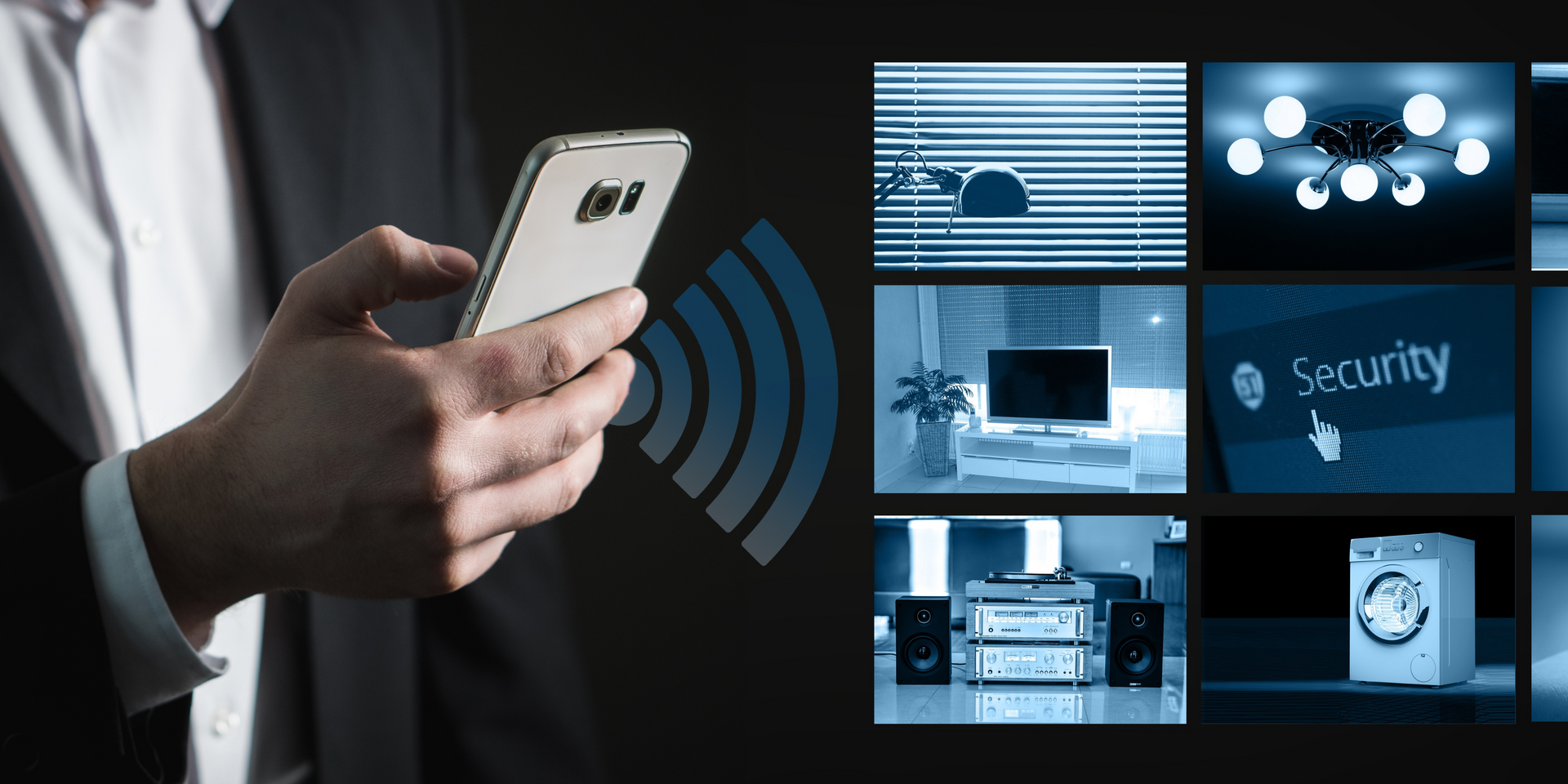
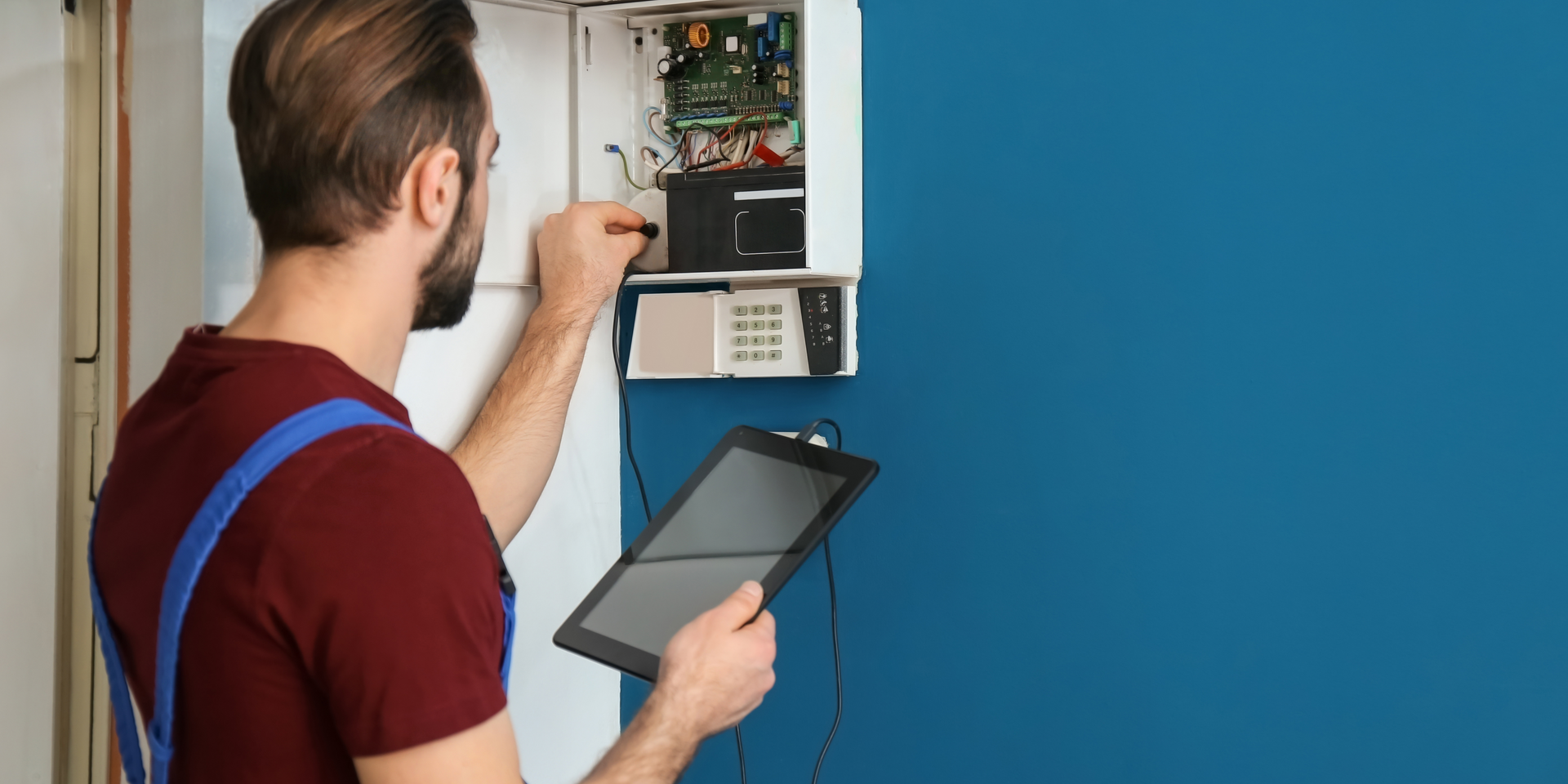