What is the MES Concept?
What is the MES Concept?
The MES (Manufacturing Execution System) concept revolves around the comprehensive management, monitoring, and control of production processes on the factory floor. MES bridges the gap between enterprise-level planning systems and real-time production operations. It captures and analyzes data from machines and workers, providing insights to optimize manufacturing efficiency, improve product quality, and ensure compliance with industry standards. By offering real-time visibility and control over production activities, MES helps manufacturers respond swiftly to changing conditions, reduce downtime, and enhance overall productivity. MES integration involves connecting a Manufacturing Execution System (MES) with other enterprise systems such as Enterprise Resource Planning (ERP), supply chain management, and quality control systems. This integration enables seamless data exchange and real-time communication between different parts of the organization. By integrating MES, manufacturers can ensure that production processes are synchronized with business operations, leading to improved decision-making, streamlined workflows, and enhanced operational efficiency. This holistic approach helps optimize resource use, reduce production downtime, and maintain consistent product quality.
Manufacturing Execution System
A Manufacturing Execution System is a crucial component in the manufacturing industry, as it monitors, tracks, and documents the transformation of raw materials into finished goods. By providing real-time data on production processes, MES helps optimize operations, improve product quality, and ensure regulatory compliance. This system bridges the gap between enterprise resource planning (ERP) systems and the factory floor, offering valuable insights that drive efficiency and productivity in manufacturing environments.
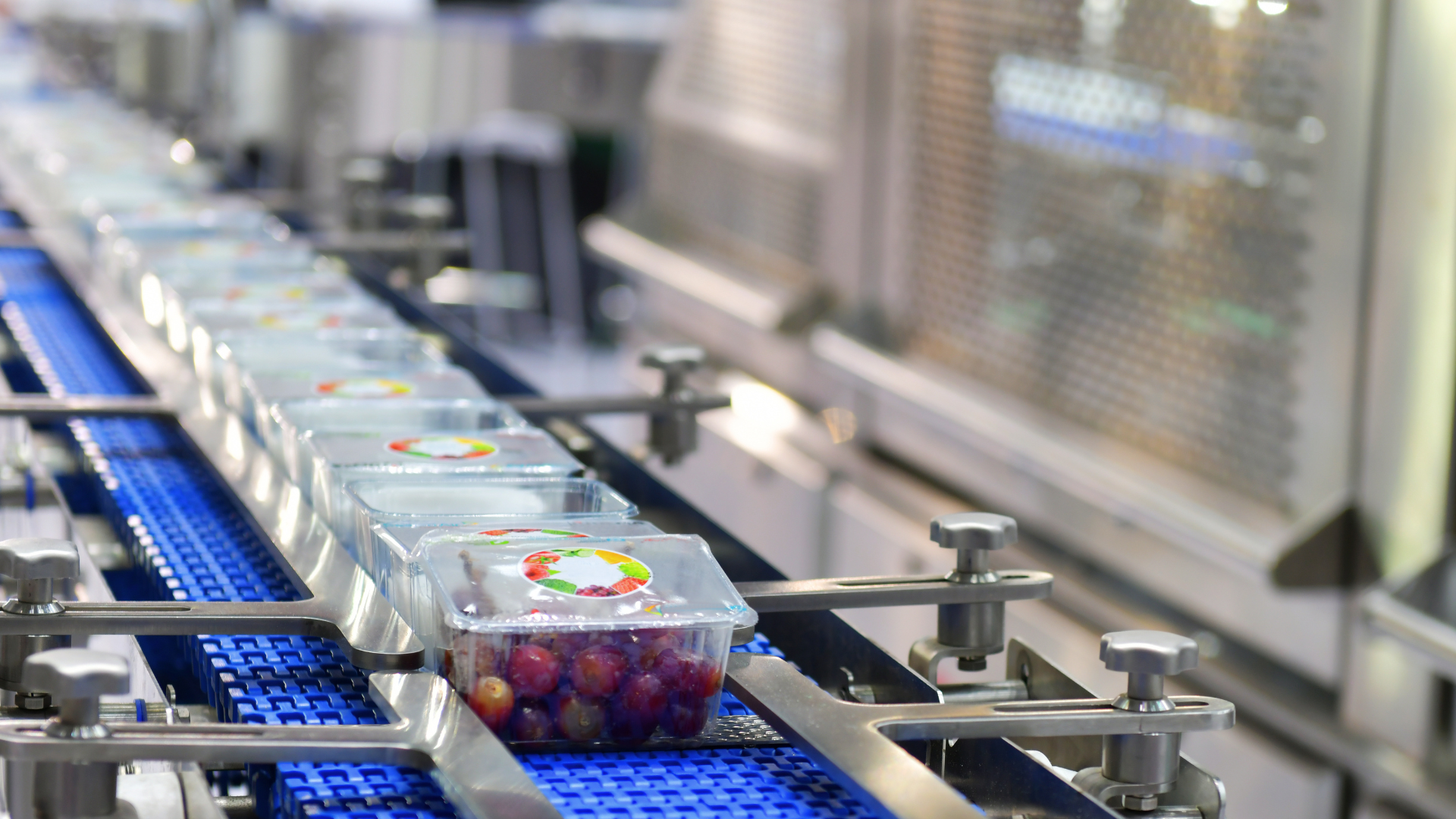
What is the Core Function of MES?
The core function of MES (Manufacturing Execution System) is to manage and control production processes on the factory floor. It provides real-time monitoring and data collection, enabling manufacturers to track production performance, ensure quality control, and optimize operations. MES bridges the gap between planning systems like ERP and the actual production activities, offering insights that help reduce downtime, improve efficiency, and maintain consistent product quality. This system enhances overall productivity by ensuring that manufacturing processes are executed according to plan and adjusted swiftly in response to any issues or changes in production conditions.
SAP and MES
MES is designed to manage and control production processes on the factory floor, providing real-time data and monitoring to optimize manufacturing operations, track product lifecycles, and ensure quality control. On the other hand, SAP (Systems, Applications, and Products) is a comprehensive enterprise resource planning (ERP) software that integrates various business processes, including finance, human resources, supply chain management, and more. While MES focuses specifically on manufacturing operations, SAP provides a broader scope of business management solutions, making it essential for overall enterprise planning and resource management. Together, they can work in tandem to provide a seamless and efficient workflow from production to business operations.
Manufacturing Execution PDF
A Manufacturing Execution System (MES) PDF is a digital document that provides detailed information about MES, its functionalities, benefits, and implementation processes. It often serves as a comprehensive guide or whitepaper for understanding how MES works, including its role in real-time production monitoring, data collection, quality control, and optimization of manufacturing operations. This PDF may include case studies, technical specifications, integration strategies, and best practices for deploying MES in various industrial settings. Such documents are valuable resources for manufacturing professionals seeking to enhance their production processes and overall operational efficiency.
What is the Significance of MES?
The significance of MES (Manufacturing Execution System) lies in its ability to streamline and optimize manufacturing operations. By providing real-time data and monitoring production processes, MES helps improve efficiency, reduce downtime, and ensure high-quality output. It bridges the gap between planning and execution, allowing for better decision-making and quicker response to changes on the factory floor. Overall, MES enhances productivity, ensures compliance with industry standards, and supports continuous improvement in manufacturing environments.
What does MES do?
MES (Manufacturing Execution System) manages and controls production operations on the factory floor. It collects real-time data from machines and workers, monitors production processes, and tracks product lifecycles. MES helps optimize manufacturing efficiency, improve product quality, reduce downtime, and ensure compliance with industry standards. By providing detailed insights and real-time visibility, MES enables manufacturers to make informed decisions, streamline workflows, and enhance overall productivity.
What Does MES Mean in SAP?
In SAP, MES (Manufacturing Execution System) refers to a suite of tools and applications designed to manage and optimize manufacturing operations. SAP offers MES capabilities through its SAP Manufacturing Execution module, which integrates with its broader ERP (Enterprise Resource Planning) system. This module provides real-time monitoring, control, and data collection from the shop floor, enabling manufacturers to improve production efficiency, ensure product quality, and streamline operations. By combining MES with SAP's comprehensive ERP functionalities, businesses can achieve seamless coordination between production processes and overall enterprise management.
What is the Difference Between MES and ERP?
The difference between MES (Manufacturing Execution System) and ERP (Enterprise Resource Planning) lies in their scope and functions within a manufacturing organization. MES focuses specifically on the shop floor, managing and controlling production processes, tracking real-time data, and ensuring product quality. It provides detailed insights into manufacturing operations to optimize efficiency and productivity. In contrast, ERP encompasses a broader range of business functions, integrating various departments such as finance, human resources, supply chain, and customer relationship management. ERP provides a unified view of the entire enterprise, facilitating strategic planning and resource allocation. While MES enhances operational performance at the production level, ERP supports overall business management and coordination across the organization. Together, they create a comprehensive system for managing both manufacturing processes and business operations.
MES vs. ERP
MES (Manufacturing Execution System) focuses on managing and optimizing production processes on the factory floor with real-time data and monitoring. In contrast, ERP (Enterprise Resource Planning) integrates and oversees broader business functions such as finance, HR, and supply chain across the entire organization. Together, MES enhances operational efficiency while ERP ensures overall business coordination and strategic planning.
What is the Difference Between MES and MRP?
MES (Manufacturing Execution System) and MRP (Material Requirements Planning) serve distinct but complementary roles in manufacturing. MES focuses on managing and optimizing real-time production activities on the factory floor, ensuring efficient operations, quality control, and data collection. It bridges the gap between planning and execution by providing insights into the progress of production orders and managing workflows. Conversely, MRP centers on planning and managing inventory levels, materials, and production schedules, ensuring the right materials are available at the right time to meet production demands. Together, MES and MRP streamline manufacturing processes by integrating production planning with execution, enhancing overall operational efficiency and productivity.
What is the Difference Between MES and SAP?
The difference between MES (Manufacturing Execution System) and SAP lies in their primary functions and areas of focus within a manufacturing enterprise. MES is designed to manage and control production processes on the factory floor, providing real-time data and monitoring to optimize manufacturing operations, track product lifecycles, and ensure quality control. On the other hand, SAP (Systems, Applications, and Products) is a comprehensive enterprise resource planning (ERP) software that integrates various business processes, including finance, human resources, supply chain management, and more. While MES focuses specifically on manufacturing operations, SAP provides a broader scope of business management solutions, making it essential for overall enterprise planning and resource management. Together, they can work in tandem to provide a seamless and efficient workflow from production to business operations.
SAP MES Integration
SAP and MES integration involves connecting SAP’s enterprise resource planning (ERP) system with a Manufacturing Execution System (MES) to create a seamless flow of information between business operations and manufacturing processes. This integration allows real-time data exchange, enabling better coordination and decision-making across the enterprise. By integrating SAP with MES, manufacturers can synchronize production schedules, optimize resource utilization, ensure quality control, and gain comprehensive visibility into both administrative and operational activities. This holistic approach improves efficiency, reduces downtime, enhances product quality, and supports agile responses to market changes and production demands.
What is MES?
MES (Manufacturing Execution System) is a software system designed to monitor, control, and optimize manufacturing operations on the factory floor. It provides real-time data and insights into production processes, helping manufacturers manage and track the transformation of raw materials into finished products. MES ensures that production activities are executed efficiently, maintains product quality, reduces downtime, and enables quick responses to any issues that arise during manufacturing. By bridging the gap between enterprise-level planning systems and shop-floor operations, MES enhances overall operational efficiency and productivity.
Is SAP an MES System?
SAP is not an MES (Manufacturing Execution System) but an ERP (Enterprise Resource Planning) system. While SAP provides comprehensive solutions for various business functions such as finance, human resources, and supply chain management, it does offer MES capabilities through its SAP Manufacturing Execution module. This module integrates with SAP's ERP system to provide real-time monitoring, control, and optimization of manufacturing processes. However, the core SAP system itself is primarily focused on broader enterprise management rather than the specific, detailed execution of manufacturing operations that a dedicated MES system handles.
MES Software Examples
- Siemens SIMATIC IT
- Rockwell Automation FactoryTalk
- Honeywell MES
- ABB Ability Manufacturing Operations Management.
List of MES Software
Here are some notable MES (Manufacturing Execution System) software solutions:
- Siemens Opcenter (formerly known as SIMATIC IT and Camstar)
- Apriso FlexNet
- Aegis FactoryLogix
- SAP Manufacturing Execution (SAP ME)
- Wonderware MES (formerly known as Wonderware Operations Management)
- Rockwell Software MES
- Plex Manufacturing Cloud
- IQMS MES
- Lighthouse MES
- DELMIA Apriso MES
Leading MES Software Providers
Leading MES software providers include Siemens, Rockwell Automation, Honeywell, ABB, and Dassault Systèmes. These companies offer robust solutions for optimizing production processes and ensuring quality control. Siemens SIMATIC IT and Rockwell Automation FactoryTalk provide comprehensive tools for real-time monitoring and control. Honeywell MES focuses on compliance and quality enhancement, while ABB Ability Manufacturing Operations Management integrates seamlessly with business systems. Dassault Systèmes DELMIA Apriso is known for its flexibility and scalability, making it suitable for various manufacturing environments.
Example of MES System
Examples of an MES (Manufacturing Execution System) include Siemens SIMATIC IT, Rockwell Automation FactoryTalk, and Honeywell MES. Siemens SIMATIC IT offers comprehensive solutions for managing production processes and optimizing operations. Rockwell Automation FactoryTalk provides real-time monitoring and control, ensuring efficient production workflows. Honeywell MES focuses on enhancing product quality and compliance with industry standards. Other notable MES systems include ABB Ability Manufacturing Operations Management, which integrates production and business systems for improved efficiency, and Dassault Systèmes DELMIA Apriso, known for its flexibility and scalability in various manufacturing environments. These MES systems are essential for streamlining manufacturing processes, ensuring quality, and boosting productivity.
Manufacturing Execution System Software List
A Manufacturing Execution System (MES) software list includes some of the most advanced and widely used systems in the industry.
- Siemens SIMATIC IT
- Rockwell Automation FactoryTalk
- Honeywell MES
- ABB Ability Manufacturing Operations Management
- Dassault Systèmes DELMIA Apriso
- GE Digital's Proficy
- PTC's ThingWorx
- Schneider Electric's Wonderware
- SAP Manufacturing Execution.
These systems are essential for enhancing production efficiency, ensuring quality control, and optimizing manufacturing operations.
MES Software Vendors
Leading MES software vendors include Siemens, Rockwell Automation, Honeywell, ABB, Dassault Systèmes, GE Digital, PTC, Schneider Electric, SAP, and Oracle. These providers offer advanced solutions to streamline and optimize manufacturing operations. Siemens SIMATIC IT and Rockwell Automation FactoryTalk are known for their real-time monitoring capabilities. Honeywell MES excels in quality control and compliance. ABB Ability Manufacturing Operations Management integrates with business systems for enhanced efficiency. Dassault Systèmes DELMIA Apriso, GE Digital's Proficy, PTC's ThingWorx, Schneider Electric's Wonderware, SAP Manufacturing Execution, and Oracle MES provide comprehensive tools to meet diverse manufacturing needs.
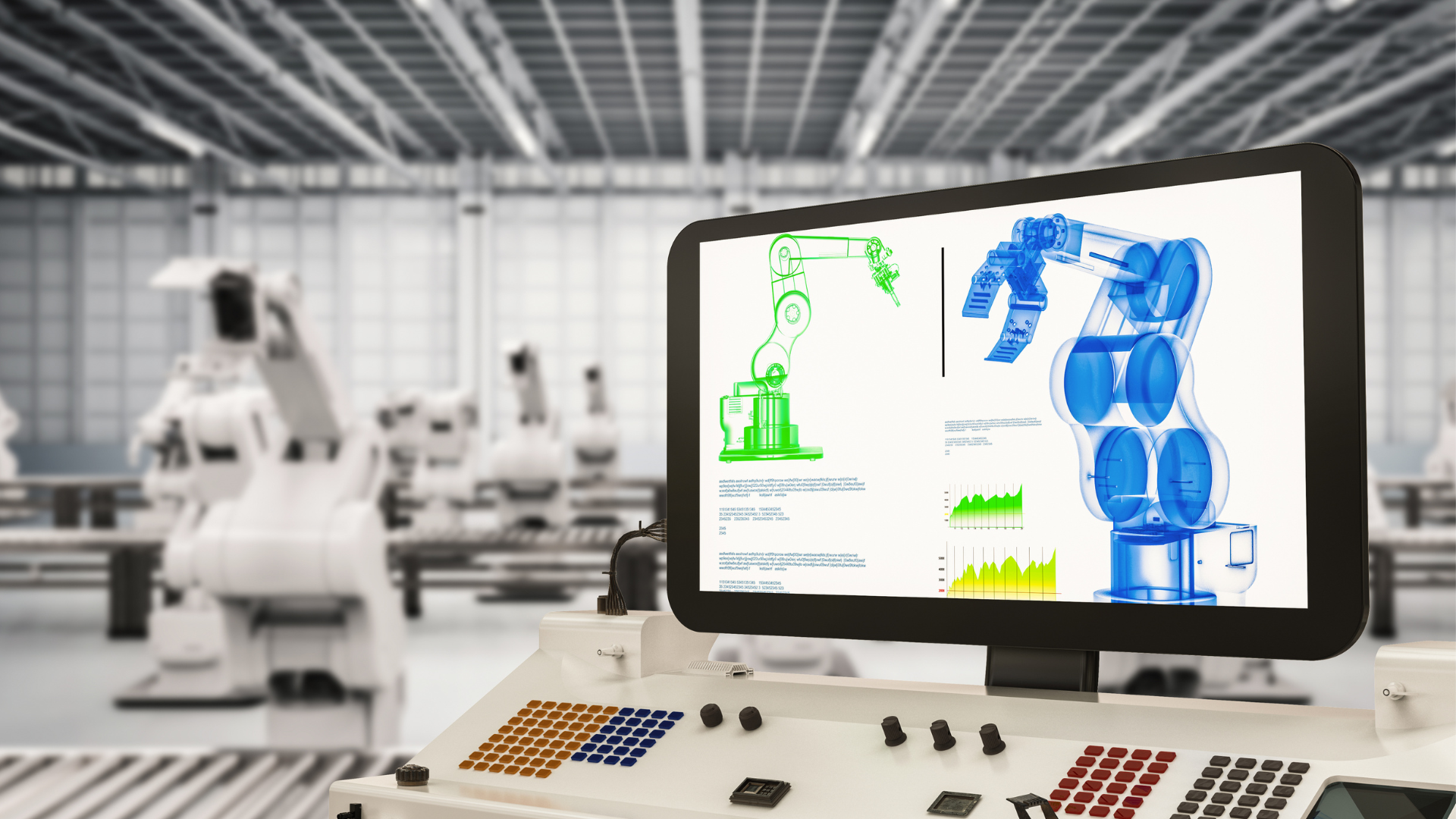
You might also like
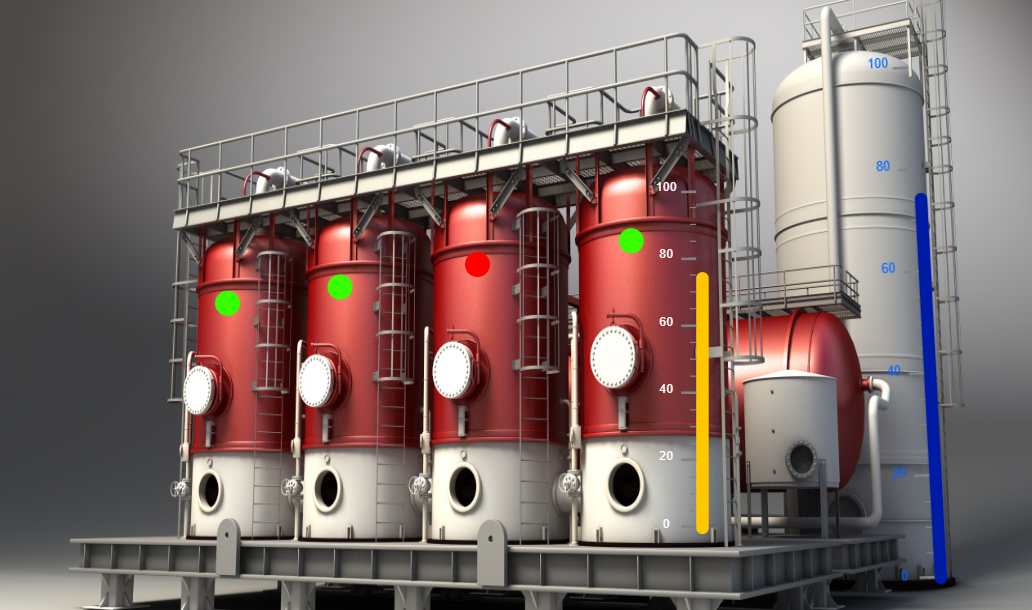
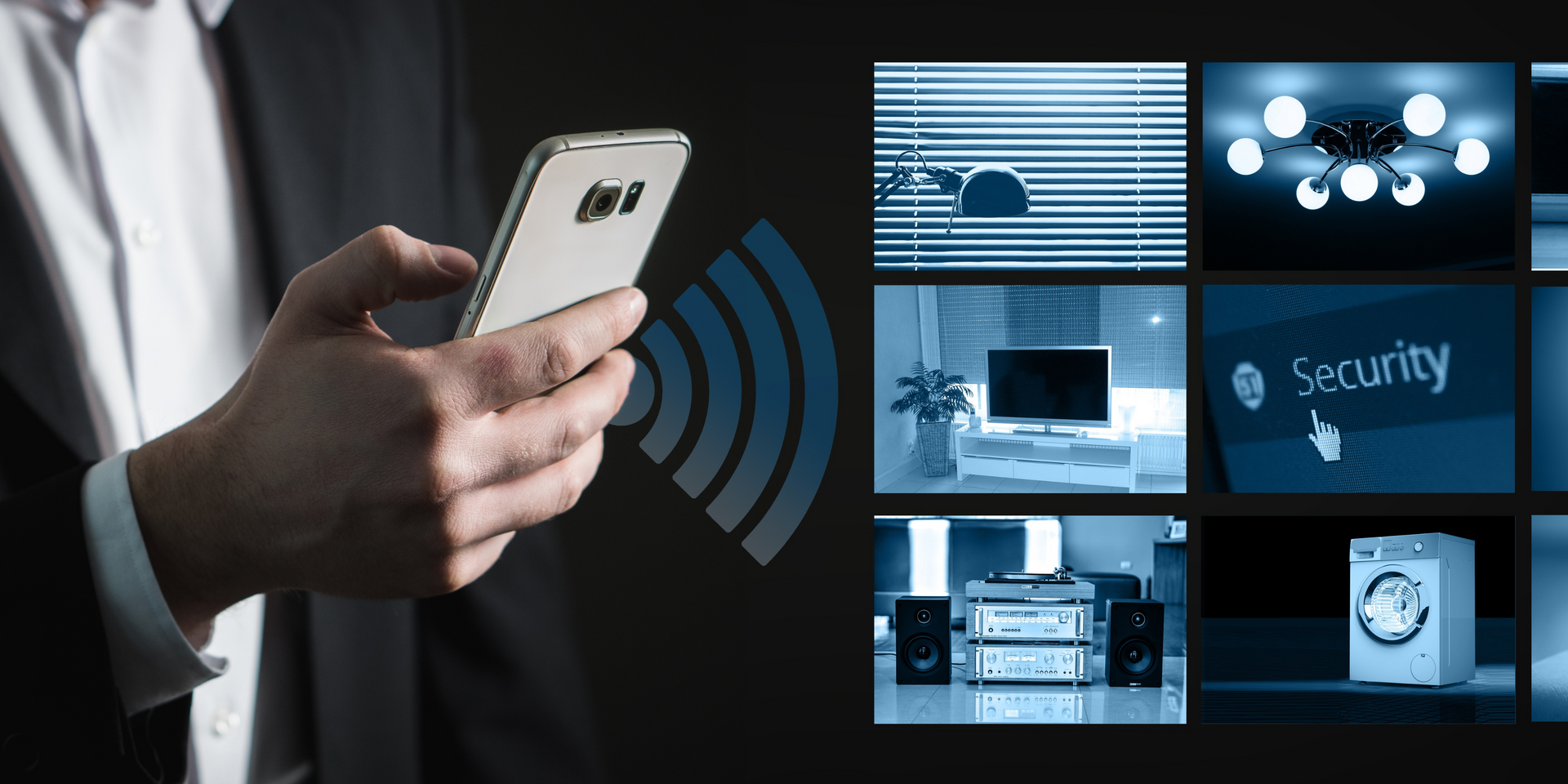
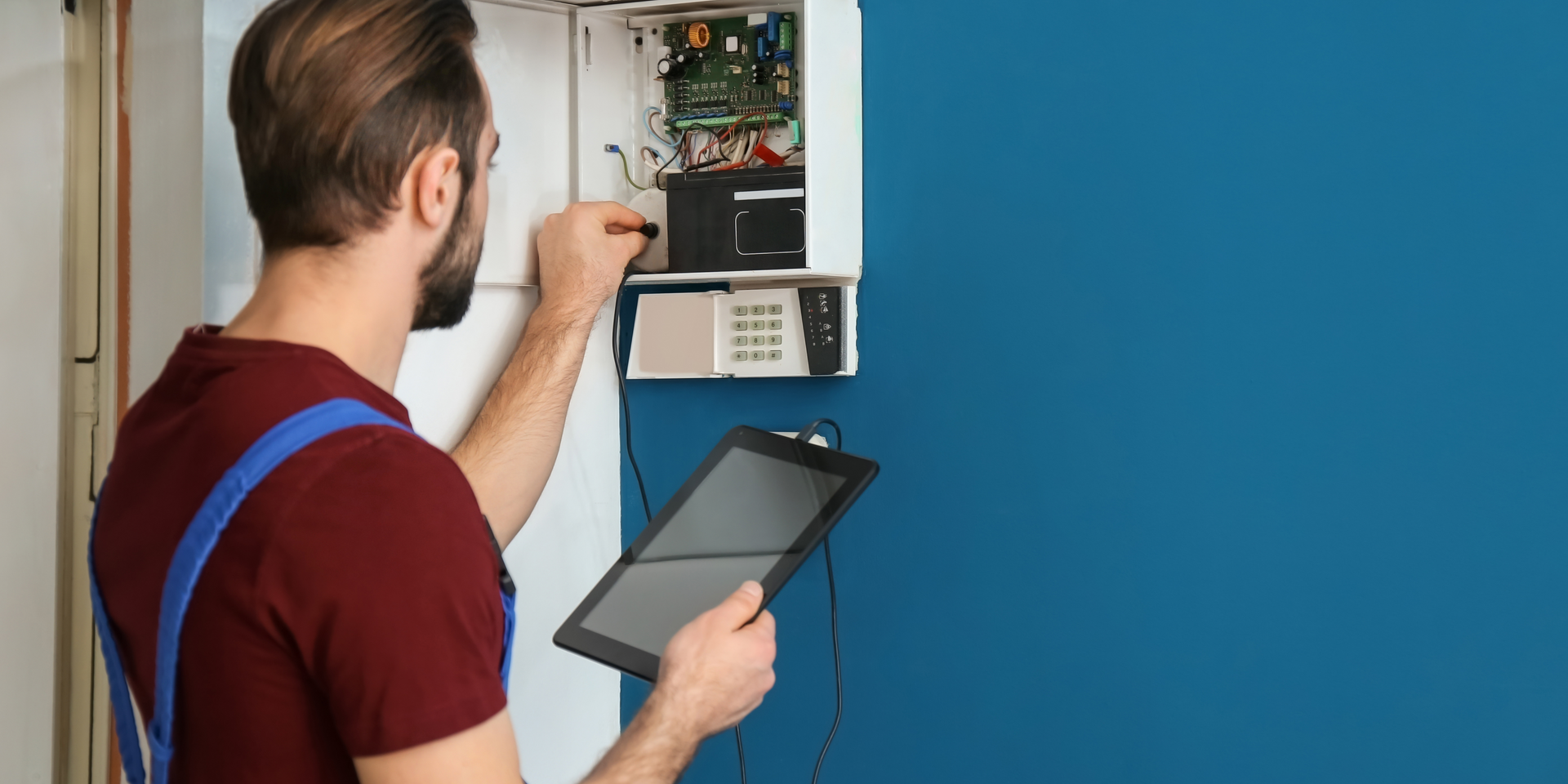